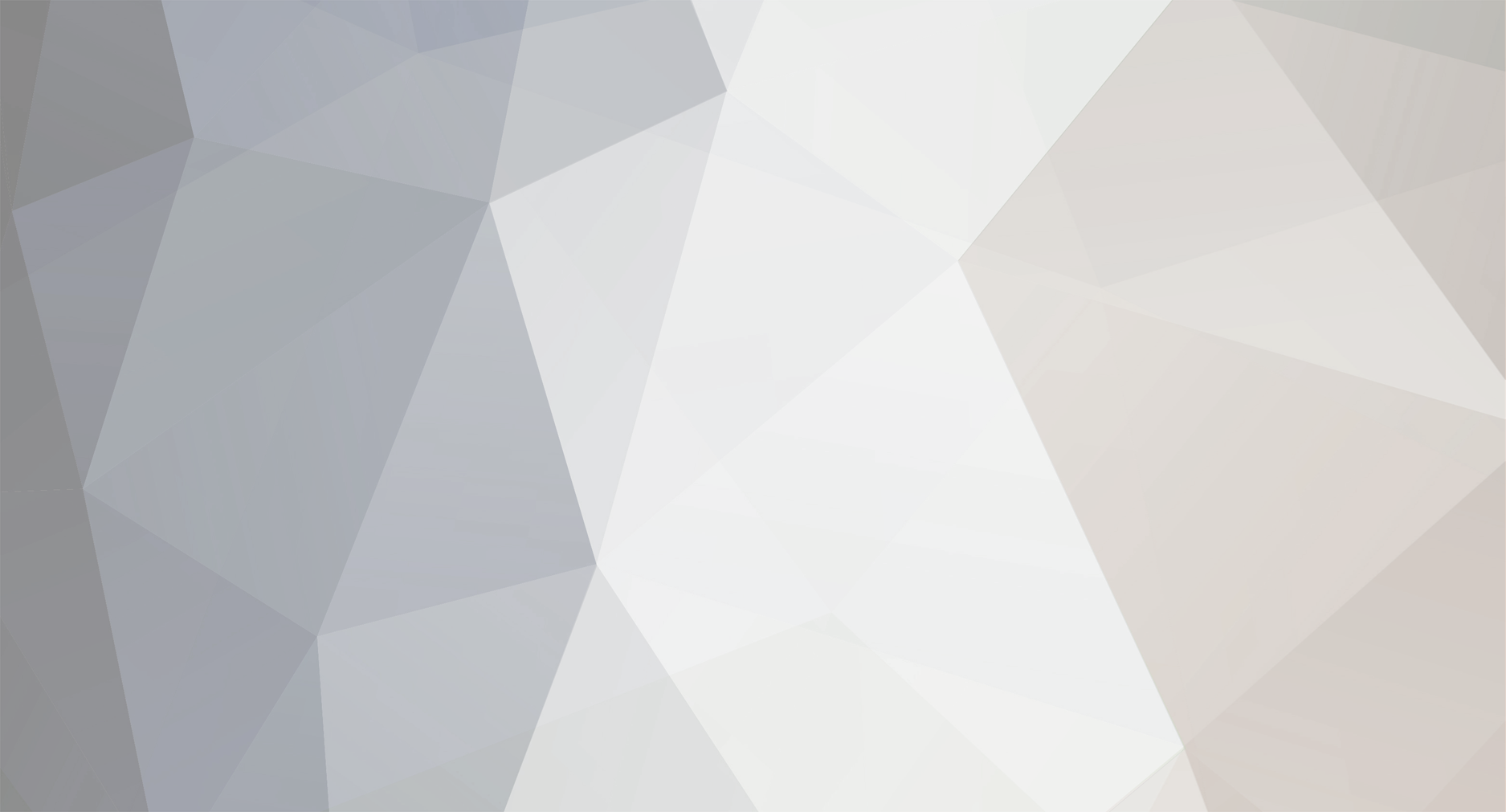
CybrStuff
Members-
Posts
20 -
Joined
-
Last visited
Content Type
Profiles
Forums
Blogs
Events
Gallery
Downloads
Store
Everything posted by CybrStuff
-
Frankly, I have a really hard time believing this. Alumin(i)um has a thermal conductivity of about 200 W/mK, so 17 times better than this is about 3400 W/mK. The most conductive metal is silver, with a conductivity of about 400 W/mK, so your material is clearly non-metallic. I have found some things that say that a carbon nanotube can get to 6600 W/mK at room temperature (compared to the paltry 3320 W/mK of pure diamond), but good luck making a radiator out of either of those. I'm calling shenanigans. No offense intended.
-
I feel like the reason you had such a hard time trying to get the Gtech lined up with "the real world" is that it doesn't take enough variables into account. For example, when you're going 60 mph, the difference between a 20 mph headwind and the same tailwind is going to be probably tens of horsepower loading on the engine. There are no instruments that come stock on a vehicle that can measure wind speed, so naturally any measurement based on stock instruments are going to be incorrect. I think by supplementing those stock instruments with a few others, it should be possible to get reasonably close to measuring real horsepower.
-
As far as I can tell, this is how all of the main commercial ones work. Of course, I'm willing to admit I'm wrong if anyone can show me one that does what I'm looking for. The way I see it, if I wanted a dyno run, I would go to a dyno (prices notwithstanding) and get much more accurate data.
-
Exactly. Really, it's just sheer morbid curiosity. I'm somewhat of a data freak and would love to see how much horsepower you actually need in most situations. Plus, correlate that with a fuel computer and you could get some interesting mileage vs. power graphs. Mostly though, it would just be a fun thing to try to implement using my digital circuit knowledge. You're right. As far as measuring effective horsepower (actual horsepower - rolling resistance - drag), such systems are probably quite good. The main reasons I'm looking into something more are that:1) They don't give you a realtime reading. 2) They don't let you see gross wheel horsepower (the number before parasitic losses). This is a tricky subject because it depends a lot on the shape of the car and the local atmospheric conditions. One that I know for sure is that wind resistance goes up dramatically as a function of speed (on the order of the speed cubed?), so your drag at 70 mph is considerably more than your drag at 60 (and who among us never goes over the speed limit?). Anyway, I know it's not a gigantic amount (unless you're looking at going over 100 mph or so, when the drag can require hundreds of hp to overcome), but the geek in me (that is to say, all of me ) is interested in knowing how much power I'm developing at any given point in time.
-
Link to the shootout An interesting sidebar on weather correction I read through the article, but unfortunately, they don't really talk about horsepower and torque numbers. Their testing is based more on quarter-mile times, 0-60 times, lateral g's, and braking. They mention that one of the meters can give you a road horsepower reading by analyzing some acceleration data, but I get the feeling that it's the same thing as the Gtech, where it just represents your net horsepower, not your actual horsepower to the wheels, and also that it is not a realtime measurement (e.g. you're cruising down the highway at 70 mph and the display reads '57 hp'). Thanks for the heads up on the article, though.
-
Yeah, it's no problem . That's the reason behind my initial idea. Since the Gtech can't do this, I was wondering if it would be feasible to develop a system that could.
-
Yeah, I know about Gtech, but does that work when you're just cruising, say at highway speeds, when all of the power of then engine is going into maintaining speed against rolling resistance and wind drag? From all the data I can find on their site, it's more for doing dyno pull type runs on the street, and it doesn't figure out how much power your engine is really making to the rear wheels because it doesn't care about aero drag or rolling resistance.
-
So I know you all love the abstract technical questions, so here's a doozy for you. What I've been tossing around in my mind for the past few weeks is whether it would be possible to measure a car's power output in realtime. I have a few ideas and I was wondering if I could get some input from the experts around here. Here's the basic idea: Base horsepower can be derived from the rear wheel torque, which is a function of acceleration (F = ma), wheel diameter, and engine rpm. From the base horsepower, we add a correction factor for wind resistance at the relative wind speed around the car (using an anemometer or some other wind speed measurement). We also include a factor to account for the angle of the car (it will be accelerating naturally down hills, etc.), which will be measured by a tilt sensor of some sort. Finally, we add a factor to account for frictional losses (that is, the fact that a car rolling in neutral on a flat surface will eventually stop). Now, assuming I didn't leave something out (which is possible), there are still a couple of tricky parts. First, we have to determine the rolling resistance, which might be possible by using a roll-down test from a relatively low speed (to avoid wind resistance). Next, we have to figure out a rough approximation of wind resistance as a function of speed, which should be possible by making a dyno run to get a feeling for horsepower, and then making a similar run on the street (probably not in 4th though ) and, using the accelerometer, figuring out the difference in power at a given wind speed. Since we now know the rolling resistance, we can account for environmental variables (temperature, humidity, altitude, all that stuff that affects mass air flow) and come up with a reasonable approximation of horsepower loss to wind. Once we do these weeks of painstaking tests and add probably a dozen instruments to the vehicle, I think it should be possible to get some kind of realtime horsepower display inside the vehicle. Any thoughts?
-
I saw a fairly stock light blue '72 240Z (or at least the markings on it said '72) by the body shop where I picked up my Subaru this morning in Leominster, MA. It made me very, very happy . It was for sale, too... Be still my heart...
-
-
You can't be serious, right?
-
The problem with the kit that you're looking at is that it just includes the HID bulbs. While you can swap them into any installation that uses standard halogen bulbs, it will create problems for you down the road. Even though the bulbs are the same size, the pattern of light generated by them differs, which means the reflectors in the halogen enclosure won't reflect the light properly, resulting in glare, which not only can be blinding to other drivers, but can attract undue attention from the police. In order to properly switch to a HID system, look for something like this (from my bookmark file, no affiliation): 5-7" Projectors
-
Sounds like a mystery wrapped in an enigma to me. Can we play charades and try to guess the answer?
-
The only problem I would see with this is that the main reason for deactivating valves at all is to keep the compressed charge in the deactivated cylinders to act as something like an "air spring" (I think I stole that term from somewhere where I was doing research, but I don't remember where) for the crankshaft to push against in between power strokes in the three active cylinders. I understand this concern, but I was already considering running separate intakes for the two banks (either one per bank or maybe even individual). Instead of having to disable both intake and exhaust valves to maintain charge pressure in the cylinder, a bit of clever timing would allow the exhaust side to remain closed after a power stroke and then just keep the throttle body(ies) closed so that even though the intake valves are doing their thing, charge pressure is maintained. Thanks again for a well-thought-out reply. It's fun to talk about this stuff, even if I'll never have the budget or skills to pull it off.
-
-
I've been thinking about this, trying to figure out the easiest way to actuate a valve deactivation system. It seems that the companies that have done this so far have used a special lifter that can be activated or deactivated by hydraulically actuating a pin inside the lifter. This seems beyond my fabrication abilities. However, I was thinking that maybe I could hook up a system that works similarly to Honda's VTEC. By making a two-piece rocker, I might be able to set it up such that a pin, which would connect the two pieces to allow normal operation, could be removed to allow cylinder deactivation. Any thoughts?
-
I'm aware that the complexity of a system like this is probably far greater than the fuel economy that I would gain by using such a system, but I'm always game for a technical challenge when it's not horribly impractical. Also, I have to do something to distinguish myself from all the other fine vehicles around here. I have to say that I've done a lot of searching online and this is the first time I really understood how the valves played in all of this (looking back, it makes me feel rather foolish ). Thanks for that. Back to the research!
-
I've been lurking here in the forums for a while to research my options for a 240Z L28(ET/ETT?) build that I want to do someday (being a college student doesn't afford one the time, money, or space for a project of this magnitude). I hope I'm not wasting peoples' time by shooting the breeze about a car I probably won't have for three years, but I have no one else to talk to about some (hopefully) cool ideas that have come to me as I've been researching . Anyway, being an electrical engineer, I tend to like to replace simple, mechanical systems with vastly more complex electronic ones (like going to standalone EFI instead of carbs), which brings me to my question. I've been seeing more and more cars lately that can deactivate a bank of cylinders (displacement-on-demand for GM, etc.) to save fuel while cruising, and thought it might be a cool feature to add to an electronically-controlled L28. With a standalone EFI system (I'm eyeing Wolf3D at the moment) in conjunction with a bit of custom hardware (disabling fuel injection for three cylinders under a set throttle position), I think it would be relatively simple to set up a basic 3-cylinder deactivation system. Further, if the intake were engineered to use dual (or even individual) throttle bodies, the three deactivated cylinders could be cut off from the air supply as well, which would reduce pumping losses and improve fuel economy even more. My main concern is vibrations. I know that the new Honda V-6 with cylinder deactivation has to have an active vibration cancellation setup in its engine mounts to keep the car from shaking, but I also know that a V-6 is not an inherently smooth system like an I-6 is. I was just wondering if any of you people who actually have your L28s might have some insight into the feasibility of a setup like this. Thanks.
-
I checked out that Being Seen site (http://www.beingseen.com) and they have white, red, and blue EL sheet, which leads me to believe that with a combination of one of the sheet colors and an appropriate transparent or opaque overlay, you could produce just about any effect you wanted. I get the impression you want something like white gauges at day with just the numbers lit up in blue at night, which could be achieved with a blue EL sheet and a white opaque mask. You might even be able to create more exotic effects like multiple colors (redline?) using multiple EL sheets.
-
I'm sure it can be done, though it would take a bit of planning/research on what the resistance of the OE knob is.
-
This is sort of the right idea, but you are a bit confused on the details. An LED works because the movement of electrons in the semiconductor material of which it is comprised (in the middle of all that plastic) produces light, whereas a light bulb works because a very thin filament carries a high current, causing it to get hot and glow. The reason that a light bulb has to be evacuated of most gas (and what gas that remains has to be an inert gas) is that otherwise the filament would completely burn up and disintegrate almost instantly (damned oxygen ). You are right that you can control the brightness of an LED with a correctly sized potentiometer, because it would regulate the amount of current driving the LED, however, a more sophisticated (and therefore appealing to me as an electrical engineer ) way to regulate the amount of light is by a technique called pulse-width modulation. You can find the details if you Google it, but I have to go to class. Enjoy!