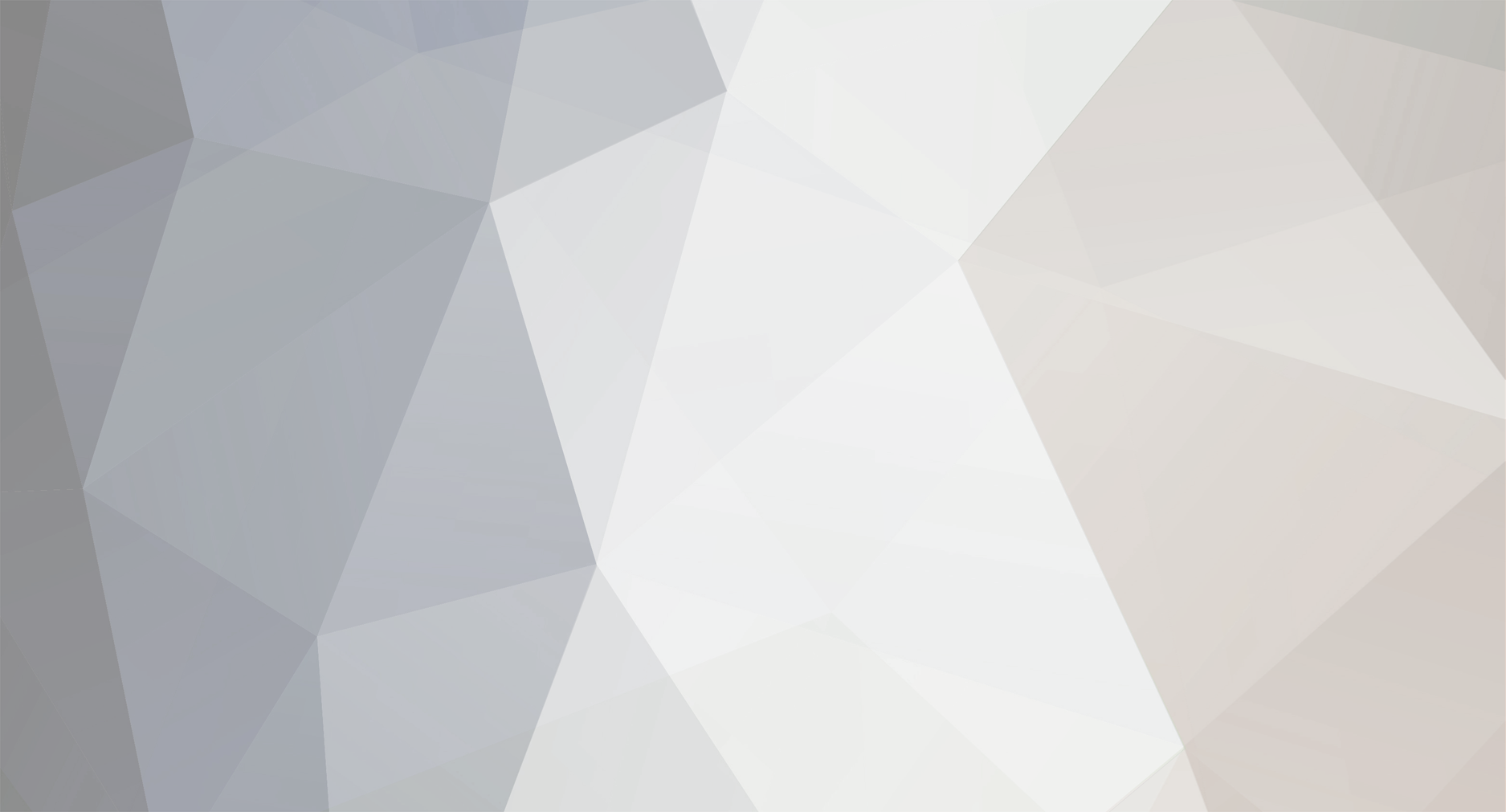
wozza
-
Posts
9 -
Joined
-
Last visited
-
Days Won
1
Content Type
Profiles
Forums
Blogs
Events
Gallery
Downloads
Store
Posts posted by wozza
-
-
Your pairing is correct. 6-3-1 is suppose to be better for midrange, It was recommended by a ex British touring car engineer I work with. If you don't run them together (at the correct length) to 1 tube you will sacrifice power. I wouldn't recommend three pipes. Is this going to be for a race car or street?
-
-
Joe's Manufacturer is replacing them at the next production run, that is in 8-10 weeks from now.
-
Update from me, Joe from Chequered Flag Racing has been in contact with the Manufacturer and they have agreed to replace my stub axles too when they make a new batch.
Thanks Joe.
-
1
-
-
I Also agree, end float is what you need to check and that is determined by spacer length. A quick Google of torque specs for m20 bolts 4.8 grade is 166 lbft, a 8.8 grade 321 lbft. I hardness tested a standard stub axle too, comes out at 15 to 20 HRC on the shaft and 9 HRC on the flange. 20HRC is around a grade 8.8 bolt
-
-
It appears I have his yahoo address that he was using in April so thank you LLave for his new address. I will email him shortly
Regarding torque, Haynes manual is 180 and up to 240ftlb if required to meet rotation torque requirements. 180 is about the most I can achieve with 1/2inch drive socket and I have never had a problem before. I lube all my threads,I use a lanolen product unless its an engine/gearbox etc. Good for your hands too!
Regarding peening with a sedgehammer, I didnt need the sledgehammer this time, its got a stiff nut, I think its from a 280zx? nowhere to peen it.
Curvature of the shaft does change the hardness reading but at this diameter its only .5 HRC
-
Has anyone had a 4340 stub axle break off at the theads?
I have attempted to contact Joe from Chequered Flag Racing / Modern Motorsport as this is the stub axle he sells, but I have not heard back, I know he is on this forum so I hope to responds.
The stub axle was purchased this year and has only done 30 miles
The failure point is not under load with engine torque or torque forces caused by sticky tires. The only failures I have had with standard stub axles is the wheel flanges failing.
The nut was not over torqued and CV axle is not too short and pulled the threads off, there is more than 1.5 inches of plunge extension left and my suspension has very little droop
My analysis of the failure.
1. Design. The threads are machined all the way to the step causing a large stress riser at the failure point, I have included a picture of the Modern Motorsport theads next to standard theads, You will see on the standard stub axle the threads stop well short of the step and have a nice radius
2. Hardness. I had the 4340 stub axle hardness tested, result was more than 51 HRC (Hardness Rockwell C scale)
Carroll Smith's book 'Engineer to Win' states 42-44 HRC range for E4340 hubs, axles and torsion bars, Aircraft landing gear are also made from 4340 and need to be in this range too.
Did I get an incorrectly machined and heat treated stub axle set?
If there are any Metallurgists out there I would like their opinion too and looking forward to hearing from Joe.
Broken 4340 Stub Axle threads
in Drivetrain
Posted
Mine are in Transit, Joe shipped about 2 weeks ago. I suspect they are from the same manufacturer. Yours must be close SH4DY.