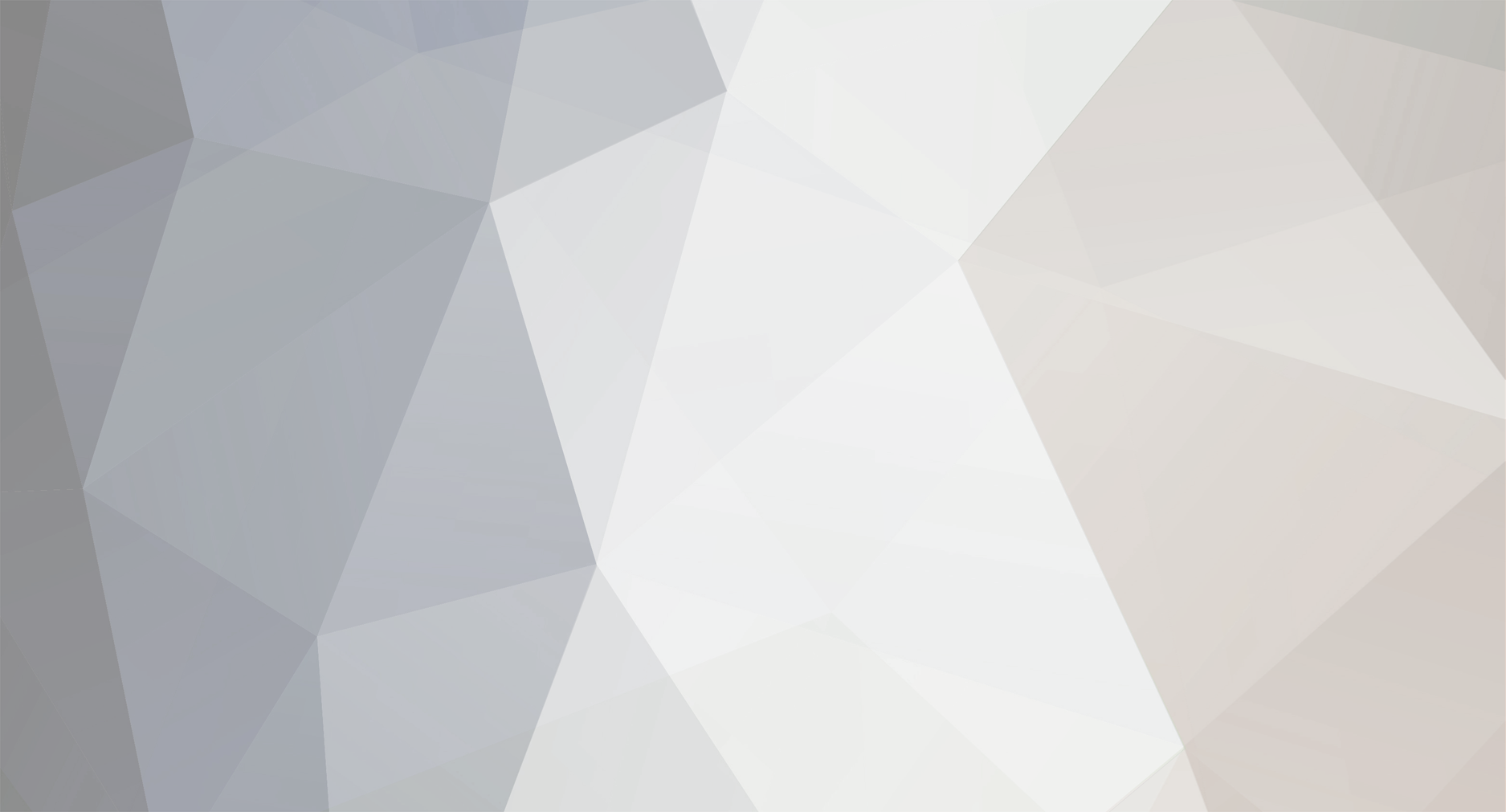
datsunmike
-
Posts
11 -
Joined
-
Last visited
Content Type
Profiles
Forums
Blogs
Events
Gallery
Downloads
Store
Posts posted by datsunmike
-
-
On 11/28/2017 at 9:45 PM, Dusty said:
So i have been around the performance industry alot when I was in college specifically 2v v8 stuff and worked in a shop that specialized in very fancy heads and still screw around with stuff for my interests. Digitizing, CFD, and CNC are the very last steps in cylinder head development. In my opinion only really relevant to someone interested in production of dozens of heads for repeatabilities sake. If you want to jump in this rabbit hole then research, the flow bench, and a die grinder is where to start.
Thanks for your wisdom. I don't have any expectation of results over this, nor is this a project which I plan to apply to my car in any kind of near future.
It's basically ''because I can'' kind of project. Also one which I hope will help me practice my skills. At the worst i'll have a neat scan of the head.
I've obtained a N42. Trying to get it done before xmass. I'll post.
-
I will definately take this into consideration. My goal was to scan the whole head using the scanner and making some resin plugs for the ports and merge the two somehow. I've got nowhere near your skills your dohc head is beyond impressive. In more trying to hone my skills while having fun. Accuracy will be around 50um.
For any kind of machining I would definately use the Faro arm.
I'm gonna post on the wtb all I need is some old head. I'll be checking eBay too...
-
I have access to a high precision 3D scanner...
I've been thinking of trying to scan the L28 head, including the ports and the combustion chambers. The goal being to make some flow simulations and maybe even develop come kind of cnc program for porting the heads. Maybe even the block at a later date too.
Heres my questions for you guys:
1-Is this even worth it ? (I enjoy the challenge but maybe it has already been done)
2- Is there someone with flow simulations experiences in solidworks or any other CAD program. I can manage with inventor for basic stuff but flow simulations would be out of my range.
3- My head is on my car, anyone with a cracked head that could still render a good scan they would want to get rid of. Or someone in Canada (east) who would borrow one. PM if possible.
Let's see what you guys think!
-
How I wish I knew that!!
I bought the Zeddfindings since they are from a fellow canadian, less complicated to obtain with customs and all...
Do I understand well that in my situation, if I choose to use the 240 style floor and rail I cannot reuse the 280 seat brackets?
-
Took me a while (ordered new floors) but I finally took some pictures.
You can see in the first picture circled an area where the folded edge of the rail connects to one of those uneven dips in the floor on the side where I didn't remove the rail yet.
The second pic shows the passenger floor how it looks after I removed the rail. You can see the areas where there are dips. There are a few along.
Third pic, new rail and flor completely straight and flat
Fourth pic, only rusted area in the entire floor pan at the rear tip of the old passenger rail.
So here is my dilemma. My first idea was to simply order new floors that would be completely flat, cut everything up and have a nice time welding flat rails on a flat floor. But after inspection, only one area of about 4x4 inch is rusted and needs replacement. The rest of the floors are in great shape, still on primer. Drivers side rails are also perfect.
I do know that it's better to do it while i'm at it, that's why I ordered floors, but really the original floors are in good shape except one small area which I could probably patch easily.
So I guess I'm looking for opinions, should I bite the bullet and redo everything, or is there a way to weld those rails nicely to the original floors.
-
I will post some picture to explain better. I beleive I have the right rails. The stock floors have some dips in them, perhaps to add strength and make pockets to drain possible water. I have not found many pictures of this since people usually change the floors at the same time, and aftermarket floors are much flatter.
From the few pictures I've seen where people only replace the rails, it seems people simply hammer the new rail to conform to those valleys,
-
Sorry if this has been covered already I did search, probably not well enough.
I'm installing some new floor rails under my 280Z. The original floors are great, but the passenger side rail had some rust holes in the middle of it that were patched by a lobotomized zombie.
The stock floor (at least I think) on the passenger side is not flat. It has some little bumps in it, the orinal rail follows this. The new rail however is completely straight and flat! I do I go about welding the rail to the uneven floor? Do I weld some little pieces of metal to flatten everything? Or I could tack it in place and use a hammer and dolly to flatten the floor sheet meal before finishing welding?
Thanks!
-
A lot of info can be found here on this car. A really cool build to check out, and a lot of pictures.
http://forums.corvetteforum.com/showthread.php?t=1818351
The interesting part is that this car does not have 180 degree headers. After reading the updates it seems that the car has kooks headers which merge into a single pipe. It seems that perhaps if someone would be willing to experiment a bit with 180 degree headers and different muffler combos, it could be possible to get really close the the high pitched sound of flat cranks.
-
I have been lurking this thread since the begining, i do not remember this beign posted, sorry if it is a repost.
This LS7 sounds really high pitched, I do not know if it has 180 degree headers or not. I really like the rumble down low and the high pitched revs its kinda like a double personality.
-
Here is what you need to do!
http://www.fiero.nl/forum/Forum2/HTML/065545.html
I thought about doing something simillar, I was thinking of flipping them so I would get the real look of a v8, Link them both to some sort of frame, have a shaft passing in the middle of both, each engine would be connected to the shaft by a chain, you could then connect the shaft to a normal transmission. That would take a lot of fabrication. This guy did it much more simply althout I dont know how the transmission are holding up. If you want even more of an exotic sound take two of those, http://cgi.ebay.ca/Arctic-Cat-1000-Triple-Engine-Complete-Thundercat_W0QQitemZ220217100007QQihZ012QQcategoryZ100468QQrdZ1QQssPageNameZWD1VQQ_trksidZp1638.m118.l1247QQcmdZViewItem put a chopper style belt on each end, with a shaft in the middle as I said, would be even simpler, and it would sound really brutal. But would probably be a brute to drive, giving the power curve of most two strokes, which would make it even cooler!
Twin cam head for the L6 from Derek at Datsunworks
in Nissan L6 Forum
Posted
Ohhhhh, I've said it before, nicely done swagelok always beings me to my happy place! Great work as usual.