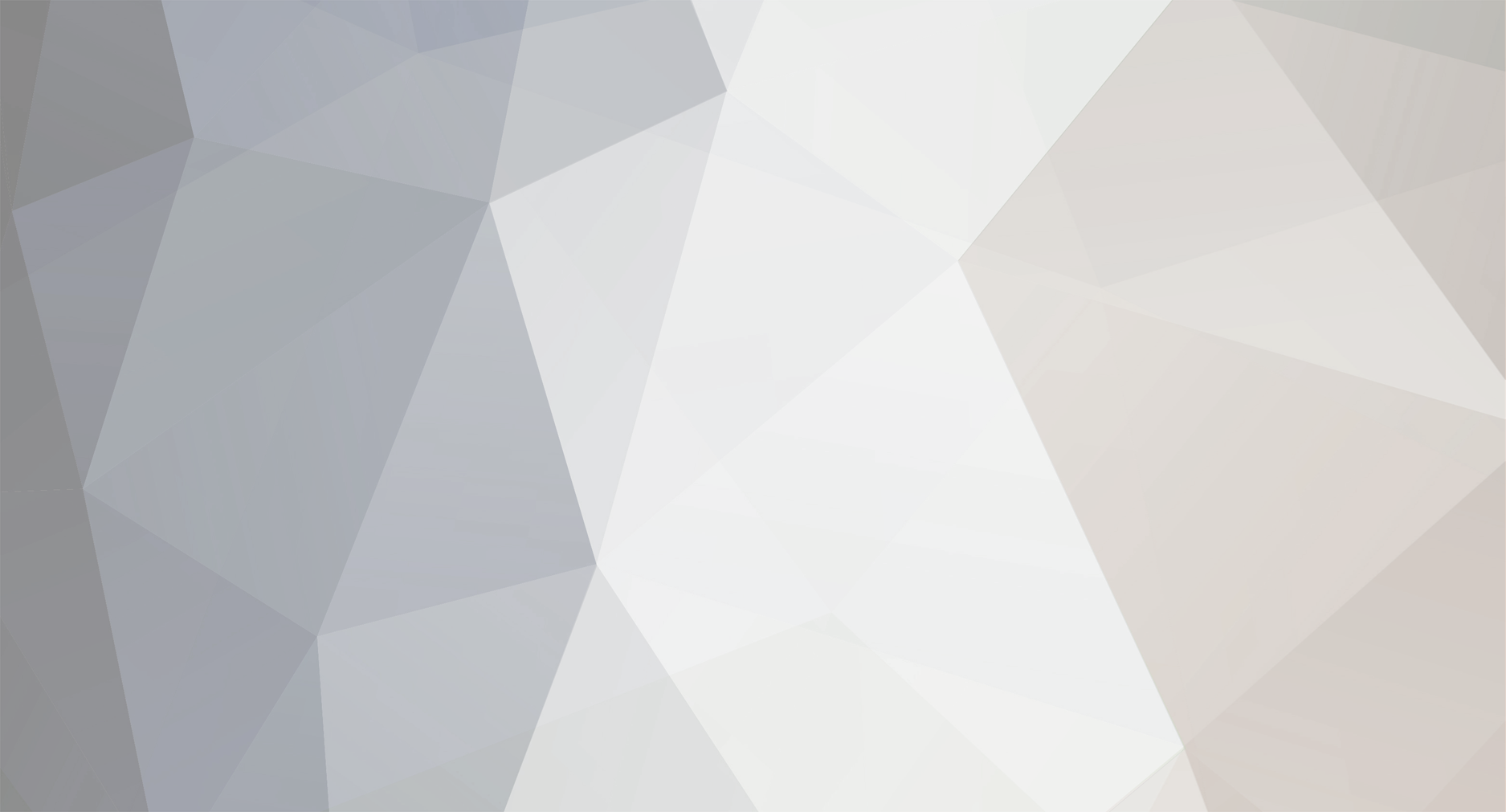
karotta
Members-
Posts
31 -
Joined
-
Last visited
About karotta
- Birthday 08/30/1977
Contact Methods
-
Website URL
http://karotta.hu
Profile Information
-
Gender
Male
-
Location
Budapest, Hungary
-
Interests
Track racing, drifting
karotta's Achievements
Newbie (1/14)
10
Reputation
-
Phar, The black vents will return, but first I wanted to be perfectly sure that the new fenders fit well. After all the epic trouble we had from finishing the first iteration of the custom body kit, all painted and airbrushed to perfection, only to find that it wouldn't fit while on the final suspension any more, this time I decided to leave the cosmetics till the very end. Hence the unpainted fenders, the lack of vents and the fit issues here and there. No, I did not call you, I'm not particularly fond of speaking through telephone anyhow. As for engine management, because of the ITBs I had to go standalone. So everything unnecessary got ditched. I'm glad I went down that road, as the throttle response and the sound is just plain vicious, as you can see in the short video above. Of course I can not be an unpartial juror, but damn me if I've ever heard anything that sounds considerably better. And it rips from idle to 7500 rpm in half a second. The hunger for revs comes partly from the lighter rods, flywheel and clutch, maybe the C8 cams, but mostly from the ITBs with the proper programming. You can see puffs of black smoke on rev-rise, that's due to the huge burst of fuel the engine needs with the ITBs. And that crazy sound is mostly down to the custom long tube headers, I'm so glad we took time and effort to fabricate them.
-
Thanks, although, in all honesty, the current weight of 2220 lbs is expected to raise somewhat. At the time of measuring, the following were not present: - driver - driver's seat - front windshield - FRP hood - side lexan windows - composite splitter, undertray and diffuser - fire suppression All in all, we shall see an increase of 200-300 lbs to reach the race-ready total weight. Still not bad IMHO, but obviously not extremely light anymore. With hindsight, a better thought-out frame could've saved us a good 100 lbs at least, and we could remove at least another 50 from the rear metal bodyshell (I decided to keep nearly everything intact under the rear FRP quarter panels for energy absorption reasons). If I had to do it all over again, we could easily dip under 2222 lbs. What I'm ecstatic about is the beautiful 48/52% F/R weight distribution (unloaded) that will lean some more towards the back once fully loaded. A mild rear bias was an important design goal, and I'm very glad we reached it. This is what a short VQ (pushed somewhat past the stock firewall) gives you. I hope it will handle.
-
The reason we went for a full tube frame instead of further modifying the original front end is that adapting the (rotten) original would have been way more complex. This is how the decision-making project went: I already had a set of rather decent S13 coilovers, a full set of adjustable racing arms and several other goodies from a previous S13 project. (That was actually a real S13) This meant that we had to use the S13 platform. With hindsight, starting from scratch, I'd choose the S14 rear subframe (slightly different geometry with less anti-squat, hence better traction, and same abundance of racing parts). For the front, considering how far we've drifted from the S30 roots, I'd go for a double wishbone setup with a much nicer camber curve than any pimped McPherson. Anyway, due to the parts I had to re-use, my hands were somewhat tied. You may call it an extreme case of automotive leftover cooking. So the rear seemed all set, and the transplant of the complete S13 subframe and all associated arms, knuckles and struts was finished long months ago. That is until I realized that the subframe angle was wrong and that the whole assy hadn't been set higher in the chassis the way we had agreed previously, but was at its factory height relative to the underbody. That's all wrong, because that way, after dropping the body, you end up with wishbones pointing to the cloudy skies giving piss poor geometry. So the front subframe mounts were cut and re-adjusted, and I bought a set of Driftworks rear uprights that fix the geo. Just the way to burn money by mistakes. So that's where the rear stands now. In the front the only thing we knew from the outset was the necessity of the front-steer setup. Seeing how many people have successfully transplanted VQ-s while retaining the original Z steering, we could have (and probably should have) gone along that route. The PCD would be good, the mounts of the S13 coilovers and Wilwood big brakes could be modified to fit and we'd preserve some authenticity. So why ditching the Datsun front end? 1: power steering In a drift car PS is a huge boon (not a strict necessity, I've spent 6 years wrestling a manual AE86), especially as you start shortening steering knuckles to increase lock and effort 2: the freedom to fail With the venerable Z parts out of the equation, we are free to screw up in modern and innovative ways 3: the original uprights got lost Oh well. So after deciding on ditching the factory solution while sticking to the sweet but primitive strut, we had to find an upright that would fit the bill. First it seemed that an old school RWD Ford item would do fine, but eventually we decided to give BMW a chance. It turns out that the E46 uprights are acceptable, if not perfect. Since I lack the skill, the money and the bravery to design a custom item, I went with the Bimmer instead. This brought with it the E46 steering rack, which has OK throw and decent directness. It's certainly not racecar quick, but much better than the unassisted Datsun rack and somewhat better than the S13 original. And we can always speed things up by shortening the steering knuckles, which we won't, for the sake of driver longevity. The most important factor of the rack selection was length: I'm terrified of bump steer. Aardvark has a much wider track now, and with the super butch 90.7 in wheelbase of the S30, it has the handling fundamentals of a real snappy, twitchy beast. To keep bump steer down, we must have perfect harmony between tie rod and control arm. The E46 rack allowed us to have the adjustable lower control arms right were we wanted them. Of course the LCA inner pickup points had to be custom fabricated to position the roll center at a suitable point in space. The BMW upright somewhat limits the position of the strut tower: sadly, the cast upright has a ring that the strut tube goes into, which means that we can't change steering axis inclination without messing up the camber, as we could with a bolt-on upright like the S13 has. All this meant that I had to relocate all the suspension hard points as compared to the factory spec, which in turn meant that it was easier to cut the whole bent and rotten mess of a car away, from the firewall forward. That's how we ended up with a tube frame front. All this struggle for two lowly struts, Colin Chapman would surely laugh. Anyhow, now we are busy tying all those tubes together to regain some chassis strength. The front X-brace holding the radiators will be removable to help servicing and trackside fettling. If the structure seems to be too weak, I'll have some sheet metal added to turn some tube triangles into shear plates, we'll see if that helps. Oh, did I mention that fixing the rear and properly designing the front suspension also meant that those super beautiful fat widebody fenders that we've put hundreds of man-hours into producing didn't fit any more? So a new rear FRP fender was drawn up, this time somewhat wider and more suited to the very low static ride height of the car. I think that the end result is just as pretty, and now the wheels can actually travel up in bump without ripping off the plastic buttocks. This also means that I can't use the first set, which is suitable for cars 6 feet 1â… inches or 187 cm wide. This is it, in its full glory: Aardvark Datsun 260Z IMSA widebody on Flickr I hope the new fenders will be just as great, but in order to tell that, we need to finish the frame and the suspension first, so that Aardvark can actually stand on its own feet again, after all these long months.
-
Hi Phar, thanks for the support. About ride height - or stance - you were just spot on. The front crossmember is 4 inches off the ground. However, all this is meaningless, as the present state is merely a rough guess, with the coilovers set to whatever height they could be set in the few minutes of tinkering we had before the show. The final setup will be done properly on wheel scales. What is sure that the front air dam will have to be modified, that is definitely too high. I plan to attach a removable lower section to it, basically a lip with a splitter for the high-speed tracks. The engine isn't installed, actually the whole car is just a bare shell with a semi-finished roll cage. However, the rear S13 suspension has already been fitted, as has the font, albeit in an incorrect way. So we'll have to modify the front setup again. This is next, together with the engine install. As for the fender vents, indenting the front edge was considered but later deemed unnecessary. The vents are right behind the widest point of the flares, effectively in a nice low-pressure zone, so we could keep 'em flush. This makes for a much cleaner, purer shape. We can easily pull uncut-unvented panels from the mould as well, if later we need for some reason. Originally I didn't consider selling the kit as the whole project is for learning/entertainment purposes, but there seems to be a quite unexpected demand. Still, I'd never sell something that I couldn't stand behind 100 percent, so first we'll have to check how the kit fits on another car to make sure that we haven't produced something that only fits my particularly bent example. Then we might have to make some adjustments, as there are some minor fitting issues, especially where the front fenders and the hood meet. Fiberglass panels this large are quite difficult to fit just perfectly. So the idea is that first I finish my master set, then we'll make new moulds based on the final parts. Then if there's still demand, I'll sell a demo set at a very-very low pice to a well known and trusted Hybridz member who can trial fit and examine it, and tell whether it's worthy of being commercialized or not. If yes, we can produce a small batch. I guess shipping would be rather expensive (or slow), but we'll cross that river when we get there. And finally about the quarter glass. I've had this vision of an integrated, pillarless side window since I first saw a dismantled, stripped Z-shell. I don't want to complicate things as this is supposed to be a race car after all, so I guess I'll eventually cut a moderately big rectangle out of the lexan, and make it slide. Won't be pretty, but will do the job of keeping me alive during a 20 minute stint in hot summer. I've also considered the idea of a contoured cutout that enables a big part of the lexan to be wound down with the original mechanism (like on a Subaru SVX), but that is too much hassle and weight. Good luck with your 2+2 glass conversion, it sounds promising.
-
After long weeks of sleep deprivation to finish it in time, Aardvark was finally ready to be shown to the public at last weekend’s classics show. The shape is inspired by the Datsun 240Z-260Z IMSA-GTU race cars of old. The body is all custom fiberglass, made by OMG Visuals in Hungary. Every single panel, the doors, the roof, everything. You name it, we moulded, hand-laid, sanded and painted it. The rear windshield and the side windows are Lexan, with a very subtle tint to emphasize the shape. Look Ma’, no B-pillars! As the body is strengthened and there is a full roll-cage inside, we decided to do away with the stock B-pillar, to really bring out the gorgeous svelteness of the silhouette. The front bumper is attached by duct tape – if it’s strong enough to hold together LMP-1 race cars at Le Mans, it must be OK as a temporary fixture until we build a proper mount. The quarter panels / wings were hand formed to exactly match the width of the S13 rear suspension underneath with the Rota RBX wheels. Total width is 186 cm or 73.2“, up 24 cm or 10“ from stock. If you are a termite, say goodbye to your beloved queen, for Aardvark is after your ass. You can just about see the factory B-pillars on the orange original car in the foreground. We cut them off, and welded the window surround. The side view wants to evoke the Japanese flag. The purity of the lines is preserved by the lack of fancy colours and decals. The black vents are there to cool the engine bay and the brakes, inspired by the magnificent Alfa Stradale of the sixties. I can barely wait to weigh the car, I’m very curious how much weight have we shed. Proper ladies for a proper old school GT. Knowing how petite Japanese girls are, you can guess how slammed Aardvark really is. In fact it’s 1175mm or 46“ tall, a full 4“ drop, done properly with redesigned geometry and Driftworks arms and coilovers all around. The crowd reaction was just unbelievable. There is no JDM crazyness in Hungary, basically nobody knows what an S30 is. Most people have never heard of the Datsun 260Z at all. Yet people just loved Aardvark to bits. I actually had to sign a scale model kit for a boy who decided to build an exact replica. What an honour! So now it's time to strip the panels and actually build that race car.
-
Welcome back to our lousy garage where the world’s least authentic Datsun 260Z is being restored. If you can call a process where a car is replaced with bits of other cars and clad entirely in foul-smelling fibreglass restoration. Semi-finished fibreglass front Last time we left off with the suspension nearly finished and the chassis ready for the roll cage. Alas, we were wrong. Now, if the idea of combining a Ford steering rack and uprights with Driftworks Nissan S13 control arms sounds a bit insane, your intuition is just right. It is insane, but it almost worked. Until, of course, science kicked in the door and slapped us in the face with spreadsheets of ugly numbers and terrifying graph plots. I’ll spare you the details, they’re tiresome. The bottom line is that our first take at the front suspension sucked big time. Mostly for two reasons: - There was no camber gain in roll - The front experienced horrid bump steer along the calculated suspension travel If by now there is a sizeable speech bubble above your head with the letters WTF in it, you should never – and I mean never – start cutting and welding a car’s front suspension at random. We thought we’d had a rather good understanding of how things worked and yet we screwed up real bad. Lesson learnt: to build a proper race car, you need friends way smarter than you are. Thankfully this description fits my friend Tschangow quite perfectly. S13/Ford hybrid front suspension So Tschangow came one evening, armed with a pen, a notepad, and a tape measure. Three hours later he had the whole suspension system sketched up. Another few hours later a wireframe simulation was created in CAD. By the next morning I knew we were in trouble. Our suspension looked OK at standstill, but once it started moving along the arcs defined by its arms, mean things started to happen. Things like front toe changing by 6 degrees during bump. If you’re wondering what that means, picture the car approaching a corner. You take the perfect line, aim for the apex, and as soon as cornering forces build up and the outside front suspension gets compressed (or you hit a bump), you find yourself hanging on for dear life as the car tries to spin and bite your hand off in the process. This is bump steer. Random illustration of cleverness Bump steer is caused by the suspension arms and the steering linkage travelling along different arcs. Normally, they should be parallel and equal in length, so when the wheel moves up and down, steering is unaffected. However, if you mess up the geometry by installing a rack from a different vehicle and have tie rods pointing at silly angles with the control arms, your front wheels will have a will of their own. And they will win. And you will crash. Slightly too wide at the front So it was back to the drawing board. But of course we don’t have drawing boards. We have a pile of greasy parts in the backyard and a strong tendency to improvise. If you’ll remember, all this trouble is because we’ve transplanted the whole S13 suspension under the Datsun, but the old Z must have her steering rack in front of the axle line, as there is no room behind it because of the big-ass VQ35DE engine that comes from the Nissan 350Z. This deprives us from the chance of using the great GeoMaster2 knuckles, which would’ve been our primary choice. If you take the steering rack from a rear steer car (such as the S13) and put it in front of the axle line, you end up with the road wheels turning in the opposite direction to your steering wheel. Now, that’s pretty hilarious when done by Buster Keaton in a Model T, but rather frightening in real life. So we needed a steering rack that had the same dimensions as that of the factory S13 item, but turned in the opposite direction. Nino Karotta with an RHD S13 steering rack looking mean However unlikely, it was actually me who came up with the ingenious – and in retrospect pretty obvious – idea to actually use a rack from a right hand drive vehicle, turned over, and placed in front of the axle. Remember, I’m from continental Europe, so I need the steering wheel on the left. An RHD rack would place the steering wheel at the wrong side. Simply turning it over would cause the wheels to move opposite to the steering. But moving it to the other side of the axle gives us just what we need. So if anybody fancies the same transplant in the UK, Australia, or even in Japan, just buy a decent, used LHD rack and flip it over. OK, enough of all this oily nonsense, let’s look at the exterior. That’s Aardvark’s painfully beautiful custom widebody with the Rota RBX’s all around. The reason it’s so pretty is that the car is due to appear at a classic car show on the 15th of April. This means that all this blessed backyard engineering was brought to a screeching halt two weeks ago and the empty shell transferred to OMG Visuals, where we tried to tidy up the semi-finished fibreglass panels and create some more from scratch. The idea is to finish and paint the shell before the show, have the car displayed, gain some inspiration from all the people falling over, drooling and crying from its surreal hotness, then take it back to Driftgarage where we’ll remove the fibreglass panels once more and actually build the car. Desperately wanting a bumper As far as I can tell we have all the parts assembled, so after the show there is only the small matter of finishing the roll cage, the stitch welding of the unibody, the installation of the suspension, and bolting in the 350Z’s engine, tranny and a few miscellaneous ancillaries. If everything goes according to plan, we’ll be putting out smoke this summer. Let me know if you like what you see!
-
Okay, so now we have a rear end as low as a beaten dog’s morale and as curvy as J Lo’s. What’s next? Naturally replacing those ugly, unadjustable control arms with some orange specialty items. As the whole suspension comes from the S13, a Pro Handling Pack from Driftworks shall do the trick. Besides the added sex, the adjustability they provide will enable us to set up a decent geometry and compensate for any minor inaccuracies in the transplant of the subframe. That's where the VQ35DE's sump goes The front end is much trickier. You see, the Nissan 200SX has the steering rack behind the front axle line. Unfortunately – or rather very fortunately – we’ll be having a lusty big V6’s oil pan right where that steering rack is supposed to reside. Now we could’ve chosen to keep the Datsun’s original forward placed rack and front facing suspension uprights, but that would’ve given us headache with the connection of the Driftworks CS2 coilovers and the 300ZX brakes, besides the small matter of depriving me of servo assistance. I do not intend to sound too sissy-ish, but having an unassisted rack in a wide-rubbered, high-castered drift car is a major PITA. As in pain in the arms, of course. Ford/Driftworks hybrid front suspension So Leslie (the guy who does all this fantastic work while I’m typing away on my laptop) came up with the ingenious idea of using Ford Sierra/Scorpio uprights and power rack. At first my mouth turned sour a little, as I preferred the idea of an all-Nissan trans-generational hybrid, but after seeing how nicely everything turned out, I had to accept he was right. Spot the Ford! Leslie tested the setup by bolting the Driftworks Nissan S13 CS2 HSD coilovers in his own Sierra, pounding it around a short, tricky sprint rally rack. Amazingly it worked pretty well. What’s more, he ran the setup for a few additional weeks on the scarred streets and highways of Hungary without any spectacular accident. That’s how I ended up having pieces of Cologne in my Datsun. Cusco strut brace and lower brace So for now it seems that the Ford/S13 hybrid front suspension fits rather well. The strut towers were transplanted from a chopped-up 200SX. The factory distance between the towers was taken care of by tying them together with a Cusco strut tower brace. This ensures their correct position relative to each other. Leslie used this same trick at the back as well. The present setup gives us some positive Ackermann geometry with average steering angle – not enough for backwards entries at Tsukuba Circuit, but enough for a season’s worth of moderately competitive fun. And we’ll be steadily experimenting with settings until we get it just right. Inspiration Now that the suspension is roughly in place, it is time to install the roll cage and properly stiffen the chassis. And, while cramming all that scaffolding into the tiny cockpit, we must try to figure out where the fuel cell goes – and more interestingly, where the exhaust system goes. One thing is for sure: we are not putting pipes under that car. No way. Stay tuned.
-
It’s been more than three months since I’ve shown you the progress of our Nissan 350Z-powered, 200SX-suspended Datsun 260Z build. Well, as they say around here, slow work takes time. But when it comes to transplanting the heart and limbs of two different animals into a third beast, one really must measure twice before the singular cut.Rota RBX 9,5" x 17 ET-19As you probably know, building a race car usually starts from the ground up, that is by choosing the tyres that you are likely to run and the rims to mount them to. This is because wheel/tyre choice has a profound effect on everything else, and what you may fit under the arches is usually dictated by the sanctioning bodies. No such luck/constraint here. In drifting and time attack you can nearly use whatever you find, while in any other established forms of motor racing you are disqualified by the mere idea of mix’n matching together a car from such distinct relatives. So wheel choice got down to issues of taste and practicality. As both the Datsun and the S13 use 4 x 114.3 wheels, and I have my brakes set up for that stud pattern as well, it was decided that we’ll be sticking to that. Fat 4 pots with unnecessary spacersThe current front brakes are 280 x 32 mm discs with 4 pot callipers from a 300ZX Twin Turbo, and chances are I’ll keep them for the time being. These require at least 16“ wheels. Diameter-wise 15 inches would suffice, but the fat callipers usually hit the spokes of anything under 16“. As I think that oversized rims with thin-film rubber look rubbish on old school cars, anything above 17“ was ruled out. That’s when I spotted the painfully gorgeous Rota RBX-s in the Driftworks webshop. I’m slightly worried by the immense width and the large offset, but I’ve always been a sucker for shiny fat lips (hi there, Angelina), so I decided that engineering doubts shall be cast aside. We’ll fix that screwed scrub radius later.200SX rear suspension under old Datsun While waiting for the wheels, Leslie finished the rear subframe transplant. That was the easy part: after making sure that the subframe is straight and level with the chassis, he cut and modified the Datsun’s rear chassis rails to accept the S13 mounting points, that were plasma cut from a dismantled car’s floorpan. The subframe is installed roughly 2 inches deeper (higher) within the chassis so that the rear suspension arms keep their near stock geometry while the car’s body does get closer to the ground. This way you can lower a car without making the control arms point up too steeply, which usually hurts handling.Wide waist + widened panels + flares = nearly wide enoughThen the wheels came. Then I came, for they are mind-boggingly beautiful. Then we trial-fitted them, and realised that the custom fiberglass widebody rear quarter panels were not nearly wide enough. Then I ordered a set of ZG flares, to fit over the widened over-fenders. Those finally covered the rears. Sort of. Almost. And so it happened that I ended up with a chopped up Datsun as wide as a 911 GT2. You just gotta love that.