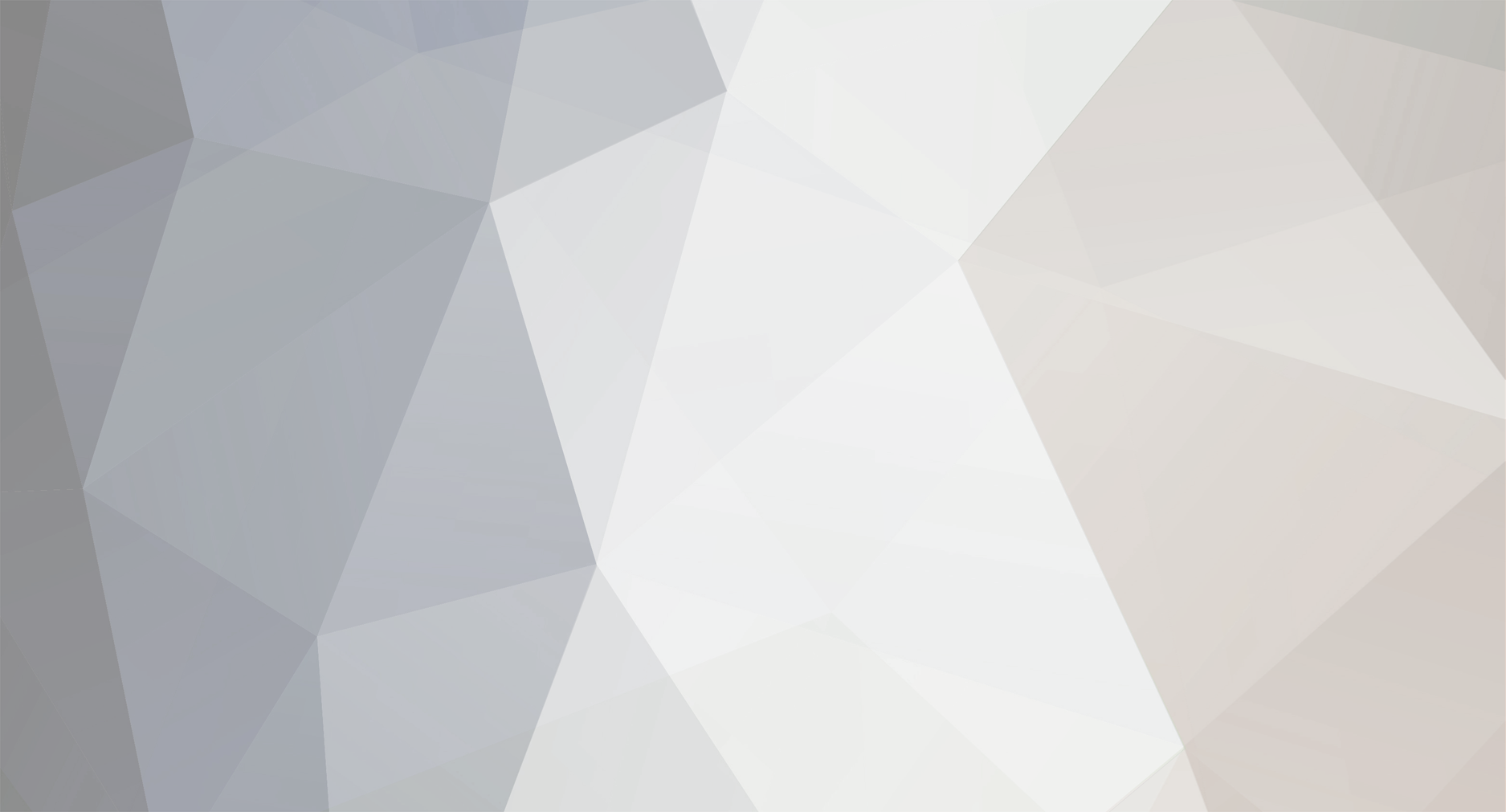
vertebraille
-
Posts
17 -
Joined
-
Last visited
Content Type
Profiles
Forums
Blogs
Events
Gallery
Downloads
Store
Posts posted by vertebraille
-
-
Nice! There is someone local to me selling front and rear setup for 500. I may pick it up too..
I would ensure that the ring/pinion gears aren't shredded or anything, I popped the back cover off before I bought mine... I'm going to buy the front from the same guy I bought the rear from, I just didn't have room for both, I really like the A-arm design of the Vette front subframe. I'll get to that eventually though.
-
Hey guys,
Quick update. I've been working my ass off. The Navy isn't great for downtime... Anyway, I scrapped the SVT rear idea. I bought a C4 Vette rear subframe for the car... It's a Dana 36 which, I know, isn't the greatest... However, I only payed $200 for it and it's in great shape, I plan to mess with it for now and if I eventually break it- Oh well I'll drop the money I would have spent initially on an 8.8 and upgrade to the far beefier Dana 44. the definite upside to the Vette assembly, is that it is a very similar design to the stock system and IMO will be an easier retrofit, as well as being way, way lighter(ie: I can pick the whole thing up by myself. I'll post actual weight once I get my scale back from the neighbor). I promise to post pictures as soon as I get a chance.
R/
Murph
-
Holy Balogna Batman!
I agree, more tire is needed. I'm a little envious of how nice that rear end looks... I just tossed the one I had, it was trash('99 model that was rusted almost completely out and when I opened the chunk up, there was so much metal flake I couldnt find the gears). I'm saving up to get a better specimen. I'm not planning to go with the full frame rebuild like that. If I had the time, and the Navy actually payed decent, I would do exactly that though. As it is I think im going to graft some "rails" under the car and tie them into the subframe and the tube front I'm currently attempting not to ruin.
-Murph
-
Absolutely, this is going to be a slow project, but I will try to document and report as I go along. There's a lot of those little " while I'm at it's" though. However, I've pretty much decided that the 8.8 subframe will be unique and a great weekend killer to take on. As far as narrowing the rear end, I may do that at a later date but for now I'd like to try and fit the whole original unit in there. If it turns out to be impossible then I'll look into tackling the fabrication of entirely new upper and lower control arms, the plethora of odds and ends that will need and getting custom half shafts made.
-Murph
-
"but with a good set of halfshafts its damn near bulletproof and, I think, fully capable of handling anything my limited budget and an LS2 can throw at it"-Same goes for the R200 that is in there.
It's a lot easier to find new carriers and change ratios with the 8.8 though IMO. I also got the car as a shell, and therefor, lack an existing rear to work with. Hence my decision to go a different route.
-
Seriously?
I would have expected some interest in this subject. At the very least, some flaming responses as to the functionality/brokea**ness of the Ford 8.8 rear.
I'm going to slog ahead with this, and see if I can pick one of these up in my area(Great Lakes, Il) for a reasonable amount of money. I will then attempt to install it without reducing it to so many metal shavings on the garage floor.
-Murph
-
Looks great so far. I'm thinking I need to build one of these. However, I have a pretty substatial pile of steel behind the house, and I think I might start from scratch. We'll see. Your welds look pretty good. However, I think, the second close up, you might focus a little more heat on the "bottom" edge. Or the surface of the metal you added. The weld looks like it could use just a bit more penetration. but I'm pretty sure it'll be fine for a light car like the Z.
-
Hey Guys,
I've been tossing around the idea of modifying and installing an entire Cobra 8.8 IRS subframe in my 280z. I've taken a few rudimentry measurments for the project, and it appears that the overall track width only increases by about six inches. whille the overall depth of the assembly is about an inch "taller" than the stock 280z rear setup. Im thinking that with some large flares and a fair amount of offset that the tires would fit with out any issues. As far as the subframe bolt up, I was thinking to shorten the mounting "ears," for lack of a better term, and fabricate corosponding hard points on the car for the bushings. Sure it weighs more, but with a good set of halfshafts its damn near bulletproof and, I think, fully capable of handling anything my limited budget and an LS2 can throw at it. I don't have any pictures right now as I was using a friends IRS assy and we're now in two different states. I've searched for this and the best thing I've found was modifying the stock rear to accept the 8.8 center section. Thoughts? Questions? Comments? Concerns? Anything would be appreciated.
R/
Murph
-
It's seam sealer. I pulled up the top panel and scraped the inside with a pick, then hammered it back down and welded. The inside of the wheel wells was especially tough, but you can do it and get a decent result, just takes a lot of time and effort, and I'm not sure the payout is worth it in retrospect.
I've started doing the same thing. Peeling up the edge and cleaning the s**t out of it then tapping it back down and welding. Time consuming and ugly as sinning with a one legged hooker.... Since weight isn't an issue to me I'm probably going to lead the seams and clean them up a bit after their all welded, before it gets painted.
-
I generally tend to drag the tip from the puddle. Being left handed this make it a little easier for me to stay straight. I also have roughly a 3/8" "stick out" which I thought was about normal. I've managed to get the blow through from happening by moving just a little faster. however, now the welder is popping more than I think it should.... Oh, just in case someone decides to ask, I cheched the manual and the welder cover and my polarity is correct.
Murph
Also: the manual does not cover "datsun super-variable thickness steel" so dont even look.
I figure, that by the time I finish seam welding these front strut towers, I'll have my issues figured out and one hell of a ugly fender well. Hey, if it runs who cares right?
-
Try 3.25 and about 2-3 on the wirespeed for Datsun sheetmetal. You have to keep moving, but my Millermatic 135 doesn't blow through at that setting unless I do something wrong.
If you're going around the top of the strut towers, there are two pieces of metal in there. There is a top piece of sheet which is very thin, and the strut top itself underneath which is probably .100" thick. If you're trying to weld to the thicker stuff you need to use a setting that will penetrate the thicker material. Without looking, my gut says put the heat on 6 and the wire speed on 5 (you can check the inside of the access panel to verify that). Then you'll blow through the thin stuff almost instantly and have to work your way back to the thin layer with the puddle.
Sweet thanks. I turned down the gas and shortened my stitch welds a little. Little less heat in one spot. I just welded a cutout steering column bearing from a 99up cobra into a 5.0 for a friend and it went just fine. Tomorrow I will try the 280's towers again. I think Im going to cut out the tops and weld in some camber plates.
Thanks for the tips guys.
Murph
-
Hi,
I have a Millermatic 130xp mig welder running .030 solid wire and a CO2 Shield gas through. Im having some issues with blowthrough. The welder has four amperage settings. 1 and 2 are just too low and 3 is having issues with not penetrating the top plate but four just blows through without blinking...? Im running my CO2 at about 30-35psi... If anyone has any info or tips to correct these issue I would appreciate it greatly. Oh, I'm currently seam welding the front strut towers. Just to give you and idea of material thickness.
Thanks,
Murph
Also: I've been playing with my wire feed speed but it's not seeming to have much effect on the above problem but just for infos sake the welder has settings from 10-90 for wire speed infinetly adjustable between those points.
-
Thanks for all the advice guys... Here's the deal, I went to my friendly local autozone and borrowed a "pitman/tierod end remover" its currently (rod end 1) (remover 0) this thing is on there... I plan on replacing this stuff but Im not sure what I need to save... so far I just removed the suspension minus the strut tube bottom/steering arm. tried to take a better picture, but my camera is dead and my phone sucks.
thanks.
-
Hey,
Here's my problem... I'm removing my front suspension and have everything disconnected, except the tierod. I removed the cotter pin and castle nut. However, it still wont budge. Am I missing something? I know its something stupid and I'll feel like a idiot, but I can't see what it is.
thanks in advance,
Murph'
-
Thanks, I figured as much but none of the pictures I found really show much detail.
-
Okay, so...
I'm pretty new to this forum and the "old" z thing, as opposed to the z32, so this question might sound stupid.... I really like this(I think its member flatblack280's) style airdam, as opposed to the curvy rock panel thing that was on my '78 280 or the hideous(opinion) msa type 1,2,3 valances. Does that replace the stock bottom pan(aka the three-piece sheetmetal thing under the front bumper? Or attach to it via some unexplained and mysterious fasteners?
thanks,
Murph'
SVT Cobra 8.8 IRS in a '78 280z
in Fabrication / Welding
Posted
Also, I'm not sure how different the ZX dimensions are, but on the 280z, even with a proposed 4 inches of fender flare per side- I still plan to narrow the track width of the C4 setup by at least 6 inches. Keep that in mind when you look at it. I have access to a TIG welder so the aluminum won't be to work. If you don't have one/have access to one labor could get expensive, as the "mustache bar" and diff cover are one solid piece on the Vette and will probably need to be shortened as well.