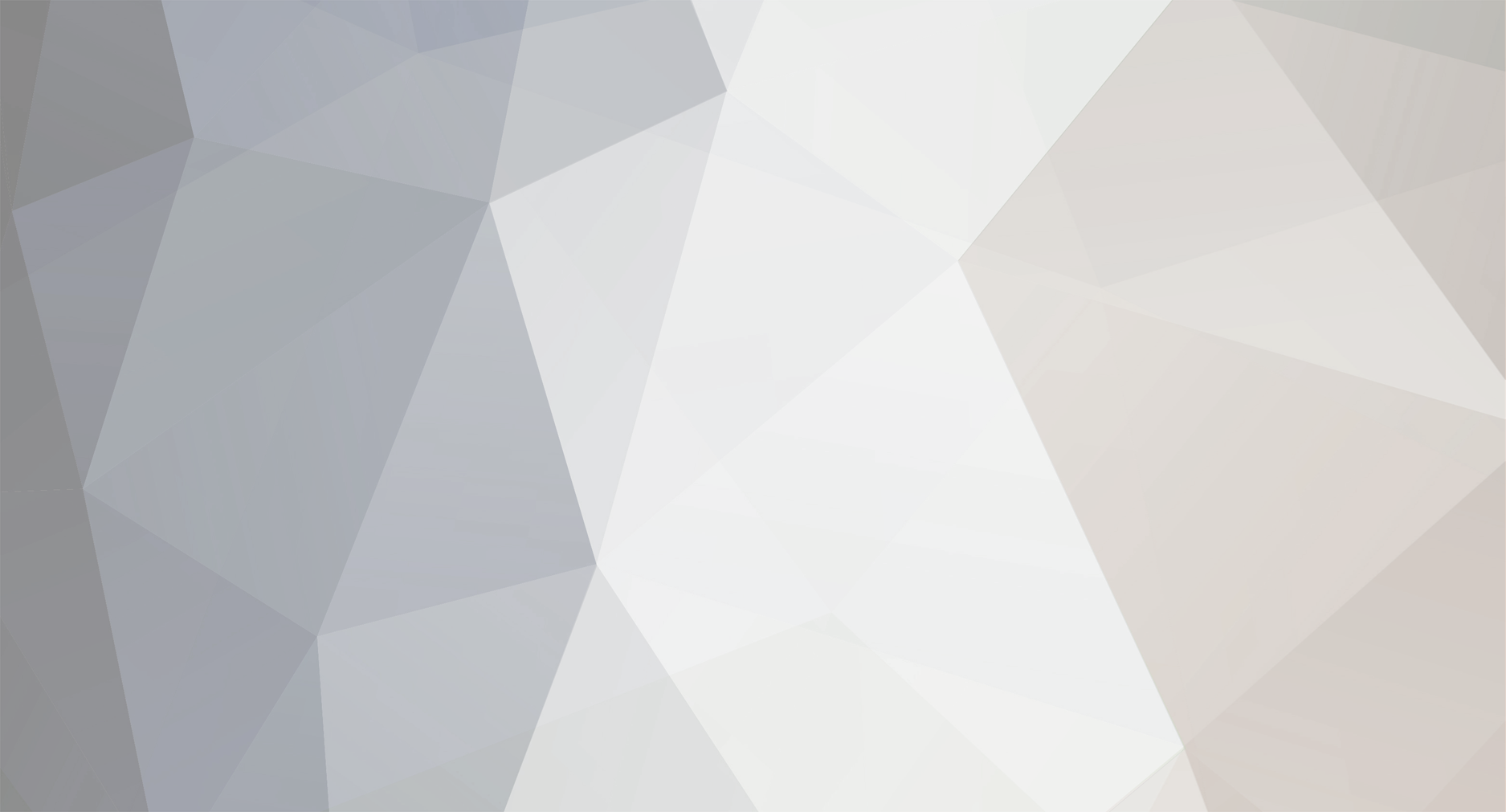
Jlhalsey3
Members-
Posts
27 -
Joined
-
Last visited
Profile Information
-
Location
Orient, New York
Recent Profile Visitors
The recent visitors block is disabled and is not being shown to other users.
Jlhalsey3's Achievements
-
I have had some experience with R200 being noisy, especially when coasting. Had it rebuilt w same ring and pinion by a local shop, just as noisy. I located a low mileage R200 and had the ring and pinion transferred to my case by the same shop. It is now dead quiet. Very happy with it. The challenge is finding a ring and pinion in the right ratio that isn’t worn out. I couldn’t find any new OEM, i think there are some aftermarket available in Japan but very expensive. I got lucky and found a R200 seller who claimed the unit was out of a low mileage car he was parting out. I am using the OEM rubber trans mount that mounts under the front of the diff. Previously used a solid billet mount there but changed to rubber in quest of lower noise. Helped a little but the big change was switching out the worn ring and pinion gears. Not sure if there is a way to test or inspect the gears to determine wear, my old gears looked ok but when i found a unit from documented low mile vehicle ( i think 30k ish miles) i made the decision to purchase. Luckily it worked out great.
-
I ended up TIG welding the broken threaded portion back onto the stub axle. It fitted well back into the original fracture and the weld took well. Torqued the nut to 80 ft lbs, well below spec but didn’t want to risk breaking the weld. I now have about 1000 miles on the repair and it is holding up. Note I don’t drag race the car or drop the clutch for wheel spin starts. I do however use full throttle going up through the gears. This is a V10 Gen II Viper motor with 500 ft lbs of torque and a T56 Tranzilla from Rockland Standard Gear, R200 with Quaife. Based upon my experience and given the difficulty of finding replacement stub axles, maybe this is a route others could take with broken stub axles if the break is at the start of the threads.
-
on Monday I will try Joe at Chequjered Flad and also Futofab.
-
Well, struck out, T3 OEM axles were 25 spline and i need 27 spline. I tried to call Whitehead Performance to see if they actually have their chrome moly stub axles in stock but their voice mailbox is full and couldn’t leave a message. Anyone have another number, maybe a cell, for the manager or owner? Has anyone attempted a weld repair on a broken stub? Maybe a big chamfer at the base of the of the threads where the fracture occurred, may loose several threads, then TIG weld the stub, turn down in a lathe any weld material that sits proud of the shaft diameter? Last resort of course.
-
Thanks for the input. I’m in no mood to replace the rear suspension to gain a better stub axle solution. I have ordered T3 5 lug stock 280z 27 spline stub axles. May have to replace the wheel studs, not sure what length they come in but i need 2 1/2” studs to clear the thick rotor spacers that my Arizona Z setup uses. We’ll see how well the T3 OEM axles last, if they last as long as the first ones, I’ll be back here in 15 years asking the same question.
-
Old thread but current problem. Snapped the left side wheel stub axle on my Viper powered 1972 240Z after approximately 6,000 miles of use. It failed in the threaded portion, not the splines. I have the early Modern Motorsports setup with 280ZX Turbo CV axles and R200 w Quaife which is holding up just fine. What is the current thinking regarding the strongest solution available for the stub axles?
-
Further update. Took the car on a 100 mile trip with expressway speeds. Once speed reaches 65 mph, a strong high frequency vibration is felt, causing the rear view mirror to be blurry. So doing some further trouble shooting. It appears the culprit is the forward U joint operating angle which is 3.4 degrees and does not match the rear U joint angle. I re-drilled the transmission rear mounting bracket to lower the rear of the trans 3/8”. Little change in the angle and I can not go lower at the tail shaft. I think probably spacers under the motor mounts would need to be considered but not sure there is clearance under the hood to move the engine up. That the driveshaft is so short (16 1/4”) also contributes to the bad geometry. So after some research, I am having a custom driveshaft fabricated with a non-plunging CV joint at the front and conventional U joint at the rear. In theory, this will eliminate the vibration due to the excessive operating angle of the front U joint. Quite expensive but seems to be the best way forward. Also found another R200 differential with hopefully a noise free ring and pinion, will have my Quaife transferred over. It’s a 3.70:1 ratio, not a 3.91 but close as I could find. Car is now apart for driveshaft and diff swap, hopefully for the last time. Will post an update when it is back on the road.
-
I am looking for a 3.91 ratio ring and pinion gear set for a long nose R200 differential. Must be in excellent condition, will need close up photos of the gear teeth, especially ring gear drive and coast faces. Will also consider ratios in low 4`s. Thanks
-
Well, its been many months and I have continued to make progress with my V10 Z. Car is back on the road after months of rewiring under the dash and drives nicely. There is still some driveline vibration at higher speeds but much improved after i had the drive shaft and rear wheels rebalanced. The u joint working angles are still not under 2 degrees after much fiddling with the trans rear mount and the differential mounting. But the current focus is the differential, after rebuilding with new bearings it still whines on deceleration and has more backlash than I would like. I need to find a nice long nose ring and pinion in excellent condition, preferably 3.91 or thereabouts, to cure the whine. Something in the low 4's would also work as the T56 is double overdrive in 5th and 6th. If anyone has one they would like to sell or can lead me to someone, that would be awesome. I just missed one on ebay today that would have filled the bill.
-
Yes, car is on a 4 post lift. I have ordered a transmission jack from Harbor Freight but I may try moving the car forward on the lift and using my floor jack while I wait.
-
Progress, took the axles, circlips and differential back to the shop that rebuilt the differential. They were able to insert the circlips into the differential thru the axle openings and slide them down until they engaged the retaining groove. Didn’t take them long. I wasn’t able to watch this part but they said they used a screw driver to get them started and then a socket to push them down the splined part. This is exactly what I was trying to do but couldn’t. Then they inserted the drivers side (shorter) axle and with a mild tap with a mallet, it seated fully. Then using two screw drivers, one prying on each side of the axle, they were able to pop the axle back out again. All good. Then came the passenger side (longer) axle with the rectangular cross section circlip groove. They were worried the circular cross section circlip would either not engage this axle or if it did engage that it wouldn’t come out. This axle went in and out just like the other, to my great relief. At some point, I may attempt to disassemble the inner CV joint on my sole “long” axle, and transfer the stub axle to one of the “short” remanufactured CV axles I have so many of so both axles will be fresh. So I will now see if I can rent a transmission jack and install the diff, cut the Technoversions/RT poly mount to the correct size and hope the new OEM lower mount fits and see what the pinion / driveshaft angle delta looks like. Thanks again for all the help I have received here.
-
Well, if I was still in LA finding a specialist Datsun differential shop would be no biggie. Unfortunately, I am now in a lovely rural area which has tons of marina’s but very few automotive specialist shops.
-
I am planning to take the axles and diff back to the shop and let them install the circlips. They are telling me that the clips are installed on the axles. I want them to install them and then insert the axles into the diff. Then pull the axles out so I can be confident I can install and remove them in my garage. If they have trouble with this approach, I will ask them to disassemble the diff and install the clips that way. Another wrinkle I have noticed which may cause a problem is that the axles that came out of my car have a rectangular cross section circlip groove. The replacements I have purchased have a more of a V shaped groove. The circlips I bought have a round cross section which would appear to fit the V cross section axle grooves and not my original axles with the rectangular cross section grooves. Perhaps why my axles had no clips at all. Does anyone know if there is a different clip for rectangular groove axles and the part number for same? By the way, fyi, I have now bought two pairs of 1981-1983 280ZX Turbo remanufactured axles from different eBay vendors, both based in China I believe. Both sets contained equal length axles, the shorter ones for the drivers side. They seem to believe the axles are the same part and part #. On my R200, the passenger side depth from the outer seal to the circlip groove is 5/16” greater than the driver’s side. Appears using a short driver side axle in the passenger side will prevent the clip from reaching and engaging the groove. Thanks
-
I am very sure they are a short and long pair. I measured the depth from the outer oil seal to the bottom of the splines in the differential: driver's side 3 13/16", passenger side 4 1/8", so 5/16" difference. Same as the length difference of the axles. The problem with running the shorter driver's side axle in the passenger side is that the circlip will not reach the retaining groove in the differential and therefore won't lock in. I will check for binding when I get the diff and axles back in. Right now I'm having a helluva time getting the circlips started down the splines within the diff. I am prying on one end of the circlip with a screwdriver to get it started inside the splines but it keeps popping back out. If I can get it started square in the splines, I'm sure I will be able to push it down the rest of the way with a 32mm diameter socket. Just can't get it started and I don't want to pound on it with the socket without already having gotten some of the clip inside the splines. Suggestions welcome. Have written to Quaife technical support for tips well.
-
Update: I now have the R200 back, rebuilt by a local shop. Getting ready to install the circlips by inserting into the splines within the differential and pushing down with a 31 or 32mm socket until they pop into the grove towards the bottom. Hopefully no drama with this and also when I insert the axles hopefully with no more than a firm shove. Due to some shipping misadventures when purchasing a remanufactured pair of 280ZXT CV axles from the source identified here earlier, I ended up with two drivers side axles.These are the shorter axles, about 5/16" shorter than driver side. Was going to reuse my passenger side axle with the new drivers side axle but after reading so many threads about Z31 axles being too long, I am now wondering if the 280ZXT axles also may be too long for the 240z chassis with R200. Can anyone comment on whether this is the case and therefore I may be better off using two drivers side axles? Thanks!