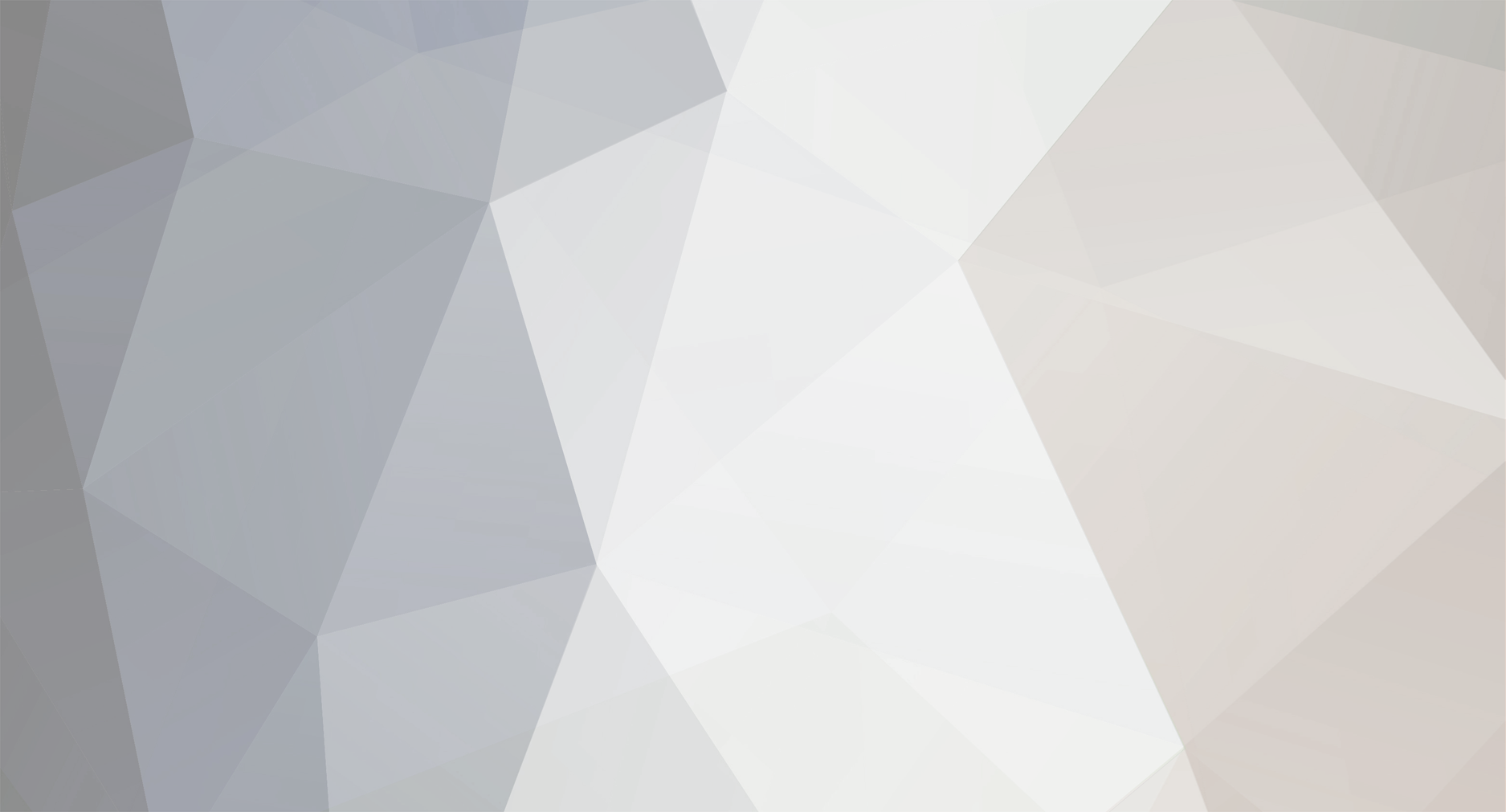
toolman
Members-
Posts
550 -
Joined
-
Last visited
-
Days Won
15
toolman last won the day on July 8
toolman had the most liked content!
Profile Information
-
Location
honolulu
Recent Profile Visitors
The recent visitors block is disabled and is not being shown to other users.
toolman's Achievements
-
Heavy Duty frame rails and connectors
toolman replied to toolman's topic in Gen III & IV Chevy V8Z Tech Board
Fourth of July 2025 Pearl Harbor Fireworks and Car Show- This Joint Military Forces Fourth of July Celebration was held at Pearl Harbor Naval Base. It consisted of Two County Western Bands , Big Fireworks display and Car Show. There were over Two Thousand People in attendance from 4PM -9Pm. My 240z won 1st Place Trophy in Classic Rod Catalogue, The Event ended with 15 minute Long Fireworks Display over Pearl Harbor. Next- Finishing Details on the 8.8 Conversion -
240Z RESTORATION PARTS IN THE USAI I found this video by Larry Chen about the relative new source of 240Z restoration parts. Their inventory covers body parts,interior plastic panels, grills,etc. If any one have tried their parts, please let us know concerning fit,quality,price and customer service. Their Website pic shows a 240z salvage yard so they might also sell used 240z parts. the company name is Resurrected Classics in Auburn, Georgia.
-
Part 2-More 240Z Restoration- Body Work is mostly done utilizing Oxygen Acetylene Gas Welding. This method of welding was mainly used to repair automotive body repair. I learned this method when I was 15 years old and used it until the 1970s when Mig Wire Welding came in. The Mig Welding is a much productive method as it applied the heat faster and welding with less heat distortion to surrounding metal. However, I still use this method in certain applications to this day. Notice- Use a Small Torch Flame and Thin 1/16" Brass Rod. More Bodywork to come-
- 1 reply
-
- 1
-
-
This 240z restoration in Japan demonstrates bodywork using basic methods and tools. These videos show restoration methods that most Do It Yourself people out there who do not access to more expensive body working equipment could still do the work. The restoration using these methods would take more time but have satisfying results. This Body Man does a lot of Vintage Cars Restoration in Japan. Race Cars are also done. Please give your comments so I can find more videos that will help you restore your Vintage 240Z or other car models. Toolman
-
Thanks for Repairing my PassWord Problem. Is there anything that I need to do prevent this problem from occurring again? Toolman
-
Heavy Duty frame rails and connectors
toolman replied to toolman's topic in Gen III & IV Chevy V8Z Tech Board
Sorry for the delayed reply. Was having difficulty with my Password and trouble posting. Thanks Administration for correcting problem. Disc brake and Hand Brake Installation- First, Important Notice-The Invinclble Extreme 8.8 Differential Conversion Kit requires the use of 2015 to 2024 Mustang GT Rear Disc Brake system. All related Suspension Parts were created to work with these parts. Check carefully if any alternate brake parts are used for fit and function. Otherwise, Different Parts may require Modification at some level. I utilized NAPA Replacements Brake Parts (Calipers, Rotors and Upgraded Pads) for 2019 Mustang GT I painted the Calipers and Mounts with Polyurethane Bright Red to improve their appearance, Stainless Steel Brake Lines(from Amazon) were used. Brake Line Adaptors from EBAY connected the Male OEM fittings to the Stainless Lines. Brake Line Adaptor installed with OEM Clip to Stainless Steel Brake Line Hand Brake Modifications- The Hand Brake required a little more fabrication to function properly. I found these adaptors on Ebay although they were not designed for this particular job. The Above Two Parts were used together to adapt the OEM Hand Brake cable to the Mustang Caliper Hand Brake Cable Mount. The Cable Bracket with roll pin must be Slit to allow the cable to fit into the Threaded Cable Mount. After being inserted into the Cable Mount, the Bracket with Roll Pin is reassembled on the Cable. The Slot can hammered closed afterwards(or even tack welded) The Caliper Hand Brake Cable Mount had to be enlarged to 5/8" from 9/16"(use Unibit) to fit the Hand Brake Cable Adaptor. Insert Cable into the Nut assembly with JB Weld Epoxy to fasten cable to prevent movement. Allow 24 hours for the JB WELD to harden. Drill out Adaptor to 5/8" to provide Cable fit. /inserting Cable into Adaptor with JB Weld to hold it. I Assembled all together With the Hand Brake completely Loose, Slide Cable Roll Pin with Cotter Pin over the Caliper Lever Arm while pulling cable. Note-Stainless Brake attached to Caliper with Bolt(with copper washers-above and below. 0 The Hand Brake Adjustment Threaded Rod must be shortened by 2 1/2". Just use a Hack Saw to shorten a non- threaded portion of the Adjustment Rod. Pic of the Hand Brake Adjustment Rod in Trans Tunnel. The Shorten Adjustment Rod will move the Hand Brake Arm forward and make it easier to access. Final Hand Brake Adjustment was made when all Four Wheels were on the ground to the point the vehicle could not be pushed be hand. Wheel Spacers- With my 17" x 11 1/2" Wide Wheels and Deep Offset, the Inner Wheel Bolts would contact the Ca[iper Outer Face. US Wheel Adaptors provided 1" thick wheel spacers which get about 3/4" Caliper Clearance. I can probably shaved the Inner Side of the Spacer about 1/2" to bring the clearance down to 1/4" Clearance if necessary. Bigger Brakes with Larger Calibers and Vented Rotors would probably fit now(trial fit to be sure) if you go to LARGER Calipers and Rotors. US Wheel Adaptors can make spacers to whatever spacing that you might need. Also, the spacers can convert to different wheel mounting patterns. Wheel Inserts with 5 Lug and 4x 4 1/2" Pattern Matt Cochan at LOVE20BEE IN California found Watanabe Wheel Inserts for me. I sandblasted and took them to a local PowderCoater to powder coat. Extended Lug Nuts- Because the Narrow Wheel Lug Pockets, I went to Ebay to purchased Extra Long and Narrower Lugs. Almost all of these 14mm x1.25 lug nuts had to been retapped with Exlarge Long 14mm x 1.25 Taps because of bad threading. Extra Long Wheel Lug Nuts on Extended Wheel Studs. Next-Struts and Exhaust Pipes -
Heavy Duty frame rails and connectors
toolman replied to toolman's topic in Gen III & IV Chevy V8Z Tech Board
Driveshaft Modifications and Driveline Alignment- I sent my old Driveshaft to be lengthen as old R200 differential was longer than the New 8.8 Differential. I got the new measurement by inserting the Front U-Joint all the way into the T-56 trans. Then measured the distance between it center of Chevy U-joint to the center of the Front U-joint of the 8.8 Ford Differential. The Machine Shop will make the shorter by 1 1/2" . This allows space to remove the Driveshaft when it is installed. Note-How large the Ford Adaptor from Sonan is. Driveshaft installed-Rear View Front View-Driveshaft After installing the New Driveshaft was installed, the Drive Alignment was done to double check. I used Two Methods -1-using Spicer Drivetrain Products Application from the Web. It requires the use of a Digital Protractor(mine was Klein Digital Protractor from Home Depot. I think it was about $30 but I bought awhile ago. Front u-Joint Measurement. Second-Middle of Driveshaft Measurement. Third-Front Differential Measurement After entering the Three Readings, the Application gives a Pass or Fail Result. In this case, the Result was "Pass". The Second Method you use the Tremec Tool Box Application. I used my IPHONE to enter the angle measurements. The Result was "Pass" also. Half Shafts Installation- This pic shows the difference between the Datsun Half Shafts and the Ford 8.8 ones. Left Side(shorter one) Half Shaft installed. . View of Both Half Shaft Shafts Left Side -Shorter in Length. Next-Rear Disc Brakes and Hand Brake -
Heavy Duty frame rails and connectors
toolman replied to toolman's topic in Gen III & IV Chevy V8Z Tech Board
Once, you installed the Differential and Cage with the Support Bracket into the Two Vertical Mounting Bolts, the Two Forward Differential Mounts can be installed into the Transmission Tunnel. Left Mount Right Mount Note-Earlier 240z has mounting bolt holes close together so drilling an another hole maybe necessary(call Vlamir for assistance), Important Fact------My New Ford Motorsport Super Duty 8.8 Differential came with the Large Aluminum Pinion Flange so I had to fabricate a New Crossmember for clearance problem. I decided to modify the Original Nissan Differential Crossmember. Pic shows Sonan Adaptor on the Pinion Flange. Pic of 8.8 Differential with the Old Style U-Joint. Note the Close Clearance between Flange and Incredible Extreme Crossmember already. Original Nissan Transmission Crossmember taped and marked for metal cutout on top area. Cardboard Template of Aluminum Flange marking Side Cutout. Using 4 1/2" Cutoff Wheel to cut out Top Section of crossmember. Top Section of Crossmember removed. Both Side Sections were cut out to form the Lower Round Shape. Finished Crossmember Side View View of bottom of Modified Crossmember. Finished and Mounted Crossmember. Next-Modified Driveshaft and Driveline Alignment. -
Heavy Duty frame rails and connectors
toolman replied to toolman's topic in Gen III & IV Chevy V8Z Tech Board
Differential Installation- I had additional work on my house after painting it. Sorry again for posting delay. First, I Trial Fit the Rear Differential Support and the Cage before trying to install the Differential. The Trial Fit is make sure all the Fuel, Brake Lines and Hand Brake Cable does interfere with the Differential. Some Early Model 240Z , Nissan widened the Front Differential Mounting Bolt Holes. So make sure your Differential Mounts fit or you must slot existing holes or drill additional ones. Right Side Front Differential Mount Old Mechanical Transmission Jack for Installing the Differential and Support Frame Together. Installing the Differential- The Best Way to install the Differential is to preassemble the Differential and Differential Support with the Two 14mm bolts. This way you just have to align the Two Main Vertical Bolts with the Two Round Mount on the Support Mount. I used a old mechanical Transmission{ screw version) Jack. One person can install the Differential by himself. If you try to install the Differential after mounting the Differential Support by itself, you need other person to screw in the Two 14mm while you lift that 100Lb Differential- a difficult task. Also, early 240s with a Spare Tire Well, the well is close to the Differential Support on the Left Side Bolt and this 14mm can not even be inserted in. Some owner install Fuel Cells which are much smaller and allow the Left Bolt to be installed. The only problem with the Preassembly Way is the Two 10mm Outer Bolts in the Center of the Differential Support can not be installed with the Cage. So I drilled their internal nuts to 3/8" hole all the way thu the box crossmember. Then, install Two 3/8"x 4" long bolts from the top. Two 2"x 3" x 3/16" steel plates to spread the load over the crossmember top. Two 3/8"NC nuts under the Support Frame to complete this modification. Some people probably don't install this bolt but it is a structural part of this car. Pic of the Two 3/8" X 4" Long Vertical Bolts through the Cross Member. Closeup View Pic of the Nut inserted between the Cage and Differential Mount. Left Side View of Left Side Nut for Vertical Bolt. More Rear End Modifications coming up. -
I found this video on visiting a Metal Supply Shop in Japan. While doing a S30 Fairlady Restoration, the Body Man needed more sheet metal to finish his job. This video shows a side of car restoration that most people never see- where the sheet metal actually comes from. The rest of the video shows detailed 240z body restoration It shows how to repair difficult body areas of the 240z. I hope you guys find this video interesting. Toolman
-
1978 Datsun 280z No Acceleration Above 4000 RPMs
toolman replied to Kad77's topic in S30 Series - 240z, 260z, 280z
If your SU carbs were not modified to allow for the larger displacement motor, you might have a fuel problem. Meaning the carb needs to provide a richer mixture to run properly. You can try smaller SU metering rods which would provide a richer fuel mixture. But doing this may still not provide a rich enough mixture as the SU bore size maybe too small. -
Heavy Duty frame rails and connectors
toolman replied to toolman's topic in Gen III & IV Chevy V8Z Tech Board
Ford 8.8 Super Duty 8.8 Differential Installation- First of all, I want to apologize for taking so long to finish this posting. I had to paint my house and had some other people's projects to help them with. The first thing that I had to do was to find a method of jacking the front end of my 240z high enough to use high jack stands. Because of the low ground clearance of my Rocket Bunny Front Air Dam and Low Vehicle Height, even my 3 1/2" Low Clearance Floor Jack would not fit. I solve this problem by purchasing a pair of 3 1/2" Car Ramps. They cost about $36 on Amazon. raises vehicle by 3" These ramps were about 28" long and would work on low riding vehicles. Short steep ramps would not work. They are very light weight and can be sacked together (taking a small storage space). jacking cross member The Ramps worked perfectly as my floor jack fit under the Front Cross Member easily. With the Car raised on Four Jack Stands about 6" off the ground, disassembly of the rear suspension can now take place. I designed my exhaust system for easy accessiblty. It consists of Three Sections-One -Front Motor Exhaust Pipes, 2-Middle Section with "X" Pipe after the transmission and Third- Rear 90 degree Exhaust Pipes with Two Turbo Mufflers. The pipes were also, connected together with V Clamps for fast disassembly. Next, the Two Rear Control Arms must be removed from the Strut Spindles. First, the Threaded Cross Shaft must be removed. The Tapered Shaft retaining Pins must be removed. With the Locking Nut removed, the Pins are removed by tapping them cafefully upwards. now, the Threaded Cross Shafts must be taken out. Because of Corrosion and lack of Lubrication, these shafts usually are difficult to remove. You can not hammer them out as both ends has threaded ends and hammering will damage the threads. ZDEPOT sells the Removal Tool but I made mine own. The tool consists of an Internal Threaded Rod which screws to the Threaded End of the Cross Shaft. The Larger External Tube( 1"OD" acts like a spacer of the Threaded Rod. A Large Nut on the opposite side of end of the Threaded Rod operates like a Forcing Screw to pull the Cross Shaft outward. I welded a proper size Lug Nut to the other end of the Threaded Rod. See Posted Pics for Size and Dimensions of this tool. Metric Lug Nut welded to one end of the Threaded Rod 15/16" Nut( pulling nut) placed on the opposite end of the Threaded Rod Removal Tool installed on Cross Shaft Rear Suspension removed With the Rear Suspension and Differential Removed, install the Differential Support Bracket on the two Long 17mm Mounting Bolts for Trial Fit. This test fit checks if any Fuel and Brake Lies and Hand Brake Cable are in the way. In my case, the Fuel Lines had to be extended and Hand Brake Cable modified. Differential Mounting Bracket Trial Fit- Next-Differential Installation -
A Excellent Video on A Complete Body Restoration of a 240Z car
toolman replied to toolman's topic in Body Kits & Paint
This video is Part 6- This video follows the complete Paint Job of the 240Z. It covers disassembly and rebuilding of the Front Suspension. Some of rebuilding of suspension parts from scratch are interesting but normally beyond normal rebuilding process. But the video was made overseas(probably Northern European Country) where obtaining a Datsun Front Ball Joint is not easy like going to Auto Zone in USA. Though, seeing how parts can be created from scratch is informative. -
Silvermine Motorsports -Ford 8.8 Rear End Conversion for 240z
toolman replied to toolman's topic in Drivetrain
Wedge, Check out my Jan 30,2024 post in Heavy Duty Frame Rails in Chevy IV section. I discuss why I decided to go with INCREDIBLE EXTREME 8.8 Super Duty Differential Conversion Kit. Toolman -
For Information and Installation details on Incredible Extreme Ford Super Duty 8.8 Differential Conversion go to: V8 ZForum-GenIII & IV Chev V8 Z Tech-Heavy Duty Frame Rail and Connectors on Page 19. Toolman https://www.facebook.com/story.php?story_fbid=502465925737642&id=1065043032290757