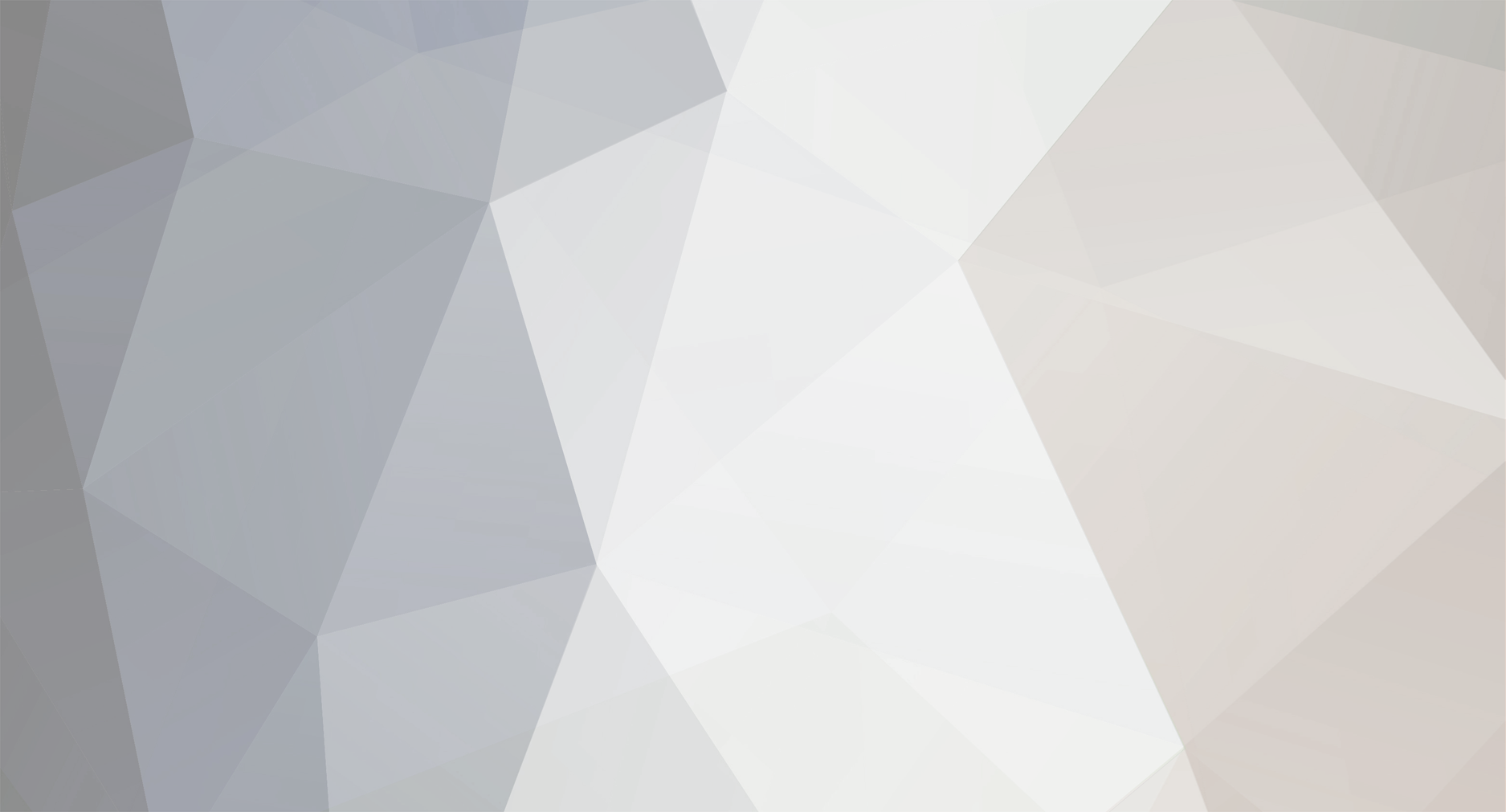
dimsum
-
Posts
78 -
Joined
-
Last visited
Content Type
Profiles
Forums
Blogs
Events
Gallery
Downloads
Store
Posts posted by dimsum
-
-
Yeah...I agree with both of you, too. Shorter bolts seem like the better way to go.
Now, I need to figure out the bolt specs and find shorter, automotive-grade ones.
-
On my Fidanza I had to add a washer to the bolts, they bottomed out before they snuged up. Check to see if that might have been the cause of your problem?
I noticed that the holes in the Fidanza flywheel are not as deep as in the stock flywheel. The bolts do not go in as far. With my clutch and flywheel, the bolts are too long to hold the clutch snug as well.
Is it better to add a washer, or try to get shorter bolts?
I did a search, and it sounds like most other people do not have this problem.
-
I'm interested in one from the next batch. Wish I didn't miss out on this one, because my car is already in pieces.
Roostmonkey, you have PM.
-
Torqued the bolts to 15 ft/lbs, did not bottom out and everything fit perfectly.
Dragonfly
SHOWOFF!
Heh heh...just kidding. It looks good. Does the clutch cover need to bottom out on the flywheel, or is it ok to have some gap between the two? I forgot to check my old one before I took it apart.
-
Has anybody else experienced this with a Fidanza aluminum flywheel? I would expect Fidanza to drill the holes to the same depth as the stock flywheel, but I guess that might not be the case.
On my Fidanza I had to add a washer to the bolts, they bottomed out before they snuged up. Check to see if that might have been the cause of your problem? -
They told me that the threads on the hole will remain untouched. I don't think the hole will need to be retapped.
I read about the process online, and it did seem pretty neat. Supposedly it is precise to 0.0005 inches.
EDM is cool, kind of like a really precise CNC plasma cutter. It should be able to get the bolt out. But will require the hole to be re-tapped. -
One machine shop I spoke to recommended using electrical discharge machining (EDM) to get the bolt out. Supposedly, this is the best way and is least likely to damage the threads on the flywheel.
I've never heard of EDM before. Then again, I've never had a bolt break off on me before, either. Does anybody have experience with EDM? Can anybody make a recommendation?
-
Everyone always rags on easy outs. I've never in my life had one break on me.
I noticed a lot of people on this board don't like Easy Outs. I've never used one but have to admit I have my hesitations based on other people's opinions.
-
Thanks for the article. I'll check it out.
http://www.madelectrical.com/workshop/broken-bolts.shtmlI have never had luck removing broken bolts with an extractor until I read the article above.
I've already pulled the flywheel. I am very inclined to take it to a machine shop if I can find one in the San Jose area. Shouldn't be too hard, I guess.
The machine shop should be able to remove the broken bolt without damaging the flywheel, right?
Another option is to pull the Flywheel and take it into a machine shop
I never thought about that. I was a bit worried about overheating the aluminum as well.
Another option is to weld a nut onto the top of the broken stud. Careful you dont' overheat the aluminum flywheel.
-
I was bolting the clutch cover onto a Fidanza aluminum flywheel, and the cover wasn't quite flush with the flywheel. I figured that as I tightened the six bolts, they would push the cover nice and snug against the flywheel.
As I tightened, one of the bolts snapped.
Not good.
Now, I have part of a bolt stuck in my flywheel. There's about 1/4" of the bolt exposed. I tried using vice grips, but couldn't get the bolt to turn.
Any ideas?
-
Ahhh. Thanks for the clarification. So, if you use the regular paper gasket, then you wouldn't use an additional liquid gasket/sealant?
-
I spoke to my Datsun mechanic over the weekend, and he recommends not using any sealant on the intake and exhaust manifolds as long as everything is straight and mates up correctly. That seems to go against what most people are saying on this board.
-
I'm about to transfer all the external components from my old engine with a blown piston ring to a rebuilt engine. I was wondering what kind of gasket sealant I need to use for things like the intake manifold, exhaust manifold, water pump, coolant lines, etc.
I did a search and found the following thread on the Chevy V8 forum:
http://forums.hybridz.org/showthread.php?t=67732
Does anybody know if the GM sealant is still the best way to go? Should I use that on all the holes that use a paper gasket? Is there one gasket sealant for the intake/exhaust manifold and another for the coolant or anything else that doesn't come in contact with fuel?
-
My brother and I always wanted to replace a strut tower bar with one fabricated out of wood or another material that would permanently deform when placed under stress. We could take the car out, drive for a bit, and see how much load the car actually places on the bar.
If the wood cracked, or even shattered, it should show an example of how much compression or tension the bar had to endure.
This is probably something best done with the rear bar, so if it does shatter or splinter, little pieces wouldn't get into moving parts.
-
Before you go and find your calculator...
The type of tubing and the way it is formed will greatly affect it's performance... You need a lot of information about specific tubing types...
The other issue is that you have only a general idea of how much force will be applied... this will vary from car to car...
All of this is true. It's difficult to calculate the exact amount of load and determine the optimal bar diameter and wall thickness. I'm sure most aftermarket companies just make something that is way thicker than necessary, so they don't have to crunch numbers.
Other than using a stress/strain gauge, I'm not sure how to calculate the loads applied to the strut tower bar.
However, it is fairly easy to look up the modulus of elasticity for the type of metal you plan on using. Some web sites will even give you specific numbers based on how the tube was manufactured.
-
I have a question that maybe one of you can answer. I'll try to be as clear as I can but I'm not sure of the proper terms for this. A curved bar would be loaded so that it would bow, but a straight bar would be loaded so that it would crush should those loads become great enough (which they won't in a strut bar application). Is there a middle ground between crushing and remaining straight....kind of like the plastic state that aluminum goes into right before it melts? Or will the bar simply remain perfectly straight until it reaches its yield strength and then collapse?
Wow...you made me dig up my old lab manual. Couldn't find my class notes, though, so I can't give you as much explanation as you might want.
Even a straight bar will bend under enough load. It will not crush, like an aluminum can, even if the loads are perfectly aligned along the bar's axis. I cannot remember why this occurs, but it was demonstrated to me in my materials lab last semester. We loaded aluminum and steel bars 5/8" in diameter, from 6" to 21" in length, and they all bent. None of them "crushed."
Once the bars reach their yield strength and begins to bow (or deform), though, the amount of load they support either remains constant or even decreases a little bit. When the bar starts to bend, it becomes a spring, and not a rigid structure any more. So, if your bar requires 2,000 lbs before it will bend, once it reaches that point, it will not support any more than 2,000 lbs (and most likely a bit less than 2,000 lbs).
How would one calculate the yield strength of bars loaded in this manner? Since it wouldn't have the tendency to bow, then does that enable us to use extremely thin wall (light weight) tubing for the strut bar and other non-sanctioned chassis stiffening members loaded in this same fashion?You can use the following equation to calculate the yield strength (critical load) and predict how much force will cause the bar to bend:
critical load (yield load) =
EI(pi^2)
L^2
where:
E = modulus of elasticity, or Young's modulus (specific for each type of material, http://en.wikipedia.org/wiki/Young%27s_modulus)
I = moment of inertia (specific for bar shape, http://en.wikipedia.org/wiki/List_of_area_moments_of_inertia)
pi = 3.14159
L = length of the bar
According to the web site, for a round, cylindrical bar,
I = 0.25 x pi x [(outer radius)^4 - (inner radius)^4]
Thanks for jogging my memory.
-
I might have to do that in the spring when I get her ready to drive. I am just curious.
If you do find out the cam profile, post it up here. I'm curious. Thanks.
-
isn't that what dry sump systems are for?
A dry sump system ensures the engine always has oil to lubricate the parts (external oil storage instead of an oil pan). One of the additional benefits to dry sumps is that the crankshaft isn't sloshing and cutting through the oil in the pan.
-
Update: I found somebody to come by and do the welding for $500. He's going to cut out the old floor pans and frame rails and weld in the new ones in my garage, with the car on jack stands. I have my reservations, but I will be there to watch him do the work and make sure that everything gets lined up properly.
Auxiliary, if you're still interested, I can let you know about the quality of this guy's work. I also had somebody to offer to do the work for me in his shop "after hours" (without the owner knowing) for about the same price.
I also bought some Rust Bullet to make sure the new pans and rails stay nice and clean.
Do I paint the Rust Bullet on before or after the parts are welded on? I already painted the inside of the rails because they will be inaccessable after they are installed. What about the other parts, though?
-
I have the same problem on my Prelude because of a bad thermostat. The thermostat is stuck in the open position, so the fluid is constantly circulating through the radiator. This cools the fluid too much, especially on winter days, causing the low temperatures.
-
I've used the Toyo RA-1 tires before, and I liked the way they stuck on the track. I would recommend them.
-
btw, this is what a typical rusty Z looks like:
I clicked on the thread to see how my car compares with the "typical rusty Z." It turns out my car IS the "typical rusty Z." Hahaha
Sigh...
-
Thanks for the diagrams. Based on the work involved and your recommendation against doing this type of modification, I think I'll leave the rails as they are.
-
Careless, I wish I could do the work, but I don't have the skills, tools, or space to weld the frame. I figure something like this is better left to the experts.
The two places I went to for quotes were White Oaks Auto Body, and Central Bodyworks, both in Campbell, CA.
They have to cut out the old floor pans and frame rails (yes, the floor pans are pretty badly rusted, too) and then weld on the new parts. I'm going to try and get another quote or two, but it's hard when the car is immobile.
Bolt snapped on flywheel
in Drivetrain
Posted
I examined the Fidanza and stock flywheels a bit more, and it looks like the stock flywheel holes go all the way through the plate and stop at the gear teeth for the starter. The Fidanza flywheel has blind taps that are a few mm shorter.
Fidanza said that they haven't heard of this problem before, but they offered to drill the holes through the aluminum flywheel if I send it back to them.
I wonder if this is just a problem with my clutch, and the clutch cover I have (Centerforce, stage 1) is not as thick as others.
The stock clutch cover bolts are M8 x 1.25, 20 mm. I ordered some shorter ones (16 mm) from this place called Mr. Metric in San Jose. We'll see if these do the job. Otherwise, I'll have to send the flywheel back to Fidanza.
Now, I'm wondering if it is better to drill the holes through the flywheel or use shorter bolts.