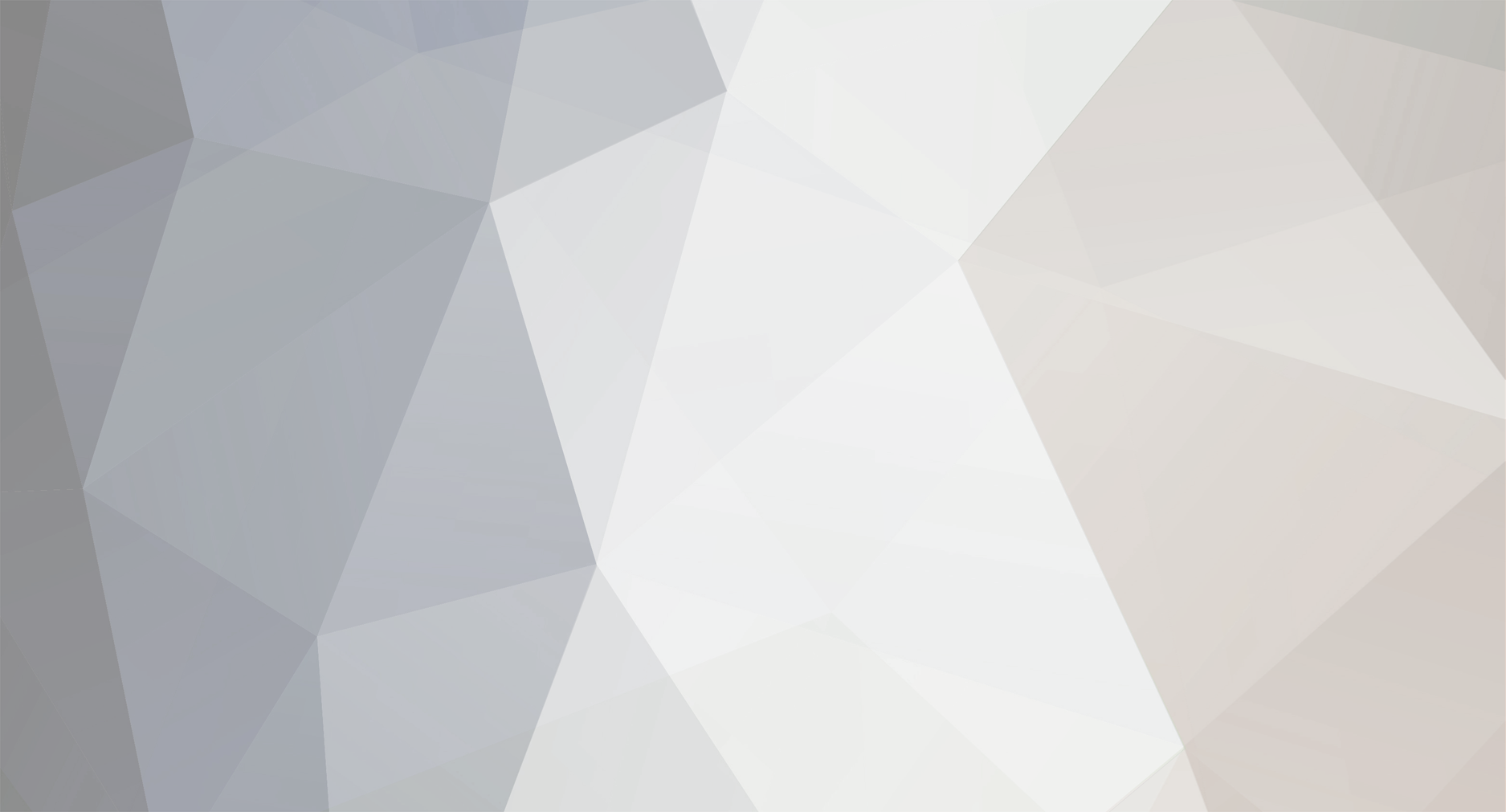
pkz
Members-
Posts
37 -
Joined
-
Last visited
Content Type
Profiles
Forums
Blogs
Events
Gallery
Downloads
Store
Everything posted by pkz
-
MidnightCafe- I bought the carbs on ebay from a few different sellers (they come in sets of two but all the ski-doo snowmobiles used two TM40s in the early 2000s years). I lined up all the carbs the other day, right before I was about to leave to cut tubes, and realized that they spacing between carbs is WAAAY to much. I did a comparison to triple webers' manifold and determined that I was definitely going to run into intereference problems with the distributor. Since the carbs come preassembled in sets of two- I'll have to chop down the spacers between them and run smaller T-Fittings than stock when I go to reassemble it all. Here's what the carbs look like before they're separated. Separated the Carbs (Sorry for the blurry photo, lighting in my room sucks) Floats and main jet: Now for the pesky throttle shaft... It's tapped, and the slide mechanism is fastened using a countersunk phillips-head screw. Now, if I'm going to machine my own throttle shaft, I'll have to run 6 tapped holes lined up precisely to ensure the throttle positions are all the same. I have access to a decent drill press, centering bits, and maybe even the cross-hole jig I'd need to do this properly. However given my machine experience is limited- and that having the throttles lined up is highly critical to this functioning properly am I better off having a professional do this? Something else I hadn't thought about running a single shaft. If I run a single throttle shaft with pre-tapped holes, I'll have no way to adjust the relative flow-rates of the carbs. In theory this shouldn't be a problem, because the throttle position holes should be properly matched up so all the throttle positions are the same. In practice though, I'm worried there will be discrepancies in flow and if this is the case I'm going to kick myself later if I build something that can't be adjusted. Maybe I'm better off trying to join the ends of the throttle shafts using end couplers like this? http://www.mscdirect.com/product/details/35465731?src=pla&cid=PLA-Google-PLA+-+Test&CS_003=7867724&CS_010=35465731
- 48 replies
-
Everyone- thought I'd check back in. Just to clarify I took on this project so I could have something unique and fun to drive- pretty subjective goals I know but it's really all I have in mind. Partway through the process I realized that the 30mm carbs weren't going to cut it and bought 40s. Now, the second-hand 40mm carbs I bought cost me a total of 200$, Steel for the manifold cost me another 60$. I know before I have anything close to driving I'll need to weld everything up, build a throttle linkage, work out fuel delivery, and then work out jetting. That said, I think I've still got a chance of having this project come in at well under the 1000$ mark and be way more fun to drive than my original 73' flattop carbs currently do. I've read up and even TonyD never liked the 73's (save for throwing them on a mill and doing some experimenting, from my reading). As for my own time spent on the project I see this as more of a fun challenge than actual work, especially if I can learn something in the process. All that said, I fully understand where all the criticism is coming from, especially given that I was less than clear about what my goals were for this project from the onset. Djwarner, thanks for the info on carb sizes. I think my 40's will work, but another source reinforcing the same things people have been saying here is good to have. By the way, carbs are Mikuni TM40 flat-slides.
- 48 replies
-
Lots of good advice guys- Thank you! This project has been on the backburner because of school, but tomorrow I'll be back in the shop sanding the mold, and laying down the last bit of filler resin (one of the gaps was a little hard to fill). I'm definitely seeing your point when it comes to sanding the female surface. However I think with a little more time and effort I can finish the mold to the surface I want. I'll admit sanding a male plug then pulling a fiberglass splash (probably using a gelcoat or something similar) would have been ideal, however seeing as I've got about 200$ of plastic into my current female mold, I'm going to stay the course and see how it goes. Sorry progress has been so slow. Rayven, I'm actually in the San Luis Obispo area until a few days in late november, otherwise I would take you up on your offer. Thanks!
-
Hello again! I've been back at school so available time for my project has been very limited. I've figured out the new carb spacing, and I'll be cutting tubes this weekend. I've also realized that I'm going to be pushing my welding capabilities a bit- especially where jigging is concerned. Could anyone offer some advice on jigging? My experience is limited.
- 48 replies
-
OldAndy- What's the benefit of pulling a splash off a plug in terms of surface finish quality? I understand that once the plug is prepped and a splash is pulled the splash requires no preparation other than release film, however wouldn't the plug still need to be sanded to the same quality that I need for the normal mold? To my understanding, the master/layup tool process is used to make cost effective production tools and to overcome temperature requirements. For example: a foam or plastic plug could be used as a master cure a tooling prepreg layup tool, which can then be post cured freestanding to withstand significantly higher temperatures and more heat cycles than the original foam mold. I've also heard this as a way to overcome costs associated with manufacturing the mold. Ie depending on size/shape (and other production factors) of the part the plug/layup tool process can be significantly cheaper than machining from a huge piece of metal. Is there a benefit from a purely surface finish standpoint from using the plug/splash method however? It's possible I'm overlooking something. Very excited to see your dash! Also, I figure it's worth a mention that my part is going to be room temperature cure. PKZ
-
69 Honda- I really like the rubber inserts. I'll shop around once I have the final part off the mold. I've bonded all the mold pieces together and sanded and epoxy coated the surface. It will still need some more sanding before it's ready to be prepped with wax and mold release. I'm hoping to have the sanding done by next week and hopefully be ready to lay up a part soon thereafter. Some pictures of the mold before bonding, and one in the 3D printer. As you can see we really pushed the size limits of the 3D printers. And here are a few of the mold prep in action: Sanding, epoxy coating, sanding again, and so on. The 3D printed PLA was pretty easy to sand, and more surprisingly was thick enough on the surface where we didn't have to worry about sanding through the shell. And a close up of one section of the mold after the 1st epoxy coat (it went on a little too thin, thus the areas where the print lines are still visible)
-
I'll go with the square tabs (assuming I get a good part off the mold). Could you explain the trim ring? I think a picture will go a long way here. Also- I've got an update: The mold is halfway done printing. The second set of pieces came out a bit rougher than the first (the surface had some ripples in it) but nothing that can't be knocked down with some sandpaper or a small file. Here's a picture of the mockup of the first 4 pieces of the mold. I'm bonding them together with some composite envisions epoxy (they're curing right now). I'm really pleased with the quality of the composite envisions top coat epoxy. I coated a test piece of 3d printed PLA and the surface came out glassy smooth. I haven't decided whether to use the epoxy coat or the polyester gel-coat for mold surfacing but I will almost certainly coat the final part with the top clear coat from composite envisions. I'm still really happy with the quality of the 3D printed mold. Hopefully next time I post pictures the mold will be complete and ready to coat!
-
Hey guys- I really like the suggestion to use rubber lining on the cupholders. Unfortunately it's too late to mold it for anything OEM (molds have been printing since Wednesday). However, I've got an exciting update! I've printed the first two pieces of the mold! The next 2 are in progress. I'm really happy with the print quality. I'll still have to do a generous surface coating of epoxy, which I'll test out this evening. It's hard to tell from the picture but the pieces connect very flush as well. More updates to come in the next couple days! PKZ
-
LanceVance- I'm actually not really into the Nissan push start switches. I really like the look and feel of the push button start I currently have. I'm sure the Nissan one works nice but I actually prefer the custom look of mine. I modeled in some cupholders in the back. I appreciate the offer for the armrest, but the mold has already been printing for a couple hours. Here's the final model I'm printing up. Currently no plans to sell these, as I'm not sure how my fabrication quality stacks up to what people here would want. I'd like to think I'm alright at carbon fiber manufacturing, but certainly not a professional- once the first one comes off the mold I can show some pictures and if I get some interest then I can make some to sell. Molds are going to take almost a week to print to get good print quality. But they're under way!
-
The 3D printers I have access to aren't huge, but I did a test to connect a couple pieces together. My buddy printed out the pieces and said he had to pry them apart with a knife in order to separate them, even though we didn't use any adhesive to hold them together. Since the surface quality of the 3D prints isn't phenomenal, I'll be giving the mold a heavy surface coat to cover up the little tiny ridges before doing final surface prep. I'll probably use duratec to seal/surface the mold, although I'm going to investigate epoxy hot coating before making any final decisions. 1969honda, thanks for the input! I like the idea of matching the molding to the switch profile. Yesterday I added another switch and moved things around to make it look a little more organized. Today I tried a few different things with the ignition switch molding. First off was the rectangular matched molding: I also tried creating a lofted feature between the existing circular hole size and the rectangular profile of the switch. I was (and still am somewhat) set on maintaining the 3 circle pattern for the top row of switches... I really liked the aesthetic of having the slightly larger inset to the left of the other two (as seen in the first picture). It had a great asymmetrical look I'm not very pleased with how the "lofted" inset looks. I tried changing around the size of the circle relative to the rectangular molding to see if that would change anything. I think at this point I'm going to go with the rectangular molding, as it looks much cleaner than the other two. It shouldn't be any harder to mold IMO. I'll have to add some soft fillets to the corners but given how small the insets are I think the carbon (2x2 twill) will drape just fine.
-
Sorry for the confusion. I'm considering machining inserts for the manifold runners to run a taper from the end of the manifold up to the head. Given that these are pretty small, it wouldn't be a huge ordeal for me to machine them. I currently don't have the capability to machine the heads. Carbs should arrive tomorrow!
- 48 replies
-
Hey everyone, I decided to replace my center console for my 73 240z. The old one has some cracks and chips and the previous owner went at it with a drill and some wiring to install some custom switches that apparently he never got around to connecting. Anyway, I decided that since I have some carbon fiber manufacturing experience that this was as good an opportunity as any to try my hand at some design work and try making a custom carbon fiber part for my Z. I started with a scan of the old console- a couple buddies of mine have a free 3D scanning software that we used to get a really rough scan of the part- Converted to an STL and imported to solidworks: Next up I went about roughly reconstructing the old console. I had to do this all visually in solidworks since STL doesn't allow you to modify or "work on" the existing geometry. They were great for reference though! I spent a while using a measuring tape and the old console and the inside of the car and making absolutely sure that what I had in CAD was going to fit in the car. Next up I started making some modifications. First off was the shifter cutout: I decided to imitate the gauge "lenses" from the dashboard: Next up I modeled in some indents for my push button start, in addition to changing the shape of the rear section of the console: And of course, another shot with everything cleaned up, shifter, switches and push button added (those were modeled in somewhat loosely): I'm still at a loss for what to do with the back section- cup holder maybe? We'll see. I'll be 3D printing the mold Wednesday afternoon. I'm also open to suggestions on better ways to incorporate the push button start- although I've decided that I won't place them directly behind the shifter (wouldn't want to accidentally bump the ignition switch and shut the car off while shifting). PKZ
-
Hey guys- I appreciate your help. I'll be looking at ozconnection's build, since I'm curious, but I'll be sticking with the stock head. Now for the good news! I managed to find some 40mm mikuni carbs from a ski doo snowmobile that were pretty cheap! They're even the flat slide type which have the added novelty factor and more linkage to work with. Now onto the adapters! Sorry for not posting any pictures lately- but since I bought the new carbs I have to wait until they arrive to determine the spacing of the manifold. The carbs come attached in sets of two so I'll have to follow the existing spacing.
- 48 replies
-
Tony D. Thanks for the info. I didn't know the head-manifold hole sizes (that was one bit of information I asked for in the original post). The only way I could think to get rid of the notch would be to machine an insert to set into the bottom of the manifold tube where it meets the head. Wouldn't even have to be welded (or metal even!), I could just press it into the bottom of the tube. I'll look into options, obviously it has to be temperature safe if it's going to be that close to the head. You've all made good points with regard to throttle size. The cost of the larger throttle bodies is a tough pill to swallow, although I suppose that comes with the territory of trying to run a performance setup. Right now my total cost is still under 300$ including carbs, sheet metal, and welding wire. If I can get noticeably better performance compared the dual flattops (73) that I run now, I'll be happy, even if my throttle response isn't competitive with some of the true performance setups. By the way, I ran a few more flow simulations using different vacuum pressures and started to see significant differences in flow between the 30s and 40s. At higher vacuum the 30s stacked up pretty well against the 40s, but the lower the vacuum the better the 40s flowed in comparison. I spent a little time machining throttle arms today. I'll be welding up the head side of the manifold soon. I'll post some pictures next time!
- 48 replies
-
I bought the carbs on ebay a few weeks ago so I'm actually not sure where I could find the rubber couplers. However at the very least I'll use a rubber gasket material to insulate the carbs from the intake manifold. I did a comparison of the 30 and 40mm carburetor sizes using SolidWorks flow simulation. Both were modeled on the same 40mm ID manifold and had a velocity stack. By measuring the flow velocity at the head-side of the intake manifold, and leaving the manifold geometry unchanged, I was able to compare the flow capabilities of the two carburetors. What I found was interesting. The 30mm and 40mm carburetors had the same flow capability when mounted on the 40mm manifold. It wasn't until I decreased the carburetor throat size to 26mm that I saw a drop in airflow. I also ran a several different simulations which included a plenum box and changes in carburetor throat length, since I was concerned that leaving out the plenum box might skew the results toward the smaller carburetor, and that changes in throat diameter might not affect airflow unless the throat length changed as well. After running about 10 different simulations, I was satisfied that my model wasn't biased in favor of the 30mm carburetors. 40mm Carburetor Model: 30mm Carburetor Model: Based on my simple flow sim models, I'm more confident the 30mm carburetor should flow comparably well to the 40mm given my current setup. More updates to come once the metal comes in early next week.
- 48 replies
-
Bearmanpete, you make a good point regarding peak flow and cam timing. Unfortunately I purchased the 30mm Mikunis about a week ago, so I'll probably be going with those and seeing how they work for now. I'll be looking around for a set of 40mms and planning to do the carburetor mounting and throttle linkage last (maybe I can find a cheap set of 40's before I get to the carburetor mounting, since the carbs will be evenly spaced anyway I don't see it being a huge issue). The Mikuni throttle shafts have a 6mm slot with a little flange on the end to hold the arm on. It's pretty small, I don't see doing any tapping being an option. At best I could see drilling a small hole and using a tight fitting pin to hold the new rod in place. Here's a picture of the Mikuni 30mm. Sorry the picture's so big, but the extra detail probably helps anyway. The throttle shaft is located in front of the vertical bronze vacuum port. As you can see there's not a ton to work with. I'll probably shop around for some sheet steel today. I'll go with some 40mm tube and some thin plate. I haven't investigated the effects of heat soak in detail. Could you explain? I know hot air is worse for performance, but will a steel part inherently get hotter than an aluminum one? I'll keep you updated with my progress in the next day or so. PKZ
- 48 replies
-
Thanks for the input guys. A few more questions DAW, when you say "plenum manifold," are you referring to running 1 throttle plate with 6 runners? Also, I did take a look at the existing Weber manifolds but given they they would need an adapter or modification to fit my application, they don't seem right for my application, especially given their cost. My current plan is to fabricate a manifold consisting of 6 individual runners and 6 throttle plates. Gareth, Thanks for the advice. Your setup looks great! The throttle linkage on the mikunis is directly on the throttle shaft. Which means to run the same setup you have I would have to pull the throttle shafts and drill/tap holes for each throttle plate to mount on. I see accuracy being a big obstacle there, so instead I'll probably start by trying to connect the ends of the shafts together using rod couplers. I really do love the cable setup though. As Xnke said, I chose steel for the fabrication benefits. Don't currently have a tig welder, just a simple Lincoln flux core welder. I figure the manifold gasket should act as an insulator between the alloy head and the steel intake. If not, some high temperature paint should protect it well enough. I'm currently running stock internals and 2 flattop carbs. I think the extra flow will give me a bit better throttle response for now (each Mikuni carb flows about 100 CFM), and flow enough where I could run slightly hotter, still street oriented cam if I decide to. 40mm+ seems like overkill to me. 600 CFM, even in a built l28, seems plenty.
- 48 replies
-
Hey everyone, This is my first post to the forum, and I have a project and a few questions to share. I'm currently working on building a 6 carburetor setup for my l28 and have decided to use 6 30mm Mikuni motorcycle carburetors. I've selected these based on the airflow requirements of the engine while accounting for volumetric efficiency, engine speed, and of course engine size, and by comparison to some other carburetor setups (triple webers, various SU setups, etc). Needless to say, the Mikunis won't be compatible with the existing N33 intake manifold I'm currently running, so I plan to fabricate one from steel sheet and tube. My question relates to the ID sizing of the new intake manifold. I've read a rule of thumb that says the throttle body at the base of the carburetor should have an area that makes up 80% of the intake manifold cross sectional area. Based on this, I'm approximating an intake manifold ID of 33.54mm (see calculations below) Area of throttle body at carburetor base= (15mm)^2*3.14=706.5sqmm Area of intake manifold =.706.5/.8=883.125sqmm Radius of Intake manifold=(883.125sqmm/3.14)^(.5)=16.77mm Diameter of intake manifold=33.54mm Can anyone confirm whether this 80% rule of thumb is safe to go by? I know there are other considerations to make when it comes to resonance tuning and airflow, but I've had little luck finding anything conclusive. I'm also considering sizing the new intake manifold to match the ID of my existing N33 manifold and N42 head. Given the simple construction of the new manifold (going with steel tube and steel sheet), fewer changes in diameter might be better. Abrupt changes in diameter of the tube will cause turbulent airflow, which, while potentially useful for achieving an even fuel mixture, could also reduce throttle response (thus my reasoning for matching the new manifold to the head). Does anyone know the size of the holes where the head meets the intake manifold? I've done some searching around the forums but am unable to find this bit of information. Thanks for your help! Any and all advice is welcome. pkz
- 48 replies