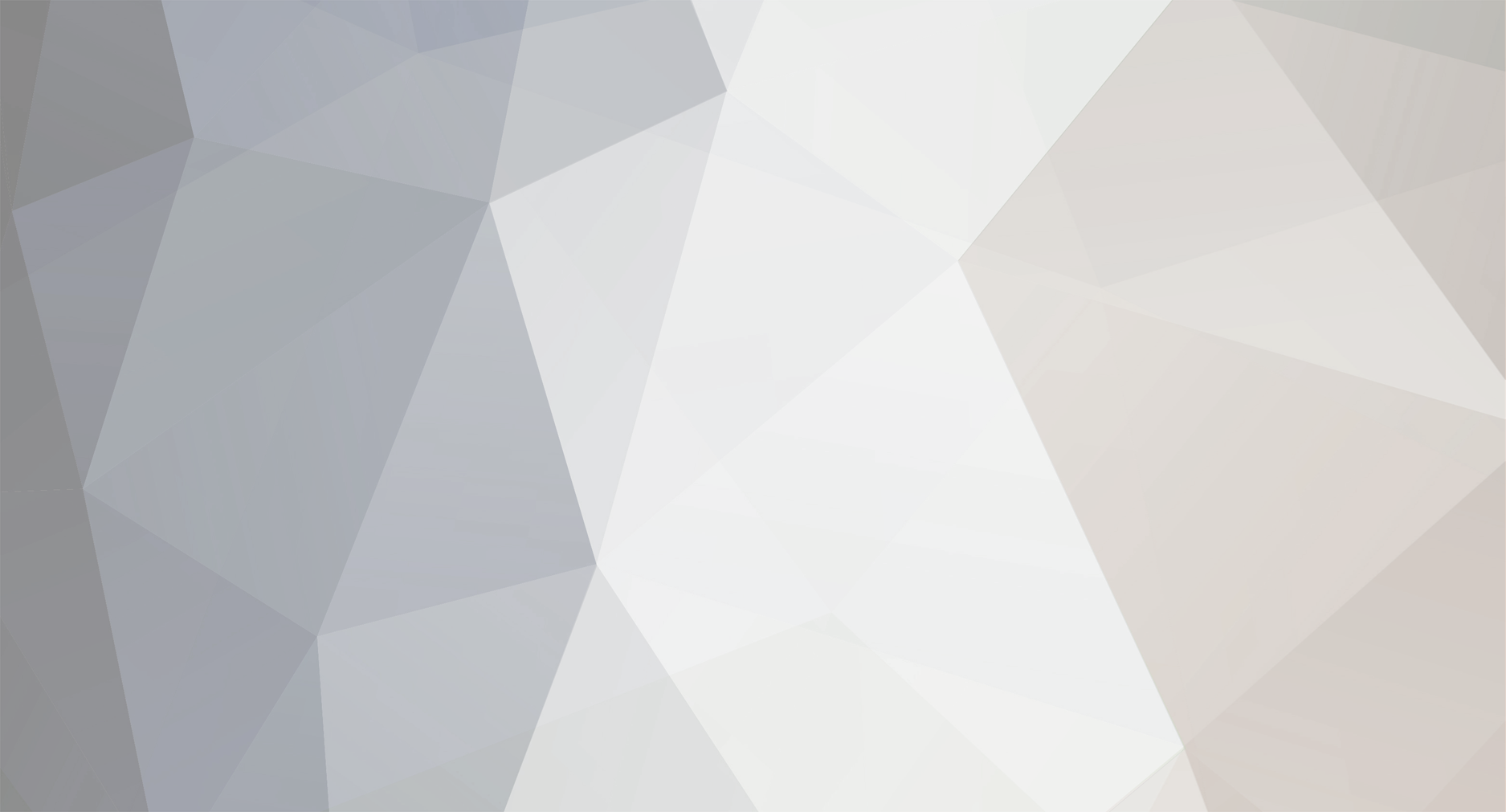
katman
Members-
Posts
611 -
Joined
-
Last visited
-
Days Won
6
Content Type
Profiles
Forums
Blogs
Events
Gallery
Downloads
Store
Everything posted by katman
-
Anybody remember the Sperry UNIVAC mainframe? As old as the Z. Lost my old HLS30 unibody finite element model on a tape somewhere. Since I have to re input it, may as well put it in CATIA and PATRAN, eh? Haven't forgot, still getting the geometry in in my spare time. May as well have a tool for exploring the age old questions about chassis stiffening for V8's, strut bar effectiveness, NASCAR door bars versus X-door cages, etc.
-
I don't believe seam welding is gonna stop a first gen Z from crumpling. I also doubt it adds any measureable stiffness. What it does do is reduce the local stresses on the spot welds, which is more of a fatigue thing than a static thing. On the downside you fry the primer between seams which give your old Z another excuse to rust. If I was a little more anal I'd disassemble the entire unibody and reweld it with the bonding agent they use on new cars which can be spotwelded through. Good seal, glued together, very strong. Wait, I am anal enough to do that...
-
Carbs are just a semi metered fuel leak, and this is especially true of SU's above 4000 rpm where the slides are slam up against the top the whole time. Yeah, batch fire EFI and other early systems weren't perfect, but I agree with JohnC- given a clean sheet EFI beats carbs every time. And personally I'd rather troubleshoot a bad sensor on EFI than worn throttle shafts/improper float height/worn needles/worn slides etc. on an SU. Much more clear cut as to what your problem is. Of course reaching down into a hot place to twiddle with the SU mixture knobs has some real world applications which are not without merit...
-
Well, if it makes you feel better, with the right megaphones at 7000 rpm they sound wicked!!!
-
Well, if it makes you feel better, with the right megaphones at 7000 rpm they sound wicked!!!
-
In ITS trim a dual exhaust L24 loses about 10hp over a single 2.5. Your results may vary...
-
Could be. My old measurements are within 1% or better from your chart in the 3-8k range. That would make more sense. The "pills" never matched very well with what our data acquisition system was telling us which is why I thought they were standard. Probably closer than most people's tach's, anyway. Funny why they didn't make it linear....
-
How much budget = how fast you can go. So how much budget?
-
www.ztherapy.com for rebuild kits, or better yet just buy their rebuilds, then you know it will be right. Sounds like your fuel bowl needles aren't shutting off the gas. Easy fix for a Z mechanic. I agree, get it running good in stock form first, then evaluate how much money you really have to spend. That determines everything.
-
I generally hate using a bolt in anything but a shear application, especially when the threads are involved, so I always squeal a little when I see people try to make something like this. Especially at the rear control arms for several reasons. I've also commented off line to some folks who've done this sort of thing. Race cars get away with it because we inspect them all the time to catch fatigue problems, and a threaded bolt in shear and bending is gonna be a fatigue problem. Plus we have a real cage for when it breaks. That said, the stresses involved are generally below the endurance limit of the steel, even when you consider the threads etc., so I can't really say it ain't safe if the quality of manufacture is up to par. However, I gotta ask why? Have yet to see one of these lighter or with more damage tolerance than a stock part. Don't we usually adjust camber with camber plates? I've considered this for my project but I keep coming back to "why change from stock?" Now for the rear it'd be nice to have toe adjustability. But depending on where you locate your bolts you could have some real bolt bending problems in the design of a rear control arm. But for the front I'm missing why we need threads.
-
pull to left under braking
katman replied to Dan Baldwin's topic in Brakes, Wheels, Suspension and Chassis
Hey, anybody else show up in your class? Bwah Hah. You ready to move back south? Got some room for another stress weenie at the bomber plant... -
Pete's info jives with a graph I made a few years ago, just from measuring a pile of the MSD rpm modules. An equation, cool. Don't forget most resistors are +/- 2 percent or so, so at 7000 rpm that's like 140 rpm one way or another. Not too accurate really, and I don't think the MSD pills are anything special in that regard.
-
As well as bad cam geometry. Don't forget to change the rocker guides (lash pads) when you shim towers.
-
Ultimate Front Strut Brace F/S
katman replied to rc's240z's topic in Brakes, Wheels, Suspension and Chassis
Actually, if the two bars from the struts met at the same point in the center of the firewall, say behind the hood latch, torsion and side loads from the front of the chassis result in tension in one bar and compression in the other, which cancels out in the fore/aft direction and results in only lateral loads at the attachment, so it ain't an issue if done properly. It is an issue when the two bars don't meet at a point. -
It is in fact very easy to collapse the frame rail when you tighten the bolts. On the ITS cars we use nylon locknuts and just snug them. The normal failure mode in stock form occurs because the sway bar loads are pulling the lower surface only, up and down like a membrane, and the inevitable rust thats on the inside allows the cracks to begin. Sandwiching the frame rail at least gets the entire box involved in the "pulling down" load, even with the bolts not monster tight. Running a tube through there so you can tighten the bolts is a great idea, especially with Ron's device since then the up loads would go right into both the rail and the strut bar, instead of into the rail on its its way to the strut bar or inner fender. On the ITS cars we're always fixing cracks in the frame rail to inner fender junction, and seam welding a street car or race car whose rules allowed it would also be a good idea for this highly stressed area. Of course we always assume good OEM structure when we have these discussions. Unfortunately the frame rails tend to rust inside out, so what looks good can easily be extremely thin compared to when it started life 30 years ago. Job one should always be a proper assessment and probable repair of this.
-
This wouldn't be necessary if you eliminated the fore/aft component of the connection here (trickier to fab no doubt), but I like your thinking. That's exactly what I'd expect with a traditional "hard in all degrees of freedom" connection, that the place you want to hit is the intersection of that shelf with the firewall. All around an excellent idea. I love it when somebody has the gumption to run a test. I can see I'm gonna hafta dig up my finite element model of a HLS30 unibody and dink around with some strut bars. I wonder if we still have that old Cray XMP out in Rye Canyon....?
-
Yeah, now I remember there being some sheet metal behind the firewall in some places up there in the cowl area, I stand corrected. Regardless, I stand by my statement that it's not very effective that way. Agreed there is a challenge to a single truss emanating from the center of the firewall because of the hood latch. There is no fore/aft reacting load necessary with the single truss if the connection at the hood latch is designed to react side loads only (the real beauty of that concept). Easily done. Side loads imparted anywhere on the firewall are easily reacted. Fore/aft loads to balance the moment are then reacted by the hood ledge area of the inner fender as I alluded to earlier (my original microfiche calls this a "food ledge"). Lemme run some numbers with each design including the bracing aft of the firewall. May be in practice there's not much difference in stiffness. I'll keep ya'll posted.
-
Actually you could get a Koni or Bilstein valved for about whatever wheel rate you want, still cheaper than the Advanced Design, but with no adjustability, which IMHO is worth a few extra sets of shocks unless you already know exactly what you want. Tokico and the other off-the-shelf players really don't have anything good for more than about 250 lb/in springs. As previously stated your options really depend on your application. Once known, then we can help.
-
pull to left under braking
katman replied to Dan Baldwin's topic in Brakes, Wheels, Suspension and Chassis
Perhaps you should park your car in a Republican garage... -
Yup.
-
Ultimate Front Strut Brace F/S
katman replied to rc's240z's topic in Brakes, Wheels, Suspension and Chassis
I've seen the same thing. We do exactly what you did on our ITS race cars. On the EP cars where the rules give us a little more leeway, we have the plate you mention extend up into the inner fender panel to smear the loads out some more. This strut bar looks like it tries to help with that, which is meritorious. -
I don't doubt that the more sophisticated teams include chassis stiffness (all degrees of freedom) in their suspension dynamics models, but I find it hard to believe they are astonishingly weak in torsion. At least not because of their door bar execution anyway...
-
Bingo! The X type door bars do a more efficient job of helping with overall shell torsion, the real weak link in an old Z. Well stated. In my cages I actually angle the upper door bar so it gets me some additional truss action for just that reason, plus it follows the squishable parts of a driver better. Attaching the cage at the ends of the X's to the unibody is a must do like you say, when the rules allow it.
-
Ultimate Front Strut Brace F/S
katman replied to rc's240z's topic in Brakes, Wheels, Suspension and Chassis
Might want to read my reply to the same post on under the L6 Perf. forum, just for yuks. -
Well, it's cool, but claims that it eliminates all strut tower movement are a stretch. The "ultimate" brace would have a single triangle from the towers to the center of the firewall, not two individual triangles. Here's why: What we are trying to prevent on the front half of an early Z is twist due to torsion and sideways motion due to lateral forces. Vertical loads are already well accounted for by the frame rail/inner fender/hood ledge assembly. All strut bars basically keep the two struts together at the top. Now to react sideways motions of the strut towers we need to react a sideload somewhere. Using the two trusses shown with this setup, a sideload applied at a strut tower is reacted back at the firewall as an equivalent and opposite sideload at each truss attachment, PLUS a moment equal to the sideload times the distance to the firewall from the strut tower. Now this moment is reacted by fore and aft loads at the firewall attachment, which would be fine if the area behind the firewall had anything behind it, but it doesn't, so there's almost no fore/aft capability up there. Consequently this setup is not very stiff for lateral movement of the strut towers, which is the whole point of having the brace. A single truss, tower-to-tower-to-firewall uses the fore/aft capability of the hood ledge in a mo' better than the device shown, effectively becoming a 3 truss system. Better angles, more efficient, much stiffer. I'd draw a freebody diagram to make it clearer if I had a napkin and a beer.