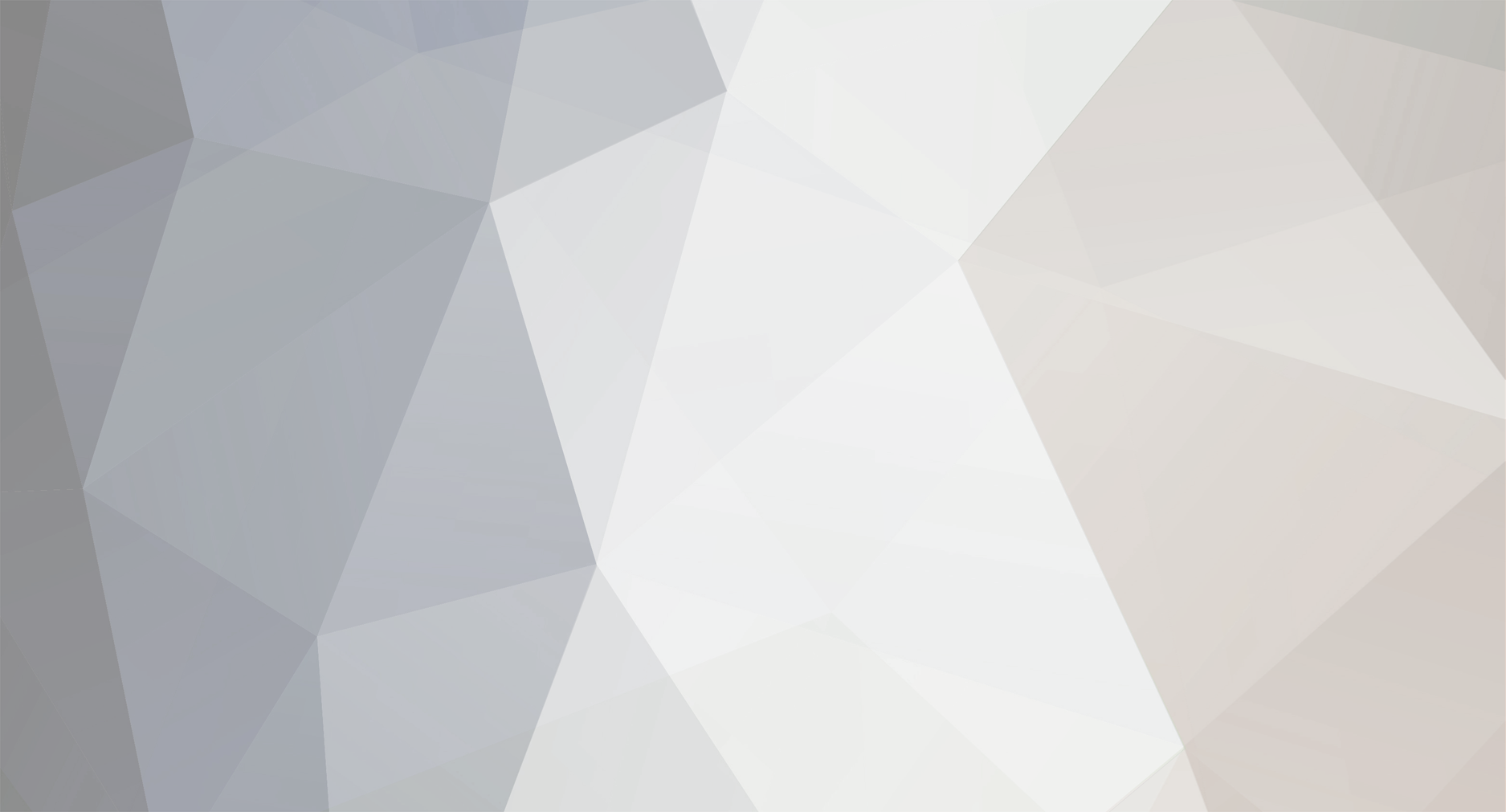
katman
Members-
Posts
611 -
Joined
-
Last visited
-
Days Won
6
Content Type
Profiles
Forums
Blogs
Events
Gallery
Downloads
Store
Everything posted by katman
-
A good primer on cage design is that old Z-Car Mag article on building a cage for an ITS 240Z (that Jefferson Spiedel guy was a genius). When I get back next week I'll find a way to get it posted somewhere, along with some extra pictures that will show how we do the stock dash. Sorry you'll have to wait. As far as stiffening the chassis for V8's, I need to think about that some more, but I will, I got the same problem staring me in the face every time I have to shoo my wife's cats off my project. I do know the weak link is forward of the firewall, and the most efficient way to help that is with a strut bar that triangulates back to the top of the firewall. That helps the overall front end torsion flexibility a lot, but there's also probably something we can do on the bottom. I've seen some ideas for that on this forum, but haven't really thought about it enough for a street car to comment yet. For dedicated race cars we can take liberties that don't translate well to something you have to live with every day. I'll get back with you on that.
-
Yeah John, you're right. X over the pass compartment is what I was thinking when I said they got some tubes up high that aren't really doing much. The basic problem with this cage is the X for the door bars, and the high tube up front in the dash area. Here's why. In a T-bone with this cage, the X is going to try to send load equally to the floor and to the upper region of the cage. Unfortunately, the load really wants to go low, because low is the loadpath to the engine and rear diff/suspension, and the load wants to go there because F=MA, where F is the other car hitting you, and M is the mass of this car being accelerated (the "A"). Most of the mass is where? Engine up front, diff/suspension/gas tank in rear. So only half the tubes in the X are involved with reacting the impact to where it wants to go. I always put 2 NASCAR type door bars in, sorta horizontal, where the upper one intersects a LOW bar1/2 inch above the tranny tunnel under the dash. This helps keep the left front downtube ("A" pillar tube) from folding inward toward your left leg, and helps to involve the entire floorpan and firewall sooner in the impact sequence. If its an EP car, and I think John is probably right on that too, it would be legal to arch the door bars out into a gutted door, which I always do if the class allows. No sense in not trying to keep the impact as far away from body parts as possible (even though as a crew chief I generally would prefer a robot over a driver, but SCCA still frowns on that and a good shoe occasionally will bring sponsor money...). That's just an example of how this cage could be better. I would like to see what happens on the other side of the firewall. Looks like it will be a really nice car though. Wonder why he didn't mount the fuel tank to the far right, 2 inches lower, and offset the driver seat to the right an inch or two? Hmmm, may be racing somewhere other than on US road courses...
-
Great in roll. Not so great in a T-bone. Also a lot of weight up high that's not really contributing very much. It can be done better, safer, lighter. Gone racing for a week, when I get back I can see I'm gonna hafta elaborate. This roll cage subject just isn't going to go away.
-
There was a quote from Car and Driver a few years ago in an article about Top Fuel. They said that using nitromethane in an internal combustion engine was kinda like using a Claymor mine to unstop your toilet. It works great but it's hard on the toilet.
-
SCCA, NHRA , IHRA legal rollcage
katman replied to DemonZ's topic in Brakes, Wheels, Suspension and Chassis
Find an old copy of Z-Car Magazine, the issue where they described the cage for an ITS 240Z. It talks about the load paths and the SCCA requirements. A must read if you want to be safe. Since this keeps coming up, I got a copy I would gladly snail mail to somebody with a scanner if they wanted to put it up on the web somewhere where we could all read it. Unfortunately I'm worthless when it comes to PC's.... -
Don't forget that when you lower a Z substantially you need to have shorter shocks. How high off the ground do you want the rocker panels to be? What spring rates are you looking for? The cheapest brake upgrade is good pads. Going to the Toyo caliper won't necessarily help you stop faster. How much are you willing to spend?
-
The front cries out for a strut bar that triangulates to the firewall. The rear is a lot stiffer so the payoff isn't as great IMHO, and most roll cages put a tube between the rear towers anyway. What's a sub frame connector?
-
Stock spring pre-loaded? danger?
katman replied to a topic in Brakes, Wheels, Suspension and Chassis
Yup, and yup. -
The headersbyed website has lots of good info about headers for normally aspirated American V8 engines, and generally good design tips. However, for a turbo application all bets are off. Corky Bell at Bell Engineering (used to be Cartech)would probably be the most knowledgeable about a L6 turbo header, but his time isn't free. Fortunately the exhaust system for a turbo setup isn't near as critical as for N/A (just turn up the boost screw, Bubba), and you can make godawful amounts of power with the stock 280ZX manifold. I don't see where AutoCad would help, CATIA maybe. I know AutoCad but it won't help you decide what primary lengths and sizes etc. you need, and its really faster to mock them up with flexible tubes than to draw them up in a 3D package like CATIA, at least for me. Might help you draw the flanges etc. so you could have a machine shop make them. Headersbyed and Stahl and others sell collectors and tubing, etc., and Stahl makes a reasonably priced head flange for Z's as a starting point. Personally I'd spend my time and money elsewhere for a single turbo setup, like in the fuel management.
-
Do we need solid brake lines?
katman replied to auxilary's topic in Brakes, Wheels, Suspension and Chassis
Ross sorta touched on this, but the reason you would like the flex line to go to the strut is because it gets it closer to the center of rotation so it isn't swinging through such a big arc every time you turn the wheel. Fatigue will occur later rather than sooner. Also, it keeps it further away from potential contact with the tire... -
I believe the FSM says 83 lb/in front, and 101 lb/in rear for the 240Z. Ain't much is it?
-
Typically it runs right beside the left side of the diff where the arc is formed for clearance in the front diff crossmember (inboard of the control arm), then curves behind the left control arm. Any reason in particular why you'd want to go over or under the control arm as opposed to the stock location? I don't think there's clearance to do that.
-
A bone stock system in OEM condition will stop you at the limit of adhesion of your tires at least one time from top speed. However, it may be very difficult to modulate at the limit with both feet on the pedal and the pads may catch on fire by the time you've stopped. A stock system upgraded with pads, ducts, and an adjustable proportioning valve will stop you repeatedly at the limit of adhesion of any DOT approved tire currently in existence and be easy to modulate. Converting to rear disk will eliminate the need to adjust the drum shoes. Converting to a bigger front caliper and a vented rotor will increase pad life, reduce or eliminate the need for ducts on track days, allow for cheaper pads, and may be easier to modulate. Any conversion like this would require replacement of the stock proportioning valve with an adjustable one to maximize front/rear efficiency and hence braking performance. It is entirely possible that just changing the fronts to a bigger caliper like the popular Toyo swap could actually reduce your braking performance because of the change in bias front to rear. There is a lot to be said for upgrading to a more modern system (big calipers, rear disks, vented rotors etc.), but stopping quicker isn't necessarily one of them.
-
The law of Civics, that's good. Actually there's probably other reasons why drag cars don't all have 4wd (rules, costs, weight, etc.). When it comes to tires, F=uN is not linear. As the normal force increases the coefficient of friction is generally reduced, so 4 tires carrying a specific weight usually have more grip than 2 tires carrying that same weight. With weight transfer in a drag launch, a 4wd car with the power apportioned according to the resulting weight on each pair would probably be faster than a car with the same power and all the weight on just 2 tires. As for the original question, there's way too many variables involving tire construction (belts, formulation, stiffness etc.) and the pavement it sits on to be very successful arriving at a formula that relates tire width to traction. As stated earlier, while theoretically width should be independant of traction (no area variable in the F=uN equation), we see in practice this is not so. Has to do with the fact that the tire/pavement interface is not smooth so there is additional grip due to "interaction". There may be a paper out there where somebody tested a tire to get grip using width as a variable, but I haven't seen one. Wouldn't be too hard to do and plot a curve though.
-
Ah, 18 inches to the bumper. Now it all makes sense. I think of supension travel as being at the wheel.
-
Okay, if we had stock springs at like 83 lbs/in for a 240, and there's about 635 lbs per corner on the wheels for a stock engine, that's about 7.6 inches of squish on the springs before they are completely unloaded. Seems like theres about 5 inches of droop from stock ride height to when the shock limits the spring extension anyway, so I'm confused about the 18 number. Regardless, I can see theoretically how you fixed it. Say acceleration raises the front end 4 inches. Well the spring is still compressed 3.65 (7.65-4) in our example, which means it is still helping acceleration push up on the front of the car by 3.65*83=303lbs per side. If the CG and acceleration are such that 606lbs will continue to rotate the car then we have a problem. If the springs were travel limited to 4 inches, then the full weight of the front end would resist the overturning moment due to acceleration, not weight minus 606lbs. So the front might stay down. Cool. At 18 inches I assumed the wheels were entirely off the ground and therefore nothing could help with regard to travel limits. Interesting.
-
Ah, but it is a beautiful piece of engineering. All alumunum block, 4 valve, yee hah. Of course, if you ever need a valve job break out yer wallet...
-
Stock thickness on all the L heads would be 4.248 (107.9 mm), although most measure a little thicker, like 4.252 unmolested. Knowing that you can figure how much has been shaved off. Up to 0.030 I wouldn't bother shimming- it likely will hose up your rocker geometry enough to need different lash pads, just adjust the cam timing with the sprocket and take up the slack with the curved chain guide. At 0.040 you might consider a 2mm HKS gasket, which is 0.079 thick as opposed to stock 0.052. However it is designed for the big bore kit and has huge holes (90mm I think). There's also a "head saver" soft copper gasket that's 0.020 from Fel-Pro which you add to a stock gasket. Best of luck.
-
Great deal on a roll cage!!!
katman replied to utvolman99's topic in Brakes, Wheels, Suspension and Chassis
I'm not sure how they got them originally, but I'd say over the years they've collectively sure crash tested enough of them. In one of Carroll Smith's books he comments that about the only thing he thought was worthwhile about SCCA was their roll cage requirements. -
All that will do is pick the front wheels up sooner. You have to either lower the CG of the car, move the CG forward, extend the wheelie bars back and down (which will have the side effect of removing vertical load from the rear tires, unfortunately), or increase the wheelbase. A short, high car like a 240Z will always want to flip over backwards. It ain't about the suspension, it's about F=MA and where the F is reacted. How much hp you talkin'?
-
I didn't initially criticize anything, that would depend on what application the cage is intended for, and that was my question. If you don't expect anything out of that cage then I have no criticism. But since you asked, here are two reasons why it is unsafe, for racing anyway. First, the main hoop for the chassisworks designs (and I think the S&W too) are missing an uninterrupted diagonal in the plane of the main hoop from a point above the driver's right ear to the bottom of the passenger side of the hoop, which effectively forms a truss above the driver's head. To not have this, which is so elementary from a structural standpoint (and required by SCCA), shows a lack of understanding of basic roll cage design principles. Sorry, their diagonal that goes from the hoop to the strut tower is worthless. Second, the chassisworks designs have a horizontal bar at dash level for the forward section of the cage. When you are T-bone'd, if the door bar doesn't collapse (and their single bar will, I assure you) the floor at your ankles will. This is because the floor of a Z will not resist the sideload imposed on the forward downtube by the door bar with most of the load taken by a single side of the floor. To fix this, the horizontal bar needs to be closer to the door bar intersection, passing right above the tranny tunnel, to help get the sideload over to the other bar (with their high bar the forward downtube just bends when the floor collapses) and react the load with both sides of the floor. Better yet is to add tube from the downtube to the firewall just above the dead pedal. The chassisworks units use 1-5/8 diameter 0.134 wall tube. A real engineer would have used 1-3/4 diameter 0.095 wall tube for the same bending sitffness (axial stiffness is plenty in either case) at 27% less weight. And since all the weight is above the CG you want it to be as little as possible. There's more, but that should be enough. Now if you want a dissertation on roll cage design for a 240/260/280Z, somebody dig up that old article in the defunct Z-Car Mag on building an ITS 240Z, the issue that discussed the cage, and post it out here we we can all read it. I would be happy to but I don't know computers. It discusses the load paths involved and where/how to get the cage loads into a flimsy Z unibody. Very thorough and explains "why".
-
Great site Douglas. A little short on the "why's" though, which is really the good part of that old Z-Car mag article as it pertains to a Z unibody.
-
What's inappropriate about asking what your objectives are for this cage? Are you insulted somehow by that question? If your objective was to look like a racer then that cage will accomplish that. If it is to mount belts then it will accomplish that. If it is to stiffen the chassis then yes it will add stiffness, albeit very inefficiently. If it is to go racing then it is woefully inadequate. If it is to protect your head in a rollover then it won't. If the objective is to save your legs in a T-bone from somebody rolling through an intersection it won't do that either. I was just wondering what the objective was for installing a poorly designed and overly heavy (in the case of chassisworks) roll cage in a car. Seemed valid AND "appropriate" to me.
-
Also a very good way for a poor man to start busting stub axles. Upgrade your life insurance and enjoy!