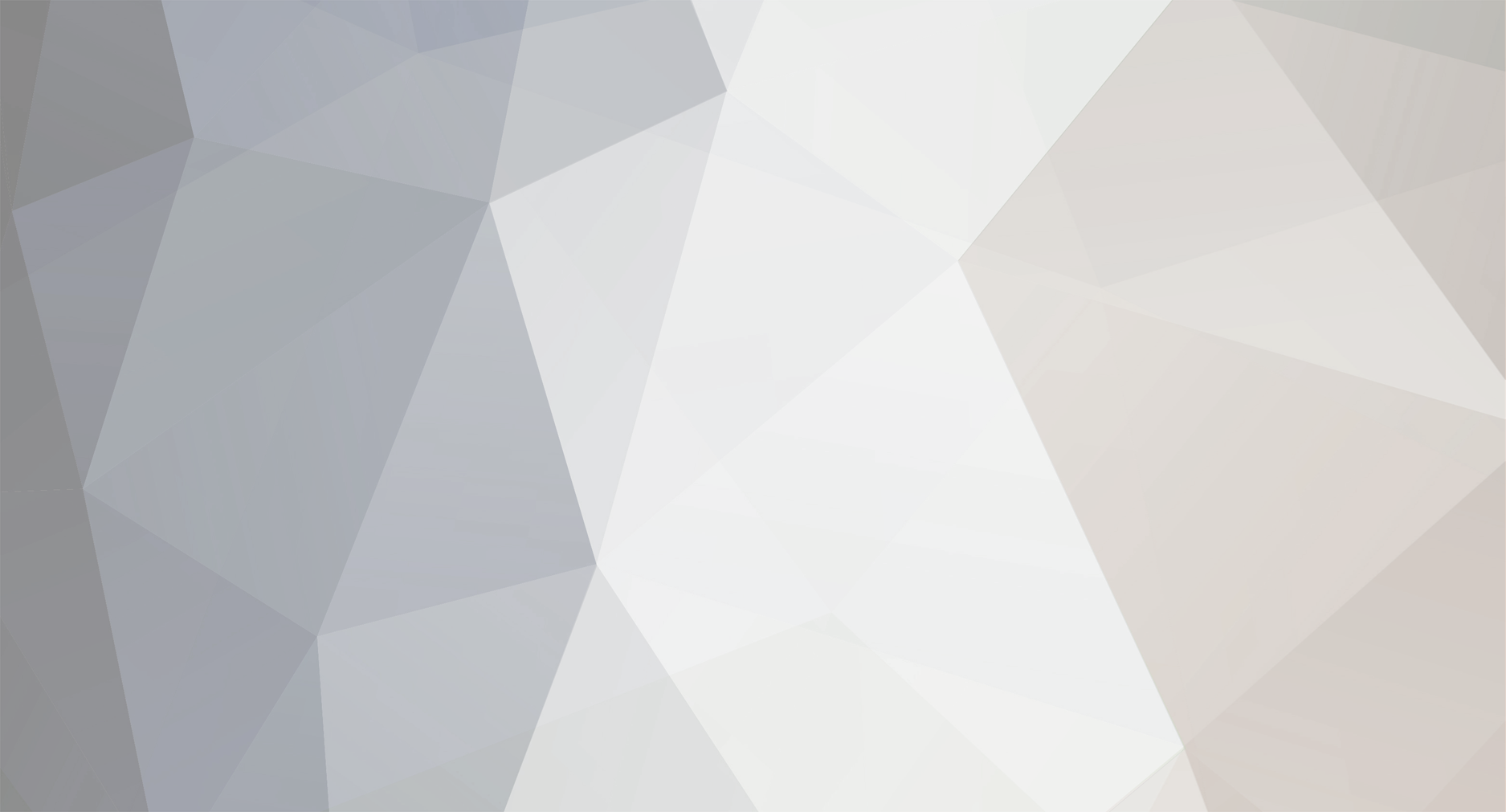
getZ
Members-
Posts
510 -
Joined
-
Last visited
Content Type
Profiles
Forums
Blogs
Events
Gallery
Downloads
Store
Everything posted by getZ
-
I agree, usually when the ignitor fails, it fails hard. I would suspect the coil more than anything and after market coils are relatively cheap. Blaster II coils can be had for around thirty bucks.
-
They are exactly what they are called. Straight plugs are perpedicular to the head. Angled plugs are about 20 degrees left or right of being perpedicular to the head. I'm not sure why there is such a thing as angled head plugs. I think they are for exhaust clearance on certain cars where the engine bay is really tight, like corvettes. If you see a picture of the two styles it becomes obvious. You can try looking at different head manufacturers and they may have a picture.
-
82 ECU/wiring harness install in 1977 280Z
getZ replied to HB280ZT's topic in Ignition and Electrical
Watch your 12v computer supply voltage during cranking. It shouldn't drop below something like 10v. I forgot where it was but I had to leave the original resistor the car came with to prevent the supply voltage from getting to low during cranking. -
Swagelock stuff is great but they use their own thread size and it is expensive. Plus you can only find it at industrial supply places. They do have a few pipe thread adapters but try pricing a tap and die set for swagelock. Of course if you have access to it for free.......well that's another story, otherwise it costs more that AN style fittings.
-
I'm not 100% positive what that resistor is for, but lowering the voltage is probably a good guess, either that or it is to prevent a direct short. Are you still eating up coils?
-
rommelrommel, The + side of the coil should have 12 volts in either the run or start position. However the - side of the coil is grounded through the distributor. It is one of the fuctions of the distributor to complete the ground side of the circuit in order to energize the coil. I was looking at the autozone schematics, but they may be a bit to oversimplified. http://www.autozone.com/servlet/UiBroker?ForwardPage=/az/cds/en_us/0900823d/80/1d/1d/80/0900823d801d1d80.jsp The Nissan schematic from CD is extremely difficult to use so I hope this works for you. It looks like the blk/white wire is what is used to ground the coil and hook up the tach as well. I'm not sure which wire you mean when you say red/blue at the front main harness, but at the front of my 72, red/blue wires connect up to another red-blue wire. That red-blue wire powers up a lot of accesories depending on where you are talking about. Hope this helps.
-
I was thinking about that somemore. It's kind of an odd way your transistor failed. I suppose anything is possible, but I'm used to seeing them die where they don't work at all anymore. One more thing, this might be obvious but does your meter measure 0 ohms or a short when you connect the leads together. Also did you get a good ground on the ignitor body?
-
35K Ohms is very high for what the device is supposed to doing. It is supposed to be pulling that signal down to ground. A resistance that high probably won't allow the MSD to trigger. Does grounding the white wire of the MSD give you an arc? I use the wire from the coil to the distributor, disconnect the distributor and go directly to an extra spark plug (make sure the outside of the plug touches a good ground)
-
Help looking for ignitor power transistor number
getZ replied to getZ's topic in Ignition and Electrical
HBO, Sorry so late getting back. I'm out of the country on business. No luck on the part number. I did find a cheaper one through rock auto that was half that price: https://www.rockauto.com/applet3.html Hope their website works for you. I had to go download a Javascript from somewhere to get there site to work, the download was free but it was a hassle trying to figure out why it wasn't working. The transistor on the replacement part I got had a number on it but it didn't seem like a part number I could cross reference. I think it was something 3c ?????????? -
I don't know this for a fact, but I don't think it matters which way you hook up the knock sensor. It looks like a variable resistor. Stuff like that ususaly isn't fussy about which direction you hook it up, the output is the same. As far as injector colors go, I have no idea, but I have seen discussions about it on this web site. You might try doing a search on "injector color"
-
Well I guess there are still a lot more questions then answers. What does you timing look like at idle, when reving up? How's your fuel pressure when reving the engine up? Did you hook up the cold start up stuff, AAR, air regulator and associated water hookups? As far as the starter, I agree with your diagnosis, sounds like the switch is going bad to me.
-
Almost have the turbo running. What did I do wrong? :)
getZ replied to Thumper's topic in Turbo / Supercharger
the green light comes on as soon as the ignition is turned on and stay on. It goes off or fades during cranking. I have another ecu you are welcome to if you need it. PM me with you address and I will send it out. It may have been off an automatic so I don't know if it will work 100% correct. I only ask that you pass it off to somone else in need when you are done. It will start and idle the car. I don't know about actually driving it around. -
Almost have the turbo running. What did I do wrong? :)
getZ replied to Thumper's topic in Turbo / Supercharger
Sounds like you have it wired right. In addition to PrO's suggestions. You should get 12 volts when the ignition is turned on at the + side of the coil which also the conector of the ignitor that is perpendicular to the coil. The signal out of the computer is difficult to see without a digital o-scope. I attached a picture of what it should look something like. This was from my 81 motor going into a bad ignitor, regardless the signal should look similar. The voltage is something like pulses over 10volts. A meter may see something like 2 volts for a short burst while it is cranking, depending on what type of meter you have. The computer sends its output to the ignitor and at every pulse the negative end of the coil is connected to ground thus completing the circuit and pulsing the coil. The computer needs an input signal from the distributor to know that the engine is rotating. My problem was a bad ignitor. You could have a bad ignitor, coil, computer or even a bad distributor. Also make sure the ignitor is bolted to the body. It has no ground wire. Instead it is ground though the outer casing which is riveted to the coil bracket. I found a cheap and easy was to check the ignitor. Remove it from the car. Attach a meter to the blue wire of the ignitor and ground the other meter lead to the coil bracket. Using a AA battery and some wire, apply the + side of the battery to part of the ignitor where the yelllow w/ white stripe wire used to be connected. Every time the + side of the battery connects to the ignitor, the meter will measure a short or less that 2ohms. -
Got my '82 distributor, kinda confused on how to install it
getZ replied to a topic in Turbo / Supercharger
I have an 81 crank position sensor and adjusting timing is just a matter of moving the sensor up and down, which seems about the same as rotating the distributor. Perhaps somone with actual experience doing this will chime in. Are you using the the distributor to trigger the MSD or the output from the computer to the ignitor to trigger the MSD? If you're using the computer output to trigger the MSD, the wiring is the same since the 82 distributor is a direct replacement for crank position sensor. There is a down side to using the 82-83 distributor as a direct trigger mechanism. It is directly connected to the engine and will never vary the timing. Using the computer output allows the computer to interpret the timing from the crank position sensor or distributor and make adjustments as needed. I'm not sure how critical that is since I don't know the timing map for the computer. That's just my 2 cents. -
Got my '82 distributor, kinda confused on how to install it
getZ replied to a topic in Turbo / Supercharger
Here's another idea: Picture an imaginary line between the two mounting bolts of the distributor. Rotate the engine so the rotor now points along that line and towards the engine, which by the way should be pretty close to TDC. Remove the oil pump and shaft and reistall the new shaft so the rotor aligns the same way. One tooth off on the pump shaft will put you about 20 degrees off, so it easy to spot when you're off. Not much oil comes out when you remove the pump. About all you get is what is in the engine passage way, just keep the pump upright after it comes out. Keep a couple rags handy and you should be okay. It is probably a good idea to have another oil pump gasket handy at the time as well. -
I have an 81 with msd 6AL, but the hookup should be similar. The white wire of the msd is the trigger signal and it needs a grounding signal. The computer uses the input from either the distributor in the case of the 82-83 or the crank position sensor like in the 81. In either case those signals are used by the computer to interpret engine speed, from there it sends an output signal (yellow and white wire, also see: http://forums.hybridz.org/showthread.php?t=99620) to the ignitor. The ignitor is used like a relay. It recieves the compter pulses and connects the blue wire (on the ignitor) to ground at every pulse. Picture the two inputs to the ignitor as being like a "T". One is a horizonal plug the other is a vertical plug. The vertical plug is the input of the ignitor. I hope you ignitor is good, mines was bad. I found an easy to test the ignitor. You need a voltmeter, an AA battery and some wire. Hook the meter to measure continuity accross the blue wire of the ignitor and the mounting body (the body/housing is used as ground) Making sure you have a good connection on the body since it is plastic coated sometimes. Now hook the battery (plus side) to the vertical bar of the "T" and body. If its working correctly the meter will read close to zero every time the battery is connected.
-
What year is the car? Z cars had alternators with different style voltage regulators. Older cars had the regulator on the firewall while newer ones had built in voltage regulators similar to the gm one wires. Here's a link on hooking up different style alternators: http://www.zcarcreations.com/howto/voltreg.htm
-
Hmmmm..... First, you have conflicting voltage readings from your regulator to the megasquirt. Which one is correct? I guess the only way to know is to use another voltage meter. According to: http://www.autozone.com/servlet/UiBroker?ForwardPage=/az/cds/en_us/0900823d/80/1d/1d/80/0900823d801d1d80.jsp The schematics show the voltmeter hooked directly up to the alternator. The voltage regulators look the same on the autozone schematics for the later turbo motor as they do the 78 so I assume the hookups are identical. My first guess, assuming all your connections are solid, would be the voltage regulator which is built into the alternator, but I would measure the voltage straight across the alternator before you changed it out.
-
Help with fuel pump wiring!!! (non Z, a bit long)
getZ replied to datsunlover's topic in Ignition and Electrical
Oh yeah, I forgot to mention something important when checking continuity on cars. There are a lot of natural shorts built in to the car which make it difficult to check grounding. Every electrical motor is basicly a wire to ground if it is hooked directly up to the battery. When I check for ground connections I disconnect the starter from the battery and the fuel pump. I suppose other cars may have even more than that. Doh! It is much easier to measure voltage on cars than resistance. -
Help with fuel pump wiring!!! (non Z, a bit long)
getZ replied to datsunlover's topic in Ignition and Electrical
okay, assuming you are going to need a grounding circuit to make the fuel pump work, does the AFR point you are hooking the fuel pump relay go to ground? To test this your meter will have to be able to measure resistance. (I hope this is not to trivial of an explanation since I have no idea what type of electronics backround you have if you need more explaination let me know). Put one lead to chasis ground and the other on the AFR output to the fuel pump relay (keep the ignition off). Resistance measurements don't need power (that might actually screw up the meter readings with power on). Push the AFR flap in and check the meter readings. If it gets pretty close to zero Ohms for a reading, you should be getting a good ground. If not then there's your problem. If you need real time help send me schematics and I will send you my cell number and I'm sure we can work fix it. Just send me a pm. I gotta solve my ignitor problems this weekend. -
Help looking for ignitor power transistor number
getZ replied to getZ's topic in Ignition and Electrical
thanks for the offer, but I should be getting one here in the next few days. I hope it fixes it! -
Help looking for ignitor power transistor number
getZ replied to getZ's topic in Ignition and Electrical
okay, I'm getting another ignitor and will post the part number when I get it. I also got an 82 distributor to try out, but it looks like a direct swap with the crank sensor. If I'm right this still won't change the ecu triggering, but I should be able to fool the ecu into thinking the engine is running and ouput the same signal to the ignitor. Speeding the distributor faster should increase the pulse frequency which is nice to know but probably a useless piece of information. By the way if you ever want to test you crank sensor, REMOVE the coil to distributor wire. Unbolt the sensor, but keep it plugged in. Then turn the ignition to on (not start) . Next run the tip of a screwdver past each of the three sensors (to test each sensor within the crank sensor). Initially the fuel pump will go on for about five seconds and then shut off. Now quickly brush the tip of the screwdriver (any magnetic metal will work) past each sensor. If all the sensors are working the fuel pump turns back on for another five seconds. The ecu thinks the engine is running. The same should apply to the 82 and 83 distributor (except all should have to do is spin it by hand), of course while it is out of the engine. Really simple to do and eliminate stuff you can't see when trouble shooting. -
Help with fuel pump wiring!!! (non Z, a bit long)
getZ replied to datsunlover's topic in Ignition and Electrical
The "run" coil gets it's power from the ignition switch in the "run" position (black w/ white stripe wire in Ba-01(F-0). The ground leg of this coil (brown wire in Ba-01(F-0) goes out to the airflow meter, where it is grounded when the airflow meter senses actual flow. If the ignition is on, simply grounding this wire will close the relay contacts and power up the fuel pump This part doesn't sound right. I maybe wrong but I was thinking an airflow meter gives you a variable resistance like a gas tank sending unit. You could get zero resistance at either fully open or closed but why would you want to be running the pump only then? There is something wrong with the above information. My guess is either a piece of information is missing or it is not the airflow meter but maybe the throttle position switch like on the 280z engine. I can sit here and theorize the whole thing bur without schematics, I'm shooting in the dark. By the way what year is your engine? -
Help with fuel pump wiring!!! (non Z, a bit long)
getZ replied to datsunlover's topic in Ignition and Electrical
I don't know much about RX-7's, but I'm okay with electronics. First you probably need to invest in a voltmeter or borrow one. Cheap ones can be had at radio shack for 20-30 bucks. When in doubt you can measure the output yourself, when things switch on and with how much voltage. When you use another wiring harness for another engine you have to integrate the wiring harness to the existing harness if you want everything to work. Sometimes you even have to run two seperate computers. If you send a set of shematics for the tbi motor I can have a look at it. I'm guessing the fuel pump should no longer hook up to the stock mazda harness. From what I have seen, electrical fuel pumps are set up to shut down when the engine stops running. so in case of an accident the car is not constantly pumping out gas. Which means the engine computer controls the fuel pump. -
Help looking for ignitor power transistor number
getZ replied to getZ's topic in Ignition and Electrical
well I managed to capture the output signal of the computer to the ignitor. Sorry if I confused anybody last time I posted about this. I thought it was a steady dc voltage. It is a series of pulses and pretty low voltage as well. The attached picture shows only .8volt pulses. I tried another cpu, it was about the same. In technical terms the frequency of the pulse is the errr.. errr.. errrr...errr of the sound of the engine turning over. Every "errrr..." is one pulse. By the way the ignitor and the output of the cpu have to be working correctly if you want to use an MSD with stock style triggering. What the igntor does is pull the "white" wire of the msd to ground at every pulse. Grounding the white manually will give you a nice arc out of the coil.