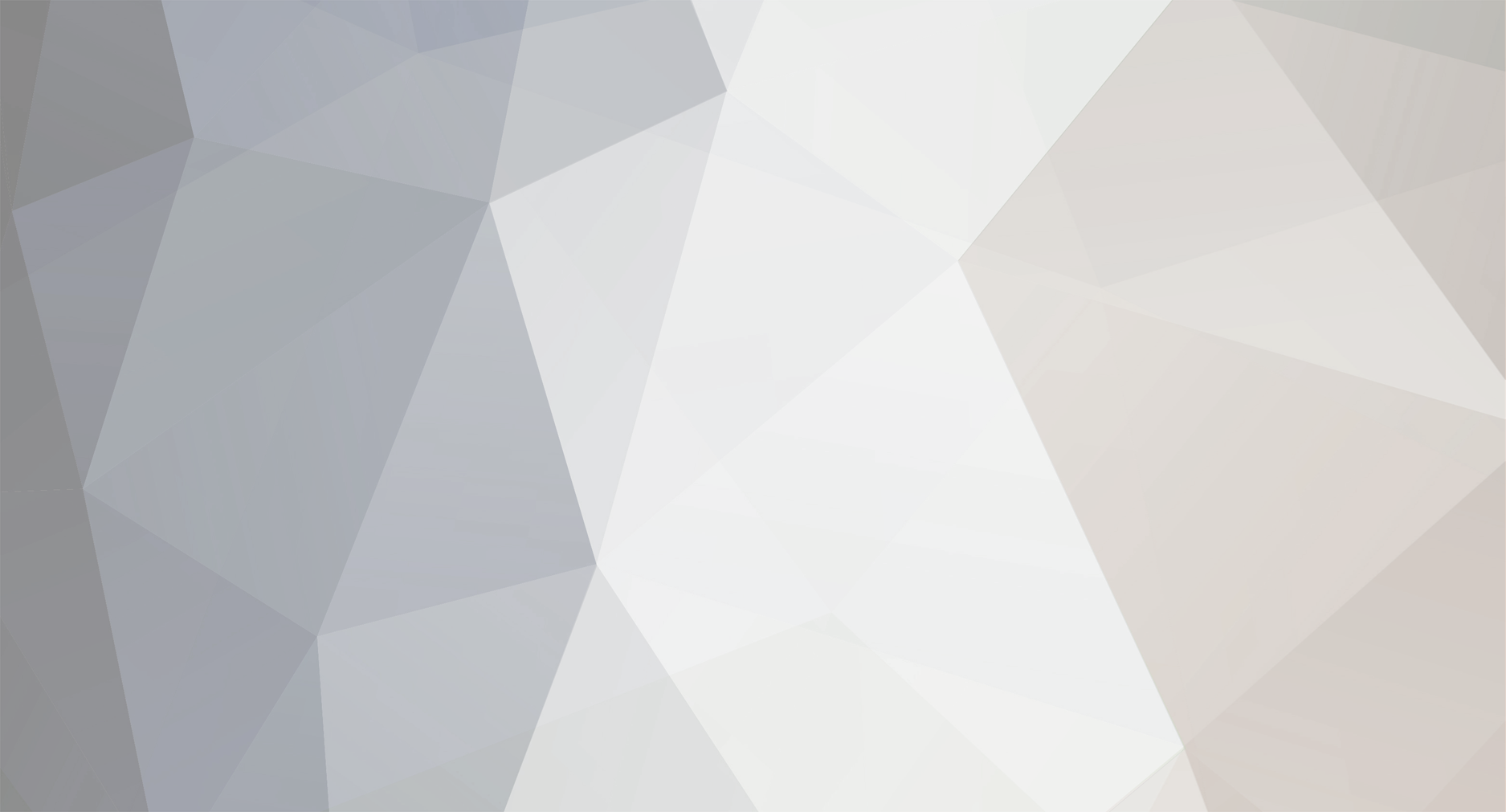
getZ
Members-
Posts
510 -
Joined
-
Last visited
Content Type
Profiles
Forums
Blogs
Events
Gallery
Downloads
Store
Everything posted by getZ
-
Your theory might be correct, but I know from actualy doing it is not instant death. I had a 70 camaro with a stock turbo 350. I used to down shift all the time 3 to 2 and 2 to 1, racing against one of my friends in what else, but a 240z. I did everything I could to out brake my friends z but never came close. I flat out abused the camaro for 3 years while going to college and the tranny never gave out. This was in Phoenix where we can see temps upwards of 115 degrees in the summer. I'll let you know how the 2004r does. If it breaks, it breaks. I'll take pictures and tell people not to down shift an automatic transmission and we can have this same discussion again.
-
I'm not babying that tranny. It was built to be run hard. I've seen a few complaints about lokar shifters on other forums regarding skipping gears going up or down. I think, I will end up modifying a b&m quicksilver.
-
Does anybody know how a lokar shifter downshifts? This may seem like a strange request but I want the ability to downshift an automatic one gear at a time. Most drag racing shifters do an excellent job of upshifting but are made to drop right into low gear from high gear. Kind of scary when you only want to drop one gear down while moving at 50mph. The reason I mentioned Lokar is because they look to be the best fit without having to hack up the center console, not to mention the can be made to look almost like a stock manual trans. I have a street bandit but that needs to be mounted way back so park doesn't smack the dash part of the center console.
-
MSD Digital 6+ confusion, think my box may be fried?
getZ replied to a topic in Ignition and Electrical
That's too bad the msd went out. They are kind of pricey. Just an FYI, an ignitor (transistor) is used to drive the timing signal because most computers do not output a strong enough signal. In general, most computers are designed to be small and fast, not handling large current. Like trying to use your flashlight battery to start a car. Relays can be used as well, but mechanical devices always have some sort of bounce when they contact. I didn't realize you were running a Megasquirt. Does it hook directly up to the msd white wire? -
MSD Digital 6+ confusion, think my box may be fried?
getZ replied to a topic in Ignition and Electrical
I couldn't find a picture, but I found my old post. The picture is kind of small, but you can get an idea of what the series of pulses looks like. http://forums.hybridz.org/showthread.php?t=103361&highlight=ignitor -
MSD Digital 6+ confusion, think my box may be fried?
getZ replied to a topic in Ignition and Electrical
That's funny you mentioned fuzzy logic. That's a real electronics word, but okay enough with my geeky sense of humor. I've never used a digital msd, but have used a 6AL and crane HI-6TR. Essentialy they do the same thing and are made need to be intergrated with the stock electronics. They are still an interface between the stock control and the coil. First, that 16 volts should not have hurt the system. Most manufacturers will build in at least a 20% tolerance range. Remember most cars will go to at least 14volts so that extra 2 volts should still be okay. I don't think that should hurt it. Voltage across the coil is difficult to measure with a voltmeter. Why? You are trying to measure a series of pulses and meters don't react fast enough. Even if it did react quick enough it would look like it's just jumping back and forth. I'll see if I can attach a picture of the signal. I still have it on my computer somewhere. If the coil seems be completely dead I would go back and check how you have it wired. Did you use the ignitor? If you are using the stock computer, you have to use the ignitor or equivalent. The computer output is a very low current output and cannot drive most devices. That is why an ignitor (or transistor) is used. The MSD goes between the ignitor and the coil. Most of the timing control comes from the computer, although I think the digital msd can do some other timing adjustments as well as rev limit. My crane unit had the ability to retard the timing based on a boost sensor. -
There is usualy always 12 volts present at the + side of the coil but not across the coil. If you measure with a meter from the positive part of the coil to ground you will measure 12 volts, but it is not what the coil is seeing. You have to measure from the positive terminal to the negative terminal, then you should see nothing unless the engine is running. Be careful it is the ground path via the ignitor that switches not the 12 volts.
-
The coil voltage is not a constant DC voltage so it can't be measured with a multimeter. The coil is only "on" when it gets a signal from the computer. I had to use a digital o-scope to capture the signal and it is a series of pulses. A higher frequency of pulses will make a multimeter read a higher voltage. Also, coils do not like a continuous dc voltage on them. I made the mistake of hooking my msd blaster up directly to 12v over lunch while working on my car. When I came back a couple hours later, the coil blew up and all the oil in the coil went everywhere. As far as the output of the coil, I wouldn't recommend trying to hook your meter up to it. It says it's supposed to put out 50,000 volts (reality is more like 20,000), but it is still way to much for your standard multimeter.
-
I agree, blue should be on the negative side of the coil. It is the ground path for the coil. It grounds through the body of the ignitor, so it is also important that the mounting bracket of the ignitor is well grounded. If you have a meter you can test the ignitor. Measure from the blue wire to the body for resistance. Apply a voltage to where the computer would normaly hookup (I used a simple 9v battery). Watch the meter go from something like a few Kilo Ohms of resistance to almost a short when applying a voltage. Sorry I don't remember which connector (horizontal or vertical plug of the ignitor) the input voltage was since I sold my turbo motor the manual went with it. A word of caution about directly wirng the fuel pump. It was hooked up to the computer so if the car wrecks and the engine shuts down the fuel shuts off.
-
If it's not the coil. I would put money on the ignitor. The coil always has 12 volts hooked up to the positive end. The computer sends a signal to the ignitor and the allows the negative end of the coil to ground. Also check that the fuel pump is turning on. For the computer to generate a signal to the ignitor it needs to know the crank is spinning. When the crank spins the fuel pump turns on. If the fuel pump never turns on it may not be seeing the crank signal. 81's have the sensor on the driver side near the harmonic balancer. The gap and position of the sensor need to be checked sometimes or the sensor can go bad as well.
-
Frustrated - flames from carb/stalling issue
getZ replied to awd92gsx's topic in Gen I & II Chevy V8 Tech Board
I took a look at my setup last night. Dart Heads, patriot block huggers and moroso blue max 8.0 mm wires. All outside cylinders will either have to go outwards or I need those accel plugs to route the wires towards the inside. Cylinders 3 and 6 come within a half mm of the headers. Nothing of mines touches but 3 and 6 will need a little header dinging. -
Frustrated - flames from carb/stalling issue
getZ replied to awd92gsx's topic in Gen I & II Chevy V8 Tech Board
I'm going to look at my dart heads to see what it is like. I havn't put any wires on yet. -
Frustrated - flames from carb/stalling issue
getZ replied to awd92gsx's topic in Gen I & II Chevy V8 Tech Board
There are shorter plugs if that will help. The accel U-grooves look about a half inch short (at least in the ad I was looking at) -
You'd think for that much money a mandrel bender would be a given. I wanted to buy one a while back until I found out how much they cost. I was thinking that picture was just a demo of their welding ability and not how they actualy build the stuff. What about the inside? Does it come out that smooth? If there are still breaks on the inside it isn't as free flowing. Seriously, I think its for people with more money than sense or if you are building a car for somebody else and they are paying for it.
-
I don't understand why it has so many bends welded together. Why not just use mandrel bender.
-
my friends landrover did the same thing. It was an over rich condition and it burned up the cat. Sounded like loose rocks in the cat
-
I have a video that came with my lincoln welder that I have no use for. PM me if you want it. It had some general theory and pointers. You can learn on your own, but I think I would take a short class at community college. Actually I still may do this. I'd like to get more consistency in my welds.
-
Motor rebuld/refresh/inspeciton advice (Long)
getZ replied to a topic in Gen I & II Chevy V8 Tech Board
do the new valve springs just drop right in? I thought stock vortecs had to have the seats machined. -
JTR sells a book on the swap, "How to Swap Chevrolet TPI or TBI. I would go for the stock computer and wiring harness than opt for the aftermarket stuff. It kind of depends on what mods you want to do to the car later and what kind of experience you have with tuning computer cars. There may be a different computer for the later model trucks that came with the 4L60E.
-
I used a "How to Rebuild the Small Block Chevy" by HP books. There are a lot of similar books out there that have some pretty good pictures as well. If you get a block somebody else has pulled out and sold to you it easy to forget where everything goes without having seen it yourself.
-
I thought I've seen information about external dimensions from the guys who make those fake blocks and a bunch of information about aftermarket blocks like Dart about internal strengthening, cylinder wall thickness, deck height, etc. What kind of information are you looking for?
-
I want to put an autometer fuel guage as well using the stock 240z sending unit. It's not important to me to be exact. Just tell me when it's getting near empty. What did you measure for the resistance range of the stock sending unit? If it goes from 0 ohms to greater than 90 ohms it should be easy enough to just add a resistor in parallel or another option is just use an autometer guage that can be calibrated. From the autometer website: Another option is if you are using the Cobalt, C2, Ultra Lite, Phantom, or Sport Comp series full sweep programable fuel level guages. (not the standard short sweep version). The full sweep programmable unit may be custom calibrated to operate with nearly any variable resistance to ground sender that has a range between 0 and 270 ohms.
-
Part of the price with someone fabricating is labor. Figure on 2x the price with stainless and almost that for dual exhaust. A lof it depends on how picky you are about the fit. The tighter you tuck it up into the tranmission tunnel, the more bends it will require. I assume you are looking for a single 3"? Those are pretty simple. I made mines for under a 100 bucks with a hooker aerochamber and aluminized tubing welded to a stock down pipe. It tucked up pretty neatly. Of course the need for stainless here is not that big a deal except to the down pipe.