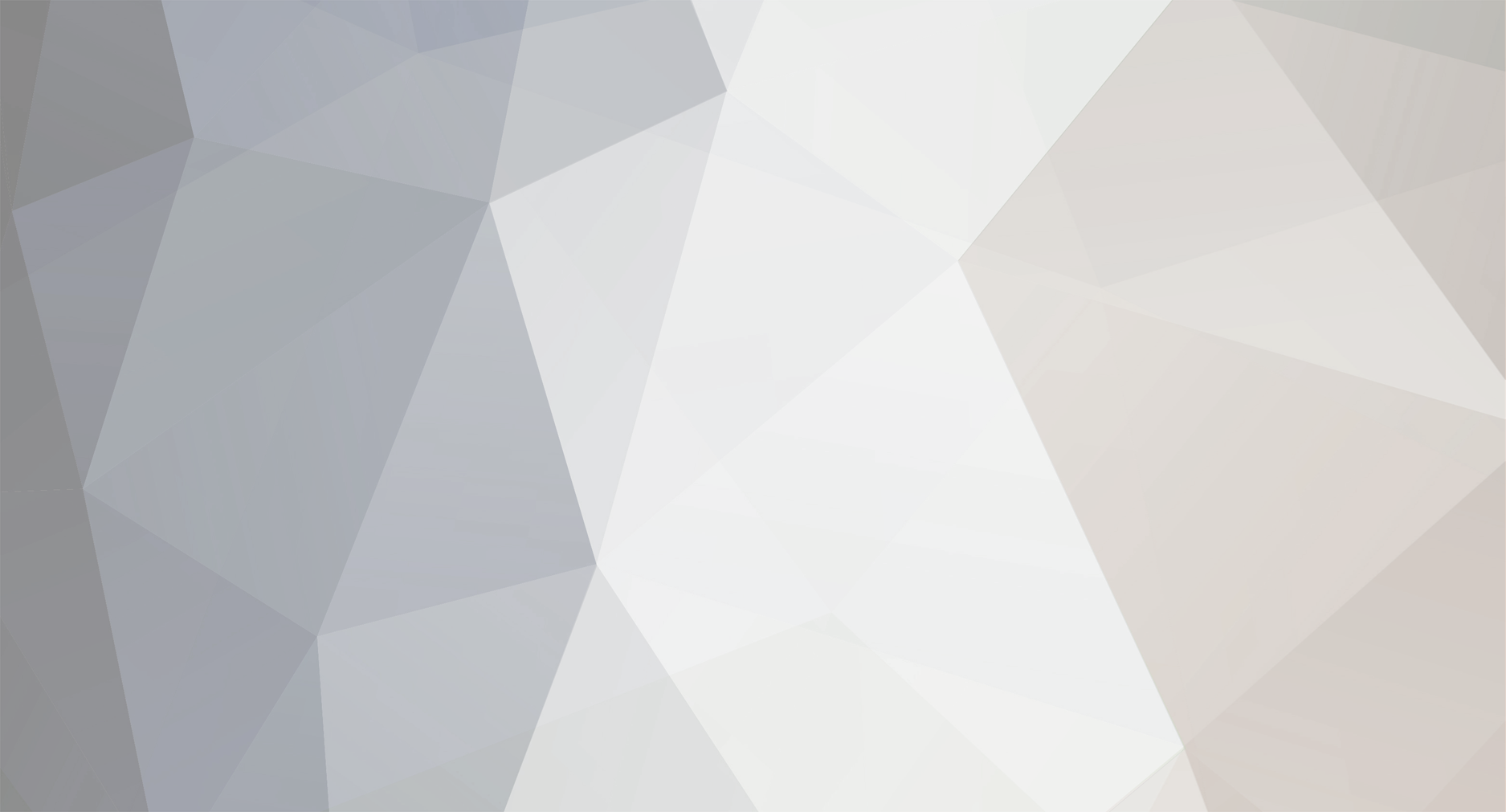
midnightmoonlight
Members-
Posts
74 -
Joined
-
Last visited
Content Type
Profiles
Forums
Blogs
Events
Gallery
Downloads
Store
Everything posted by midnightmoonlight
-
I have a question about installing foam into a fuel cell. Ive read I should put a screen over the sump so the foam doesnt get sucked into the fuel line is this right? I also read I should wash the foam before putting it in the cell. How should I go about washing the foam? Should I rinse it with gas? There does seem to be some flakes of foam coming off the foam when I shake it. I bought 3 blocks that will fill my entire cell is that to much. I was told I need 3 blocks for my 8gal cell. Any other points I should know about putting foam into the cell?
-
Anyone have the specs on the slave roll pin or a GM part #. I think its metric. I tried some hardware store roll pins but couldn't find the right size
-
Tuner cat problems
midnightmoonlight replied to midnightmoonlight's topic in Gen III & IV Chevy V8Z Tech Board
I had 2 bad installs now I have it right but Im getting an error: invalid response from PCM. I have to check the jumper on the usb cable and hope I dont have a OBD2 computer. My PCM is 16209461 BMFN *86BMFNK14322A59X* Im looking for a way to verify this is a OBD1 Computer. Its from a 95 Firebird -
I have the tuner program from CATS. Everything is installed right. cable software, definitions, ect. Im not getting anything from the tuner program. I can see the PCM from a tech1 and a tech2 but tunercat has a problem. I re installed tunercat. All I get for options on the top of the tool bar is File, Options, and Help. Of course the help files dont work and there isnt any real options under Options. What am I missing? Software is registered. Im out of ideas. Key is on just doesnt make sense. Cant find any place for port settings.
-
1995 obd1 obd2 Touble
midnightmoonlight replied to midnightmoonlight's topic in Gen I & II Chevy V8 Tech Board
Okay I have no switched power with a bit of investigation. I have switched power to the LT1 fuse block at the ignition fuse and to the two harness connectors that meet the main PCM harness. All the fuses and relays have + and switched where they need it. Now what am I missing I'm not getting switched power to the black and blue PCM connectors for ignition feeds. -
I have a 95 LT1 F-Body thats data link is giving me problems. It was the one with a OBD1 computer but had the OBD2 data link connector. My problem is I have the OBD1 connector hooked up like a OBD1 should be but Im not getting any data. Everything is hooked up right and all the PCM power and grounds checked out. I used the D20 and D30 connected to the obd1 and have it grounded. I double checked that all the connections are right m b and a. Is there a different hookup for this obd1 computer that uses a obd2 conecter?
-
So you think if I lower my sway by 1" at the frame mounts I should also drop the end link by 1"? Will this affect the geometry at all?
-
The LSD r200 rear end (set 3/4" lower) with the RT mount hits the sway bar. The larger yoke for the LT1 swap hits the sway bar. I would have to lower the sway bar by 1" at the square poly mounts to clear the drive shaft yoke. The driveline is set perfect with all the correct angles so if I change the sway bar pickup points by 1" do I mess up the geometry of the suspesion? I dont want to increase the angles of the tranny and diff because my driveshaft is right at 1.5 degrees and thats where I would like it to stay. Now I could raise the diff one inch in front and at the mustach bar but then I will have almost no driveshaft angle anymore. Hmmmm Ive also read its better to have no rear sway bar with the LT1 swap with no LSD but this car has LSD so whats the best route to take from here? Thank You
-
Thanks for the help and clarification. There really needs to be a sticky about the specifics of driveline angle and it sounds like your the guy to do it
-
So I should be good with tranny 2.5degrees down, diff 2.5 degrees up, tranny and diff lined up on the vertical plain, and my drive shaft at 1.5 degrees? Im confused by #3 in that the suspension doesnt effect the rear end or tranny. So on a Z the suspension travel doesnt play a roll right? Thanks for the help
-
The article is the picture I posted above. Ive read everything I can find here and everyone talks about the driveshaft angle being 1-3 and the diff and tranny need to be parallel. The way Im seeing it is the angle of the diff and tranny dirrectly effect the driveshaft angle and that just because the drive shaft has a 3 degree angle doesnt mean the ujoints opperating angle is 3 degrees because you have to take into account the angle of the diff and tranny. With your set up your tranny and diff are not parallel. Which is supposed to be a problem because your ujoints are at different angles and should cancel each other out so there the same. Do you know what your driveshaft angle is? How long have you been running this set up? When mine diff was 4.5 up tranny 2.5 down I only had about .5 degrees on the driveshaft. Thanks
-
This is what Im refering too. The way I understand it is operating angle is what needs to be 1-3 degrees. Right now Im at 2.5 tranny 2.5 diff 1 driveshaft. So that gives me 1.5 operating angle isnt that going to work?
-
I just need to clear something up. If my tranny points down 2.5 degrees and my diff points up 2.5 degrees my drive line will work well if the angle of the driveshaft is between 1 and 3 degrees? Im confused because of an article posted here shows operating angles should be less then 3 degrees which is different then the actual drive shaft angle. Operating angle takes into account all of the angles. In the article the example shows tranny 3 degrees down, drive shaft 4.9 degrees down and diff 3.2 degrees up. The operating angle is 1.7 and 1.9 which is the drive shaft angle - diff angle or tranny angle. So is the 3 degrees operating angle or drive shaft angle? Then another article shows it different too. Engine 1 degree down diff 1 degree up drive shaft 2 degrees up. They refer to working angles engine+drive shaft=3 Diff+drive shaft = 3 and 3-3=0 and thats good. Which I now realize, is the same as operating angle above
-
Any tips on coast down testing? I cant use a wing it can only be a spoiler. I was hoping to see some wind tunnel tests next time on these types of spoilers. I was going to make the spoiler from lexan. I have a large 10" nascar type spoiler template made but then I thought the 4" may work better because in the tunnel info it shows lift with the 6" rear spoiler.
-
In the class rules for FP I can either use a 0-10" spoiler at the rear of the deck lid or a 0-4" spoiler at the top of the deck lid above the rear glass. These spoilers can be at any angle but they can't come out further than the body work. So whats the best set up for speeds 65 and under from an aerodynamics point of view?
-
I need some cheap an fittings or something that is similar. All I need is to come out of a plastic fuel cell in three spots. 3 90 degrees to a barbed end for rubber fuel line. I dont see the sense to spend big $$$ on aircraft grade fittings on anything less than an airplane. Anyone have alternatives to the AN fittings coming out of the tank?
-
I understand the roll over valve/vent line. My question is the valve on the cell cap that lets air out and has no provision for a line
-
I did something similar to this and shaved the outside handle and lock.
-
The Jaz Fuel cells have a one way check valve vent in the cap of the fuel cell. I have a Harwood cell thats the same. It lets air out if the tank expands. The way Im understanding it is I still need a vent line to let air in correct?
-
race tire allingment
midnightmoonlight replied to midnightmoonlight's topic in Brakes, Wheels, Suspension and Chassis
Im triing to get my alingment set so I can make marks to change it fast before autox events with out strings. So should I measure toe at the tire edge or just go with the Rsin(x)=y where r is tire dia. x=angle and y=inches toe? -
race tire allingment
midnightmoonlight replied to midnightmoonlight's topic in Brakes, Wheels, Suspension and Chassis
Okay I get it. I think I read some mis info out there or just mis read it. Where is the ideal place to measure? rim or outside edge of tire? Thanks -
race tire allingment
midnightmoonlight replied to midnightmoonlight's topic in Brakes, Wheels, Suspension and Chassis
Back to alingment...I set my toe 1/8" out at the rim. Like the picture above. I got everything finished up took my string lines off the car and realized I may have screwed up. Let me see if I have this right. A 1/4" difference measured between the front of the front tires compared to the back of the front tires = 1/8" toe in or out depending on where the difference is front or back. So if this is right I nailed the 1/8th inch toe out that I wanted....but its at the rim. Where is the right place to measure for toe? Im assuming now that Im done, it should be at the outside edge of the tire. -
race tire allingment
midnightmoonlight replied to midnightmoonlight's topic in Brakes, Wheels, Suspension and Chassis
I have been reading some of your posts about slotting the cross member to set the control arm in the perfect spot. I need to re-read it again so I set up my dial indicator correctly. I wont do this until july so I have plenty of time to get ready. Am I adding extra stress to my ball joint by having the control arm not right? One other thing I did take your advise on the air hammer to get the rear stubs out. Except the air was my arm with a sledge and a cold pointed chissle in that nice hole. That worked great. If I had the air chissle it would have been even better. -
race tire allingment
midnightmoonlight replied to midnightmoonlight's topic in Brakes, Wheels, Suspension and Chassis
I was going to try running strings to adjust my toe. and make a gauge like this Now do you set your toe at the track by x number of turns gives me x toe from measurements you took at an earlier date? I really need to go back to the drawing board on my front end and change the CA inner point to fix my geometry. I need to do some research. As I see it I should move my point 7/8" up and 1/4" out and add "bump steer" spacers -
Should I adjyst my toe with my race tires on if my main concern is the track? Basically do the tires effect toe adjustment?