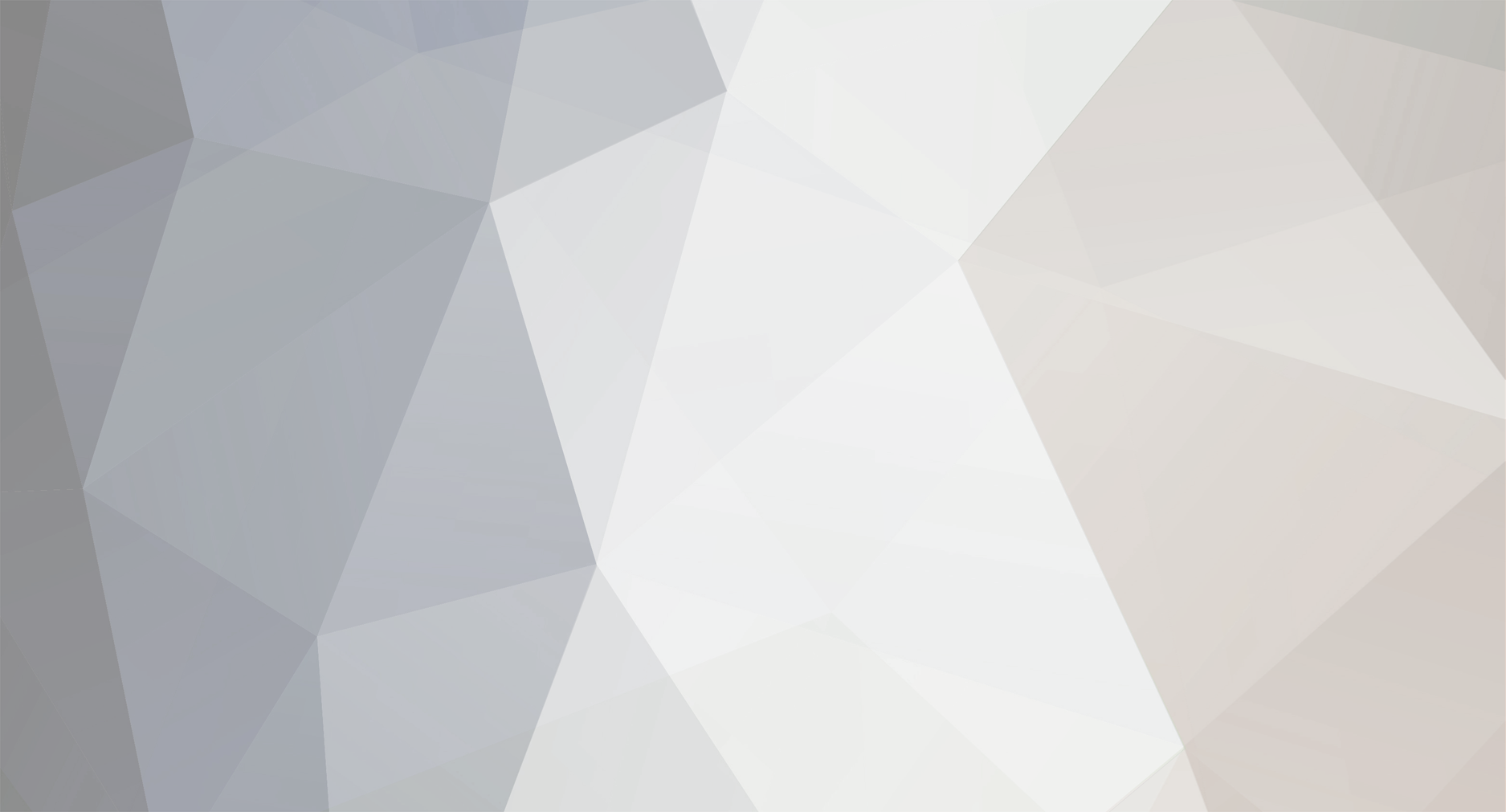
weedburner
Members-
Posts
44 -
Joined
-
Last visited
-
Days Won
1
Content Type
Profiles
Forums
Blogs
Events
Gallery
Downloads
Store
Everything posted by weedburner
-
Manual Trans? Inexpensive Way to Get More From Your Rear...
weedburner replied to weedburner's topic in Drivetrain
The problem with the oem dampers is that they slow the pedal's whole release cycle, and are not adjustable. There are aftermarket dampers that are adjustable with variable orifices and changable orifices, but they still slow the entire pedal release. My slipper is adjustable not only on the rate of pedal return, but also the point in travel from where the pedal's return is delayed. Reaction time does not suffer. -
Manual Trans? Inexpensive Way to Get More From Your Rear...
weedburner replied to weedburner's topic in Drivetrain
You are not slipping the clutch for very long, typically just an added 1/2 to 1 second of slip. My personal car puts 700+ whp to the ground, even at that level the added slip is not a problem. I've used the slipper on ceramic, kevlar, DF and sintered iron linings. If you are making 500+hp go with the iron, but at lower levels even a good quality stock lining is fine as long as the lining is appropriate for the power level. -
If you have a manual trans and can pull off minor fabrication, here's a simple way to get more power thru your stock rear axles. Just a simple, commonly available, hydraulic storm door closer cylinder installed on the clutch pedal. It allows tuning a bit of "slip" into the clutch's initial engagement, damping the peak shock loads as power is being transmitted to the rest of the drivetrain. It's adjustable for exactly where in the pedal travel that it becomes active, and adjustable for rate of release from that point on (it controls slip only during the final part of engagement). The cylinder is hydraulic (not pneumatic like most), with characteristics similar to those of a 90/10 shock, pulling the rod out is easy, only the return stroke of the cylinder is controlled. With the hillbilly style slipper installed on a clutch pedal, the final bit of clutch pedal's release is delayed, not the whole release cycle. The rest of the clutch pedal's travel works like normal. During normal driving you will not even know it is there...no detectable difference in clutch feel. If you are using the clutch pedal during shifts, the slipper will soften drivetrain shock during gear changes as well. We first came up with the idea back when we were drag racing using Saginaw 4spds. We went thru a lot of them and could pretty much predict which gear was going to fail depending on which ratio gearset was in it. After playing with the hillbilly slipper, we quit breaking gears in the Saginaws, and were able to get the 60's down to 1.45 before we started twisting mainshafts. Our experience is that the Hillbilly Slipper is not going to help much after you start twisting mainshafts. How does it work?... ...Basically when the clutch pedal is depressed, it pulls the rod out of the cylinder. When released, the clutch pedal comes out unrestricted until the nuts on the cylinder's shaft contact the dash bracket. From that point, the rate of release is controlled by the adjustable orifice inside the cylinder. How is it adjusted?... ...Adjusting the nuts on the threaded portion of the shaft changes the point in the clutch pedal travel where it's release is delayed. From that point, turning the dash knob changes the speed of the pedal's final bit of release. There are 10 turns of adjustment on the knob. At "0" turns the pedal is delayed very little, barely noticable. At "10" turns, the pedal takes about a minute to return. Typically, the rate of release is usually set between 2-1/2 and 4 turns. When adjusted to protect your drivetrain... the slipper's main function is to delay/soften the clutch's final engagement, effectively damping the peak shock loads that the drivetrain will see. When adjusted for making a fast pass at the strip... the slipper will delay clutch hookup, allowing the engine to spend more time operating closer to it's power peak. If the clutch grabs too quickly, it will pull the engine down, away from it's power range, every time the clutch is released. While experimenting, we found our car to be much quicker when the clutch was slipping a little more than we liked. We found the optimum slip to be one that did not pull the RPM down during launch, but allowed the engine to go straight to it's power range and stay there without activating the shift lite prematurely. It's affordable too... ...The only change made to the $15 hyd cylinder was to add a section of 5/16" all-thread to the end of it's shaft. The slipper works on both mechanical and hydraulic clutch linkages, as it directly attaches to the clutch pedal itself. Below are some pics of the parts we used on our project. They were all purchased at our local Lowes's Home Improvement... ...Wright Products VH440BL medium duty door closer ...Hilman 881357 bar knob (5/16" x 18) ...5/16 x 18 "all-thread" (comes in 3' lengths) ...5/16" x 18 flange nut ...5/16" x 18 jam nut ...Delrin plastic (for making the dash bracket slide bushing) above items likely less than $50 at your local hardware store. The VH440BL actually comes with attachment brackets that could be modified for use on a clutch pedal, but we made the bracket that attaches to our clutch pedal from scratch. Here's a link to a more refined version...... http://grannys.tripod.com/hillbillyclutchslipper.html Here's a link to an install & tuning guide... http://grannys.tripod.com/hillbillyslipperinstall.html If you would like to quit breaking transmissions, rearends, or halfshafts, installing a Clutch Slipper just might be your answer.
-
Another thing to consider is that after you get a faceplated or pro-shifted transmission, you will likely quit letting other people drive your car.
-
My transmission has roadrace style faceplates/dog rings, which stay in gear. The Drag-only sets have little or no self holding taper, and fall out of gear easily. I would not recommend pro-shift unless faceplating is not available. The edges can burr up and when they do, the slider will not slide over them freely. The only fix is to take the trans apart and dress them up. I used to run a pro-shifted box on the street/strip, it was out about every 4-6 weeks for dressing up the lugs.
-
The wham! is only the engagement of the lugs, as the clutch disc instantly syncs to it's speed in the next gear. You don't have to drop the clutch at every gear change, so extra drivetrain breakage is not a given. The lash is just the open space between the drive lugs. The space is quite a bit wider than the lugs themselves, making a wide "window" for the lugs to drop into. If the fit was tight, everything would need to be aligned perfectly before the lugs could engage. With the wide window and a self holding angle on the face of the lugs, they draw together instantly when contact is made. Just accidentally bumping your shifter with the engine idling is enough to put the car into gear. Since there is no such thing as easy engagement without rev-matching, getting the engagement of the lugs completed as quickly as possible means less wear/tear on the edges of the lugs. Below is a pic of a faceplate slider and a dog ring that welds to the gear itself to replace the stock synchro style lugs. Both sides of the slider pictured has lugs, it justs slides back and forth on the mainshaft to engage whichever gear is selected... Below is a pic of stock engagement teeth (lower left), a "pro-shift" style ring (lower right), and a faceplate dog ring (top center)... Here's the inside of my transmission... notice that i kept the stock synchro on 1st gear.
-
Pretty much impossible to miss a gear.
-
I have a street/strip car w/ a 4 speed. Stock synchro on 1st, faceplated 2/3/4. It's been bulletproof for the last couple years. When you are idling thru town w/ a big cam, the extra lash can make banging noises under some situations.
-
When i made mine, Liberty did not offer a 1st gear synchro option when they did a faceplate conversion on a Toploader, but i hear that they do now. It's a busy time of year for them, might not be very quick on service, but you can give them a call at 313-278-4040, email is libertysgears@aol.com
-
They are "road race style" with a back cut angle of a few degrees to keep it from popping out of gear. The "drag only style" have little back cut angle on the engaged faces and a ramp angle on the trailing side to kick the slider out of gear when the force thru the gearset reverses. If the slider is split, you actually engage the next gear before the current gear dis-engages. Definately drag only, kicks out of gear on decel.
-
Here's a link to the clutch slipper setup i designed... http://grannys.tripod.com/hillbillyclutchslipper.html used on this car... http://tntrc.com If your clutch is hydraulic, a line-lock solenoid could be used to make it button-release on launch.
-
Another option is a Ford Toploader, stronger than the T5, Muncie, or Super T-10. I bought a Toploader 4 spd off craigslist for $275, looked rough and the front collar was broken. (3) faceplates- $65/ea (2) faceplate slider- $100/ea input shaft- $150 master rebuild kit- $175 hyd t-bearing- $150 RAM clutch disc- $225 I have a lathe, so i installed the 2/3/4 gear faceplates myself, and modified the 1/2 slider for 2nd gear faceplate / 1st gear synchro. Also turned down the front collar to allow using a Chevy hyd t-brg. In your case, you would also need... ...bellhousing ...driveshaft ...shifter mods You could probably sell the T56 for enough to finance most of the swap. Shifting is foolproof. If the engine even slightly coughs and the shifter has any preload at all, it's instantly into the next gear even without the clutch. I faceplated 2nd gear in a Saginaw once, when 1st gear broke, the trans instantly short-shifted into 2nd gear before i even knew what happened. I use mine for drag racing, but it's been bulletproof for 2 years at about 700rwhp...
-
I cut all the parts out by hand with a plasma cutter, it sure would have been a lot quicker to just draw something up and cut the parts out on a cnc table. No idea how long it took to make this one, i spent most of the time coming up with the process.
-
I have thought about grinding some little directional slots in the face of the synchro rings to give any excess oil somewhere to go, but i went straight to dog rings before i got around to trying it.
-
Thanks guys. Most of the stuff i do is for RX-7 V8 conversions (since that is what I do), but the tech in that project wasn't really brand specific.
-
Basically, I made my own bellhousing to adapt a Ford Toploader 4spd transmission to my old school SB Chev V8. I can buy one for around $450, but it's a heavy 1/4" thick steel monster, and I prefer building my own lighter parts if i can. I'm not concerned about it not being "SFI certified", as it's just a fun street car and i have no desire to make it legal for the track. The mock-up began with an old 400 block and an empty transmission case. I am using the alignment bar from my rearend narrowing jig to keep everything straight and true. I spent a couple nights machining some steel pucks to fit in the block's main bearing bores and also the bearing bores in the transmission case. The pucks have an 1.501" hole in the center so that my alignment bar will slide inside everything to keep the engine and transmission bores concentric. I made a ring to center the plate that the transmission will bolt to, and a tube spacer that will set the desired distance between the block and transmission face. I have also made the rear plate that the transmission will bolt to, and have laid out the the flange that will bolt to the block and serve as a pattern for the block plate that will fit behind the flywheel. I'll snap some pictures in the next day or so. Working in my spare time after hours, I expect it will take me a week or two to get it done. The transmission is getting some special work as well, getting faceplated in 2nd, 3rd, and 4th. I'm adapting an aluminum tailhousing from an SROD overdrive trans to replace the Toploader's stock iron piece to shed some weight. Also machined down the Ford throwout collar so that I can use my existing Chevy hyd throwout bearing. Here's the pattern I made out of 1/4" steel. All the hole locations were laid out, centerpunched, and drilled 3/16" so that the pattern could be transferred to the blank piece of 1/8" that it's laying on, which will be used to make the block protection plate. The steel pucks on the right are the pilot rings and spacer that i mentioned in an earlier post that locate everything in the correct positions for mock-up. Later this pattern will get the bolt holes drilled and the large center hole will be cut out, turning the pattern into the flange for the front of the bell... Here's the drawing I used to lay out the block bolt pattern... This is the block plate after it was cut out and drilled. The large hole in the center is for the crank's flywheel flange to stick thru, and the 2 larger holes on the sides are for the locating dowels in the block... This is the pattern after i drilled it out and cut the center out. It is going to be the forward flange of the bellhousing that bolts to the block, the large hole in the center is necessary to clear the flywheel... Here's the block plate on a block. The upper "wings" were added as mid-mounting points that will hang the back of the engine at the firewall... Here's the block plate and flange on a block. The block plate will be sandwiched between the block and bellhousing as shown. I'll soon be creating a hole and pocket for the starter. Here's a pic of the rolled ring welded to the bellflange. All the holes still fit perfectly... The mid-mounts incorporated into the block plate allow me to easily remove the bellhousing/clutch/flywheel from the car without needing to support the engine. Greatly simplifies my clutch and transmission maintenance. Here's the alignment bar in place in the block, as well as the spacer that sets the depth between the block and trans case... Here's the trans case in position located by the pilot rings... I had to take it out of the fixture to make sure i had created enough room to install a SoftLoc clutch, so i figured i'd snap a few pics of the progress. I started making patterns for closing in the bell by laying out the the top section on posterboard. I quickly realized it was much easier to just cut out slightly larger pieces of posterboard, hold them in place on the bell, and simply apply a little pressure by running my finger around the edges of the steel. This puts a small crease in the posterboard and transfers the exact shape needed, a much quicker way to create a pattern... The transmission plate is still only tacked in 4 places. After all the rest of the welding is done, i'll put the bell back into the fixture, cut the tacks, and re-position the plate for the best alignment possible before welding it in place. I doubt there will be any need to machine the block or transmission mating surfaces. Still need to make a pocket for the mini-starter that's going on the car... Added a cutout for the mini-starter's drive... Added a starter pocket to the bell as well... Next is adding a few holes, one for setting the clutch gap and a hole for the hyd t-brg's hose. After that, i'll drill all the bolt holes to finished size, sandblast it, and send it out for powdercoat. UPDATE-...I went to a 3pc style bellhousing...blockplate, midplate, bell/can. Now i can remove the engine from the car with the flywheel and clutch, and leave the bell and transmission mounted in the car. I can also remove the transmission/bell/clutch/flywheel from the car without supporting the rear of the engine. I also added a couple external "ears" to the block plate, which gives me some easy attachment points for lifting the engine. The finished bellhousing itself weighs in at 16.3lbs, lighter than a "Quicktime" bell. The entire 3 pc assembly shown below, including the block plate, midplate, and bolts weighs 26.2lbs. I'll take some pics of the engine lifting fixture i made for it. It plugs into the blockplate's added "ears" and into an "eye" that screws into a hole in the top of the waterpump. It fits over the complete engine with the aircleaner and distributor in place. When using chains, finding a perfect balance point without damageing something can be a challenge. Having a dedicated fixture that plugs in makes the job easy. Been thinking about attaching the radiator to the engine just to make choosing between a couple engines that much easier.
-
Recessed engine mounting (into the firewall)
weedburner replied to z1 zonly's topic in Fabrication / Welding
Here's a 1st gen RX-7 that i set the engine back 10" in... I just cut the entire tunnel / firewall out and trimmed 10" off of the rear, re-installed. 18ga cold rolled steel make up the seal panels on the sides up front. The sbc distributor just barely wiggles down past the stock windshield. The front motor plates are from a 410 sprint car. Radiator mounts off of the engine and sits on tabs welded to the front crossmember. Still looks pretty stock on the inside. The pedal box was spaced rearward with simple 8" aluminum spacers, requiring longer pushrods for the brake/clutch masters. Seats were re-located rearward too.