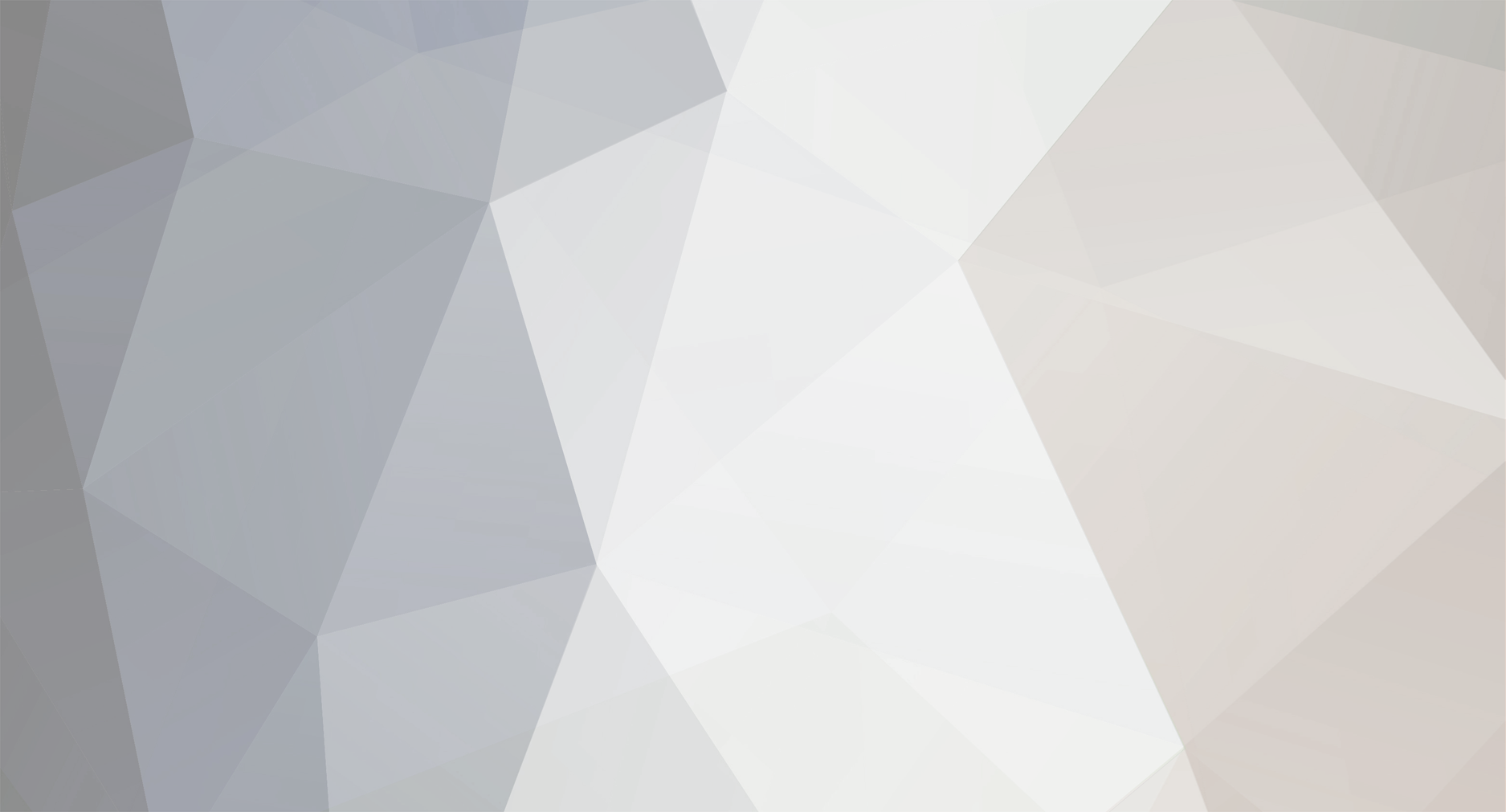
mark
-
Posts
1567 -
Joined
-
Last visited
-
Days Won
4
Content Type
Profiles
Forums
Blogs
Events
Gallery
Downloads
Store
Posts posted by mark
-
-
Too bad one of those was not around at the wind tunnel test day.
-
Thanks for the info guys.
-
Who makes those?
-
How long have you been running the new halfshaft with the 930 P car cv's?
Did this start after the new halfshafts?
-
Mark,
I've been looking to do the same thing with floating 13 inchers but was looking at 170-7038 hats. They are 2" offset and wouldn't require redrilling. Are you working with Dave to tweak the caliper brackets? Maybe tweak them to relocate the caliper to make up for the .12 difference in hat offset would work? I have MM billet 5 lug hubs and I'm not sure if there is an offset difference between them and the AZC pieces. If at all possible I'd like to have the caliper positioned to use an off the shelf hat and rotor. Modifying the caliper mount seems to be the likely way to go.
What do you think?
Joe
The hat you have specified is not a floating hat. The rotor mounts solid to that hat. A 2 inch offset on my set up would require moving the caliper .25 inches toward the outside of the car. That reduces the bracket thickness to only .12 inches. That would not work. I reduced the thickness of the bracket to .25 inches and everything lines up on my setup. How close does a 2 inch offset get you?
You hubs may be a different offset. If you can use that hat and your hubs and get a 13 inch set up to bolt on, go for it. I went with the floating setup because this is a track only car and it eats rotors for lunch.
I had contacted Dave a while back about making some brackets in steel and he was not interested at that time. The hot ticket on this setup would be to get Dave involved. It would require a run of hubs that were
1) Offset .12 inches toward the inside of the car
2) Had a .25 inch thick shoulder to center the brake hat
3) had the holes drilled and tapped to accept the locating screws around the perimeter to hold the hat to the hub.
All that would be needed then would be to drill a new lub pattern in the willwood hat. I'd bet Dave could have that done also. It would be a nice option in my opnion.
-
The AP set up was going to cut into the kids college fund. This one ain't cheap but the kids can still go to school.
-
They must be made of some really lightweight material. I haven't actually tried them, but I'm pretty sure none of my rotors would float.
jt
There made of flubber.
-
I would love to be there and I could have probably gotten the car together 10 years ago but I don't move as fast as I used to.
-
That hat is as close as it gets unless you have a custom hat made.
I always need more brake especially at CMP.
I'm hoping a floating assembly will get rid of the pulsations that come with a few hot laps at CMP on rotors that have only a couple of track days on them.
I think the way this works is that a floating setup allows uniform expansion of the rotor since it is not bound to the hat, reducing pulsation, rotor wear and cracking.
-
Looking for comments. This is just a mock up caliper, I know the bleed screws are down.
This uses a wilwood hat pn 170-6583 with a new lug pattern drilled in the hat.
Wilwood rotor 13.06 x 1.25 GT 48 curved vane rotor
Hardware is from wilwood
Caliper brackets are custom made from .25 inch thick chrome moly steel
I have Arizona Z's aluminum hubs.
With a few tweeks of the hub by Dave, his stock brackets could be used so the only machining needed would be drill the new lug pattern in the hat.
-
I measured the depth of the CV housing and figured what thickness would be required to keep th CV in the housing with a little to spare.
-
Dead strut insert? Have you had the rear apart to check?
-
-
If you have stops on both ends, you need a longer axel. Sorry for the bad news.
Let us know what you end up doing.
-
You need a stop on the inboard and outboard side
-
Good luck, It took me a couple of hours to get mine right. One side was perfect right out of the box. The other took some work to get it right.
-
,
Jon,
are you sure you are shimming in the right direction? I had the same problem the first time I did it. I was shimming the low spot and I should have been shimming the high spot. If you are measuring from the outside face of the rotor, and shim the low spot, it makes it lower. Shim the high spot to push the rotor back. Hope that makes sense.
Went out and bought a couple cheap feeler gauges and used a hole punch to make shims out of them (drilling DOESN'T work). I don't get what is going on. I find the low spot, shim it, and then it is LOWER afterwards. I triple checked to see if I'm reading the dial indicator the right way, and I am, so I'm just a bit stuck. I guess tomorrow I'll shim it the exact opposite of what I think I should and see what that does, but I really don't think I have the dial indicator fundamentals wrong. I'm also worried that I might be chasing the torque on the rotor. If we know that torquing the rotor warps it just a hair, and so I'm taking the bolts off, shimming, and putting them back on and then getting different readings, isn't it likely that just tightening the bolts again is the cause?Thinking hard about taking all the shims off, torquing the bolts, cutting the rotor, then reinstalling and seeing what that does on the dial indicator. I suppose the other thing I could do is take a little more off of that pilot hole, just to make sure that is not the issue.
Frustrated...
-
A guy named Matt Sullivan. His shop is in Charlotte. He actually did a better job than I wanted. How cool is that.
-
Nice job. I love the color but then I am biased
-
Another great looking Z car. Thanks for the pics. Is it red or orange? Let me know when you are thinking about getting it to the track.
-
Here is the car at VIR when it was ugly. Still fast but no pays attention to a primered car. Mike Kelly was nice enough to post this video.
-
My vote is NOT fake. I think the kid is a future death row inmate. The videos are funny stuff.
-
Cmp is in Kershaw SC. About 1.5 hrs from Charlotte. Thats the closest place for me to go. I love VIR and look forward to getting back there soon. Road Atlanta and Roebling are also tracks I get to occasionally. I have not been to Road Atlant in a long time but hope to get back there soon also.
Any pics of you project? We used to live in Morrisville under the runway for RDU. My wife worked in Apex. Nice town.
Great looking car and fast.. Reading your post is CMP your local track? Or do you come up to VIR or down to Roebling? I used to drive/instruct with Tarheel and other clubs in the area... Got out of it about 8 years ago. It's a long story involving a ex wife.... But I've been building a LS1 240Z for street and track for about 3 years. I'm hoping to get it on track late next year...Thanks for the thread it makes me want to get out there in the garage:).. -
Any day at the track with Z guys would be a fun day.
Koni Shock Adjustment Help Needed
in Brakes, Wheels, Suspension and Chassis
Posted
Tom,
Glad to hear you have found the problem. Keep us updated with a report from VIR.