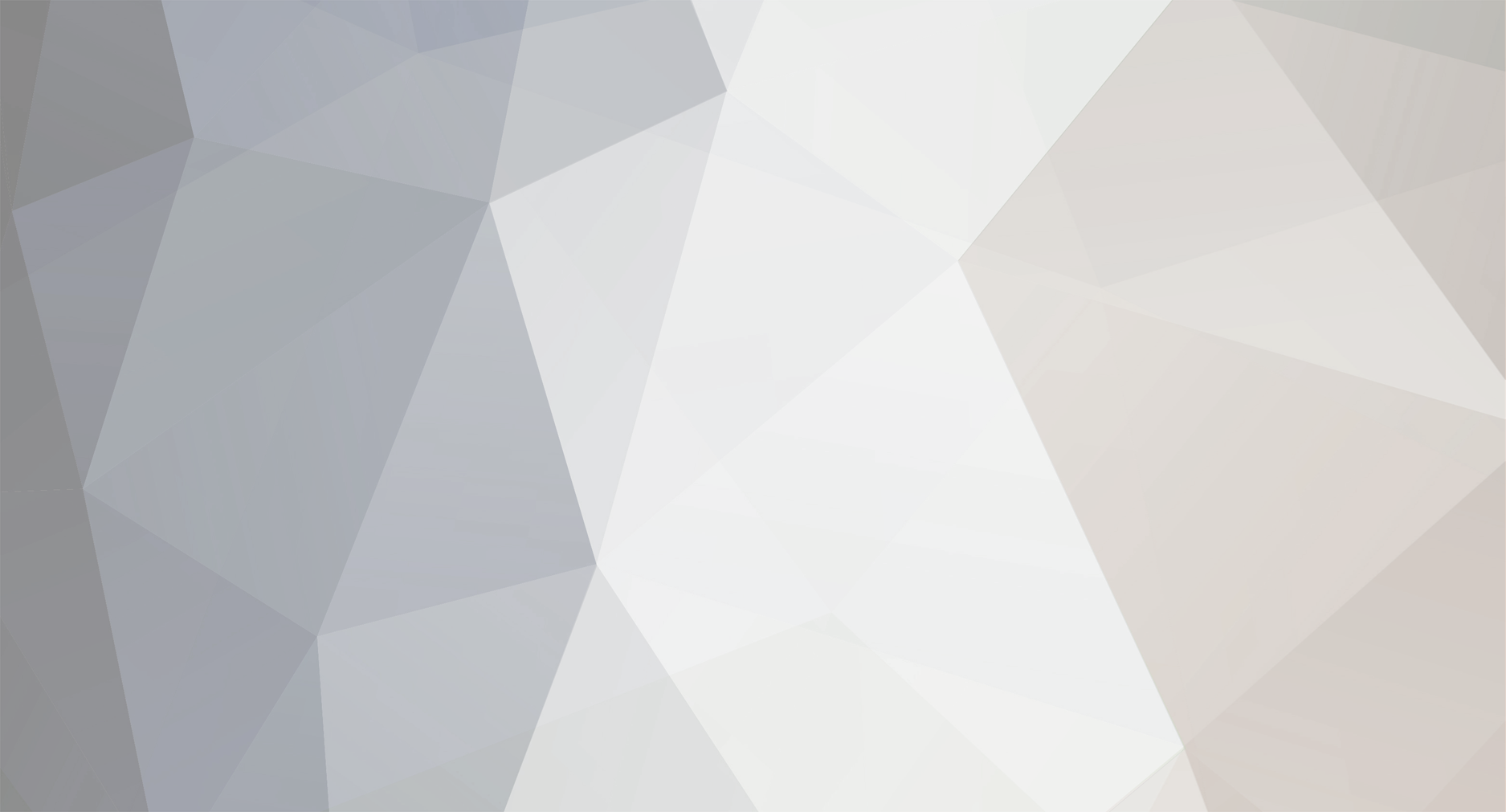
AtlantaZ
Members-
Posts
259 -
Joined
-
Last visited
Content Type
Profiles
Forums
Blogs
Events
Gallery
Downloads
Store
Everything posted by AtlantaZ
-
When I try to use the Trigger Wizard in TunerStudio, it's grayed out. So I don't seem to have any way to adjust my base timing offset. I have tried playing with the trigger wheel offset under the ignition settings, but to no avail. I still can't get the engine to idle above 600RPM, and I can't get it to run for more than a minute or so. Any other ideas?
-
It sounds like I need to buy or borrow a timing light. I never have adjusted timing before... what number or setting in MS am I adjusting? And how do I know when it's right? Finally, I assume I need to mark the damper timing mark with white paint or something...? And since I am using Derek's VR bracket, I may have to take the bracket off, mark TDC some other way, and continue from there...
-
Another dumb question: do I need to turn on "tacho output" in Megasquirt to send timing info to the EDIS ignition module?
-
Update: Will now hold a rough idle at ~500RPM The only thing I changed was unplugging and reconnecting the spark plug wires, and now I can get it to crank almost immediately and hold a 500RPM idle. However, when I step on the gas and feed it any air at all, the engine goes dead. So I can get it to idle-barely-but can't get it to throttle up at all! What do I adjust next? Also, I discovered that my upgraded 280zx alternator apparently needs a diode in the exciter circuit, as I can't kill it by turning off the ignition.
-
Here's my log file and Megasquirt settings video. I humbly ask for anyone with the time and inclination to give these a look and point out any glaring problems! After that, I'm down to troubleshooting the timing. And I don't know how to do that without a lot of work... http://www.youtube.com/watch?v=5Hsea8pgQdU
-
I'm starting to run out of obvious things to check. Since I'm using EDIS, I assume that it should at least run in "limp home" mode if Megasquirt isn't sending it valid timing information... Now that I've properly calibrated the TPS, it's definitely moving fuel. It coughs and splutters up to about 400-500RPM, then gives up and goes back to a 100-200RPM cranking cycle. And the garage is now full of hazy bluish-white smoke.
-
I noticed that and am looking for the low impedance settings. Have any suggestions?
-
Posted my plea for help on the Megasquirt forum: http://forums.hybridz.org/index.php/topic/99834-turbo-project-no-start-help/page__p__936094__fromsearch__1#entry936094 I do have a log file, and I just noticed that the battery is only pushing 9V. That could be a problem! To see my log file, visit the Megasquirt link above.
-
I'd very much like to hear from our resident experts. After several months of building this engine: http://forums.hybridz.org/index.php/topic/95992-another-s30-turbo-project/page__p__902552__fromsearch__1#entry902552 , I can't get it to start! Here's my basic setup: Rebuilt L28ET, stock bottom end 440cc Supra Turbo low-impedance injectors on custom fuel rail Walbro GSL392 fuel pump Megasquirt II V3.0 with DIYAutotune relay board EDIS-6 with Ford coil pack and 36-1 trigger wheel using a Ford VR sensor Wiring: Tapped ignition Run/Crank wire (black w/white, used to go to ignition coil) to feed a terminal block that distributes switched 12V power to the alternator exciter wire, Megasquirt switched 12V input, and EDIS/coil pack 12V switched inputs. Not currently using capacitors anywhere on the system. Starter: Good. Engine is rotating. Fuel system: Walbro is wired to a 30amp automotive relay, triggered by the Megasquirt relay board's "Fuel Pump" terminal. Pump primes just fine when I turn ignition to "run" position. Aeromotive fuel pressure regulator gauge shows ~55psi on the rail with engine cranking. Ignition system: Pulled plugs and laid on valve cover. All six plugs fired like a Pink Floyd light show. So the coil pack is sending spark. Timing: Haven't tried a timing light yet, but I installed the timing chain with the damper pointer squarely on the "0" degree marker, and the bright link in the chain on the cam sprocket tooth with the punch mark. I installed Derek's toothed wheel in what I believe to be the correct orientation, as it has two drilled holes that line up with the damper removal holes on the crank damper. ECU: Loaded Megasquirt with cygnusx1's latest .MSQ, and all values look okay to me. Plugged into my laptop, and here's what the gauges/sensors show: RPM: Fluctuates between 100-200RPM when attempting crank. Seems to me that the VR sensor is reading okay. IAT & CLT: Showing ambient temperatures MAP: Shows 97kPa, even when attempting to crank. Should I be seeing this drop toward vacuum when cranking? TPS: Was working until about an hour ago, now it's showing me nothing. Will double check my wires. Pulsewidth & duty cycle: Both show zero...?? I expect to be smelling hog-rich fuel vapors as I attempt to crank this thing, but I'm smelling very little fuel. I suspect that there's a problem with the fuel injection, but I can't determine any obvious causes. Even if the ignition system is off-the-wall wrong, shouldn't I be surrounded by a cloud of raw gas fumes by now? I have attached a log file to this post. PLEASE help a fellow enthusiast get his beloved project running! It's hard to justify this sort of project with my dear wife when I have nothing to show for it (yet)...
-
Still not running. Update: The buzzing was the Idle Air Control relay, which I had inadvertently activated when I turned on one of the Idle Control features in Megasquirt. I pulled the relay to stop the buzzing, and I'll poke around the settings later tonight and figure out what to turn off. But what's going on here? I have spark, the fuel rail shows about 55psi of fuel, and all my settings look okay. Megasquirt is definitely powering on, and I'm reading solid coolant/inlet air/manifold pressure readings. I did notice that the manifold pressure stays steady even when the engine is trying to crank - should it be dropping towards vacuum? I'm pretty sure that my timing is solid too. I installed the timing chain when the crank damper was pointed at 0 degrees, and I hung the bright link in the timing chain on the marked tooth on the camshaft sprocket. I'd love to verify that my injectors are firing correctly. Is there perhaps a test mode in Megasquirt? Or maybe I need to set some priming/cranking pulse setting? I may have to repost this in the Megasquirt forum.
-
Checked my injectors, and they all read the correct resistance. But now I'm noticing a loud buzzing from my Megasquirt relay board when I switch the key to the "run" position.
-
I have cygnusx1's tune, and all the numbers look fine - so I don't think it's my settings anymore. I still think I'm missing *fuel*. At cranking pulsewidths, I would expect to have a much richer fuel smell coming from the car. It may be an injector problem - either I'm not getting enough current at the injectors, or they're not opening correctly.
-
Still not running... Updates: -Installed 7.5 amp injector fuses. They're not blowing now, so that's good news. -Pulled a plug and saw that it was moist with fuel, but not soaking wet like I expected it to be. -Laid all six plugs on the valve cover and saw sparks from all six So I have fuel and spark, but I suspect that I'm not getting as much fuel as I should. The fuel pump is running and my FPR gauge shows about 30psi in the rail, so it's got to be in the Megasquirt cranking settings... right? I'll post MegaTune settings later tonight. In the meantime, love to hear thoughts!
-
I'll replace my fuses tonight, check my settings, and post an update.
-
WOW. That was a long, long, marathon car wiring session. About 20 straight hours of measuring, cutting soldering, bolting, heat shrinking, cable routing, and so on. My engine bay is a mess right now as I haven't cleaned up the wires, but that is way down low on my list of priorities right now. So here's what I did: 1. Finished connecting stock harness to lights, alternator, etc. 2. Mounted and wired Megasquirt and EDIS ignition module, plugged in necessary sensors. 3. Connected Speedhut sensors to their respective wires and routed into the engine bay. 4. Wired up my junction box with 12V "hot" connections to headlight and fuel pump relays, and 12V "switched" connections (tapped the old black/white wire from now-gone ignition coil) to alternator exciter wire, Megasquirt switched input, EDIS switched power to coil pack and ignition module, and... something else... I'm blanking. Man I need some sleep! 5. Ran a #12 power wire to the Walbro pump, and rigged up my fuel pump relay. That was a lot simpler than I thought it would be. Turns out relays are actually rather straightforward. 7. Semi-installed the dash (enough to hold it in place, but easy to remove if necessary). 8. Re-re-rerouted my intercooler plumbing. The air filter is now directly on top of the A/C compressor and fits quite nicely. I'll keep an eye on air temps and make sure that it doesn't get too warm, but for now I'm optimistic. The interior is still a frightening mess of wires, but I made a great deal of progress. More to the point, I actually got to put the key in the ignition!!! After checking for loose wires and obstructions, I hopped into the driver's seat and turned the key to the accessory position. Nothing happened and I started to worry, until I realized that I didn't have anything on that would've drawn accessory power. I checked my parking and brake lights, and both worked. So far so good. Before turning over the engine, I made sure to flip the fuel pump kill switch to the "Off" position. Why? I wanted to give the engine a chance to circulate oil before igniting. So I turned it over for 5-7 seconds. The good news was that the starter worked and my laptop - connected to Megasquirt - showed an RPM reading. My sensors were working, electricity was in the system, and the engine was rotating. So far so good! I then flipped on the fuel pump and heard Walbro say "vrrrmmmmmm!" Sounded a bit like an electric antenna extending. Jumped out and looked at the Aeromotive fuel pressure regulator, which showed ~30 psi. But also smelled a strong fuel smell and realized that the gauge port on my fuel rail was a bit loose. Whoops. Tightened that down and hopped back in the car, confident that Megasquirt was ready to bring my engine to life and that fuel was in the rail (and staying there now). So I turned the key again and, despite about 20 seconds of attempting, failed to get the engine to light. I sent my wife to the exhaust pipe to smell for fuel, and she reported nothing. I hopped out and confirmed that there wasn't even a hint of a fuel smell! I knew my wires were good, so I checked the fuses on the Megasquirt relay board. Both 5 amp fuses were blown. I recall reading that 7.5 amp fuses were better for anything larger than a 4-cylinder, but I'm thinking that my 440cc injectors might need something even larger. Anyone have inputs on fuse sizing for the Supra MKIII turbo injectors on a Megasquirt setup? 7.5 or 10 amps? Or even larger?
-
Wiring up Megasquirt relay board now. I'm about to mount my homemade junction box , land the wires on the terminals, and plug in sensors. Will have an update in a few hours!
-
Hopefully I'll have a fully functional car that you can check out in person. Tim (another HybridZ user) was gracious enough to let me comb over his setup, and I'd be happy to pass on the favor to another Z-car fan.
-
I picked up some #12 wire and a 30-amp automotive relay so I can rewire my new fuel pump. I hope to do that tomorrow. I got the modified "first layer" stock wiring harness laid in place in the engine bay. This harness is for the headlights, turn signals, backup light switch at transmission, side markers, horns, A/C, washer/wiper motors, starter, alternator, and the fuse block feeds to the interior wiring. Most of the wires are routed and connected, so I should have this finished tonight. I plan on mounting Megasquirt and wiring the sensors tomorrow, then on to the Speedhut gauge wiring. Once that's all done, I'll put the dash back in and attempt to fire her up!
-
I forgot to mention that I got my same-side bar/plate intercooler and 2.5" piping from CXRacing's eBay store. I was a little disappointed that these guys refused to combine shipping on the intercooler and piping kit (to save me a few dollars), even though they DID combine shipping when they actually shipped the intercooler and piping together. Still, it's one of the cheapest new setups around, so I guess I can't complain. As long as the thing works... Quick comment on another wiring issue regarding my fuel pump setup: I'm using a Walbro GSL392 fuel pump (the 255 liters per hour model that everyone seems to like). I'm also using Megasquirt II, v3.0, with the Megasquirt relay board. The relay board has a fuel pump relay and 10amp fuse onboard, and a fuel pump wire, but the fuel pump wire itself is only a #18 AWG wire. According to my research, the Walbro fuel pump draws up to 20 amps of current, which is WAY too much for a tiny #18 wire. It seems that the relay board setup is okay for a smaller stock-ish fuel pump setup, but the wire and fuse are woefully undersized for a high flow model like the Walbro, let alone a Bosch 044 or dual pumps! In addition, I couldn't get a large enough wire to fit inside the tiny relay board screw terminal if I wanted to. So what's the solution? Another relay! My plan is to use the Megasquirt relay board fuel pump wire as a trigger to run another relay. I'll use #12 AWG wire for the Walbro's power and ground circuits, with the ground wire terminating on a piece of clean chassis metal near to the pump. The power wire will be routed up to the passenger side kick panel, where it will connect to a 30 amp automotive relay. The "trigger" terminal of the relay will connect to the Megasquirt relay board fuel pump circuit. The "source" terminal of the relay will be routed to my 12V "hot" terminal block in my junction box, with a 25 amp fuse inline between the terminal block and the relay. I recommend sizing a fuse at 125% of the planned maximum load on the circuit, and I recommend sizing a relay at no less than 150% of the maximum load. So for a 20 amp fuel pump, I need a 25 amp fuse and a 30 amp relay. I used the following chart to properly size the power wire to the fuel pump: http://www.tessco.com/yts/industry/products/itm/automotive/get_wired.html If you've looked at the Walbro flow/pressure/load chart, you might be thinking "Well I'm only going to flow ~45psi, so I only need about 7 amps." However, the motor's initial load will spike much higher than its normal operating load, as it has to overcome inertia to both rotate and to pass fuel. So plan on 20 amps! Hope all this stuff helps! I'd love to save somebody a little research time.
-
I'm continuing to work on the main engine wiring harness. It was nice to be able to remove the entire harness, inspect it for damage, cut out unused connections, and generally clean things up. I've gotten pretty good at soldering and heat shrinking! As a guy who used to only mess with the bolts and nuts, it's nice to get into the electrical side of a project. I wouldn't dare do most of this without a good wiring diagram; thankfully, the PDF version of the Factory Service Manual is available. I plan on marking up the drawing with my changes so that I can update the drawing and keep a current copy for future reference. Here's a summary of the electrical modifications so far: 1. Fusible links: Converted to a 4-circuit AGU fuse block with 50 amp fuses. The input (feeder) circuit to the fuse block is a #4 AWG wire that runs from the battery (+) terminal to the starter solenoid (+) terminal, then to the input side of the fuse block. This setup will be much more reliable and easier to troubleshoot in the case of a major electrical problem. The stock wiring used a messy spliced/branching wire setup that fed voltage through the stock fusible links. 2. Junction box: To make it easier for me to wire up things like Megasquirt, headlights, new gauges, and the new alternator, I made a simple junction box with two terminal blocks: a "Hot" block that connects directly to battery (+), and a "Switched" block that connects to a voltage source when the ignition switch is in the "Start" or "Run" position. I will feed this block from the old ignition coil (+) feed - a black/white wire that comes from connector C4 (see the FSM wiring diagram). 3. Alternator: Upgraded to a 60-amp, internally regulated alternator from a 280zx (bought a reman from Advance Auto). This link was very helpful: http://www.atlanticz.ca/zclub/techtips/alternatorswap/index.html Since I'm using Speedhut gauges, I won't be using the stock voltage charge light. There are three wires that I have to concern myself with at the alternator: the BAT feed to the fuse block (the main charging circuit), the S ("sense") circuit that will connect directly to the battery (+) terminal to provide voltage information for the internal voltage regulator, and the L circuit that "excites" the alternator field when the engine is first starting. I will wire the L circuit to my 12v switched block from #2 above. 4. Backup lights/starter control, aka "Pac Man": On the 1976 wiring, the oil pressure sensor, backup switch wires (to turn on the reverse lights), and the starter solenoid control wire all go through a big round connector that I call "Pac-Man." If you were to look at the lower left portion of the FSM wiring diagram, you would see that there is a male-to-female locator pin in the middle of the connector that looks like Pac-Man on the wiring diagram. These are the sorts of things you start to say and think after you've invested 100+ hours in a project... Anyway, on my 1976 California Z, the backup/oil pressure/starter control wires are all that's used on this clunky 8-pin connector - and I'm using a different oil pressure sensor anyway. So I decided to delete Pac-Man. 5. Headlights: The HID ballast boxes have an audible hum (albeit quiet), so I decided to mount them in th eengine bay. The most convenient spot was at the old charcoal canister mounting point. I am also mounting the headlight relays in the same place. Now I just need to clean up the wiring. I am installing the wiring in three layers: -"Stock" harness with headlight, A/C, wiper/washer motors, turn signals, and horns -"Megasquirt" harness with MS hot/switched power, MS sensors, and EDIS/coil pack wiring -"Instrument" harness with Speedhut gauges and pigtails Somewhere in here I also have to figure out how to drive my tach. I'm hoping to use the blue wire with inline resistor from the stock wiring.
-
Minor hiccip - the driver side hood hinge collides with the silicone 90 degree coupling on the intake pipe. So I'm reworking that to try and make a tighter turn. Man. I did get the Speedhut 2 1/16" gauges adapted to the stock housings. I started by opening up the stock housings and removing the gauges themselves. The clock housing's inner bezel was pretty much a perfect fit. On the stock 2-in-1 gauge housings, I used a die grinder to carefully round out the inside metal gauge face and to cut the center cross bar that divices the upper and lower stock gauge faces. I was glad to see that Datsun used metal and not plastic on the inner bezel, as it's harder to accidentally over-grind metal vs. plastic. The back half of the gauge housing needed to be drilled out just a bit so that I could bring the new gauge wiring straight out the back. So with very minor adaptation, the 2 1/16" gauges fit in nicely. The gauges do have sort of a bezel-inside-a-bezel look, so I'll try them out and see how much it bothers me. I also started replacing the heavy power wires in the main engine wiring harness. These are the white-with-red-stripe wires that provide voltage to the entire car, and they all used to run through the stock fusible links. Now they'll run through a much cleaner and more modern four-fuse AGU fuse block. I thought about using Maxi fuses, but it seems that the AGU fuses are much easier to find. Either type of fuse is fine, as long as you use the correct fuse rating.
-
Pics from my intercooler install: #1 - Driver's side metal removed for piping: #2 - Started with the compressor outlet to intercooler inlet, as these were the lowest points in the piping setup and would eventually be buried under the other pipes. So this was the "lowest" layer in the piping. I had to carefully bend the A/C hardline away from the fender to make room for the pipe to sit down nice and low. #3 - The second layer of piping consisted of the cold air intake to compressor inlet. Although the compressor inlet is physically lower than its outlet (based on the way I clocked the turbo), I knew that the 3" intake piping would have to exit the radiator support area somewhere between the intercooler inlet and outlet pipes. I also had to make a quick 45 degree upturn right out of the compressor inlet so that I could clear the A/C compressor lines. So this is the "middle" layer: #4 - The third layer of piping is the intercooler outlet to throttle body. I found it useful to tighten down the connectors on the couplings that passed through the ground-out area BEFORE trying to feed the pipes through. It was almost impossible to get a screwdriver or socket/ratchet in place to tighten down the clamps otherwise! My blowoff valve is on this section of pipe, and my inlet air temp sensor is on the other side of the BOV pipe. So this is the "upper" layer: #5 All done! Really happy with how everything came out. NOT happy with the scratches all over my brushed aluminum piping! Also not thrilled with the mixed colors on my couplings. If this offends any of you purists, feel free to come over with a set of matching couplers and fix it for me!
-
Replacement housing located nearby. Also finally got the same-side intercooler piping installed. That was a LOT tougher than I thought it would be! I ended up cutting away nearly all the metal between the driver side of the radiator support and the driver side fender support. I did all this with the stock A/C components still installed and the stock bumper in place. The A/C compressor and hardlines, and the stock '76 bumper shocks, made it rather tricky to get everything to fit. But it's done!! 90 degree intercooler fittings really helped me make the turn into the same-side intercooler. Forgot to mention that I used 2.5" intercooler piping, with a 3" feed to the compressor inlet. Pics tomorrow. Also hope to eventually update the wiring diagram PDF that I linked to elsewhere, with my changes marked up. I'd hate to have to try and troubleshoot this thing later without having my new wires included on the drawing!
-
Part acquired, please delete!