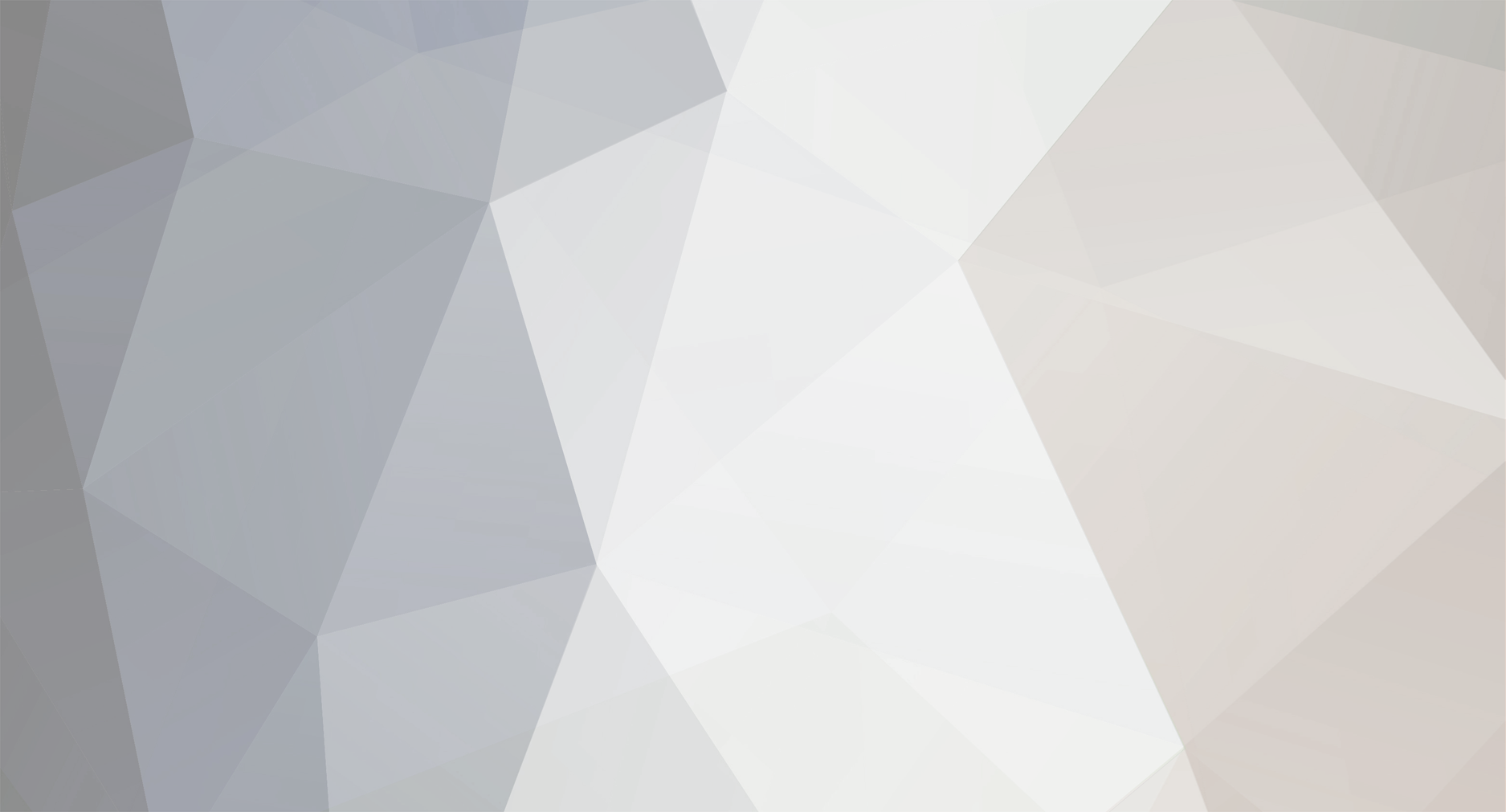
rsicard
-
Posts
889 -
Joined
-
Last visited
Content Type
Profiles
Forums
Blogs
Events
Gallery
Downloads
Store
Posts posted by rsicard
-
-
Agree with NewZed. Voltage readings are normal without the alternator running. Sounds like a fuel line blockage. Bottom of tank, one of the filters etc. Disconnect and check flow of lines to front with compressed air nozzle. Test filters for restriction.
-
If the button flywheel bolts are already torqued down, MAYBE those are the wrong diameter shank bolts for the button flywheel. The bolts must have a step down shank dimensions for mounting both the flexplate and the Button Flywheel. Best to get QuarterMaster on the phone and ask about the 13 thousands play and if you have the proper bolts for the button flywheel. Just some suggestions. Best of luck to you.
-
Went with a Speedhut 3 5/8" quad gauge. Oil Press, Water temp, Voltmeter, Fuel Level. Programmable Fuel level. Double Pole Double Throw switch for either Fuel or Oil Pressure on Pressure portion of gauge. Several temp sensors, selectable through rotary switch for display on temp portion of gauge. Also installing Speedhut 3 5/8" Speedo. Both Indicators fit within the original buckets from which the mechanical speedo and elec tach came from. Three empty center panel openings. One for Air Fuel Mixture, one for Vacuum Gauge and other for tachometer? Would like Analog LED + digital number display tach which as INSTANTANEOUS (zero lag) analog display of RPM.
-
I don't quite understand your statement. The Holley stuff (dominator) is capable of single cylinder EGT monitoring. You can then trim fuel by cylinder, since there's 1 injector (or more for the big boys) per cylinder.
I injector per cylinder is NOT throttle body injection yet is port injection. The throttle body is an air valve. Throttle body injection has the injectors AT the throttle body. Gen 5 GM small block has fuel injection directly into the cylinder, like diesel injection.
-
Throttle body EFI causes some cylinders to run rich and some to run lean. Just the nature of this level of EFI technology.
-
After market ECMs are getting more sophisticated. The basics of EFI remain the same. The latest development is the self tuning capability. This requires MORE intelligent embedded software code in the ECU to self modify the fuel injection output parameters based on inputs to the EFI. I have invested in GM PCMs and gotten to the point of TOO much money to invest to reap TOO little benefit. Finally went with Electromotive EFI ECU and have not looked back since. They appear to have the tech bedrock from which all other modern EFI systems have developed. Lots of intellectual property stealing going on among manufacturers. The cheaper self tuning system all appear to be THROTTLE body EFI, not port injected EFI, which is a technological step BACKWARDS but better than carbs.
-
Caution, ordered kit from Jegs and got ERW tubing! Purchased DOM stock and had it bent same as Jegs main hoop.
-
Priming the oil pump will NOT reveal the problem. The positive way to go about it is doing a cylinder by cylinder leak-down test. The tool to do this with has two air pressure gauges. One for line pressure and the other for cylinder holding pressure. Once a cylinder is pressurized at top dead center, for that cylinder, note the reading on the cylinder hold pressure gauge. The instruction sheet that comes with the tool has a chart of how much leakage per cylinder pressure read. Open the valve cover cap and get near it with your ear when the cylinder is pressurized. If you hear an air leak, then it is the piston rings for that cylinder. Also listen at the exhaust and carb intake for air pressure leaks. It will tell you whether there are valves leaking. There are quite a number of variables when an engine is being rebuilt. The more experienced the re-builder is, the better the outcome. Don't be afraid to disclose facts about the rebuild and there are many of them.
-
Sounds like there is too much piston ring blow-by. The more RPM, the more crankcase pressure build-up. What is the mileage on the engine? Was it from a carb or EFI induction system? EFI always runs a lot cleaner on the cylinders. Carbs tend to wash down the oil on the cylinders and accelerate piston ring wear. Sounds like at the least it needs a rering job. More likely, bore and hone the cylinders with replaced pistons and rings. This should drastically reduce piston ring blow-by.
-
Sure, geno51. I was thinking I might have to go swing out bars and a remove able steering wheel too, but it is remakeably easy to get in and out, although I may shorten my turn signal stick so I don't break it off. I'm on a diet, and that will hopefully help even more. Too much BBQ. But I'm trying to offset some of the weight I added to the car. Braille battery will help too, but I would really like to wait for the current battery to poop out first. Also, I probably don't need all the relaxing of the harness bar that I have. That would allow the diff bars to be more straight, which I would have preferred. I'm not certain that will help enough to justify the weight. You may come up with a better solution to that issue. I was planning to take car to be certified, but it turns out that isn't required until you go sub-10s. I'm still trying to play the game as close to the letter as I can so no track turns me away.
Keith:
Now that your cage is in, and very nicely done, where will the drivers harness attach points be? Please post photos of the bottom of the main hoop welded attachments. Trying to get ideas as I have received a main hoop etc. for 4 point cage and will use the same Kirkey seats. Not trying to be annoying yet "....don't need all the relaxing of the harness bar..." and "...diff bard..." just don't understand the thinking contained here. Also, what is the purpose of the down bars going to the tunnel. Just wondering.
-
jhm
Thank you very much for the information.
You will want to watch for RUST in the floor pans especially and other areas inside the vehicle. You won't need one with a Small Block Chev (SBC) as you can install one of those yourself. There are many aspects to be covered in a Datsun with a SBC, drivetrain, suspension etc.
-
Kirkey Intermediate Road Race seat arrived today. I feel like Goldilocks: the 17" seat was too loose even with the cover on. The 15" is too tight even without a cover. Sooooo, I just ordered a 16" from (Summit had them in stock, but had no covers in stock) and a cover for it (Jegs had covers but no seats). This weekend's project is to get a seat mounted on the adjustable rails. I think the 16" is gonna be the ticket. If so, I'll send the darn 15" back to Jegs. After talking to MiKelly, if the shoulder wings are too wide, it will be time to bend them in with pressure and a dead-blow hammer. It sucks to be so picky on seat fitment, but I want to be able to autocross and road race as well as hit the road for a cross-country cruise or do Drag Week. Time's a tickin'.
Keith:
What series of Kirkey seats did you receive? I have to do the VERY same as I want to road race my 240Z also. I am very interested in your installation of these seats especially the adjustable rails. Please advise. Thanks.
-
The 204-1003 requires that you cut the top of the tower up and the 1017 doesn't. I have been a big advocate for the 1017 but I am running into a snag with them: I am having to cut up the top of the strut tower anyway in order to access the adjuster screw on my new koni shocks. The adjuster on tokicos cleared stock sheet metal. Now I'm cutting anyway, so it is kind of a wash. Keep an eye on my build thread in the projects forums and when I'm finished in a couple of weeks I will post photos.
Thanks very much for the part numbers. Want to install the 204-1017 on my 240Z. What needs to be underneath the 1017 to the top of the coil spring? Right now have the original doughnut on top of the Koni Racing Shocks inside shortened struts with adjustable coilovers. Really would appreciate your experience in this subject.
-
Pulled it apart to find my pivot balls on the clutch came out of place and were just rolling around inside the pressure plate. The centerforce clutch will not be going back in and fidanza flywheel will be going up for sale. PM me if your interested has 4 miles on it.
Sounds like the pivot ball for the pressure plate disengage lever broke off. Seems all it needs is a replacement pivot ball/shaft. No need to get rid of the fidanza flywheel. The centerforce clutch should also work with the replaced pivot ball/shaft. Just need to remove the transmission from the bell-housing, then bolt it up to the block with the clutch and pressure plate installed, install the disengage arm, adjusting the pivot ball/shaft, for a very small amount of free play between the throw-out bearing and disengage arm. I will be installing this same setup with a Gen 1 engine with a 1 piece rear main bearing. Already have the external hydraulic slave cylinder from McCleod. Going to order a Quicktime 9023 scatter-shield bell-housing and check it for dimensions against the GM cast aluminum bell-housing.
-
I did something kind of like this. I don't think you want a bar across the floor on the main hoop and then go forward from there. You would be putting the loads from the front struts into the middle of this bar across the main hoop, and the bar is most flexible in the middle of the span. What I did was a V to the diagonal in the main hoop, a bar from there straight down the middle of the car, and then a V from the front struts that hits the dash bar in the same spot. Dr. Sideways did the same thing but better. Rather than have a single bar straight down the center, he has an X between the dash bar, the diagonal, the A pillar bar, and the main hoop. The problem with his solution is that it completely eliminates the possibility of having passengers, and I love giving rides.
In the book Chassis Engineering by Herb Adams he does some scale model testing with balsa wood frames and something close to what I have is used and found to be effective.
This relates to what others have been saying both in that the strut tower loads are tied together front to rear, and also the notion that the front clip is the weak part of the chassis. On my 70, when I put jackstands under the TC rod buckets and let the jack down, you could SEE the front end of the car droop about 1/2". You have to figure that the same thing is happening when you step on the brakes; essentially the car is trying to fold at the firewall.
With regards to the STBs, I don't think their main objective is to increase torsional rigidity per se, it's to tie the strut towers together. When the outside tire takes a lateral load it tries to pull the strut tower outward. When both tires hit a bump simultaneously they try to push together. Tying both strut towers together even without an attachment to the firewall should help both of these situations. I have doubts about the benefits of tying to the firewall unless the firewall is reinforced.
Jon:
Thanks VERY MUCH for your comments. It's really nice to have a discussion on this level. Agree with you totally on the STBs with the same thoughts. In reading your comment, the longitudinal tube you installed from the diagonal in the main hoop must have been elevated such that it intersected the firewall near the top of same and onto the strut towers via a "V". This is a much more DIRECT approach to increasing the "Y" axis torsional rigidity especially the front struts towers and structure. I used an indirect method by having the tube just above the floor hump then extending upward the inside of the firewall with steel and then downward and outward on the front of the firewall to the framerails.
I have also purchased the Chassis Engineering book by Herb Adams and read it thoroughly. I want to keep the original Datsun 240Z dash. That is why I may place the longitudinal tube just above the hump. Also want to beef up the forward frame rails by adding rectangular tube to the bottom of the existing frame rails forward of the front towers and far enough to the rear to gain rigidity in the "X" axis of the vehicle.
-
Did that in the front but not in the rear using a jig but not the suspension itself. Wanted to eliminate the bushings from the test. The jig bolts to the strut tower top and the inner pivot of the lower front arm (front crossmember in place). Most of the load it going to the strut tower top.
Chris:
Have given a great amount of thought about torsional stiffness to my 240Z. After mounting a good Roll Cage to the rear of the vehicle, use that portion to transfer torsional stiffness to the front of the vehicle. Weld in a thick wall round tube laterally above the floor hump between the main hoop uprights. Then add another thick wall round tube between the seats from the lateral hump tube forward to a thick plate on the rear of the firewall that extends upward. Then add another such thick plate on the forward side of the firewall in the same position as the one on the rear of the firewall. Then weld a thick wall short round tube to the top of the plate on the forward side of the firewall. Then fab some substantial rectangular tube angling down to the integral frame rails. Weld these rectangular tubes to the short tube and to the frame rails. This would transfer some of the rear torsional stiffness to the front end. Also fab and add rectangular tube to the bottom of the frame rail from about the firewall forward to where the front suspension is located to increase the vertical depth of the frame rail in that area.
-
Thanks heavy. Good to know that I'm not the only one seeing this. I was thinking of milling about .002 off the spacer and trying that to preload the bearings as right now I don't think I am at all. Do you remember what thickness spacers you were playing with? I just want to make sure I'm in the right ballpark.
Not certain why there is ANY pre-load needed on Ball Bearings. If there is, then that would induce excessive wear and heat on both inner and outer races of both bearings. If there is axial play of the stub axle, then add shims to one end of the inner spacer until the axial play is 0 to .001" such that there is still NO axial pre-load on either bearing. The FSM says 0 to .0059" axial play which in other words says NO pre-load countering their pre-load specs on the same image.
-
The trick to not twisting the chassis is to tack weld the rear sections in first (both sides) while shooting a last down the chassis to make sure they point toward the center of the front rail structure at the TC rod mount. Then tack weld the front sections in place (both sides) again using the laser for alignment. Then weld the front and rear sections together. Now you can do the full stich/seam welding of the frame rails to the car, alternating sides of the car, front to back, and inner/outer edges of the rails for each weld. If you get the rails welded together straight while tacked to the car, the stich/seam welding will not affect the chassis alignment if you alternate where you weld. The won't overpower the rocker panels, closed doors, or the roof structure.
John:
More to the story. It appears my 240Z was in an accident where the right front was damaged. It now appears to lean to the right a small amount. Is there a way to correct for this?
-
The trick to not twisting the chassis is to tack weld the rear sections in first (both sides) while shooting a last down the chassis to make sure they point toward the center of the front rail structure at the TC rod mount. Then tack weld the front sections in place (both sides) again using the laser for alignment. Then weld the front and rear sections together. Now you can do the full stich/seam welding of the frame rails to the car, alternating sides of the car, front to back, and inner/outer edges of the rails for each weld. If you get the rails welded together straight while tacked to the car, the stich/seam welding will not affect the chassis alignment if you alternate where you weld. The won't overpower the rocker panels, closed doors, or the roof structure.
John:
What is the method to use to check for any chassis twisting knowing the amount of experience you have with these cars?
-
Good luck with that. I would absolutely not do that. If my floors were thinned to the point I couldn't weld to them, I would have to replace the floor pans or get a new chassis all together. Screwing bad dogs to rusty pans, probably wont hurt anything, but it wont help either. Basically they would just be down there hanging on for the ride. Its a unibody, all the panels contribute to strength, if the floor is compromised the chassis is compromised. Sorry to be the bad guy and a big jerk, but that is just bad advice.
I did not say the floor pans were RUSTY. They are NOT. The 240Z is the lightest in weight of the Zs. The Bad Dogs will keep the floor pans from oil canning and the floors are stronger. I know it is a UNIBODY. The floors are NOT a significant structural components of the chassis. It is not bad advice. It is good advice
-
Thanks guys and gals for all the input. Most of the body-shop that i stopped by have extreme well reputation and work with all new and modern cars. Some of them are friends and they asked why I spend money on this piece of ****. Anyway, they said it is not just welding the frame rail in but it is more involve with the car body structure and alignment and such. They didn't want to wrist the body ( I'm really don't really know what they was talking about), so they would align it and then weld the frame.
I still don't know how far will I go with this car-project. I don't know if I will put it to 500HP or just keep it stock but I know the frame rail is critical part and redo it will not a funny or easy job.
So, 800 bucks seem reasonable to most of guys here, I will save up and do it after the Black Friday if still have any money left. I will keep you update and will take some pictures of the process.
Get some Clecos, 10-32 screws and self locking nut and fender washers. Drill every six inches along either side of the new frame rails and bolt them together with the floor. My 240Z has floor metal SO THIN it just made sense to do it this way. Lot cheaper than welding.
-
OK. The basic 4-piston AZC kit is completely installed and bled. Why do all aftermarket brake kits position the caliper so that you have to remove it to bleed it? What a PITA. While I was at it I flushed the clutch hydraulics too. Let the clutch reservoir run dry (heard the dreaded sucking sound and thought: "Oh snap!" Spent the next 3 hours getting air out of the clutch system only to learn that the thing making bleeding so difficult was, once again, insufficient pedal stroke. I gotta ponie up and remove the clutch pedal and weld up the oval hole. Readjusted pedal stops and it bled no problem. Got the 9" slicks mounted on the 8" drag wheels after doing the mods needed for bead lock screws and tubes. One wheel took 8oz of wheel weights to balance-dang used ebay wheels! Looking for a second set of drag wheels for some 28X10.5s. Ordered parts to finish up the hydraulic handbrake and put new studs in the spacer. Also ordered fender welting from Speedway for the BAMF flares. Gonna straighten up some things in the tranny tunnel tomorrow and start planning to tackle the Konis. Perhaps I can make that 10X more complicated than it should be? What I do best.
Keith:
What is the part number of the spanner wrench from McMaster that JohnC recommended. Also have Koni Racing Shocks and need tool.
-
Pan came in. Looks good but the paint job sucks. Says it should have a 5 qt capacity, plus the remote filter, plus the 3 qt accusump I'll be running. I think I'll be OK.
Very Nice 4 trap doors. Curious to know with the trap doors, if the accusump will be activated in hard corners. If you can remember, please let us know. I have a SBC oil pan with kick-outs and trap doors and want to know if an oil accumulator will be needed for hard cornering in road racing.
-
hey everyone i currently have a 700r4 on my z and wanted to change it to a T-56 6 speed tranny.....the block that i got is a later model to be exact its a 77 350 block..so i was wondering will the T-56 bolt right up or would i have to fabricate it in? ive also read that you have to buy a different fly wheel for the T-56 tranny so that it would work? well let me know what you guys know thanks a bunch.
Z fever///
You can purchase a Fidanza 198541 aluminum flywheel from Jegs for $369.99 and may need balance plate Fidanza 624001 for $19.99 from Jegs also, if the engine is externally balanced. Look at the rear of the flexplate to see if there is a counterweight attached to it. If so then you will likely need the balance plate. These are low prices. Also purchase a ball or roller bearing to be pressed into the rear of the crankshaft to accommodate the pilot shaft of the T56 or manual transmission. The T-56 LT-1 bell housing is an aluminum casting and will bolt up to your engine. Or if you want to be safer, purchase a Quicktime scatter shield bellhousing part number 9023 such that if the clutch or flywheel explodes and leaves the crankshaft, it won,t saw off your feet and will be contained by the Quicktime STEEL scattershield / bellhousing.
Dual 7.25 clutch install issues
in Gen III & IV Chevy V8Z Tech Board
Posted
That speaks VOLUMES about the quality of the supplier. Fit checks should be done in the prototype stage of development.