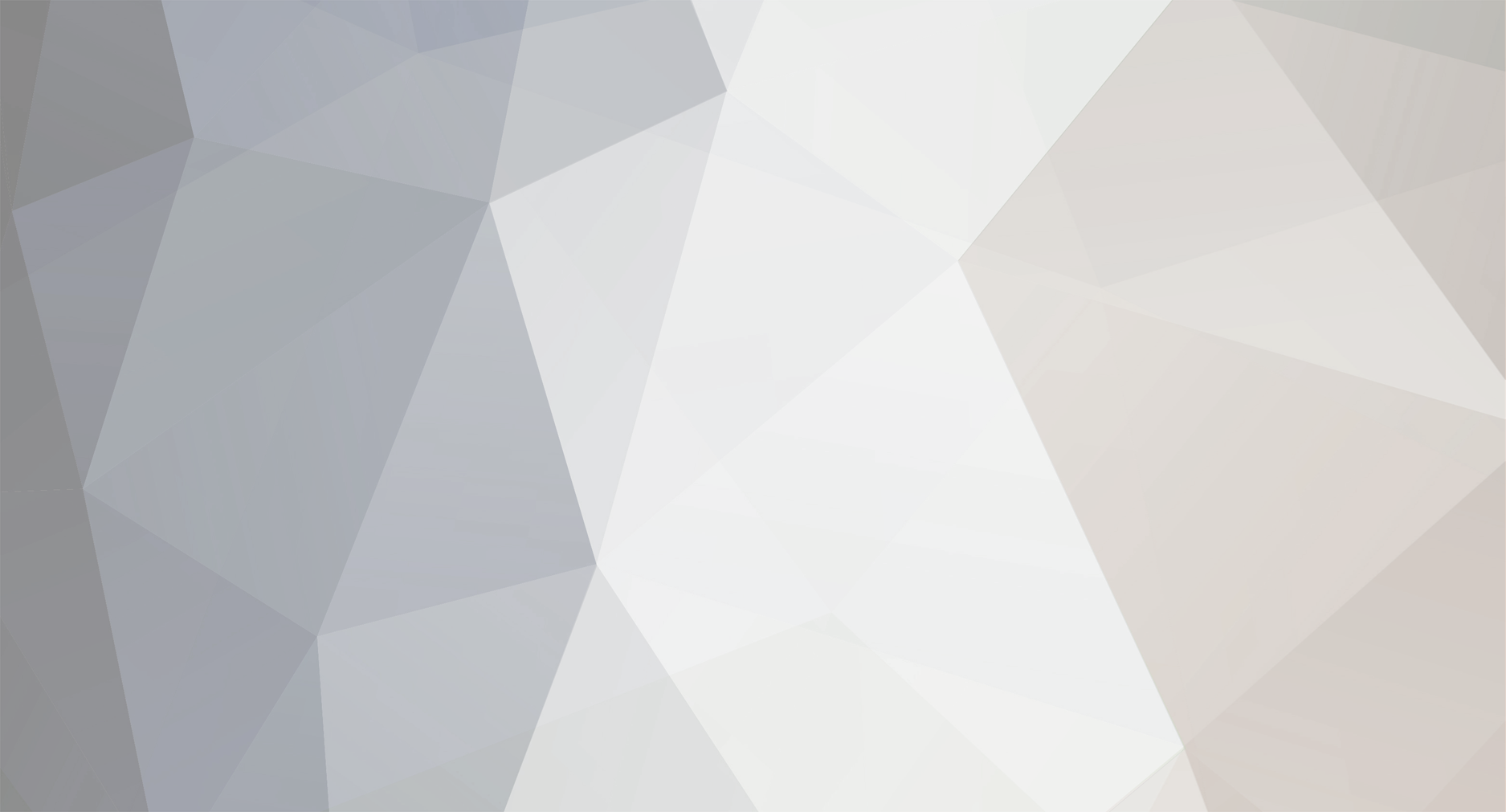
rsicard
-
Posts
889 -
Joined
-
Last visited
Content Type
Profiles
Forums
Blogs
Events
Gallery
Downloads
Store
Posts posted by rsicard
-
-
I have also built a 383 stroker with AFR-195 heads and solid roller camshaft. What is the chamber volume of your AFR-195 heads?
-
If measuring a lower pressure area against a higher pressure area or vice versa, this type of measurement is MEANINGLESS. The meaningful way is to measure the two different pressure areas is each with respect to a reference/ambient/static area.
-
If I'm not mistaken (And I may very well be!), I think as long as he uses the cabin as the low-pressure side again while testing the engine bay side of the fenderwell and drives at the same speed that he measured the tire side at, hell get a useable set of numbers to compare
The cabin, with closed windows, would be the least influenced by ram air pressure at speed. Therefore, it can be used as a REFERENCE. One side of the manometer should be vented to the REFERENCE and the other side to the point to be measured whether is be negative or positive pressure with respect to the REFERENCE. That way you can tell which are higher and lower pressure areas.
-
It sure is nice to reuse the original gauge housing to mount the new gauges. Have done that with Speedo and Tach. Then on to the center three.
-
I also used the Speedhut speedo. Ordered the 3 3/8 inch and machined a round plate with a round hole in the middle to mount the speedo. The outside of the plate is machined to just fit within the back half of the original speedo. Then tack welded the machined plate to the back half housing just behind of the four dimples of the original housing. This places the speedhut gauge bezel where the original was at an optimal depth reusing the original plastic bezel that mates with the original metal housing. The tach is triggered by ignition breaker points, 0 volts closed or 12 volts open or equivalent by solid state electronics.
-
Risicard, The gauge I have is designed for measuring differential pressure or absolute vs. a fixed reference, and I wanted to know the DIFFERENTIAL pressure, not the absolute. It also only swings positive, it's not a center-zero gauge.
I have made myself an absolute map over the hood on 4" grid squares, but for hood vents that's not the data I want...I want to know at what point on the hood is the DIFFERENCE between the top side and bottom side of the hood the greatest.
When I was measuring in the open area at the front of the car, I was graphing absolute pressures, measuring in the wheel wells, measuring over the hatch area, I wanted to know the pressure relative to the cabin.
For vents or for enhancing airflow through the coolers, I want differential pressure, so I can work out what produces the greatest flow potential.
One port of the manometer, be it electrical or mechanical, MUST be a (static) absolute pressure REFERENCE!!! The other port should measure a positive differential from the reference. This is the ONLY meaningful way to measure relative wind over the car or sources of differential pressures. With the curvature over the hood, it should provide a negative or lesser pressure than the reference as in an airplane wing effect wherein the top of the wing generates LOWER pressure with respect to ambient (static) absolute pressure. I have been doing this part of science for 38+ years. In other words, I know what the HELL I am talking about!
-
I'm working away from home once again so this is just a thought, I can't take a look to see if it will work, but what if I mounted the ECU horizontally inside the cab on the passengers side with the pin connector going through a slot cut in the firewall? That way the ECU is tucked away out of sight but the connectors are accesable without doing a bunch of bulkhead connections. I would want to seal the ECU to the firewall somehow.
If your 280Z headlight circuit, on/off and high/low beam, is like my 240Z, then headlight relays need to be added. The LS PCM will control engine cooling fan(s) and output a tach signal. To keep thing simple mount the PCM immediately behind the radiator core support either LH or RH side which ever works out best for the harness. Then address an oil pressure, coolant temp, electrical system voltage, fuel tank level and transmission speed sensor/gauge(s).
-
I purchased a Dwyer Magnahelic gauge to measure differential pressure over the hood, and found that the highest difference was right about the middle of the S30 hood. This is measuring both top and bottom of the hood at the same time, on a differential measuring tool.
About a 10" long section, from the side of the hood bulge out toward the outer frame of the hood, starting at the front corners of the bulge and coming back. This is where I measured the highest differential pressure, of 4.8 inches WC at 80MPH...too chicken to go faster on a public road.
Fun part...the gauge showed low pressure on this spot of the hood from about 15MPH up!
The way to test is have the ambient port of the gauge inside the cabin and the higher pressure port on top or bottom of hood at the same point for the conclusions to make ANY sense. Have 38+ years in Aviation testing pitot/static systems. Am VERY familiar with Water and Mercury Manometers and aircraft instruments and Digital Air Data Systems. Should rerun the tests with precision to get good results.
I would like to have a data acquisition system with 16 Analog to Digital ports and map 16 airspeed sensors in several different spots on the car. This is what should be done in the Wind Tunnel. The results could then be recorded and graphed appropriately. This would lead to a lot of knowledge about the aerodynamics of the 240/260/280Z cars. Do it both for laminar flow and non-laminar flow.
-
I've been doing some research on getting the wiring harness for my 280 and LS to work correctly, hopefully the first time.
I'm not deep enough into it to have any specific questions but I've stared at the diagrams enough to cross my eyes and started stripping the chassis harness of the stuff I know won't be needed.
I imagine once I really get started and break the whole system down to manageable pieces it will be a lot less intimidating.
I just wanted to know if there are any things you guys are glad you did or wish you would have done the first time around - fuse boxes, relays, routing, etc.
The PCM should control a relay that controls feed of voltage to the fuel pump. For safety sake, a crash switch to cut off the electric fuel pump. Relays for headlights. Relay(s) for engine cooling fan. Relay for A/C compressor. Clean and repair turn signal, bright/dim and headlight switches on the stalks. Send LS harness to Rebekahsz Lan Culvert for modification and labeling of applicable wires.
-
I think the truck setup will be too tall to allow the hood to close. The camaro setup is what I believe that I have and fits underneath the hood closed.
-
Thanks for conferming that they will fit. Now to try to find some brackets that are not over priced.
Go to Ebay item 221253789591. The price is RIGHT. $75.
-
Don't have to worry about coming in contact with the strut tower. Have the factory brackets you describe and the question was do they fit under the hood. Answer, yes they do.
-
If the air behind the radiator was stalled, then likely there is not enough of a rear vent for the under-hood air.
Jon: I have gone over the circletrack magazine article and have captured same. The closer the splitter is to the ground, the lesser amount ram air will go under the air-dam/splitter. That means less positive pressure underneath the vehicle therefore the lesser amount of upward pressure or lift. There needs to be a way to evacuate the air coming through the radiator and around the engine.
-
Am uncertain what the airflow under the hood is in front of the struts is. More certain about air flow at the rear of the engine compartment either out through the ventilated inspection covers and/or boring a large hole through the inner fender panel underneath the inspection cover. Also have given thought to mounting an electric squirrel cage blower inside the wheel well with the intake affixed to the large hole beneath the inspection panel. Then run an exhaust tube from the blower downward and rearward. Or, a stovepipe from the large hole on the inner fender to vents on the outer fender.
-
It must be the intake manifold that is TALL. I have a Holley port injection manifold. The only way the tall spectre carb hot fits under my hood is if it is pointed to the 4:00 position. At this position its is very close but still fits under the hood. Had to fab brackets for the Electromotive TEC3 ignition coils around the throttle body. Two in front and two in rear of TB.
-
Jon:
Thanks for your comments. I screwed up thinking the upward air dam at the leading edge of the hood would work. You are correct about the effect of same. Don't know that I have the real estate for radiator exhaust ducts out the hood. Please expand on the NASCAR exhausting under-hood air out the front fenders. Is the space behind the front spinning tires a low pressure area? Don't know what Tony D stove pipe thing is. What was he exhausting where? If large round holes are cut into the side pockets below the inspection panels into the wheel-house area, is that an area of low pressure and would that exhaust the under-hood hot and higher pressure air? Does putting an air dam with splitter at the bottom within 2 inches of the road surface create DOWN force?
Really appreciate your thoughts and comments. You keep me on the straight and narrow.
-
Jon:
What would be a way to rid the hood of its lift potential? I proposed putting just enough of an upward angled air dam to the leading edge of the hood, to cancel the Bernoulli effect of the hood. Perhaps this would create a low pressure area behind such an air dam to create down force and it also would create DRAG. The way to reduce under-hood pressure is to restrict the amount of fresh air entering through a tunnel to the radiator. Then exhaust the under-hood hot air out through vented hinged inspection covers. Have also thought about putting electrical squirrel cage blower just beneath the vented inspection covers to SUCK the hot air out from underneath the hood.
Your comments please. Thanks.
-
Mike:
I apologize if I have offended you. I thought this was where we share ideas. I try to keep emotions out of the discussions. I used JTR kit for mounting the SBC Stroker 383. Used the JTR fabbed transmission mount for the rear of a T56 transmission. That transmission has proven to be the EXPENSIVE way to go. Never envisioned this project costing so much but it is my hobby and I really like it as such.
-
peej401: Agree area is not the only aspect. Shape also has a lot to do with airflow. With the Spectre 4 inch 90 degree elbow/hat the air into the throttle body has to turn 90 degrees. This is likely the worst restriction in the intake air system. The other is the throttle body. Another is that after the throttle body the air in the intake manifold has to make another 90 degree turn to get to the intake ports. Have also considered going to a 102mm LSx throttle body. No matter, the air flow still has to take a 90 degree turn to get into the throttle body. Have also considered Edelbrock tunnel ram single log at top of same from smaller area LSx throttle body. STILL there need to be at least TWO 90 degree turns in the intake air system.
Question for YOU, which datalogging system are you using that shows up in the photo in your post? I think it is the AEM data acquisition system. How do you like the data acquisition system? Comments please. Thanks
-
Mike, that last opinion is TOTALLY illogical. It's a freaking IC engine. If its built correctly and it's installed with the correct subsystems, it will undoubtably "mix" with the car just fine. Again - a different design (LS vs SBC) will gain you nothing but less money in your pocket and an increased amount of time until you are back trouble shooting the subsystems that are giving you problems now. A different engine with the same subsystems (i.e., breather setup) might have the same exact problems.
Sorry to be a hard ass but you're making an emotional judgement about the engine and the car. Just because you have a pile of LS parts sitting there ready for much time and money to be spent on them doesn't mean that you SBC, if built correctly and having the correct subsystems connected to it won't do the job wonderfully with a minimum of time and money invested.
I second what pparaska has said. Could not say it any better.
-
Get rid of all the lift force on the hood by putting a spoiler extending upward from the leading edge of same. Then modify the flip up inspection panels, put Gurney flaps in front of them, so they can vent out pressure under the hood. This goes along with reducing the grille opening and ducting the smaller opening to the radiator.
-
Miles has the right idea. The front grille opening should be reduced to reduce the amount of positive air pressure going through the radiator. Secondly, the airfoil shape of the hood creates a lift on the hood. The two forces aid each other pushing up on the latched hood. Part of the goal should be putting a spoiler extending above the leading edge of the hood and testing different widths and angles of such a spoiler with tufts taped behind it along the length and breadth on the hood to make certain all the tufts are lifted from the hood surface negating the hood as a lifting body. Then the downward air dam and splitter can provide the necessary down force at speed.
-
The better the quality of the engine, the greater it will cost. First clean the block, check it and the crank for defects. With 180cc intake 64 cc combustion chamber cylinder heads, this has become the limiting factor. Strongly suggest decking the block such that the pistons are level to .005 inch in the hole. With the careful choice of pistons, try your best to get the maximum amount of squish out of the pistons and cylinder heads. With a cast crank there will be stretch in the rotating/recip assembly. Strongly suggest using longer Scat "I" beam con rods, shorter dished (lighter weight) SRP Professional Pistons then internally balance the crank with neutral balance damper and flywheel.
-
It is really hard to comprehend why practical solutions are IGNORED. I managed to fit the 4 inch spectre elbow/hat (NOT the low profile unit) under the hood and was able to close same. The area of the 4 inch elbow is greater, for air flow, than the throttle plates in the Accufab throttle body.
thinking of doing swap
in Gen I & II Chevy V8 Tech Board
Posted
Go to a 350 V8. Don't buy someone 350 v8 problems. Go to Summit Racing and purchase an already preped bare 383 stroker block for the same cost as 350 block. Then purchase 3.75 stroke crankshaft, 6 inch rods and Pistons. Then invest in GOOD cylinder heads from AirFlowResearch. Best advise that can be given to have REAL GOOD Engine!