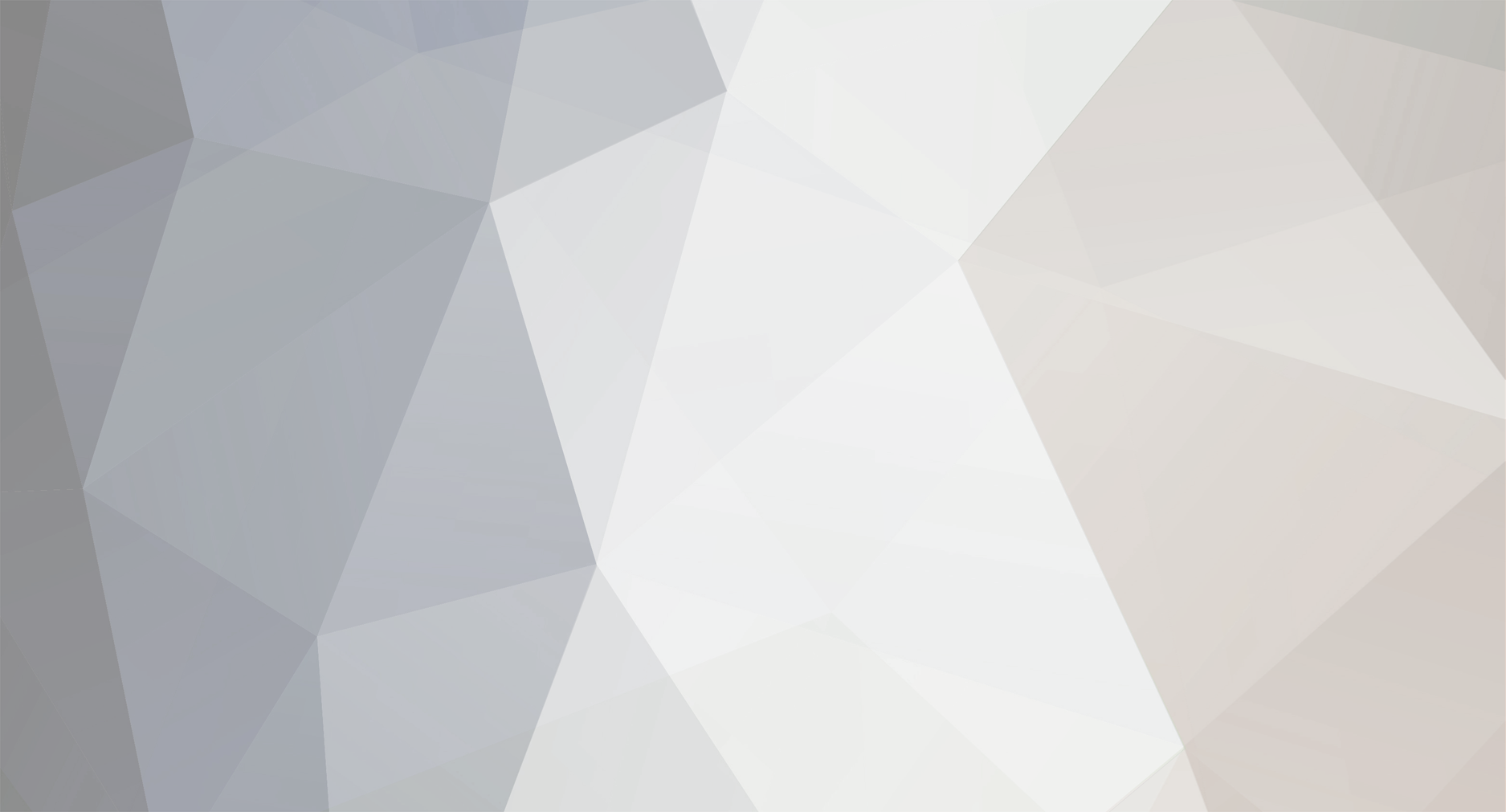
WHP
Members-
Posts
93 -
Joined
-
Last visited
Content Type
Profiles
Forums
Blogs
Events
Gallery
Downloads
Store
Everything posted by WHP
-
Before you go tearing everthing out as mentioned above check the hoses and valve. Get the motor real hot, turn on the heater and stand on your head with a good light and inspect carefully. That little 4" elbow hose is often the culprit. Mine took a dum on my wifes feet. Lucky she was not burned. Check the heater hoses too. It has been about 2 yrs ago but I got valves from the Nissan dealer.
-
I have not bought it yet but I am going to soon purchase one of these. Anybody using one of these? http://www.southernrods.com/search.php
-
Frame Rail Repair, What Have I gotten Myself into.
WHP replied to zgn's topic in Brakes, Wheels, Suspension and Chassis
I capped my frame rails on my early 74 with the Baddog full length rails this week. It took two of us 6 hours to fully install them. My car had rust free rails and and the floor pans were solid too. I was adding the rail caps for extra strength for my Ford 302 conversion. To access the rails we attached a chain to the seat cross member and used a motor lift to tilt the car about 45*. The car is only a rolling shell. We bolted the rails in place to pull them up tight to the car, then welded the upper side of both rails, then flipped the car to the other side and welded on the upper sides. -
Well I sent an email to AFR bashing them for building heads that no exhaust fits and they admitted they blend the step just like I was planning to do. So plan well guys. I spent hours researching heads, but I don't remember anyone mentioning this problem.
-
I basically will have to make a .1" transition in the thickness of the flange. I contacted AFR and was very disappointed in their answer. Basically they made a large port with no provisions to connect properly to any off the shelf exhaust system. I would think a smaller port but smooth connection to header would outflow bigger connecting to smaller= turbulence? Here is their reply: Hey Will, You are not going to find any headers off the shelf that will completely clear the port. The problem is the stock 2" bolt pattern, then factor tube thickness, weld thickness, then room to actually remove and install the bolts. Just doesn't leave manufacturer's much to work with. Feel free to contact me again by phone or by e-mail with any further questions. Thank you for choosing AFR, Jason Dow AFR Tech./Sales Dept. (661) 257-8124 Ext. 124 Am I too much of a perfectionist or is this mismatch an expensive mistake on my part?
-
Nice. What kind of headers are those that fit with no steering rod mods?
-
Great post! Rarely do we get real apples to apples comparisons. At work we used to say- In God we trust, all others bring accurate data.
-
What I was trying to describe, is weld the tubing to the outside of the flange and remove it from inside the flange only. I was not looking to thin the tubing. It seems all too common for header mfgers to cut the flange to match the port then stuff the tubing inside that. Well that was a MSA header I once threw away was.
-
I am putting a 302 in an early 260Z. I bought the Summit blockhugger headers because they look like the best fit in the engine bay. But they do not match the larger exhaust ports of my AFR 165 heads. The flange is the correct size, but by the time the pipes are inserted and welded they are .1" undersize all the way around the port. Would it be possibe to weld around the outside flange and grind out the tubing from inside? Any suggestions? Thanks! Will Piatt
-
MY MSA headers matched up so poorly to my exhaust ports I trashed them and ported a P79 manifold and hooked it up to an oversize twin downtube. Heavy, but cheap, no leaks, and pulls good to 8K.
-
not a V and not an 8 but I want one in my Z!! 2.4L = 34 lbs http://peswiki.com/index.php/Directory:Massive_Yet_Tiny_(MYT)_Engine
-
85-86 XT 4WD 86-87 GL 4WD 86-91 Loyale/GL 4WD 88-91 GL and XT-6 4WD Look at all the above. Remember it was frequently and OPTION. The big silver "LSD" sticker on the rear cover is a quick way to tell. Of course do the rotation test to be sure. The common 3:7 ratio is a fantastic ratio for street with a 5 speed.
-
I have them in two of my 240Zs. To bolt in you need to remove the R160's side stub shafts. They are retained by a PITA bolt requiring a very thinwall 8mm socket that will probably break. The easy way is to cut the shaft with a cut off wheel to access the bolt. Then withdraw the shaft and replace with stock 240Z stubs that have the flange to bolt the halfshaft to. The nose flange will work with a shorter driveshaft or swap it with the stock R180 one, but that requires removing the difficult retaining nut and maybe a puller. I have run one 70K hard miles behind a hot street L28 so they are tough. I would not expect it to hold up to hard drag style launches. They are considerably lighter than a R180. The LSD diffs have a big silver "LSD" sticker on them. The ones you want came as options in early to mid 80's Subarus and are 3.7:1. A few 411:1 LSDs are out there, but rare. The clutch pack from a 3.7 r160 will fit a 4.11 r160 but requires special bolts for the ring gear.
-
I'm running a 1mm over 2.8 with flattops, Isky L9 cam and a modified E31 head (not my first choice, but it's what I had at the time) with 280Z valves and 5cc removed from each chamber. I have had 2 sets of tripple Webbers, 3 different 4 bbl setups and dual SU's. The SU's ran out of punch at 5800 until I put in 3/8" fuel lines. Now it pulls clean to 7K. I won't run anything else until I get around to FI.
-
My car will be mainly street (not daily driver) with infrequent drag strip and track days, so weight dist. is important, although a one gal cell even full is rather insignificant. I am considering relocating the battery behind the passenger seat with an approved battery box and putting the cell under the hood. Any other bright ideas?
-
Is anyone running a seperate dedicated fuel cell for injection with nitrous? I am thinking about using a 1 or 2 gal fuel cell (Jegs) for race gas to enrich with the NO2. If yes, what size and where did you mount it?
-
I posted this in the welding forum and did not get any responses so I'll try here: I bought a set of Summit (Patriot) SBF block hugger headers because they will allow engine installation without cutting my steering linkage. I am using AFR heads and the exhaust ports are bigger than stock so the header ports are too small by 0.2". The hole in the 1/4" flange is the correct size for the larger AFR head, but after inserting the header tube and welding they are undersize for the AFRs. Would it work to weld around the tube on the outside of the flange and then take a rotary grinder and open the flange back up by grinding out the tube and inside weld? There is enough material built up on the head side of the flange to still have the raised "sealing bead". I am concerned if they would be strong enough not to crack. I plan to send them out for coating so rust should not be an issue. If welding will work what kind of weld would be best?
-
I bought a set of Summit (Patriot) SBF block hugger headers because they will allow engine installation without cutting my steering linkage. I am using AFR heads and the exhaust ports are bigger than stock so the header ports are too small by 0.2". The hole in the 1/4" flange is the correct size, but after inserting the header tube and welding they are undersize for the AFRs. Would it work to weld around the tube on the outside of the flange and then take a rotary grinder and open the flange back up by grinding out the tube and inside weld? There is enough material built up on the head side of the flange to still have the raised "sealing bead". I am concerned if they would be strong enough not to crack. I plan to send them out for coating so rust should not be an issue. If welding will work what kind of weld would be best?
-
Thanks John, that is what I am asking. Since the head ports are larger than the manifold I guessed the turbulance would be minimal, but I don't have experience in V-8s. If it is just 2-3hp on a 380-400 hp combo then I could let it ride. One article I researched even said it would help minimize reversion and recommended it on street engines. But the hotrodder in me says match it perfect for max hp? Pro engine builders chime in please! Will Piatt
-
My Edelbrock Air Gap intake manifold runners are smaller than the AFR head's ports by a very uniform 0.1" all the way around the circumference of the port. My searching yields conflicting advice. Some say port match it perfectly even, the AFR instructions say leave .050, the Edelbrock instructions say leave a .020 edge. Is it worth spending my time port matching for a hot street motor in this case?
-
Good stuff, thanks guys, it got a few new wheels turning in my head. Will Piatt
-
Well I hit my head on a rollbar in my Jeep four wheeling when I was a teenager in the 70's and it felt like the padding was not there! I really would like to increase rigidity and get some roll over protection. Here is what I was thinking. If you can understand my description let me know how this might work. Run a heavy main hoop from the rocker/pillar junction angled back more than usual going up tied to the wheel well and going behind the dome light where the hatch begins. Brace it rearward with an X. Make a horizontal U from the main hoop for harness attachment and let it tie in to the strut towers too. Then from the main hoop at the wheel well, triangle more sharply down to the rocker beside the middle of the seat bottom. Where that door tube attaches to the rocker use a plate about 14" long to box the rocker (like the bracing on a Z convertable conversion). That would give some roll over protection, keep the hoop back away from my head and the door bars end up not very for forward so as to be minimal impact on the side of the body and allow easy access. Then I was going to reinforce the frame rails and tie them to the rear subframe similar to Bad Dog parts. Use a PDK style front brace to tie in firewall, strut towers, and front swaybar mounting points. My big concern is I have watched crash videos and with 3 pt street belts the head can travel pretty far around the cockpit. If the cage is going to increase danger I would rather just go the subframe buildup route.
-
Thanks guys, keep the ideas coming. And yes Mike, I corner hard. I live and drive in the Blue Ridge Mtns. and hope to do track days at VIR someday. Because I drive in the mtns I am looking especially for rollover protection in case I go off road. What if I angle the main hoop just behind the dome light and brace it good?
-
Folks, frequent lurker, seldom poster here. I have spent countless hours researching via the search on this forum and have accumulated a lot of great ideas. However I would like some additional ideas for a roll cage. This car is an "early" 74 with zero rust issues, and will have a SBF engine with about 350 ft lbs torque at the crank. It will be a weekend street driven car with a passenger, once or twice a year track days, and a couple times a year drag strip evenings. Therefore I do not have to conform to any santioning rules. My goals are: chasis stiffening, increased safety without a helmet, minimal weight gain, not too difficult entry/exit. Also, combinations of other stiffening methods are ok, ie cage plus PDK braces or subframe connectors. My engine will be mounted to a square tube frame crossmember connecting across both frame rails behind the factory front crossmember. Let me hear your ideas on design and materials where rules don't limit design.