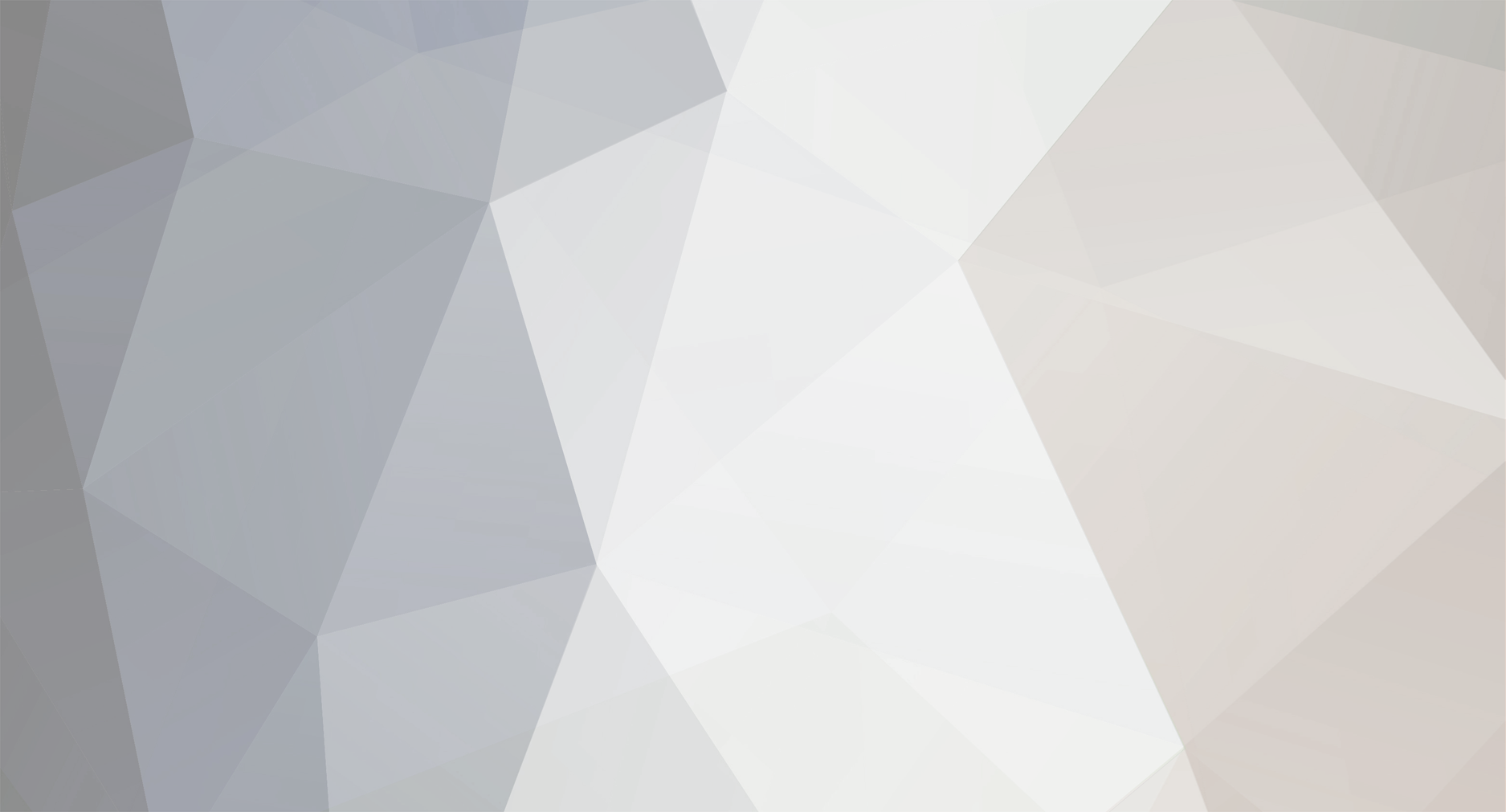
WHP
-
Posts
93 -
Joined
-
Last visited
Content Type
Profiles
Forums
Blogs
Events
Gallery
Downloads
Store
Posts posted by WHP
-
-
I did a search and just got confused reading the threads. I have an early 74 hybrid project car and I want to put in a Quaife R200 with CV axles. I have several different gear ratio R200 diffs, all with bolt in halfshaft flanges. I have 2 CV axles from unknown ZX cars, but they have 2 different diameter splined shafts that plug into the diff. I also have the ZXT CV adaptors welded to my 74 outer stub axles.
1) Do all R200 diffs use the same dia. spline axle? (maybe the smaller one came from a R180?) Or is the ZXT the larger one?
2) Can the proper CV axle be put in ANY R200 diff? I thought there was a snap ring to reatain the axle in the diff. Can I just buy ZXT CV shafts and plug them in the diff I have?
3) What is the cheapest source of getting a Quaife installed in my diff?
Please spell out what I need (in simpleton terms) to achieve my objectives. Thanks!
-
I have a fiberglass BRE spook I want to put on my '72. What is the preferred way to attach it? Does it need to be removable for service such as a ramp at the alignment shop?
-
Josh, I'm using Al's front cross member, thus that engine position. I'm also going to reinforce the car by running rectangular tubing from the front just behind the TC mount to the rear subframe. To maintain ground clearance on my lowered car (it will be street driven) I'm cutting out the floorpan rail and slot the floorpan where the rail was and allow the tubing to protrude into the cockpit. Kind of half in and half out, then weld it up. This will allow me to turn the rectangular tubing vertical like a full frame vehicle. The factory rear subframe is higher than the front rails so the new rails will angle up toward the back some. The intrusion into the cab will be between my feet and minor at that point. As it goes up toward the rear it will be mostly concealed under the seat. I plan to make a JTR style transmission mount that ties across to these new rails too. I plan to sandwich the front rails with tall reinforcement scab plates just forward of the firewall, hopefully even welding to the firewall contour. I'm going stock EFI until the car is sorted, then add AFR heads, cam, intake, etc. What are you using for headers?
Will Piatt
-
Looks great Josh! I'm doing the same thing and your pics are making me excited. Where did you get the motor mounts to fit Al's crossmember? I got my '91 Mustang EFI 5.0 motor with all accessories, cables, ECU, harness, sensors from All Mustang Recycling in Phoenix AZ. It was very clean. I also bought from them a new HD clutch, T/O bearing and new world class T-5, bellhousing, fork. Shipping to NC was only $375 for all of it. Speak to Tom, 800-454-8387. They sell hundreds of these to kit builders and hot rodders.
-
Do a search about the fumes, its been covered. The cars did not stink when they were new. There are a number of details that can contribute to fumes in the car.
-
Don't risk your bearings any more! Pull the distributor and oil pump. Remove the the distrubutor drive shaft. Fill the oil pump with oil and replace it without the distributor drive shaft. Using dowel stock shaped like a flat screwdriver and a drill turn the oil pump in run direction(CCW) until oil circulates. Check under the valve cover for oil to the cam also. Use your third arm or girlfriend to manually turn the engine over with a wrench on the crank pulley bolt while the drill keeps the pressure up. Reassemble and start the engine. The stock oil pumps almost never are bad and will prime fine with regular oil.
-
My car settled quite a bit after two weeks. I cannot say how they compare to stock because my original springs were sagging bad. I also cut 1 coil off the AZ springs for lowering. I checked rate on these springs before cutting and they were as advertised 180/200. Regular inserts could not control them, I ended up buying Tokico adjustables and like the combination a lot.
-
Great information Dan, thanks. Anybody tried any aftermarket intakes for fitment?
-
Bluex-v1's site says there is hood clearance. I'm starting this swap this month, but would prefer to keep the original hood lines. What is the consensus on EFI hood clearance?
-
I was reading about head porting theory on this site and found it extremely interesting.
-
Is anyone running this on their 240Z that could verify the fit before I plunk down the $$$? Ross said he had no verification as of yet. Thanks.
-
Thanks Tim, where would I go to find/learn about one. I'm putting a 5.0 EFI in my early 260Z.
-
Can a fuel gauge be made to work with a fuel cell?
-
Lincoln Mark VII engines with low mileage are easy to obtain here, unabused GTs are rare. Did any come with forged internals like the late 80's GTs? I was thinking of getting a low mileage engine and swapping cam, heads, and intake. Any Ford techs know?
-
Looks good Al. I did extensive port matching and tapering the indented areas cast to clear the mounting bolts. PITA, but it was cheap. I got the 2.5" exhaust system from Motorsports. The twin downtubes are slightly larger and do not slide up into the manifold. They required port matching to the manifold. Looks like it will work ok.
Will
-
Acccording to the manifolds I have in hand the twin exit holes are the same 240/260/280/280zx, although the 3 stud bolds change size and location. I would get NISMO headers except I'm on a tight budget as this is my daily driver. I don't want to divert funds from my other car, a 302Z project. I'm going to open up the twin holes, contour the inside of my port matched P79 and make an oversized twin downtube with crush bends. I think it will not be so bad since the bends are not that sharp. It will connect to a 2.5" mandrel exhaust.
Will (high performance projects are always compromises, usually $ related)
-
When I look at the internal size of the 240 "skinny" manifold I am afraid it will be restrictrive on a modded 2.8. However, the interesting thing is the exit holes where the downtubes attach are the same size as my ZX boat anchor. Should I look into opening the ZX manifold up to the next larger size tube?
Will
-
I'm facing the same delema. got all those manifolds on my bench now. Dyno data would sure help! There is a dyno test I think its on Zcar.com with the N42 manifold on a stock L-24. It was 4 hp less than expensive headers. I'm using a modified E31 head on built L-28. I have a new set of motorsport headers but they port match really bad and look poorly made inside too, pure junk. The L-24 used the skinny manifold and a long twin downpipe I'm guessing for scavanging, but I'm skeptical if it will flow well enough for the larger hot L-28? I settled on a P71 "fat" round port manifold as it looks like it will flow better after port matching. The port squish for bolt clearance is less so the passages are larger. BTW, it has the same size outlets for the downtubes as the 240. I'm thinking of using the long 240 downtubes welded to the larger conector flange and add 2.5" exhaust on where the downtubes converge with a fabricated conection to make a good transition. I'm going to live with the extra 14# and not worry about exhaust leaks. Port matching is half done, boring......
Will
-
Guys, I haven't done it yet but my plans sound a lot like ZXGTS-4. I don't want a cage in my street 240Z. I'm going to cut out the original framerails and slot the floorpans to run square tubing from the front TC area to the rear subframe with the tubing protruding thru the floor as needed to go straight to the underside of the rear subframe. Then weld the floorpans to the side of the rails. That should save my ground clearance and not stick up much between my feet, but will stick up slightly higher under the seat. I am going to tie these new square rails together laterally with a modified transmission mount simular to JTR. I'm installing a 5.0 Ford engine and have ansil's motor crossmember to tie the front frame rails together. And finally front and rear strut tower braces. Comments or suggestions appreciated....
Will Piatt
-
I tried a linelock for a parking brake on my 510. It bled down and my car with 1 week old paint job rolled across the parking lot and into a concerete wall, DOH! Somehow I managed to not have it all the way into 1st gear. Not cool being paged to the front office just 2 days after everbody at work was outside admiring my newly completed project.
-
Per K&N the formula for air filter size is:
A=CIDxRPM/25,500
A= air filter area
CID= cubic inch displacement
RPM=max engine revolutions per minute
I never knew, but ASSumed the area is the general outside deminsions, not the surface area of all the pleats.
Will Piatt
-
I've seen two kinds of hazard switches. One is a push-pull with green light in the knob. The other like I was working with is a toggle switch. Inside it are a couple of sets of rocker contacts. When you push the handle down, inside 2 spring loaded plungers rock up to push the top contacts closed. Flip the switch up and the plungers move down onto the bottom contacts. I carefully straightened out the metal switch body and removed the non-conductive back with the contacts. Don't lose the spring loaded plungers, they are not held in by anything except grease. I then sanded the contacts, cleaned them with contact cleaner and reassembled. I used a small punch to stake the back closed again. Works like a new switch now.
Will Piatt
-
The problem was the back of the hazard switch was loose. I took it apart, cleaned the contacts and staked the back on securely and it works fine now. Got that inspection sticker whoo-hoo! Thanks Old Rice.
Will Piatt
-
I hope the TS switch is not it. It was replaced with a new Nissan part last year and they ain't cheap. I have a spare Hazard switch, I'll try that first since all the power goes thru it before getting to the TS. Thanks guys.
Will Piatt
R200 axle fit-HELP
in Drivetrain
Posted
I know the CV axles were removed from 280ZX or ZXT cars. I don't know for sure that what was in the donor cars was original. At the time I didn't know what I was looking for and got these at a JY and the cars are probably gone now. I got a RHS from one car and a LHS from a different one as the boots were torn on the other CV joints. I knew about the different stub lengths but missed the diameter difference. The larger diameter one does fit a R200 from a 200SX turbo that I have laying around. However I want to use my 3.54 R200 and it has bolt in halfshaft flanges for U-jointed halfshafts. I am sure these are R200's as I have numerous diffs R160, R180, and R200. I really would like to avoid swapping ring gears etc. Can anyone give me some advice on how to end up with a Quaife 3.54 R200 with CV axles?