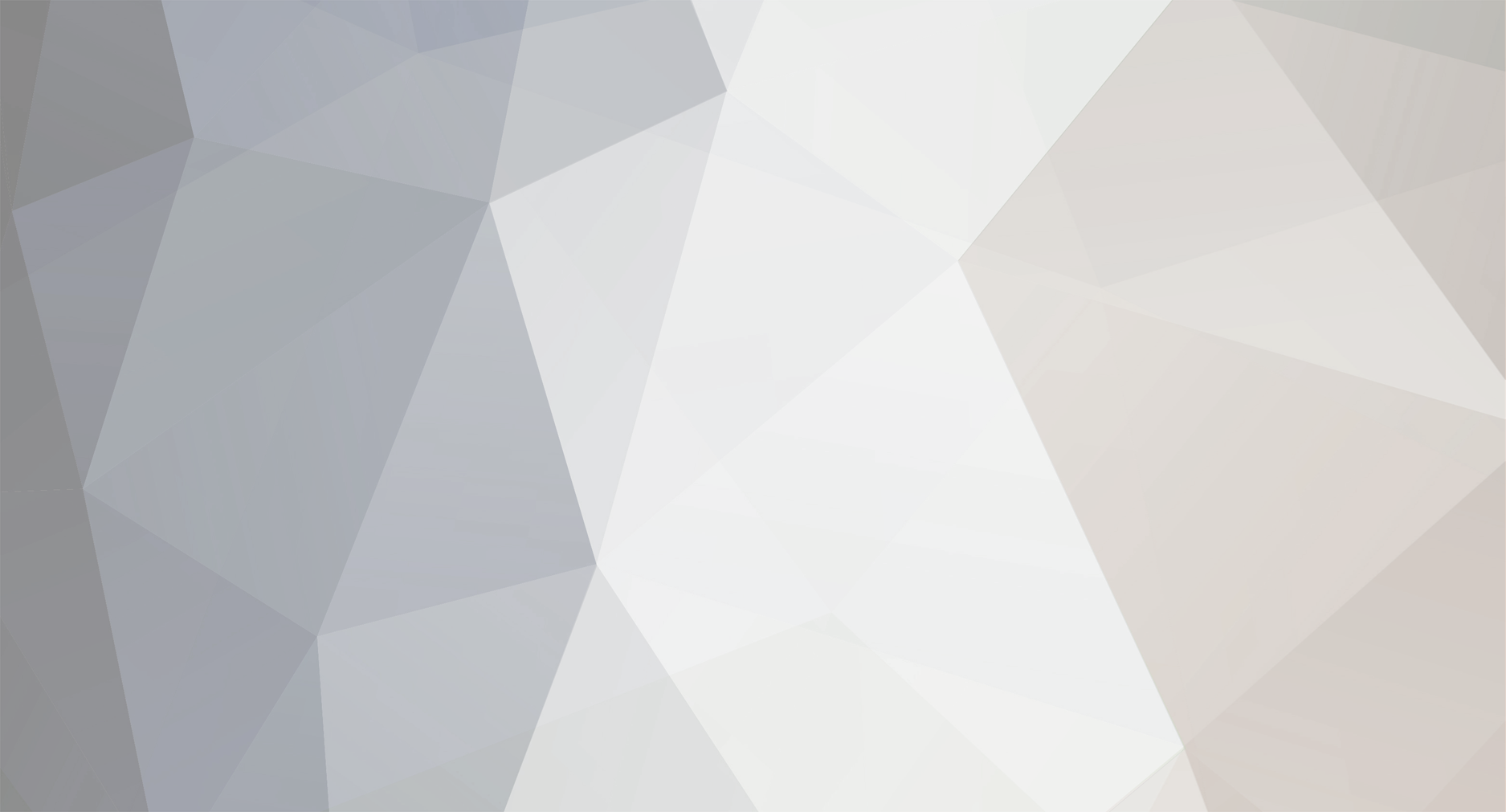
Oddjob
Members-
Posts
129 -
Joined
-
Last visited
-
Days Won
1
Content Type
Profiles
Forums
Blogs
Events
Gallery
Downloads
Store
Everything posted by Oddjob
-
Finally got the pressure switch in and wired. It was a pain because of the crowded area for the plumbing connection, due to the pancake adapter for the oil cooler. If you would like more information on how this is wired, go here: http://forums.hybridz.org/showthread.php?t=151929 and scroll down to post # 4. The two thumbnails show the completed installation. The top wire on the RH column of the ground buss is the ground for the pump.
-
Omar: You don't have enough information yet to know for certain it's the alternator. Do you have a voltmeter on the car? If not, borrow a VOM from someone. Read the meter with the car off, on the battery terminals. It should be 12 to 12.7 volts DC. Now start the car. If the voltage goes up to about 14.5 volts, there is probably nothing wrong with the alternator. Does the car still have a voltage regulator? Also, please confirm this: The battery goes down when you run the car, not overnight when it's parked?
-
Well, I don’t agree that a ground plane amounts to many parallel resistances. A ground plane is, by definition, one massive ground. Now it is certainly possible to have a number of paths through that single ground, but that will not necessarily result in “an imperceptible resistance”. However, it probably isn’t very helpful to quibble about theory, so I did a bit of empirical observation. The 1971 S30 on which I installed the star grounding system is a full-on restoration/enhancement, which is about 65% done. Everything on the chassis which would come off has been off, has been rebuilt or replaced and has been reattached with new hardware. Any rust found has been repaired by welding, including the replacement of the floor pans. In short, as regards grounding, the physical car is probably pretty average for a restoration, is very much better than an un-restored vehicle, and I am guessing is equal or better than a stock Z when it was new. I disconnected the star grounds at the buss and insulated them, effectively restoring the car’s grounds to “stock”. I then measured the resistance from the negative battery cable, which was attached to the stock location on the starter, to various points around the car. I then restored the star ground buss and re-measured. For this measurement, I borrowed a 3M 965 DSP, which is essentially an industrial digital VOM, costing about $3000. The instrument measures from 0 Ω to 999 MΩ. The chart below shows the results. The first two columns are the observed resistances in each case. The resistance readings for the standard ground and the star ground are directly comparable. The voltage drop calculations for the star ground apply even though the measured resistance is zero ohms in all cases. Note that I did not calculate voltage drop for the stock “ground plane” configuration. None of the voltage drop tools I usually use will do the calculation, because they assume a two-conductor (out and back) circuit of copper or aluminum of the same gauge. The ground plane material is steel (mostly), and of no certain gauge, with many connections. The best that can be concluded is that the ground resistance through the chassis is both higher and very uncertain. That much can be seen directly from the data. Since the measured resistances through the ground plane, in all cases, are higher than zero, I am left to conclude the voltage drop in a chassis ground is rather worse than the star ground. [The chart is in the .pdf at the bottom.] Crib Notes: For those who are not electronics types, a VOM is a volt-ohm meter, a test instrument. When measuring resistance, a low number is either a short or a really good connection and a high number is either an open or a really bad connection. Which is most desirable depends on what you are doing. In the case of a ground, a reading of zero is perfect, and anything less is undesirable. Even with a reading of zero, there will be some resistance and therefore some voltage drop. Even a very good meter does not resolve low resistances very well. Voltage drop at your load is undesirable because all electrical devices are designed to produce their rated results at a particular design voltage. In the case of your Z, that is about 14.5V with the car running. So if you expect your 55w headlight to produce its rated number of lumens, it must see 14.5V. If it is actually getting say, 13V, it will be dimmer than it should be. The interesting thing is that in this example, the bulb is seeing 89% of its design voltage, but will only produce something like 75% of the light it should. This is true for all the load devices in the car. Volt Drop Chart.pdf
-
Oil pressure switch wiring... To coil or not to coil?
Oddjob replied to 7MGFORCE's topic in Ignition and Electrical
The "NC" goes to the starter solenoid. The "NO" could go to the coil, if the wire and fuse feeding the coil are big enough (they probably aren't), and you are certain you have 12-14V on the terminal. The wire you found under the dash is a much better candidate since it is probably fed by your fuse panel. -
Oil pressure switch wiring... To coil or not to coil?
Oddjob replied to 7MGFORCE's topic in Ignition and Electrical
I'm in the process of installing a Holly fuel pump and the pressure switch. If it would help you, you can follow along here: http://forums.hybridz.org/showthread.php?t=147928 and scroll down to post # 19 and # 21 (I'm working on 22 now). To answer your question: first, don't ground any of those contacts! The three contacts on the switch are marked "C" (common), "NO" (normally open), and "NC" (normally closed). Common goes to the positive wire on the fuel pump. Normally closed goes to the positive terminal on the starter solenoid. (The small terminal that goes positive when the key is held in "start" position, not the big one connected to the battery). Normally open goes to any positive source which goes live with the key on. This one should have a 15A fuse inline. Don't use the coil, as it is often fed by a resistor wire, which will only apply 6V to your pump. What happens with the above connections is this: When you crank the engine, the pump will run only while you are cranking. When the engine starts, and the oil pressure comes up, the pump will run. If the engine dies, the pump will stop. This switch is a safety, to keep your electric pump from squirting fuel onto a fire in a collision. It makes your electric pump act more like a mechanical pump in this regard. -
Take a look here: http://forums.hybridz.org/showthread.php?t=147928 and scroll down to post # 13. I got it here: http://www.rallylights.com/ and they do have other styles.
-
If you would like to see the industrial, overbuilt, never-have-trouble-again solution, take a look here: http://forums.hybridz.org/showthread.php?t=147928 and scroll down to Post # 15. Fair warning: it's long and a bit theoretical....
-
Can poor ground weaken starting power?
Oddjob replied to Tempered's topic in Ignition and Electrical
Do you have a cable from the starter case to the frame? Some relocation kits come with one, some don't. The original location negative battery cable connects directly to the starter case. The lack of this connection would increase resistance to a point which would make it sluggish starting, as you would be grounding through your motor and transmission mounts, and other uncertain paths. -
The first thumbnail below shows the electric pump assembled with its brackets, prefilter and fittings, together with some of the other parts which will be needed. The brackets will bolt to the spare tire well, with the pump below the low point of the gas tank. The pump is a Holly red top, which will be more than enough for a twin SU induction on any L engine. The prefilter is 100 microns. The main filter located on the fuel rail (shown above) is 40 microns. The mechanical pump will be removed and blocked off. Note the wire. This two conductor jacketed wire (12AWG) is actually automotive wire, not speaker wire. It is rated at 105 C. See the discussion on grounding above for the reason for using it. The second thumbnail shows the oil pressure (safety) switch assembly. The existing analog oil pressure guage line connects in a very crowded area, with the pancake adapter for the oil cooler taking up the space needed for a tee and the switch (third thumbnail). The switch assembly will be remoted to the nearby wheel well. The existing guage line goes in the open side of the tee.
-
This is in response to an inquiry from PanzerAce: The part is from MSA, and is listed as a "radiator overflow kit" on page 80 of their CD-ROM catalog, part #16-7000.
-
Fusible Link Upgrades Will this work?
Oddjob replied to beebeecivic's topic in Ignition and Electrical
Here's the one I used: http://www.crutchfield.com/p_211FBXS024/StreetWires-FBXS024.html?tp=3001 It's a bit more expensive than yours, but takes up to 125A fuses, and uses #1/0 cable in/out and #4 on the circuits. -
This may be of some help to you if you are trying to run down and fix grounding problems in the Z. This is how I handled it: http://forums.hybridz.org/showthread.php?t=147928 Scroll down to Post #15. I'm not certain an electrical diagram will be much help to you because of the way grounds are done in most cars, including the Z. The post above explains why.
-
The pump itself may tell you its draw (in amps) on a label attached to the pump. If it's the stock 260Z electric pump, you can get the draw out of the service manual. If all else fails, check to see the size of any existing fuse (and wire) and just copy those. An inline fuse holder, fuse and automotive wire are available on the shelf at most any auto supply. They usually have momentary switches, as well. The capacity of the switch will be printed on it, usually on the back. In general, if you size everything for 15 or 20 amps, you will be fine.
-
Yes, idea #1 is right, with reservations (the devil is in the details). Do not use any switch other than momentary for the primer circuit, and do strongly consider the pressure switch. Check on the current draw for the pump. If it's too high for your switch, you'll need the relay. Be sure to include a fuse right after the connection to your power source. The right value will be about 150-200% of the running current for the pump. Be sure to size your wires to carry this current. Good luck, I hope this solves your problem.
-
The primary idea of the safety switch is to avoid feeding a fire in an accident or rollover. If you want a manual primer, you would put a momentary (pushbutton) switch from an always live B+ (eg. the battery) to the NC terminal of the pressure switch, and don't put in the connection from the starter. The pump would run when you held down the button, and would run normally when the engine was running.
-
You might look into a pressure switch (Holley makes them, Summit carries them). This has a big safety function: if your engine has no oil pressure, the pump won't run. The pressure switch has one B+ out, which goes to the pump +. It has two B+ in terminals, a normally closed (NC) and a normally open (NO). The NC contact goes to your + starter terminal so the pump runs when you are cranking the engine, even if it has no oil pressure. The NO terminal goes to any + which is live when the ignition switch is on. The pump runs when the ignition is on and there is oil pressure. The pressure switch comes with wiring diagrams, including one for using a relay, if you like.
-
During the rebuild, the gas tank was removed, cleaned and remounted with new straps and a new sender. The vapor recovery was dismounted and cleaned and all of the hoses associated with it were replaced with new. The gas filler was repaired and chromed (it had some rust damage). The gas cap is new. The fuel lines were blown out with compressed air. The fuel pump is new, as are all the rubber hoses associated with the fuel lines. All clamps are new. The carburetors were rebuilt and the fuel rail was customized, including a new fuel filter. When the car is under acceleration, it seems to “run out of gasâ€. It doesn’t do it in first, and sometimes not in second, but always does it in third and fourth. It does it sooner under hard acceleration, and later under moderate acceleration. At highway speeds, it will eventually do it in fifth while simply cruising fast. The fuel pressure gauge sometimes reads 0, sometimes 2.5 PSI (at idle). The gauge has been replaced once, as the first was thought to be defective. Relief holes were drilled in the gas cap to eliminate any possibility of vacuum in the tank. This helped, but did not solve the problem fully. The ignition has been thoroughly checked, and is not at fault. The only real deviation from stock trim is that the fuel bypass line is currently capped off, as there is a pressure regulator on the fuel rail. This problem has been described by others in the Hybrid Z archives, so it seems to be somewhat common. Since Datsun added an electric pump at the tank with the beginning of the 260Z model (retaining the mechanical pump), they were apparently also aware of this as a problem. The existence of this problem stands to reason, as the inlet of the mechanical pump is 18†higher in the chassis than the opening of the siphon tube in the gas tank. It is well known that most fluid pumps do not “suck†well, although they will “push†fluid quite well. Most pumps prefer their inlets be gravity fed, so that they are flooded continuously. This is obviously impossible as the car was originally made. From all of this I have concluded that installing an electric pump at the gas tank should solve the problem.
-
The big belt on the alternator works wonderfully. The car is actually running perceptably stronger. I am going to leave the "Electrical" topic for a while, and come back to it. I am currently building the B+ (positive power supply) buss, and revising the associated wiring. When I have enough pictures, I will post. The next topic will be fuel supply, which has some interesting problems, problems I notice others have experienced.
-
At some point, you have probably held an alternator in your hands. You probably will remember spinning the pulley by hand, which turned easily. It should, as its shaft is suspended on two good ball bearing assemblies. After you overcome the inertia of the heavy rotor, the shaft spins freely. This applies equally to a small 40A alternator or a big 105A one. If you mount the alternator and put the belt on it, but don’t connect any wires to it, your engine will turn it every bit as easily, albeit faster. At this point, the fan on the alternator pulley is the only significant mechanical resistance, and that is not very much. Once you connect the wires and put a load (an electrical device which uses electricity) onto the alternator, it will begin to produce both voltage and current, which are collectively called electromotive force or EMF. The key thing you should understand here is that the alternator does not produce much of anything unless there is a connected load demanding it. Now here is where it gets counter-intuitive. When a load causes the alternator to produce an EMF, that entire working circuit generates a reverse EMF in the alternator. In practical terms, what that means is that the alternator shaft gets harder to turn. This relationship is directly proportional. The more current you demand from the alternator, the more horsepower the alternator will demand from your engine to turn its shaft. In my Rose’s Ride example above, the stock belt slipped because the big alternator became too hard to turn as the load on it increased. When the smooth stock belt was replaced with a toothed one, which wouldn’t slip, it worked fine until a bigger load came along (the headlights), then it broke. But, you may say, why does the stock 40A alternator not cause the belt to fail? First, the small alternator is self-limiting. It can’t produce much more than 45A (surge), and therefore can’t demand much mechanical force from the engine. Secondly, when you load the small alternator at or above its capacity, you will get a voltage drop. You will have exceeded its ability to regulate its output to its preset maximum value. This is much like a brownout you may have experienced in a city during the summer. When the load on the city electrical grid exceeds its capacity, the voltage drops off. This voltage drop in your car will go from 14.5V to 12.0V, at which point your battery begins to discharge to support the alternator. The trouble is 12.0V is only 82% of your peak voltage and your performance suffers accordingly.* When you use a big alternator, it does not self-limit until 125A (surge). Nor does it go into voltage drop until over 100A. What that means is that the electrical system is performing at peak voltage pretty much all the time. The trade-off is that it takes more engine power to maintain this higher voltage. For me, the trade-off is worth it. The matchbox distributor uses full supply voltage (there is no dropping resistor), so it will perform at its peak all the time. The lights will be fully as bright as they ought to be, the horn will be as loud is it should be. It is my belief that this trade-off literally makes as much horsepower as it costs, and is therefore worth it. Since we are on the general subject, I am going to digress a bit, and tell you about some choices I did not make for Rose’s Ride, and why. In this case, I chose not to install an electric fan and an electric water pump. Before I go further, I will admit I think both are very cool, and both have their proper applications. But I think their application is not on an S30 with a NA L-series engine. Here’s why: The usual reason given for this conversion is to “save horsepower†for the rear wheels. OK, good idea. The water pump and fan use a certain amount of mechanical energy to accomplish some work. That is, they circulate water and air, respectively, both of which are needed, and they are driven by your engine. If we assume that the amount of water and air circulated are the same for both the mechanical and the electric versions of each, then it follows that the amount of energy each uses must be the same, or very nearly so. If you drive the pump/fan mechanically, it will take a certain amount of engine horsepower to do it. But if you drive them electrically, you will still use the same amount of horsepower or more to do the work. Why? Remember reverse EMF from the discussion above? The same amount of horsepower will be sucked up by your alternator to drive your electrical pump and fan. In fact, it will actually be more, because of conversion efficiency. Your mechanical water pump more-or-less directly converts rotational mechanical energy to moving water. But your electrical pump must get its energy from the alternator, which is converting the engine’s mechanical energy to electrical energy. The trouble is, it isn’t very good at it. The alternator is only about 40% efficient in making this conversion. So you really end up using more horsepower, not less, to drive these accessories. Yes, you can adapt. You can use a smaller pump or fan. You can use a thermostat to turn the accessories off when they are not needed. You could even design a control circuit to use when you are racing. All of this is possible, but not, I think, practical for a daily driver. * Note: The voltage drop condition described above is not the same thing as a low voltage condition when the car is idling. Low idle voltage is a problem with the design of the voltage regulator or the alternator itself. My 105A alternator produces a solid 14.5V at idle.
-
As I noted above, one of the additions to Rose’s Ride was a Z Specialties 105 ampere alternator (thumbnail 1). http://www.datsunstore.com/product_info.php/products_id/1?osCsid=3748af39a3ff513aec6edd48bedbde3f Aside from the sheer additional capacity, it is a modern one-connection design, which is internally regulated. It bolts right in, and potentially cleans up some archaic technology and several potential failure points. As advertised, it was an easy installation, but it came with one very big gotcha. After running the car about 100 miles after its rebuild, the indicated voltage on the car’s voltmeter dropped from 14.5 to 12.0. Some troubleshooting revealed that there was no output at the alternator terminal. Bad alternator, right? Nope. From observation, I would have sworn, truly taken an oath that the alternator pulley was turning at the exact same speed as the engine pulley. It was not. The belt was slipping on the alternator pulley to such an extent that there was no output from the alternator. The car has a lightweight single-groove harmonic balancer and MSA’s billet aluminum water pump pulley. These are both grooved for the stock belt (thumbnail 2). It turns out the stock belt slips badly through the alternator pulley, which comes grooved for a larger belt, which Z Specialties recommends (thumbnail 3). By replacing the stock belt with a heavier-duty one of similar size to stock, but internally toothed, the slipping pulley was cured. However, turning on the lights produced the results in thumbnail 4. The new belt shredded in less than 30 seconds. I will explain why this occurred in the next post. The balancer and water pump pulley were sent to the machine shop to be re-grooved for the bigger belt Z Specialties recommends (thumbnail 5). The long-term results are pending, but I think this will solve it. The next post will go into some theory regarding why this condition occurred, and I will also discuss some design considerations which are not immediately obvious.
-
Theory: The Z as it comes from the factory uses a ground plane to supply the negative side of all its electrical circuits. This scheme is cheap to manufacture, both in time and materials, but does not perform particularly well, and really does not age well. The chassis is grounded to the negative side of the battery and alternator, and negative for all electrical devices is picked off of any convenient nearby metal. The trouble is, the ground plane is not a single massive piece of metal. It is composed of hundreds of welds, bolts and rivets holding various pieces of sheet metal together. To begin with, steel is not a great conductor as metals go. Add to this the necessity for undercoating, vibration deadening, adhesives, gaskets, caulk and other non-conductors, and things get complicated. Then add age: iron oxide (rust) is a semi-conductor under the best circumstances, and a non-conductor under the worst. With corrosion, road grime, paint, salt and oil working into once tight connections, and the ravages of 35+ years of vibration loosening everything up, you can see why your grounds might be less than perfect. I think I can state without fear of contradiction that the number one source of electrical problems in the Z is from bad grounds. There are two general ways of improving your grounds. Both involve running a dedicated copper ground wire to each load device. Before you panic, no, you don’t really have to run two wires to everything on the car. You certainly could, but that would be more trouble than it was worth. The two grounding schemes are referred to as loop and star. In looped grounding, you take a ground wire from your reference source, which will be either end of the negative battery cable. You run it from there to your first device, say the alternator case. You then extend from that point around to your next device, say the distributor. You keep going like that until you have connected every target device. Notice that I say “target” device as opposed to “every” device. You will certainly want to do this with mission-critical devices (the distributor), and possibly devices which are performing badly (that annoying tail light), but you need not do everything on the car. In star grounding, you build a central grounding point (a ground buss) and homerun each ground from the load device directly to the buss. Again, you need not do everything on the car, just the important stuff. Of these two schemes, star grounding is preferred for technical reasons. There is a subcategory of star ground, usually called a technical ground, which is even a bit better. For those of you who are running ECUs, sensors and any other complex electronics, this is the way to go. A good technical ground scheme will usually clean up all sorts of electrical performance problems which don’t seem to make sense. For my project, I chose a star grounding scheme. Since I deliberately selected a pre-smog, normally-aspirated engine without the need of an ECU, I did not need to go with a technical ground. The first thumbnail shows the ground buss mounted below the battery. This is a drilled solid copper bar purchased from Storm Copper over the internet: http://store.electrical-insulators-and-copper-ground-bars.com/index.html Click on “ground bars”. Note that it comes with stand-off insulators. I mounted mine on metal sleeves bolted directly through the sheet metal, without using the stand-off insulators. If you are going to do a technical ground because you have an ECU you must use the insulators to isolate your ground buss from the chassis. The negative terminal of the battery is connected directly to the buss bar via a black 1/0 cable. The ground buss is then connected to the starter case using another black 1/0 cable with ring terminals on each end. Be sure to burnish (sand) the copper right under the terminals, and use lock washers (star washers are best). The remaining larger cables on the buss are all #4 AWG, purchased as part of a kit. You can see it here: http://www.sportcompactonly.com/Grounding-Wire-Kits/Ignition-Electronics/Performance/part_c-78_p-66401.htm This kit is pretty typical, and is actually intended for looped grounding installation, as the kit does not contain a ground buss device. The #4 cables on the buss run to the alternator case, and the cylinder head near the spark plugs (2 places). The smaller cables, which vary in size from #8 to #12, run to the matchbox distributor, stereo power amplifier, horns, a distribution point for the headlights, electric fuel pump and a distribution point for the gauges and other under-dash loads. The third brake light is also grounded directly to the buss. When I get around to putting in LED tail lights, I will run a distribution point for that to the rear. A word about wire size: bigger is better, within reason. I used a #4 to ground the alternator, but remember, it’s a 105A alternator. If you have a stock 40A alternator, a #8 would be plenty. A good guide is to look at what was there originally, if anything. If the design engineers used, say, a #14 to supply B+ to a light 12’ from the battery, you can bet they allowed the maximum voltage drop for that run. If you install a #12 (2 sizes bigger) for the B+ and a #12 ground for that same light, you should now get something very close to full voltage at that load. Just remember that Ohm’s Law applies; the resistance of the conductor material along with its length and cross-sectional size (gauge) will determine voltage drop to the load device. Well, that and contact resistance. In simplest terms, the more connections you have in a wire run, the higher the resistance. This is one reason why star wiring is superior to loop wiring*. There are fewer connections. In a typical star-ground circuit, you will only have two contacts from the buss to the load. The number of connections and their quality will determine your contact resistance. These contacts should always be terminated: use the proper terminal, swage (mechanically compress) it, solder it, and heat shrink it. The heat shrink is not just an insulator. It keeps moisture and oxygen out of your connection, which are both sources of corrosion. *For you ECU guys, the other reason is ground contamination, which is mostly electronic noise and ground loops, both of which upset electronics and can cause all sorts of undesired performance. Another note: if you still have an external voltage regulator (I don’t), be sure to run a #10 wire to the ground point on the regulator. Thumbnails 2-4 show the far end of various grounds.
-
Rationale: When a motor vehicle is designed, a team of engineers is given two lists: one of features and another of constraints. These lists are themselves the product of various committees: marketing, finance, management, R&D, design. It is small wonder that the eventual vehicle is full of compromises, and sometimes downright mistakes. This process is probably necessary when you are planning to sell hundreds of thousands of cars and to try to make a profit in the bargain. Unless you, the buyer, can afford one of those ultra-expensive, production-run-of-100 supercars, your starting place is going to be a mass market vehicle full of compromises. Fortunately, the design-by-committee process produces a real gem every so often, like the early Z cars. This is your starting place. You are only building one car: yours. So you are not required to make any compromises at all, excepting those dictated by your own time, budget, and creativity. The electrical system in the Z cars is a known weakness, and badly in need of upgrading. The electrical may have worked well enough in the cars when they were new, but it did not age well. Most of the compromises you will want to address originally related to money. The copper in wire is expensive, so manufacturers use the fewest wires possible, and in the smallest possible gauges. Upgrading your wiring is relatively inexpensive when you are only building one car; it contributes substantially to the reliability and performance of the vehicle, and does not increase weight enough to make any real difference.
-
Here are some odds and ends worth note... The third brake light is an LED unit, a Hella 9071. If it saves a rearender on Rose's Z, it was worth the trouble. The horns are also Hella. Loud, very loud. The headlights are Hella 7" Euros, with 55/65 xenon bulbs. This pretty much finishes a quick overview of Rose's Ride so far. I have not provided great detail on most of this, because it is all very well detailed in the Hybrid Z archives. Indeed, this is where I did most of the research for this build. In my next series of posts, I will detail some areas which either aren't covered thoroughly in the archives, or for which I have gone a slightly different direction. I will also detail some of the inevitable problems we ran into, and their solutions. Some of this may be useful to others.
-
The thumbnails below show various details of the suspension. The springs are Eibach, the struts/shocks are Tokico, the front sway bar is a 1" MSA, the rear a 7/8". All of the bushings have been replaced with urethane, and all of the usual suspects which are prone to wear have been replaced. Any component which appears grey in the photos has been powder coated. Anything black is POR-15 with the POR gloss topcoat. The front and rear strut bars can be seen in photos above, as well as the roll bar. These components contribute to chassis stiffness.
-
shorting? grounding issues? I SUCK AT ELECTRICALS!
Oddjob replied to reintr0ducing's topic in S30 Series - 240z, 260z, 280z
This is all absolutely correct, and is a possible problem. However, I don't think it is the cause of your problem. Here's why: Your problem occured suddenly, and killed the car. You don't say whether it was day or night, but I assumed it was daytime. If so, the amp draw on your electrical system was minimal (no lights on, and you weren't starting the car). You say the ground cable was melted and broken. I took "broken" to mean burned through. It takes much more amperage to do that than a loose terminal would generate. And lastly, you say the paint was burned. If that happened suddenly, then again, you generated more heat than a loose terminal. My money is on a short.