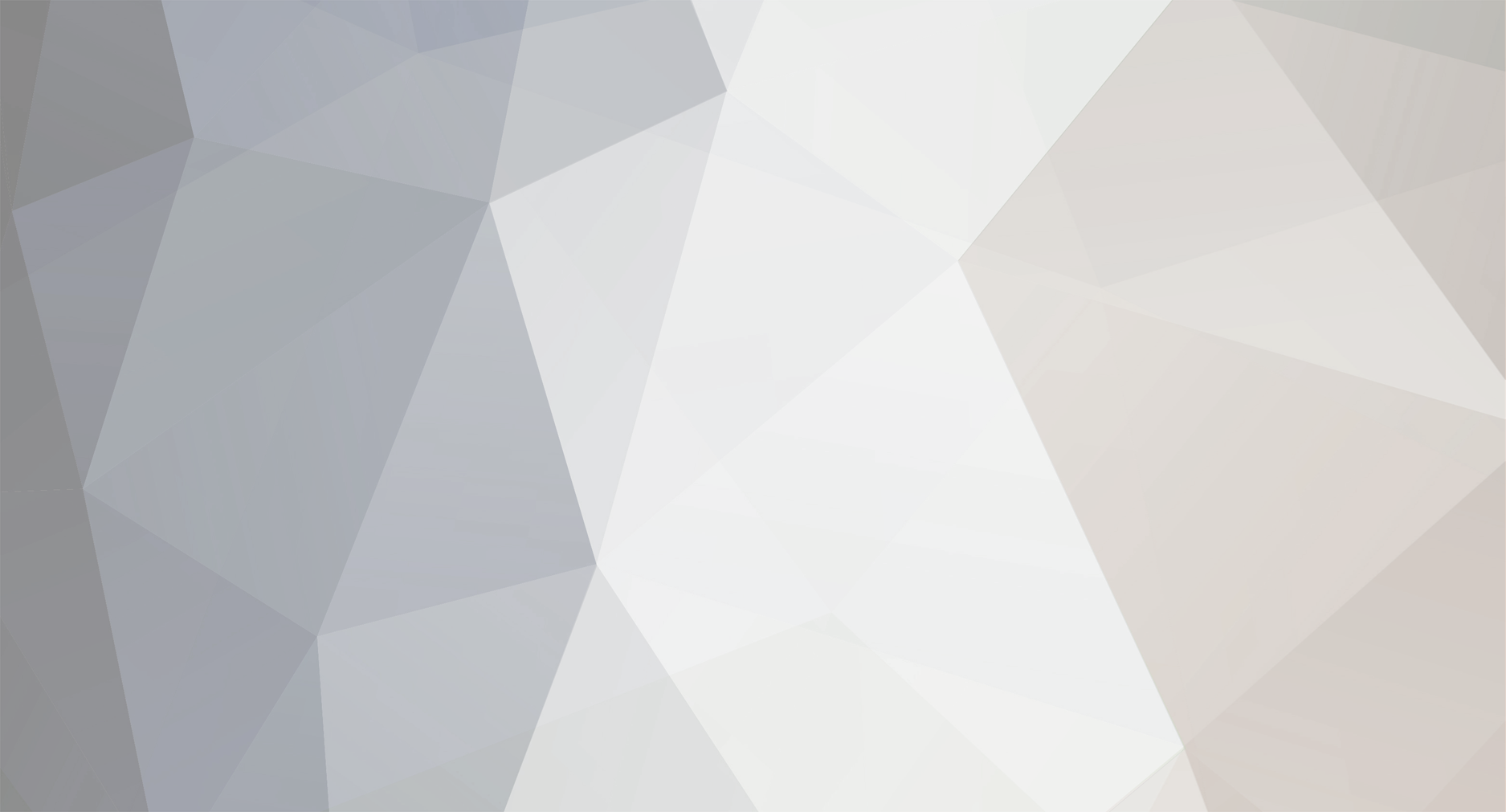
tube80z
-
Posts
1383 -
Joined
-
Last visited
-
Days Won
25
Content Type
Profiles
Forums
Blogs
Events
Gallery
Downloads
Store
Posts posted by tube80z
-
-
I just wanted to say nice work. I totally understand how long this takes and how easy a few pics on the forum make it look. This is a metric shit ton of work.
Hat tip,
Cary
-
There's another really good reason to get the car ready for the upgrade first. And that's by the time you get done with all that work and expense new engines or engine combos may have come onto the market and tempt you. I don't know how many times I have done this backwards only to find by the time I finally can get the engine in there are far better options, which are often cheaper and more powerful. Even if you don't change your mind as the LS platform ages better and better versions will be available.
Just something to think about,
Cary
-
On 3/19/2019 at 8:08 AM, JMortensen said:
You can't get around the limitation of a 1.250" stub axle no matter what CVs you use. IMO you're never going to keep the stub axles from breaking at that power level.
Time for backhalf or an IRS solution that allows for larger diameter stub axles. I'd look to an 8.8 if you want IRS. Might as well upgrade that too while you're in there. The diffs are cheap and readily available, lockers and limited slips galore, wide range of gear ratios, there are very strong CV options for them, etc.I really don't think it would be too hard to create a new rear strut housing using newer car bearings and stub axles. Perhaps something along these lines https://afloresengineering.files.wordpress.com/2014/06/2010-rear-upright-design-report-1-2.pdf.
Cary
-
22 hours ago, rabrooks said:
In essence, it sounds like there is no way to deal with a large scrub radius if you run a wide wheel and tire because it will have to run a high negative offset, driving the large scrub. I hoped to find a way to get a smaller scrub with the wide wheels. The only way I can envision this happening is doing what I mentioned earlier, running a longer LCA and then reducing the negative offset of the wheel. This will lower the scrub and leave the track as wide as it was with the high negative offset wheels. That was why I suggested pushing the top of the strut outward (because the lower ball joint moved out with the LCA). But I would set the camber to what it needed to be, not just shoving the top of the strut over until it hit the end of the camber plate.
That just robs Peter to pay Paul. Reduce scrub and you add steering axis inclination (SIA). It depends a lot on what tires you want to run and how you plan to use the car. With power steering you can increase caster to help cover some of this but you can't go too far. And I suck and have only made it about half the way into trying to make a dual-balljoint front end layout in the suspension software I'm using (Susprog3D). I can move points around but need to have a basic CAD model to make sure they'd actually be doable. For my small 13-inch diameter wheels I think it won't work unless steering lock were severely limited.
-
On 1/1/2019 at 10:58 AM, jhm said:
Also, be advised that if you do decide to replace the stock strut isolators with camber plates, you will not be able to take advantage of the camber adjustment unless you replace the stock-sized springs with smaller diameter springs and top hats as well. The stock springs and top hats interfere with the inner portion of the strut towers and severely limit camber adjustment. (You can achieve roughly the same amount of neg camber by simply slotting the three holes on the strut tower to allow a small inward adjustment of the strut assembly. 2.5" diameter springs are probably one of the most common ID spring used for adjustable coilovers on the S30, but there are certainly many other options to choose from.
And don't forget the trick of taking the isolators apart so you can remove the gap in the rubber to make the top solid rubber. This will reduce the amount of camber loss from the rubber deflecting under cornering and can save you dollars that can be spent elsewhere.
-
There used to be a Z that autoxed with us in central Oregon (Eugene/Bend) that used a circle track system pointing forwards. He had to cut a clearance hole in the strut towers for the primaries to work. He was using a 400 small block versus an LS. We also used to have a Ford GT40 replica that ran a set so I know what you mean about cool sounds. You definitely will want to have good hood ventilation to get both header and radiator heat out of the engine compartment.
The video headers are going to have some problems when it comes to removing or putting them on. There needs to be a sip fit or flange (like your second image) between sides or getting them on and off will involve a lot of effort. If you have studs (a good idea) I'd bet they may not work at all.
If you have access to a 3D printer head to Thingiverse as they have header modelling blocks and LS headpipe (https://www.thingiverse.com/XeonDesigns/designs, https://www.thingiverse.com/thing:2800881).
Hope that helps,
Cary
-
I'm probably just piling on info you already looked at but did you see these, (https://www.hotrod.com/articles/venting-to-cure-crankshaft-pressure/, https://www.yellowbullet.com/forum/showthread.php?t=609182&page=5)? Is that how you plumbed things? I saw a number of people claiming on road race LS motors you need half inch (-8 AN) or larger lines to deal with the problem.
Before I did any of this I'd make sure you don't have excessive blowby/leakdown from a broken ring. I should add that all this disappeared when we dry sumped Kipperman's engine. His locost that had a wet sump LS2 had some vented breathers that ran to a catch can and it was always having some oil mist come out. If you do want to think more about the dry sump I did my complete system using NASCAR take off parts for around $1300.
Cary
-
There's been a lot of good replies to your question of how to build your car. I wanted to share some hindsight from a number of projects I've been involved with over the years. In the end you'll decide if any of this is useful or not.
1. One of the toughest decisions you'll be faced with is do you want a street car that can tracked or a track car that's street legal. Those may sound like the same thing but they are from from it. The first involves adding performance using the Z chassis for the most part similar to the Green Hornet mentioned above. The latter is much more like building a chassis and dropping the Z body onto it. This gets you more to a car like the Fairlady Z06 mentioned above. This also determines if you start with a solid chassis or you use one that's nothing more than the roof and doors.
2. Research, research, research. I'm not trying to be funny but you need to have the entire build plan figured out before you start. Then create a checklist and start crossing of items. This research and list will help you build a budget for the car. It may end up being a lot more expensive than you imagine (nothing wrong there) and you may never want an SO to see this spreadsheet. But if you've done your research and stick to your plan you won't but parts two or three times to get the right item. It will also keep you from having to figure certain things out along the way, which really adds up time wise. And lastly it will keep you from having scope creep. The latter can be a real killer of projects.
3. Determine/buy the drivetrain parts last. This is engine, transmission, wheels & tires, etc. If your project takes more than a year to build it's often possible better items will come along or prices in scrap yards will get better. The only time I'd say you can break this rule is if you have determined their is a specific drivetrain you're going to use and it's not going to get any cheaper and in fact may be harder to get later on down the road (L28ET for instance).
4. For the things you can't do find a good professional that can help you. While it's often tempting to use a buddies buddy or someone doing this from their home I've seen a lot of projects get stalled this way. This is generally around body and pain but could also be around having a roll cage built. For any vendors you plan to use take a look around to make sure they have a good track record.
I wish you luck and good fortune on building your car. In the end there's nothing better than something you built yourself, well at least to me.
Cary
-
1
-
-
On 6/29/2018 at 7:02 AM, jpndave said:
Any suggestions for the "good program" anyone - particularly one that would allow the double joint lower? I've played with the cardstock models that the suspension design references suggest and they help to get an idea of 2 dimensional dinamics but 3d is lacking and changes to pickup points and lengths are tedious. I'd rather not drop thousands on a single car design but would certainly pay a resonable amount.
I'd recommend Susprog3D. It's nothing fancy but gives you all you need to solve the DIY pick-a-part suspension designs. That's what I'm using to see if we can figure out a simple approach to reduce scrub on Jon's car.
Cary
-
This won't be no project Blinky, that much is for sure.
-
That's a really good thread to read through even if you don't decide to go into that depth of detail. It will help make you a much better purchaser of suspension and help with what to ask for. Inverted monotubes are nothing special really. They are just an upside down shock and what looks like the large rod in the top of the strut is really the insert body. Bilstein or a good example of this. They are often used/hacked to create one off setups. There are a number of good threads around using them as a base.
Hope that helps,
Cary
-
Since this is a racing car you should really not be thinking about some off the shelf solution. I would either work with someone who can help you pick a setup for your car based on sprung/unsprung weights and the available grip you expect to have or go through the exercise of calculating that yourself. I would look very hard at inverted monotube designs as they have a much larger shaft to bushing ratio that helps with not only how long things will last but the amount of compliance that you'll see in cornering. You may want to check the rules you race under to see if there are any issues you might run into on that front. Don't get in a rush and end up buying the same thing twice. A little work/research up front will help you save dollars in the long run.
Cary
-
One thing I might suggest. If you look at a new car and compare the chassis to the Z you'll find a connection from the rocker to the frame well in the front wheel well. This is the same area that saw a lot of work in the B&W pictures you linked to previously. And on our race cars we often put tubing into the rockers to make the floor stronger. At the front wheel end this was connected to the TC box. Very similar to some of the photos you have shared.
Props to all the work to save this one. At some point these cars will be rare enough this will be commonplace. I'm glad I live where they don't salt roads.
Hope this helps,
Cary
-
Did you notice this is a ten year old thread?
-
On 12/9/2017 at 3:21 PM, seattlejester said:
The rear one looks to be non adjustable on car as in you would have to remove the spindle bolt to adjust it. Not really a problem once you have the track width set, but if you have to adjust that your alignment guy will be annoyed with you, my guy told me it was kind of a pain to get the tracking just right because you would have to disassemble the strut from the arm and check every half turn.
That could easily be solved with using an oversize bung and adjuster added so you can change length on the car. I never bothered with my set as they were made in a jig matched to the arms that came off the car.
-
Rather than weld the mustache bar to the drop links you can make a new setup that's one piece and bolts in. Here's some pics of what I'd do for the inner frame. While this does use a mustache bar I'd replace that with tubing that connected to the uprights out to the mustache bar outer mounts. Then some simple triangulation would make it very stiff. Rather than use the H style control arm I'd move to one of the toe-link style arms that have been built by a number of people.
In case you're curious these are the rear suspension pics from John Thomas' national championship winning FP car.
Hope you find them inspirational,
Cary
-
My advice, from screwing up this a number of times, is to get the engine and tranny last. You never know how long it will take to complete these projects and what looked awesome now may be a lot less awesome in years to come. Not to mention potentially cheaper.
Cary
-
anyone have experience racing with the billet axles? Did anyone decide to use the 300M for road racing? They're all pretty expensive vs using the 280z with regular inspection. Broke mine at VIR and trying to decide what to put on the car for the next races.
A friend who runs a EP car used the CFR 4 bolt variety and there wasn't any problem. They broke one too and then changed to the CFR part. I put one of them in and they looked nice and used good hardware for the studs.
Cary
-
Sounds like you're well down the road with the Teves unit then. I'll be curious to see how that works with slicks. I was going to suggest another option is the Ford FR500 unit that is programmed for slicks. Install is very similar but Ford motorsport has a much cheaper harness option.
Cary
-
Yeah, photobucket seems to have screwed almost all the car threads and other forums I view. It's understandable but it would have been nice if there was an easy way to migrate but then they couldn't hold people's pictures hostage.
-
I know we all like to fly the Z flag but if you do have to start over a newer platform could be a better move. Not only suspension is better but you get a stiffer chassis often and much better aero. Sure you can get there with a Z but you're going to need to do a lot of work rebuilding much of the car. So my vote from a racing results standpoint would be to look at some other platforms.
Cary
-
The view of the passenger rocker/floor is scary.
Holy fill your pants you're not kidding. Time for a flat floor conversion? Or do you think everything else is too tweaked?
Just happy you're not hurt.
-
Bummer for sure. Glad all the work you put into safety was worth it but too bad it had to get used. From the video it almost looked like the road had a drop going into the corner and compression braking was enough to lose the rear end. And on a hill there's rarely any room for run off.
Cary
-
Talked with Vicky from PTT a few moments ago, she informed me the organic discs are not recommended for anything above 400TQ, my v8 makes almost that in stock form. She did say however that they have a metallic that is much smoother engaging than their competition that they would recommend for dual use on the street for the same price as the organic discs. Vicky also quoted me a blank button 7.25" button for close to $160 and then I can get it drilled to what ever pattern I want locally.
So if I do go their discs are between $250-360 depending on the thickness and number if discs I order and another $160 for a flywheel that I can mount to my stock flexplate. The other nice thing is they actually have the mounting hole dimensions and thickness of their flywheel buttons on the catalogue page so I can mock it up on CAD and see how things should line up.
Their online material (http://www.powertraintech.com/Files/PDFs/Clutch%20Facts.pdf) states 400 TQ per disk. So you may want to verify. That sounds like it might be an okay way to go. My limited experience is that you raise the revs and do a couple quick dips to get the car rolling and then fully engage (pit driving). I think as long as you use the button and the stock flexplate it will be a little better. Mine is a button and ring gear that's mounted to the clutch cover. This is using a low ground clearance bellhousing and reverse starter. If you're planning to ebay a cheap cover I'd go with a Tilton as they had hardened pads for the disks to touch. I have a quartermaster cover and they are just hard anodized from the look of it.
As to how loud they are it's fairly obnoxious when in neutral. It sounds like something is broken or about to fall off. Many of the street dual disk systems employ some kind of strapping between the disks to keep them from rattling back and forth.
Cary
Double adjuster for control arms, where to source?
in Fabrication / Welding
Posted
Not sure if you ever found it but you can buy them from here https://midwestcontrol.com/shop/index.php?route=product/search&search=banl
They are called a barrel adjuster nut or sometimes a barrel bung nut. I use the 3/4 outside thread and 5/8 inner. If you need fine control I'd recommend not a left/right setup but using two different thread pitches.
Hope this helps,
Cary