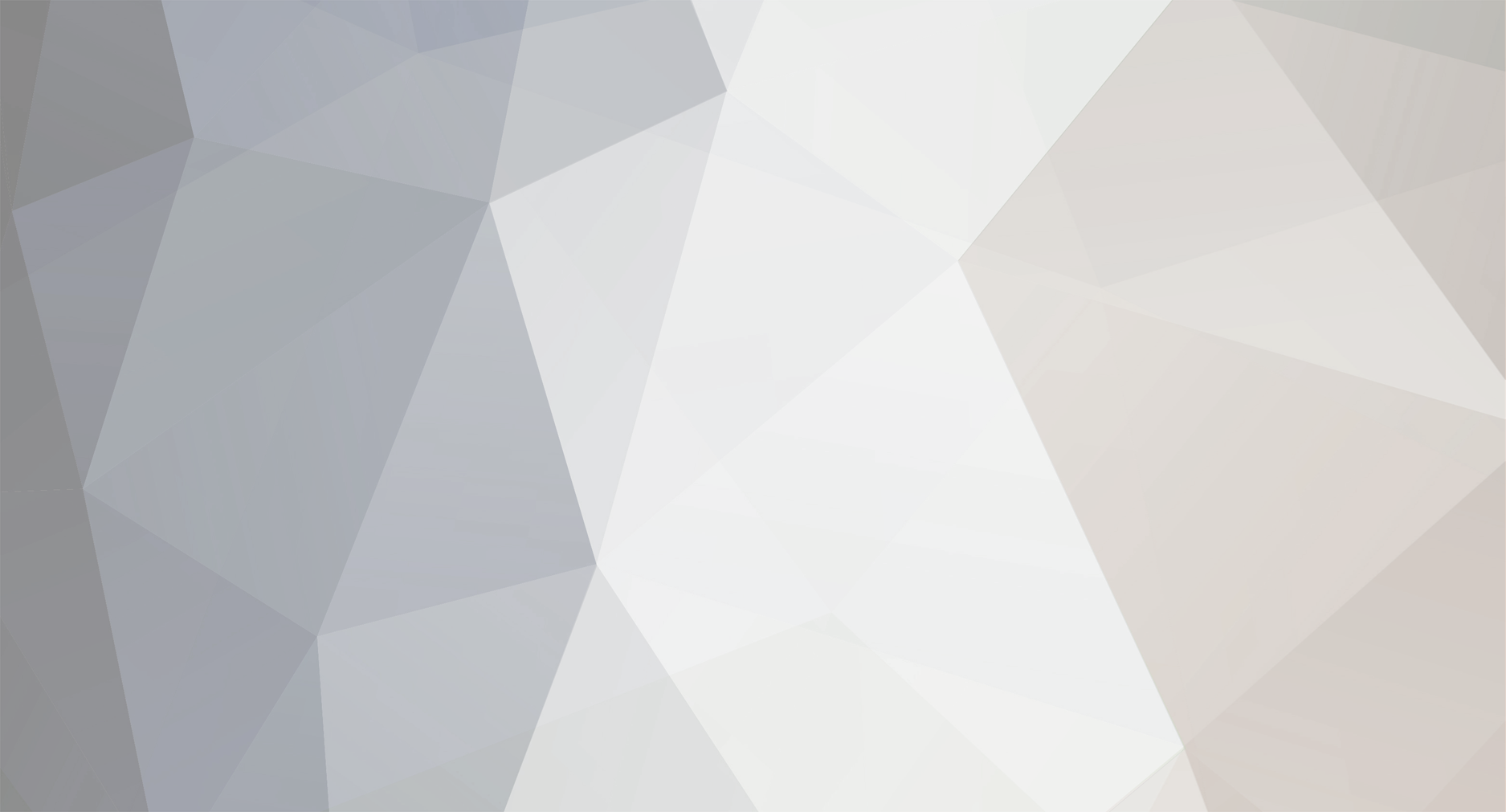
tube80z
Super Moderators-
Posts
1387 -
Joined
-
Last visited
-
Days Won
25
tube80z last won the day on April 1
tube80z had the most liked content!
About tube80z

- Birthday 11/04/1966
Contact Methods
-
Website URL
none
Profile Information
-
Gender
Not Telling
-
Location
Rickreall, Oregon
Recent Profile Visitors
The recent visitors block is disabled and is not being shown to other users.
tube80z's Achievements
-
Wish I could find an intake mani
tube80z replied to Bakerz22's topic in Gen III & IV Chevy V8Z Tech Board
Check Amazon. They have shipped by Amazon for the plastic piece of $115 and free shipping. I know you'll need the rest but this may help. https://www.amazon.com/ACDelco-89018187-Original-Equipment-Manifold/dp/B00S0A2JHY/ref=sr_1_13?crid=AOD5M4YFK7S2&dib=eyJ2IjoiMSJ9.IrazLZcks-CeAYxm7Nnw9H2LntY3DpM73oIQRsYT5Q4kI1yKjso87_ovlL4gKf7IZwTBIOQwjcjoCZ-wm6uIlepFewMz9Ayqdldqr6r87dC5Ehy4pmoQSIDcWD7pFUPZlXwOMxtO4QzB-smVvXAPewzAbfdukibkpMTnaMkrNUtvILiaJONc57aR6maJaoARvNG1cv-nVY5gaN78BHLNFCheIc7_v1jAALZ5NVwAAZU.S7qhbRJHRfu8O6PFfX2faRbbpk6JiNPx6YMpDGWCdPE&dib_tag=se&keywords=chevy+ls1+manifold&qid=1727123364&sprefix=chevy+ls1+manifold%2Caps%2C151&sr=8-13 You can also get the Blazer SS too. Good luck. Cary -
When I need inspiration I check out your thread. Cary
-
You can remove the core support but you'll need to add the structure back for support. If you needed the top out of the way you could make a new core support angled out of the engine bay for clearance. If you have a thicker cooling stack this could be moved out for engine clearance. I've seen a few on race cars where this is removable to make engine changes easier. There's been more of the make the top part of the core support removeable to ease engine changes. The often fall into the turbo DOHC engine swaps if I recall directly. You can do a search here or in Google (or search engine of your choice) and see how people have made this modification. Hope that heklps, Cary
-
240z SCCA vintage race car, restoration
tube80z replied to AydinZ71's topic in S30 Series - 240z, 260z, 280z
Aydin, I didn't mean the adjuster was electronically controlled. Just that with pressure sensors, if you found a sweet spot for brake balance wet or dry you could easily get back to it. Push pedal for 1000 PSI total pressure front to 700 and rear to 300 for a 70/30 split as an example. Easier than needing a helper use a torque wrench on a front or rear wheel to set balance. On the electronic side you could have a channel to send info to a stepper or servo motor connected to the adjuster cable and do fun things like preset pressure by corner or based on weight transfer (light vs, heavy braking). And you could implement the old 90s technology of pendulum brake bias. BMW and Mercedes had systems that used a hanging weight to adjust side to side balance on the front to help with inside wheel lockup. I think if you search groups on FB for E36 Bimmers and the 190 Mercedes they have pictures or video of them working. -
240z SCCA vintage race car, restoration
tube80z replied to AydinZ71's topic in S30 Series - 240z, 260z, 280z
If you have a logger/dash and front and rear brake pressure sensors you can set it by pressure in the pits. Instead of turns. Turns are also hard to keep track of when you come running up to a corner. I have a Tilton pedal set and their bias adjuster already. I'm looking at changing from turns to a linear system of steps to easily change from max front to max rear. I've seen two systems I like. During the Schumacher era at Ferrari they created a stepped system so Michael could change brake bias between corners. Triple Eight racing (V8 Supercars) created a system like an ARB adjuster for their drivers and that's another option. I have had too many runs that rain started falling and I would have loved to be able to change bias and ARBs quickly. I'd like a Bosch motorsports ABS but it's too expensive to justify for me. -
You have packed a lot into your intro. There's some good advice below to consider in the posts to your question. But I have to ask you what is it about the 280 you love? I don't mean that coyly or as some flippant remark. What is it you really like? I'll give you why I like the Zs. I grew up around them when they were new, my uncle was a general manager of a Datsun dealership so we got to try out the new cars. We raced with my uncle at autocross and hillclimbs (I was a kid so I just went along). Back then the Z cars were fast and sounded awesome (I have the hearing loss to prove it), and were amazing at cutting through the corners both stock and modified. Our local racing club had about 10 people driving stock to all-out racing versions. 50 years pass and a lot of that coolness has mostly worn off except for the look of a lowered S30 with an airdam and rear spoiler. I have to admit the sound of a modified Z makes me happy when I hear it. But this site exists to help people get the most out of them. And the reality of that is as cool as the L28 engine is you're looking at spending a lot of money and you'll have an engine that makes 200 to 250 HP. Sure you can get more but then all the other parts that connect to that engine are starting to get pushed past their limits given the age. While I don't disagree with any of the posts below you should still read about a lot of the mods and why they were done. You'll find that in many cases they were driven by it costing too much, parts NLA, etcetera. A bit of advice from me. Never by an engine, transmission, or rear end unless you plan to use it within a few months. Even if you plan to use it that's not the same as ready to bolt in. If you want a street car with a certain coolness and triple Weber carbs, then build it. But when you spend 10K on an engine and find it's somewhat finicky to drive but cool all the same. But for less, you could have 350 HP V6 in the DI Chevy LV3. It won't sound the same as the L-motor but it's lighter, a lot newer, and will get excellent mileage, It will start anywhere if it's hot or cold by the sea or at altitude. This site has a ton of info on how to do the same for the suspension and how to get a cheaper rear diff, especially if you want an LSD. I could write a lot more but this is probably too long as it is. Welcome to Z ownership. Cary
-
240z SCCA vintage race car, restoration
tube80z replied to AydinZ71's topic in S30 Series - 240z, 260z, 280z
Here's the Mustang GT-4 camber plate I mentioned Here's a slightly better picture. You can see they moved the center a bit. You could make something like this but has a square shape or even just a flat edge and easy shim adjustment awaits. I was looking at this for being able to make faster adjustments between runs when testing for autocrossing. Having to jack up the car wasn't going to help make it faster. In some of the events I run, we may get 10 minutes between turns. You need to add in looking at the data to see if it helped if the lap time doesn't seem to show an improvement. I have a long list of items I want in my next car. At the top is a lever adjustable brake bias with presets. So while driving I can change between slow corners and fast corners. Drive adjustable ARBs, and externally adjustable ride height. -
240z SCCA vintage race car, restoration
tube80z replied to AydinZ71's topic in S30 Series - 240z, 260z, 280z
@AydinZ71 I'm not sure that bending the strut will work for Konis as they are generally tight. I've heard rumors but never seen them in person about a certain BMW team that had a jig that mounted in a hydraulic press to bend in some extra camber. Getting the tube out of the is going to be some work but I think that might be the best way to go. Another option would be to build a custom strut and use Nascar hubs 5x5s I think are called. That will help with pad knockback. Another option if you haven't used them is 280Z struts. They are thicker and should flex less. Or you can show up with some DTM inspiration Cary -
240z SCCA vintage race car, restoration
tube80z replied to AydinZ71's topic in S30 Series - 240z, 260z, 280z
It's funny how certain rules are set in stone and others are ignored. You could make a custom camber plate that is mounted to the top of the strut using the tower edges. There would be no more center hole in this design as it would all be covered. If they challenge it you could argue that you wanted to be able to swap springs more quickly out the top. Take a look at rally car service videos and many of those cars come out the top. My personal choice for camber plates would be a square/rectangle design where you can shim for camber or caster/strut angle (rear). Ford has a really cool design I meant to steal but couldn't find it again on their GT4 Mustang. Hope that helps, or inspires some rule bending. -
You can use autotranslate to get a version that will give you the gist of what's being discussed.
-
240z SCCA vintage race car, restoration
tube80z replied to AydinZ71's topic in S30 Series - 240z, 260z, 280z
To be fair to GC the plates aren't intended to be used with that much track increase. You may need to back that off to stay legal in EP rules. I don't have a GCR so I'm not sure what you can or can't do with the shock tower and camber plates. When I widened the front track in my car, I moved the camber plate to almost under the fender mount. I've also used a porta power to add some positive crash damage but that needs to be done before you tie into the roll cage. Cary -
I have a long history with sidedrafts and used to have tons of jets, emulsion tubes, etc. The advantage you'd see on just a 45 mm throttlebody is that you don't have the auxiliary venturi and the chokes. So you'll see more airflow with EFI than with the carbs. Do you need a larger throttlebody is the question? Do you currently see a vacuum in the manifold? If your engine makes over 300 HP then I'd be inclined to look at a 50s or 55s. I'd call Rebello and ask him for a recommendation as he'd know best. Cary
-
240z SCCA vintage race car, restoration
tube80z replied to AydinZ71's topic in S30 Series - 240z, 260z, 280z
Look up used NASCAR parts on eBay for some stuff (window nets, fire suppression, etc.). I'd check local club newsletters for used parts and any of the facebook groups for used racer stuff. But you probably already know all that. And you can ask around at some of the races/track days to see if you can find anything. Cary -
If you want to do a modern flush mount look this is probably what you need to do. I'm half-assing it with a different method for my car, at least at first. And that's gluing the windshield and then using RTV to fill the gap and smoothing it. I saw this back in the 80s and 90s on a few of the IMSA cars. I asked a pit member how they did this and that's what he told me. I'm also thinking about a 3D-printed rain gutter bridge to make air flow down the side of the car better. Cary