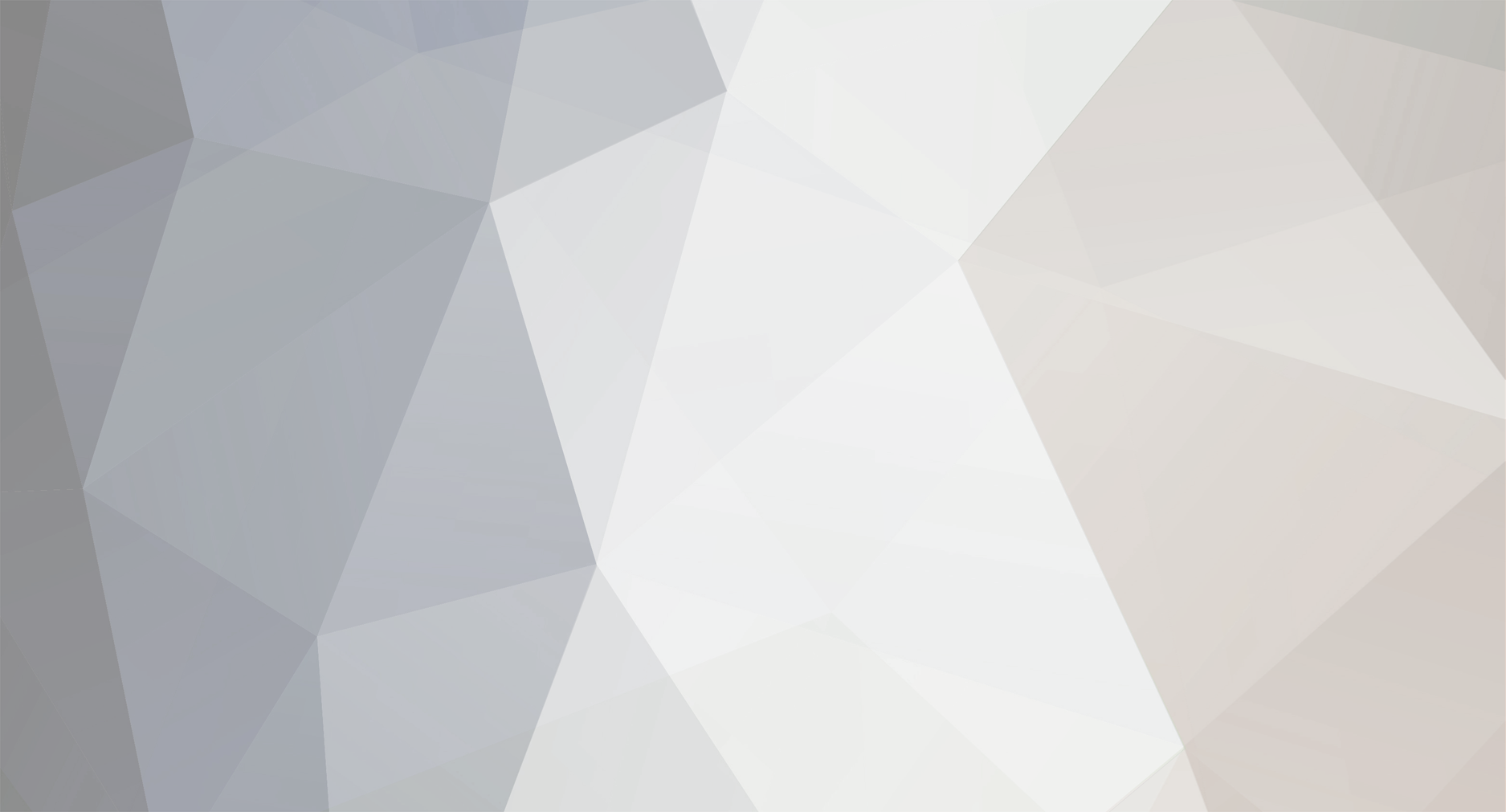
carbuilder723
Members-
Posts
51 -
Joined
-
Last visited
carbuilder723's Achievements
-
td6965 started following carbuilder723
-
BMW S54 into S30 Chassis - Build Thread
carbuilder723 replied to carbuilder723's topic in Other Engines
@Aerodynamic The reason I ended up going with power steering was pretty much only to avoid having to crank on the wheel so hard in the parking lot/ driveway. Also, I have an M3 already and love the steering feel in that car, granted it's is a much more modern suspension design. I also already had the power steering rack sitting on the shelf, so I figured, "why not?". The custom front subframe was a combination of a few factors... mainly I wanted the engine to be down low and as far back as I could reasonably expect. I started by modifying the original subframe, but found as I went deeper into it, that it just wasn't going to allow me to accomplish those two goals, in addition to fitting a power steering rack in also. So, I bit the bullet and just went custom. But don't worry, if you still want to do the engine swap, it is possible to do it with a modified stock cross member. If that's the way you go, I would keep the original steering rack and just position the engine around it. @grannyknothas done a similar swap. Another thread I've used as a huge inspiration is: https://retrorides.proboards.com/thread/139679/bmw-m3-powered-240z -
BMW S54 into S30 Chassis - Build Thread
carbuilder723 replied to carbuilder723's topic in Other Engines
Thanks, I appreciate the complement! My goal is realistically to have a fun street car. But... I do want some key systems to be up to the task of track duty should I want to do that also. (Fuel cell, Recaro seats, harnesses / half cage, lots of cooling for the engine etc...). I do plan on having AC and power steering in the car...the engine and transmission are mounted on OEM BMW rubber isolators, and the exhaust will be relatively tame. I want to be able to comfortably drive it so it will have an interior, albeit not the same as the original. The other thing I've kept in mind a lot is trying to think about the serviceability in the future. I've tried to use parts that should be available for a long time into the future as well as think about the process involved with repairing something should it break down. -
BMW S54 into S30 Chassis - Build Thread
carbuilder723 replied to carbuilder723's topic in Other Engines
Got the frame rails and floor pans completely done! Used the Bad Dog rear frame rail connectors, KF Vintage front frame rails/battery tray / firewall, and Zedd Findings floor pans. Finished up the seat mounts and briefly started to put some of the pieces back together. I included mount points for sub belts in the seat mounts. Next up is the front core support and getting accommodations for all of my cooling needs sorted out. -
BMW S54 into S30 Chassis - Build Thread
carbuilder723 replied to carbuilder723's topic in Other Engines
It's been a while, but a lot has happened in the past year. Not a ton of progress on the car, but enough to warrant a few pictures. On top of everything else, I moved, got engaged and changed jobs. On the car, I just got one of the front frame rails completely replaced, along with the battery tray area and the passenger side firewall. I got the floor reinforcement in and the subframe connector in. I've just started working on the driver side and I expect it to go more quickly now that I know what the process is after learning on the passenger side. -
Reproduction Nissan Fairlady Z432-R works wheels in aluminum
carbuilder723 replied to SeanD's topic in Parts for Sale
potentially very interested in 15x8 +0 if that ever becomes an option -
BMW S54 into S30 Chassis - Build Thread
carbuilder723 replied to carbuilder723's topic in Other Engines
Floor pans are in! Mostly ... They went in pretty well on all but the front edge at the firewall. I had some rust at that seam, so I had to cut the bottom part of that sheet metal out, which I'll have to get back to later. Also the fit between the curve at the rocker and the existing metal was a bit off, but very manageable to massage into place. I butt welded the seam with the transmission tunnel and spot welded everything else (rocker and rear seam), After all of that, I have either one of two paths. I found a little bit of damage to the passenger side forward frame rail, where it looks like the part closest to the firewall was pushed rearward about 1/4 inch or so causing a little wrinkle in the metal. This would basically lend me to replacing the entire front frame rails also, and while I'm in there, it would allow me to get to the battery tray area, and fix the firewall rust... So that may be coming soon, but I may take a break from the sheetmetal / rust restoration side of this for a small bit and work on the seat mounts for the Recaros to give me something a little more "fun". -
BMW S54 into S30 Chassis - Build Thread
carbuilder723 replied to carbuilder723's topic in Other Engines
Holidays are over, some progress has been made. I got the car torn back down to the shell and started working on the rotisserie. I used two Jeg's engine stands which were on sale and about $100 in steel to put this together. All in all, I think it came out pretty good. I can spin it around with one arm. I got the garage all cleaned up, and ready to tackle the floor pan and frame rail replacement. Clean up one mess, before making another one. Also, I finally got my final oil cooler. A CSF 8066, "The Boss" oil cooler. It should be plenty of cooling for any use this car will see. -
Interested. Curious to see what the final pricing comes out to. I definitely need a windshield at some point. Hatch and doors I need to double check condition of what I have.
- 21 replies
-
- windscreen
- tuning
-
(and 2 more)
Tagged with:
-
BMW S54 into S30 Chassis - Build Thread
carbuilder723 replied to carbuilder723's topic in Other Engines
ECU was about $250 for an MSS54HP Software and feature modifications and MAP sensor kit by Kassel Performance was in total about $900 Engine wiring harness was about $150. There are probably a few other small things, but that should get you close. @grannyknot... I should've asked before, but what did you do for radiator hoses? -
BMW S54 into S30 Chassis - Build Thread
carbuilder723 replied to carbuilder723's topic in Other Engines
I'm running a stock, but modified BMW ECU. It's had a lot of the factory BMW features disabled and a custom map uploaded to it to allow it to run as a standalone. -
BMW S54 into S30 Chassis - Build Thread
carbuilder723 replied to carbuilder723's topic in Other Engines
We have touch down. This is the first time the car has been on the ground in about 18 months... I think. It's sitting on all of it's new suspension with the powertrain installed also. Next is going to be building a rotisserie and stripping the car back down to the shell so I can work on the floor pans and a few other body work items. -
BMW S54 into S30 Chassis - Build Thread
carbuilder723 replied to carbuilder723's topic in Other Engines
The AN fittings will have flexible hose between the fittings. I have to try to make sure that there is enough hose to allow the engine to move adequately. I can't argue the cost item though. -20AN fittings are not cheap, but it's a one time expense and it will go better with the whole build in terms of craftsmanship than spliced together rubber hoses would. -
BMW S54 into S30 Chassis - Build Thread
carbuilder723 replied to carbuilder723's topic in Other Engines
2 Months later ..... I've made some good progress, great progress really. I've been able to prototype 3 different revisions of actual engine mounts, and settle on a final version and fabricate them. I 've gotten the steering linkage sorted out, I put the pedal in for the first time with their lines connected to the bulkhead, and I got the engine wiring installed (very temporarily) and actually started it up for the first time in the car, with the whole drivetrain connected. So, engine mounts first. 3D printer was working overtime again going a few different versions. I ended up straying away from the idea of welding to the frame of the car in favor of going with a solution more like what Nissan had originally done. I welded some support stand offs from my custom subframe to come up to meet the engine side supports and rubber isolators. I just couldn't bring myself to weld to the front frame rails and lose the ability to drop the engine out the bottom of the car. Next, since most of this custom subframe and engine mount work was to manage to get my BMW steering rack into the best position, I had to figure out how to actually connect the Datsun column to that BMW rack. It turns out that the BMW rag joint has a nearly identical bolt pattern as the original Datsun one, so that let me just take apart the BMW one and use half of it to adapt the Datsun column down to a 3/4" DD shaft. Then I found a collapsible DD shaft online (3/4" on one side, 1" on the other) that I used to connect from the steering column, to a Flaming River universal joint that has a 1" DD on one side and the BMW spline pattern on the other. I also am using a poly version of the original Datsun steering column coupler. Result?? The steering feels absolutely perfect... 0 slop from the wheel all the way down through to the tires. https://youtu.be/18_B0R0pzEc Once all of the engine mounts were fabricated, and the engine was finally sitting in its final position, I decided it was time to get it running... I dug out my box of wiring from the engine stand and started hooking it up. I put the dash in since it had all of my gauges and switches now and hooked those up too. This was also a good opportunity to try out the new in tank fuel pump set up. (much improved in terms of the noise vs the externally mounted Boash 044) I filled up the coolant, topped off the oil put in a few gallons of 93 and gave it a try. First go, it didn't quite want to take, but I think there was just a bunch of air in the fuel rail. After a few more cranks, it came to life. Good stuff! https://youtu.be/hwrzxf-Cf7w https://youtu.be/JXuYEDszmUA https://youtu.be/KQYHxMbQgWU A few things coming up next... I made the decision to go with AN fittings for the radiator hoses, for a few reasons. 1) I'm kinda opposed to having to splice together a bunch of rubber hoses to get the shape I need. 2) Flexible radiator hoses aren't the aesthetic i'm going for. 3) despite is being a tough pill to swallow now $$ wise, it will make future trouble shooting or even modifications easier to adapt to a new set up if needed. I'm probably going to leave the engine in for a bit longer, give it some run time since it hasn't seen much since last August (2019) and try to get a few things sorted out like coolant overflow tank location, oil cooler location, and maybe a few more plumbing things. Then it's back down to a bare shell to make a rotisserie and get those floors and frame rails replaced. -
BMW S54 into S30 Chassis - Build Thread
carbuilder723 replied to carbuilder723's topic in Other Engines
Sub-frame is done... at least it's all tacked together. And wow, not to pat myself on the back or anything, but I am thrilled with the way it came out. It couldn't be packaged any better in my opinion given the placement I want for the engine. I checked the bump steer again, and now instead of my laser drawing a horizontal line when going through the wheel travel, it makes a much more suitable vertical line with an acceptable amount of variation. There are some small adjustments I could do down the road to make it even better on the pitman arm / tie rod side of things, but this is going to be it for now. We'll see how it drives and go from there. Onward to engine mounts... after some thought I think I'm going to try to a bit of a hybrid approach from what I was originally thinking. I'll get some more pics up, but basically, I'm thinking i'll incorporate the passenger side engine mount with this sub-frame and the driver side engine mount will be on the front frame rail. I think it's going to work better given the steering column placement and the environment. More to come -
BMW S54 into S30 Chassis - Build Thread
carbuilder723 replied to carbuilder723's topic in Other Engines
Back again. Couple more updates. I got the driveshaft adapter back from my machine shop. and it fits like a glove between the BMW CV joint and the r200 input flange. I guess my measurements were pretty good and their machine work was top notch. I also went ahead and got the tires mounted onto my wheels and tossed them on for a brief test fit. Granted there's no sub-frame in the car to hold the wheel in place very much, but just hanging there, it's looking pretty good to get away with out any fender flares. In front sub-frame news, I think I have all the pieces I need to finally get this thing completed. I have the tube bent, the steering rack mounts plasma cut and the end brackets all laser cut. I used a new company for the laser cut parts this go around due to availability of my original source. OshCut is the name of the company I used this time and I was very happy with their whole process and at the end of the day their pricing was reasonable. It pays to have them cut multiples of what you need the first time, since it turned out that 2 sets of parts only cost about $15 more than a single set and the first set cost $80. Anyway, I just need a solid day to trim the tube, finish welding up the end brackets and the steering rack mounts and I should have a functional front subframe. Then to readdress the engine mounts. I'm not sure if i'll use the frame mounted ones I already designed or if there is a way to potentially integrate them into my new subframe. 1 step at a time...