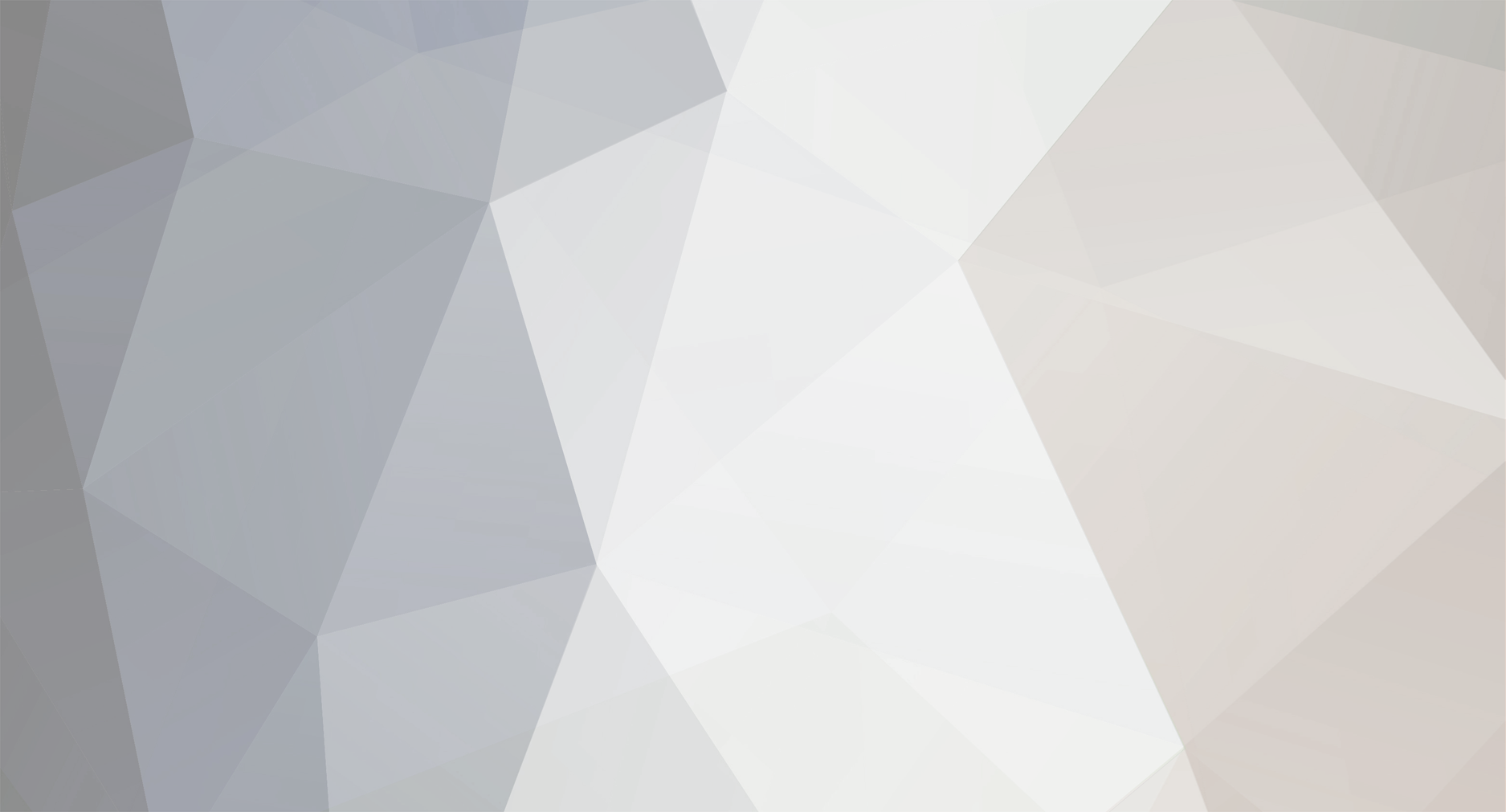
zuhow
Members-
Posts
38 -
Joined
-
Last visited
-
Days Won
1
Content Type
Profiles
Forums
Blogs
Events
Gallery
Downloads
Store
Everything posted by zuhow
-
No, this is wrong. In a sealed vessel, the density is constant. INDEPENDENT of temperature and pressure. it's SEALED, so no mass goes in or out, and the volume remains constant (i assume you meant a ridig vessel) so the density, which is mass/volume is constant because the mass and volume are constant. boost pressure has nothing whatsoever to do with flow through an orifice. flow through an orifice is an EXPANSION process Volumetric effiency is a totally different beast. I agree that, in practice, doubling the boost pressure doesnt double the mass flow of air, but that's a fine point that isn't really important. if you double the density (however you do it) you WILL double the mass flow for a give volumetric flow rate. If you're flowing 500cfm and the denisty is 0.08 lb/ft^3 and you change to a density of 0.16lb/ft^3 and keep the flow of 500cfm, you will flow twice as many lbs of air.
-
So I've been following this thread and I've gotta make a couple of comments: Pyros formula is a good formula, if used correctly. I think we're trying to take it beyond it's limits here though. I use it frequently. It IS a really good SWAG (Scientific Wild A$$ Guess) if you dont strech it too far. Basically, it works damn good if you only project a little ways from your starting point. Look at it this way, say my house was worth $100k last year and $150k this year. I can project that my house will be worth (150/100)*150=225K. probably pretty good guesstimate. The problem comes if you try to strech this 30 or 40 years out- you'll see my house is now (projected) to be worth more than the output of many nations!!! That's whats going on here. Bastaad, you were right on the money when you guessed a turbo w/o the turbo would put out about 100hp. If you take "the formula" and apply it in reverse (ie divide by the ratio of pressures instead of multiply) you'll come up with 98whp (at the wheels). check it out: assume 145 whp for l28t bone stock the ratio is (14.7+7)/14.7=1.48 so 145/1.48=98hp still following me? good, now the problem comes when you say I'm gonna put 20 psi boost on this engine: ratio= 14.7+20/14.7=2.36 2.36*98 (base l28T "naked" power output)=231whp I agreee this number is low, as evidenced by Bastaads hard data of 240ish hp at 14psi. That said, this formula is great if you say "i've got a a given engine and I want to estimate the power output if I turbo it (a little bit)" (you have to assume here that you dont change anything, leave the CR, cam lift timing, etc the same) You can say, which is Pyro's point- and he's totally right, that if I double the air mass flow (ie 15 psi boost, or 2x the density of normal atmosphere) I can expect (about) twice the power output. Just keep in mind that you're now projecting "years" ahead like in the house example and it's bound to be off quite a bit. If you stick to "just a little bit" around your starting point, you're good to go. But it's just a SWAG, not any sort of gospel truth or theoretical limit. It's just a simple way of saying, "if I consume 20% more air I'll get about 20% more power" which is totally legimate. Just remeber, all bets are off when you start talking about 'large' changes....... Oh, and Bastaad, thanks for keeping my math skills sharp, you always give me something to crunch over a bit (but my employer is pissed that you're killing my productivity!)
-
Simply: "buy the best- cry once" You will never regret having extra capacity. Make sure you check the rating, you are NOT getting a 5 hp compressor that plugs into 120V AC, no matter what that label says. Figure somewhere between 3 and 5 cfm per horsepower for air at 100psi.
-
I'd say Kenny gave you good advice, but make you best estimate and multiply by 3 not 1.5. You need to decide now if you want to turbo it or not. If you want to turbo it, and you're going with the stroker crank be prepared to spend some serious cash. Personally, thats what I wanted to do, but I couldn't find a LD crank for a good price and decided that that money would be better spent on turbo and fuel upgrades. You will need to look into better valve springs, check out Top End Performance, they sell a real nice engine rebuild package. You can chose the bore/ stroke/CR for whatever you happen to want. $1900 for just about everything (parts only). Ask yourself why you want to increase the rev limit. The loads on parts go up really fast as you spin it faster, you'll have to pay for that strength. Don't worry about forged rods, the stockers are good, just have them balanced and polished.
-
Bastaad I've got to spend a little more time at work today since I left early the last two days and I'm putting that to use for you, plus I'm dying to see what happens: let's call your bhp 240 ponies (at the wheels) you're using stock injectors right? those are 265cc or 25.2lb/h (so says that great turbo link that I dont feel like looking up the address to put in here, but you all know it) Ok, on to the meat of it: 25.2 lb/h * 6 injectors is 151.2 lb/h ----this is 100% duty cycle *more on this later 151.2 * 0.9 = 138.1 lb/h ---90% DC 151.2 * 0.8 = 121 lb/h ----80%DC if we take: (121 lb/h) /(240 bhp) =0.50 BSFC * at 80%DC (138.1)/ (240) = 0.58 at 90% (151.2)/ (240) = 0.63 at 100% *so which number is it? You're using the RRFPR correct? Any idea what pressure it's going to? If you (or someone else) can give me an estimate of that it would help. You're clearly flowing more fuel than the 80% duty cycle at stock fuel pressure. How much more, I've got no idea. Hopefully you or someone else here (there's a lot of guys smarter than me here, come on, I know one of you knows this...) can give us a better idea You're certainly in the ballpark of 0.6 BSFC, give or take. We need a little more data to really nail it down. Do you have any way to "borrow" or otherwise appropriate an ocilliscope and find out just how long those injectors are open and tell me what fuel pressure you're running at peakpower? My gut tells me you're probably pushing 10-15% more fuel because of the RRFPR and operating at about 80-90% duty cycle. that's pure speculation, mind you. in that case you be looking at a BSFC of about: (121 * 1.1 ) [10% more fuel flow] / (240) = 0.55 on the low end (80% DC) (138 * 1.15) [15% more fuel] / (240) = 0.66 on the high end (90% DC) so it seems 0.6 BSFC is a good number to use for the L28ET
-
BrandonsZ, I think you're right on . I was thinking more along the forced induction lines. As we all know, getting more fuel into the engine is the easy part, it's getting more air into the engine that's the trick. I guess you'd have to know what kind of flow you were getting on the NA set up (either carb or FI) but you should be able to SWAG (Scientific Wild A** Guess) that. Or as you say, 'empirical data' sounds better that way..... I'm really interested to see what Bastaad comes up with ( if you get screwy numbers because of the units let me know if I can help you out) . I'm guessing that he'll come up over 0.55 but i dunno, let's see!
-
The final question from me then, is a turbo-motor specific one. As I have said, I have seen it mentioned on these boards (I believe quoted directly from Corky Bell's Maximum Boost book) that the ideal BSFC for a turbo engine was 0.55. That wasn't my number I didn't even know what BSFC was. Just to be clear: The ideal BSFC of ANY engine is 0.00 In that case your engine would make power without consuming any fuel!!! A lower BSCF is always better because you use less fuel. But my question is, what air/fuel ratio would that BSFC roughly equate to? YOU CAN’T GET THERE FROM HERE BROTHER! (I hope that doens’t come out wrong,- I’m not shouting at you….) If I am putting out 300 flywheel HP at a BSFC of 0.55, how much fuel am I using (in lb/hr or cc per min), how much air by volume, and what would that make air/fuel wise? I’ll cut you some slack, but you should plug the 0.55 into the calcs I laid out for you, and you’d see that with 300 hp and 0.55 BSFC you’d need about 165lb/h. You then have to DECIDE what A/F you WANT and then calculate the amount of air mass flow to reach it. I’m thinking you’re not quite understanding the brake part of BSFC. It takes into account all the losses, so asking about what’s going on at the flywheel makes me thing you’re still a little unclear. Maybe I’m not so good at explaining the concept…. There is no ‘backward’ connection from BSFC to A/F, but there is a connection ‘forward’ from the A/F to the BSFC. You CAN’T determine the A/F from the BSFC, but the A/F is part of what goes into measuring the BSFC
-
You don’t calculate BSFC-you measure it. It is what actually happens as opposed to what the math and engineering say should happen. BSFC is simply how many lb/h of fuel flow you need to make 1 bhp. If you are running very rich you will have a higher BSFC then if you are running an ideal A/F ratio. Work it this way then- just for the sake of argument assume you’ve measured 400 bhp at the wheels and you’ve measured that your 55lb/h injectors are running at 80% duty cycle there. Ok 55lb/h * 80%*6 injectors gives 264lb/h In this case the BSFC is (264/400) =0.66 That’s how one gets the BSFC, and it will vary between 2 cars running the same set up (granted, it won’t vary much). And it will naturally vary between different setups. So then you can work this in reverse, but you have to estimate the BSFC. You can use 0.55 if it makes you happy, but the reality of it is that our estimates are really guesstimates and 0.5 is as good as 0.55 is as good as 0.6, I’d err on the side of caution myself, and stick with 0.6 or higher. All that will happen in that case is that you may over size your injectors a little bit. So assume BSFC is 0.6 Calculate the required fuel flow rate for a desired power output- say 300bhp Fuel mass flow rate= (BSFC) * (BHP) =(0.6 lb/h*bhp) * (300bhp) =180 lb/h of fuel flow (divided by 6 injectors gives 30 lb/hr) don’t forget to factor in duty cycle: that 30lb/h is required, so you would need a bigger injector (30/0.8= 37.5lb/h or more would be a good choice) now decide on your A/F, lets call it 10.5 calculate the air mass flow rate 10.5=(A lb/h air flow)/(180 lb/h fuel flow) 10.5=(A)/(180) A= 1890 lb/h airflow ( call it 14ft^3/lb dry air and you get about 440cfm at atmospheric pressure) Like wise you could use 12 And you would come up with 2160lb/h BSFC isn’t some thing you really have direct control over, it’s just a very quick and dirty measure of efficiency, basically you take the final net power output (after all losses in the drivetrain and whatnot) and simply divide the fuel mass flow rate by that number to get BSFC. Don’t get hung up on this number, but you can use it to guesstimate component performance requirements for fuel and air delivery. Or you can use it to guesstimate max power output Assume a NA setup with a head that can flow 250cfm (pulled this number from my arse) 250 cfm is about 18lb/ min or 1070 lb/h so for a 11:1 A/F you would need 97lb/h of fuel (divided by 6 gives 16lb/h per injector) and you would expect a power output on the order of (again assume BSFC of 0.6) Fuel mass flow rate/ (BSFC) = (BHP) (97/0.6)= 160 bhp
-
The performance characteristics of an internal combustion engine can be reported with or without the effect of power reducing friction and other losses. A value of a property (power, fuel consumption, etc) that includes the effect of losses is know as a brake value. (If the effect of losses is removed it’s know as indicated value). The specific fuel consumption is the fuel usage rate divided by the power generated. Typical units are lbm/h*hp (pounds per hour-horsepower) or kg/kWh (kilograms per kilowatt-hour). The term specific refers to a quantity that is referenced to mass. i.e specific volume would be cubic feet per pound and specific energy would be Btu per pound It’s probably best to think about BSFC along the lines of wheel fuel consumption. Note that lower values of BSFC are better. The air/fuel ratio is the ratio of air mass that enters the engine to the mass of consumed fuel. You’re right that the 2 can be directly linked, but not really usefully. If you know the brake hp and you know the fuel mass flow rate (in lbm/h) you can calculate the BSFC: Fuel mass flow rate= (BSFC) * (BHP) And if you know the (desired) A/F ratio, you can calculate how much air flow you need. Likewise if you estimate the BSFC and you know how much wheel power you want you can calculate the required fuel mass flow required and then the air mass flow required for your desired A/F ratio. But you wont get an A/F from the BSFC. A quick search turns up a range of values for BSFC between 0.4 and 0.6 with 0.5 being a good general number.
-
jmortensen: UNITS my friend, units. that source quotes per gallon (volume) what matters is mass (per pound)., some data: diesel #1 19,240 BTU/lbm 133,332 BTU/gal specific gravity (weight relative to an equal volume of water) 0.876 gasoline 20,260 BTU/lbm 116,485BTU/gal spec grav 0.68-.74 so while it's true a gallon of diesel has more energy than a gallon of gas, it doesnt matter. what matters is how much energy you get from combining it with oxygen (air) and that take place on a per mass basis (actually on a molar basis- so many atoms fuel to so many atoms O2). Diesel is just denser. if you go by a per volume basis you would believe that diesel has more energy than acetylene, but if you've ever used a blow torch (and I'm sure you have) you can clearly see it's not the case. acetylene is a lot less dense than diesel (because it's a gas) but it burns like a mother#$^*& Beware power is not the same as effiency. Yes a diesel engine is more effiecient, but less powerful. The diesel is more effiecient because of the higher pressures involved. the effieciency of any internal combustion engine (either spark ignition or compression ignition ,ie diesel) is directly related to the compression ratio, higher compression ratio= more efficient. compare an L28 to an LD28 land you'll see what I mean LD28 ~90Hp and ~150 lb-ft (source: http://retro.co.za/lr/tech/engines.html) L28 ~150hp and ~160 lb-ft L28T ~180hp and ~200 lb-ft (source: http://zhome.com/History/zcarperf.html) we're saying the same thing on the compression issue, I think. I love this site! diesels make torque, not power Chewievette. Whens the last time you saw a dump truck tear *** away from a steet light? They just pull hard and never stop!
-
This is wrong. Diesel has 19,200 BTU/lb and gasoline has 21,000 BTU/lb. A diesel engine will make less power for a given displacement than a gas engine of the same displacement. You need a higher compression ratio to get deisel to burn because you aren't using a spark, just the heat of compression of the air, in essence a diesel engine runs on detonation! The deisel makes so much torque because of the increased cylinder pressure. The torque an engine makes is directly related to the cylinder pressure, more pressure= more torque- that's why a turbo engine makes more torque than a NA engine. You should start with the LD block and all its parts. Dont even think of trying to use the L series aluminum cylinder head on an L series diesel, they wont last too long. I'm confused as to why you would want to do this. If you just want to tinker with something I can understand. Seems to me your gonna spend a lot of time, money, and effort on building yourself a headache. But don't let me dissuade you. I'd go down to the barnes and noble or borders and read the chapter (ch9) on internal combustion engines in "Mark's Standard Handbook for Mechanical Engineers" the book is pricey (like $150) and will be largely useless to buy, so just go read the chapter. Good luck! keep us posted on how it works out for you!
-
I've got a basket case and I need some help to sort out what goes where. What pieces-parts go under the fenders on the 280? Basically, my problem is that this was all taken apart many years ago- life got in the way between then and now - and I don't remember what goes back in there. Anything in addition to the plastic splash guards? If someone has some pictures or even a sketch it would help. I have the microfiche but it's not real clear.... it shows what looks to be some stamped metal parts, but I'm thinking those are part of the fender itself, correct? Can anyone help me sort this out? Thanks
-
I saw the panda wheels in Tire Rack ad once. You may want to give them a call and see.
-
As I learn more, more questions present themselves...
zuhow replied to a topic in Turbo / Supercharger
Moby has it mostly right. Let’s look at it this way: your engine doesn’t store any energy, so the energy in (fuel) has to equal the energy out. Now what is the energy out? Well, it is the work done to turn the crankshaft and all the accessories- water pump, AC compressor and so forth- and the heat that is sent out of the tail pipe. The work done on the accessories is indeed a parasitic loss. Adiabatic is a whole ‘nother can of worms. I think you understand it right, you just have the terminology wrong. Adiabatic losses are losses due to heat transfer, basically (gross oversimplification here!) all the heat that goes out of the radiator (and oil cooler) are adiabatic losses. Adiabatic losses are loses due undesired heat transfer, instead of heating the engine block, that energy, in principle could be used to do work- ie turn the crank and put a smile on your face! Inefficiencies in the compressor are called isentropic losses. Basically you can never operate at 100% efficiency, so you don’t get the actual compression (in psi) out of the compressor that the math (and engineering) says you should, hence you get a 70% efficiency on the compressor as you mentioned. Clear as mud? I hope so! So, the blower you mentioned, and I’m assuming it’s a roots type blower, does indeed operate around 50% isentropic efficiency. The other 50% of that efficiency goes into making heat, not compressing the air. These blowers are what are called “positive displacement†a compressor like the one on the turbo is a “centrifugal†compressor. These are much more efficient- typically 70-80%. Still with me? So, you can have a centrifugal compressor driven by a belt- like a vortech super charger, or by a turbo. This brings us back to the energy in= energy out. The reason a turbocharged engine is more efficient is because it manages to pick up some of the energy that normally would be lost in the heat in the exhaust gas and use it to drive a compressor. A belt driven supercharger, sucks up some of the work that otherwise would go to the crank to drive the compressor. FYI, power plants do the same thing we do to our engines. A large natural gas fired turbine power plant will take the exhaust gas and use it to make steam to drive a second turbine to scavenge some of the energy and boost the overall efficiency, not exactly turbocharged, but I think you get the drift. Sorry for the long post, hope this helps clear it up for you. If not, by all means, ask away. I’ve been a long time lurker, and I’ve learned tons, so I’d love to be able to give some back. -
Newbie to hybridz here! My $0.02: I would look for the P79 head and get rid of those hydraulic lifters. Have the rotating assembly balanced and polished. Forget coating the maifold. While I too crave a set of forged pistons, unless you're looking for crazy boost, stick with the stock (but I will say, if you've got the ca$h, go for the forged and O ring the head, that way you can run easy 20+ psi boost- but you'll need alot more upgrades to get there) Leave the stock crank alone, spend your money on a programable fuel injection system instead, you'll be glad you did. Forget about the port work on the head, that turbo will stuff more than enough air in the engine, spend the effort you would on the port work on a better exhaust sytem. flame on!