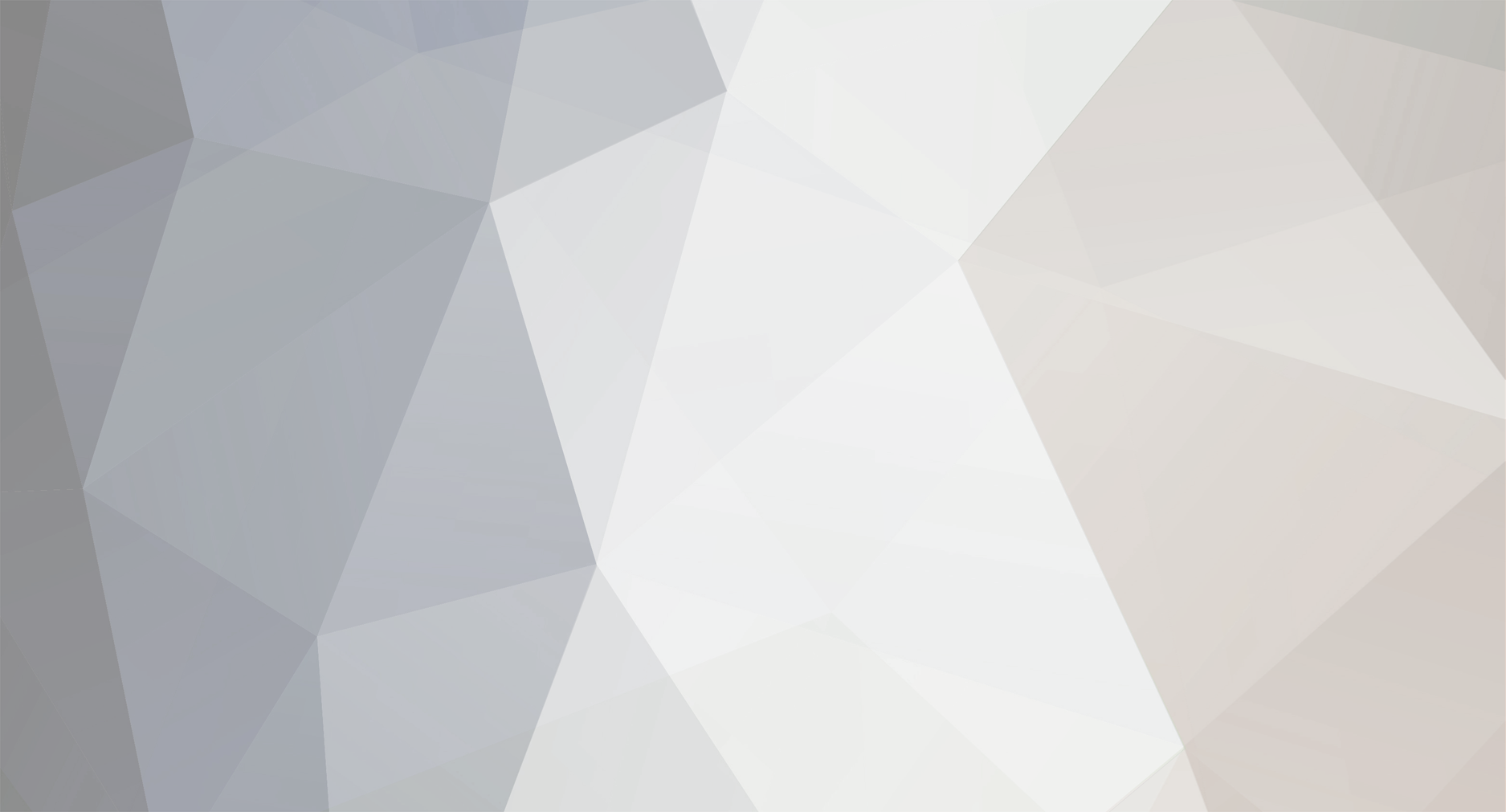
jakeshoe
Members-
Posts
258 -
Joined
-
Last visited
Content Type
Profiles
Forums
Blogs
Events
Gallery
Downloads
Store
Everything posted by jakeshoe
-
Mike, No issues with shift timing changing over time, it would take a significant change in the operating clearances (band and 3rd clutch) to cause a change in the shifting. The clutches would be worn beyond use to create this amount of clearance. These clearances do affect initial setup, as the band clearance could vary widely but any good builder will set band clearance within a reasonable spec. Band clearance has a greater effect because the 2nd gear servo acts as the 3rd gear accumulator. The band has to be "kicked off" by 3rd gear feed oil. So the oil has to simultaneously force the servo to the "off" position and feed the direct drum. The tighter the band clearance, the less movement the servo is capable of, so less oil it will consume to release it on a 2-3 shift. Less oil consumed by the servo = more oil goes to the directs, which makes a quicker apply.
-
The problem with most "local" shops is that they are in business to do stock rebuilds. The more they do the more $ they bring in. You'll also expereince the same (maybe even more so) with a delaership trans guy, very good at replacing parts, rebuilding stuff, but knows nothing about improving the stock transmission. I can tell you now, most local shops will not even touch a 200-4R for performance work because they believe in the old wives tale that they are junk. Not only that but they will have no idea about how to make it live under power. The dual feed technique I discussed is really only used in the performance world for the 2004-R and most builders would likely not know how to do it. If they knew how to do it, they would then probably pull there hair out trying to figure out why the transmission had a bind-up on the 2-3 shift after rebuild. Using this method to feed the direct (3rd) clutches causes them to come on more efficiently. A little theory for you, On both the 700-R4 and the 200-4R, the 2nd gear band must release, and the 3rd gear clutches must come on. This is unlike a TH350 or TH400 where the 2nd clutches stay engaged and the 3rd gear clutch then "stack shift" on top of them. No matter what you do on a TH350 or 400 to speed the 3rd gear shift, it isn't an issue, because there isn't any real timing involving releasing another element. The 200 and 700 shift has to be timed, so that the band releases as the 3rd clutches apply. If the 2nd band releases too soon then the transmission will have a "flair" which will feel like it is slipping, however it is actually a momentary return to 1st gear. There should be an overlap between the band releasing and the 3rd cltuches applying, so that you get a clean shift. If this overlap becomes to great, the trans is effectively in two gears at once. 2nd and 3rd. It acts somewhat like a trans-brake. In severe case you will actually be able to hear and feel the motor lug on the shift. If the car is on a lift you will see the tires stop, as the shift takes place. This causes extreme stress on the friction elements as they work against each other, and this is why the forward drum must be the billet unit for a dual fed 200-4R. To make a firm shift you will have just enough overlap so that moment of release of the band coincides with the moment of lockup of the 3rd clutches. There will be a bit of crossover that will strain the forward drum at WOT shifts. It will snap the stock drum. It is an easily corrected problem on the 200-4R, the band release orifice has to be properly sized so that the band releases quicker. However you often have to start from a known point and drop the pan a couple of times to get it perfect. Most local shops aren't going to understand this and won't mess with it. Chris at CKPerformance in car tests each unit before it leaves. So warranty issues should be few as long as the installer gets the geometry setup correctly for the TV cable. MIke Kurtz is well known as a 200-4R builder and will know these things. There are really only a couple of handfuls of decent 200-4R builders and that's the issue with using this transmission. Most shops have done THOUSANDS of 700's so are more comfortable doing them, but you will find that many offer no warranty for a performance unit.
-
Mike, The main weakness in the 200-4R for high performance use is the forward drum. Keep in mind the GN's used these transmissions and they put out quite a bit of torque stock in a moderately heavy platform. The forward drum is about $400 by itself for a billet shaft type unit. This is the main expsense. The other issue that has to be addressed is servo size. The stock 86-87 GN's has a decent servo size but the best answer is to use the Superior or Sonnax servo which is a $100 item. Other than these issues, you can do some minor upgrades internally (stuff that should be done even on a stock rebuild) and the 200 is a fairly tough unit. I was running one behind the 427 BBC in my '69 Chevelle. The same trans will likely make its way into the Z project soon. The 200 needs: Alto Red frictions in the direct drum Improved forward drum Larger servo Alto Red Eagle 2nd band 3 clutch overdrive setup (simple procedure to add an extra clutch, this alone really firms up the OD shift) Dual feeding the direct clutches (simple mod but requires the improved forward drum to prevent breakage, this firms up the 2-3 shift, makes a huge difference in the liveability of the directs, same mod is done on almost all performance TH350 and 400's...) A 10 or 13 vane pump setup with chromoly rings (parts are the same as 700) Larger boost valves (same parts as a 700) Valve body mods (TransGo kit works with some mods) Hardened sun shell and stator (necessary on stock rebuild, later models already had this) Both parts cost less than $30 total. If you wanted a 200, Mike Kurtz is again a respected vendor for these units. he can make recommendations as to what he thinks will work. Chris at CKPerformance is also well known for his 200-4R's. He makes the billet forward drums that I use when I build them. I would probably suggest using his shift kit over anybody's. He KNOWs the hydraulics on these trannies.
-
Mike, 400Hp/TQ is about where I believe the limit is on a 700 to live "reliably". By reliably I mean without issue and not rebuilding it every year. Also not worrying about WHEN (not IF) the input shaft/drum or 3-4 clutches are going to quit. That said, the 400 Hp/Tq range should be reliable especially in a lightweight Z car. Your only issue will be the use of nitrous. When you add a 100 HP shot of nitrous you boost the TQ much more than 100 lb/ft. So now instead of a 400 lb/ft torque launch, your leaving with 600+ probably. The weight of the Z car may let you get by with this, or the weakness of the 700 make cause failure. To build one fairly stout I would recommend you use: 10 or 13 vane pump setup with (TransGo) chromoly pump rings. Raybestos Z-pack for the 3-4 clutches. Alto Red Eagle band for the 2-4 band. Beast Sun shell. 093 (Vette) servo. TransGo reprogramming kit. Large boost valves. Otherwise mostly stock stuff and good rebuild technique. Mike Kurtz of Century Trans is in the Houston area and could probably do you well. Also of note, a 200-4R will fit easier into the chassis with no driveshaft mods, only moving the crossmember would be required (and TV setup). You would probably spend slightly more to do a 200-4R right, but would save some of it on driveshaft mods. The 700's deep first gear and your rear ratio will make for a hard to hook combo. The 200 has a better gear spread.
-
I LIKE to stay at less than .040" overbore, and in your case, you need to find a STD block to salvage your pistons. I have run them at .060" and IMO the cyl wall thickness isn't the problem at .060" it's the head gasket sealing on a stock block. .180" cylinder wall thickness minimum on the thrust side.
-
I would shop for a different OEM block. You asked about a medium heat street engine, so I'm guessing a sub 6500 rpm N/A platform, probably around 450 HP? If so any of the blocks will work for you. Even the "weak" 817. Have it thoroughly checked, and for machining I would have it line honed as needed, decked, bored and honed with torque plates (absolutely necessary on a 400), and otherwise nothing fancy. You could have a partial fill done about halfway to the water pump holes to make the cylinders more rigid.
-
The problem here is he has purchased a block that already has a cracked cylinder. Not a good idea to sleeve a 400 for reasons I mentioned.
-
I've built quite a few 400 based engines. The 509 block IS the best block. It has CONSIDERABLY more material along the main webbing and pan rail than an 817. On a 400 based block the index of the main caps is as large as a regular 4 bolt SBC whether or not it has 4 bolts, the 4 bolts actually take material out of the main webbing and weaken it. I don't have any bare blocks laying around at the moment or I would post pics of the wbbing differences. The 511 is not quite the same as the 509 but does have more meat than the 817. That said, I've built some 817 blocks that were abused I would not sleeve a 400 block for performance use. IF you do decide to do so be aware that the adjacent cylinders must be bored because the siamese cylinder configuration, and the press fit of the sleeve will distort neighboring bores out of round (alot). As much of a fan as I am of low budget/ OEM parts builds, this is one place where the money invested in an aftermarket block is worth it. The average price of a guaranteed 400 SBC core block now that will machine to .040" or less is ~$200-up, usually around $300. Figure $250 for a block, $80 decking, $125 for bore and torque plate hone, $50 clean, $80 sonic test, $50 R&R cam bearings and block plugs, $100 for block-fill and labor, plus labor and parts to plug deck holes (should be done to firm up deck), align hone if needed ($70-100), etc.. That's about $900 pretty quick, and it will never have as good of ring seal as a Dart (preferred) or World block.
-
-
One thing to watch put for when measuring crank journals is taper from the center to the sides or across the journal. You can end up right on in one area and too big or too small just across the journal if it wasn't set up properly on the crank grinder.
-
-
I know of one guy who was running King bearings, had an issue with an oil pump or shaft during staging on a 10 second SBC powered car (383, Chevy II). He made the pass anyway, loaded the car. tore engine down to find he did in fact have an issue, the crank polished after making a pass with no oil pressure. Bearings were toast but they did what they advertise. King bearings are Israeli manufactured and are a good quality part. IMO bearings are not used to "polish" a crank, nor should you be running dirty oil. Type of bearing material depends on application, some specific applications will need more embedability, others may need a very hard bearing due to the very high oil pressures needed to keep the engine together.
-
King bearings are excellent quality. Some builders prefer them over the Clevite... I've had excellent luck with them.
-
Yes, Starter bolts do matter. Until you get a proper bolt it will continue to move around. The correct bolts are knurled and maintain a large diameter approx 1/4-3/8" into the block. Look at the bolt holes in the block, they are counterbored for the correct bolts. If you use the wrong bolts, you will eventually break one in the block, and possibly break the ear off the block.
-
getting the valve train geometry correct
jakeshoe replied to grumpyvette's topic in Gen I & II Chevy V8 Tech Board
Bill, I use a solid in place of a hydraulic even if the motor will use hydraulics. The hyd will compress to the end of the plunger and mess with the readings. If you have a way to setup a dial indicator or a pair of calipers to measure and make sure the pushrod cup is in the same location that is good to check. Remember the hydraulic plunger will compress when adjusted, depending on how much you adjust it. On a performance motor I usually go about 1/8-1/4 turn on a hydraulic after it quits clacking on a running adjustment, and right at 1/4 turn on a static adjustment on the stand. 1 complete turn on a 3/8-24 stud is about .042" of plunger travel. If you use a hydraulic lifter specifically made for it, you can keep it at the very top of the plunger almost against the keeper, and it prevents hydraulic pump up at high rpms. -
getting the valve train geometry correct
jakeshoe replied to grumpyvette's topic in Gen I & II Chevy V8 Tech Board
Well the earlier photos I thought you were using a different rocker. Check the geometry with the rocker you are using now (roller) set at 7.800, and be sure the rocker isn't rubbing against the rocker stud. The first photo shows a very wide pattern, that gets too close to the rocker stud side of the valve. The wide pattern may be because you used a stock type rocker and not that the actual motion is that far... The photo with the 7.850 shows a narrower mark which is good, but it is offset too far towards the exhaust side of the head. Ideally you want a nice narrow range of travel across the top of the valve, but very slightly off centered towards the intake side of the head. So that at the widest part of it's travel it comes to center. -
getting the valve train geometry correct
jakeshoe replied to grumpyvette's topic in Gen I & II Chevy V8 Tech Board
And those pics are after rolling the motor through a revolution? It's a LITTLE too far to the outside of the valve actually indicating the pushrods are a bit long. Try it at 7.800 on the adjustable pushrod and see if you can pull it back on the valve a bit. Couple of things to watch for with roller rockers, be sure they aren't touching the retainers, and often the bottom of the rocker will rub the hex portion (or its radius transition) of the rocker stud on a SBC and it will skew the geometry test. -
should you buy a custom designed cam?
jakeshoe replied to grumpyvette's topic in Gen I & II Chevy V8 Tech Board
Another tibit of information, Comp does NOT make cam cores. There are 3 major cam core companies that everyone buys cores from. Cam cores are hardened before grinding by the core manufacturer in most cases (as far as I know except for the OEM rollers made from 8620 material IIRC). Some of the problems in the last few years have been core related, some have been quality control related, some have been lifter related, and some I believe to be cam companies getting a little too aggressive with their flat tappet profiles. -
getting the valve train geometry correct
jakeshoe replied to grumpyvette's topic in Gen I & II Chevy V8 Tech Board
The roller rockers will show up on the valve fine, very clear... -
should you buy a custom designed cam?
jakeshoe replied to grumpyvette's topic in Gen I & II Chevy V8 Tech Board
Just a bit of information... There is nothing wrong with a properly done regrind.. A reground core can save you money and in some cases is as good as or better than a new core. A reground core, especially for about any American V8 is not going to be "welded up" it will be from a good used core that lasted many thousands of miles. That tells you it is properly hardened... On a motor with an adjustable valvetrain, I will select a regrind for most flat tappet builds for that reason. If you need a small base circle cam for a stroker motor, guess what, you may as well get a regrind, because the smaller base circle is oftentimes the same blank as a stock size base circle but ground down further. I've ran literally hundreds of regrinds in my own and customers motors and never had any issue. How many can say they have had a flattened lobe on a new cam...? -
should you buy a custom designed cam?
jakeshoe replied to grumpyvette's topic in Gen I & II Chevy V8 Tech Board
A "custom" cam usually consists of a regular shelf stock lobe configuration but with a different LSA or a split pattern that isn't available stock. It's not that anybody is designing a specific lobe for you, just using what's already there. I almost always select a "custom" grind based on the engine and intended usage. The cost is usually minimally more (if any) than a shelf grind. Often there are other reasons to use a custom grind, as in the case of the austempered iron CAST cams used by Comp and others now for a street roller. My advice is to NOT use this type of core. Call and order the grind you want on a billet core, and if used on the street get it with a cast dist gear pressed on the back so you can run a conventional distributor gear. I personally use http://www.deltacam.com for most of my stuff. They can grind on a new or used core about any profile you need. Many of their lobe masters are Comp Cams masters, so you can get a "Comp" cam with better quality control for cheaper. -
getting the valve train geometry correct
jakeshoe replied to grumpyvette's topic in Gen I & II Chevy V8 Tech Board
Bill, Go back and re-read what I posted about the plastic checker.... It is marginal at best... First you need to figure out what your bind was. Did the engine rotate OK with just the lower end assembled? Now that you have the heads on and are checking it could be a piston to valve clearance issue, retainer to guide, valve spring coil bind, rocker to retainer issue, etc. Better sort that out first. What is your combo? -
getting the valve train geometry correct
jakeshoe replied to grumpyvette's topic in Gen I & II Chevy V8 Tech Board
Grumpy is correct it is easier to just purchase than build unless you need one in short order or for an odd length. -
getting the valve train geometry correct
jakeshoe replied to grumpyvette's topic in Gen I & II Chevy V8 Tech Board
I haven't used a welder, I have drilled the inside of the pushrod slightly and threaded it and used a small diameter stud. The jam nuts are to lock the final setting. -
getting the valve train geometry correct
jakeshoe replied to grumpyvette's topic in Gen I & II Chevy V8 Tech Board
Dr. Hunt... You are absolutely correct... This is why I stated in my post that the best method to check the geometry was to use an adjustable pushrod. I'm just a fairly experienced mechanic and machinist, not a high speed engineer type but I would be willing to bet that they teach "minimizing variables". If you are not using the components you intend to use on the engine as assembled, you are wasting your time to check the geometry. The little plastic checkers cannot accurately determine the geometry when you are eliminating one of the key components, the rocker arm. A stock pushrod cut and threaded in such a way as to be able to adjust ( not necessarily centered), a small stud with 2 properly sized jam nuts will accurately check the pushrod lengths on many combo's... much more useful and likely cheaper than the plastic tool pictured.