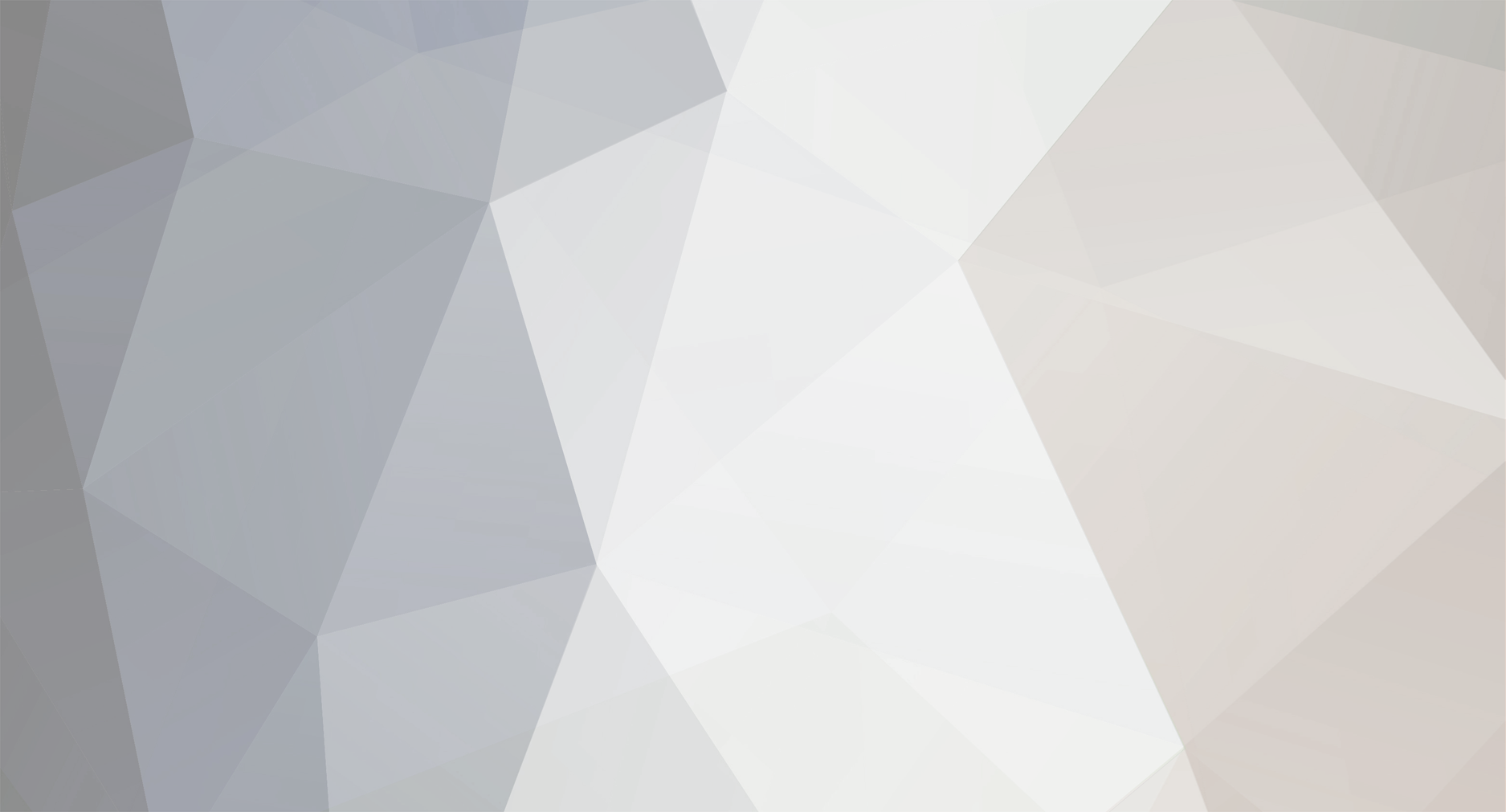
X64v
Members-
Posts
543 -
Joined
-
Last visited
-
Days Won
1
Content Type
Profiles
Forums
Blogs
Events
Gallery
Downloads
Store
Everything posted by X64v
-
Thanks. The port above #5 will be routed back to the water pump inlet, in the same manner as the original bypass line for the SU/TB water. This will provide a great pressure difference and pull lots of water out from #5. The port above #6 will be routed up to the lower thermostat housing, via a new tap, or perhaps I'll tee into my GM coolant temp sensor fitting. This will pull water out from #6, but not as much, because the pressure difference will not be as great. That help?
-
They were tempting, but based on this photo, I thought the casting mark looked far too high to me, and I was worried about hitting the top wall of the water runner and/or hitting the casting bump in the top of the water runner in that picture. What did you say they were, chill pads? My roommate and I were wondering exactly what they were.
-
I did my drilling and tapping tonight. Super easy with a drill press. I'm glad this head will be hot tanked at the machine shop, there are shavings everywhere. (Yes, it's a P-79, leave me alone) Note: In the cut-away pictures, the top of the #5 exhaust runner casting is about where the top of the machined gasket area is around the port. Well, looking through my new water holes, the #6 exhaust runner casting comes up 1/8" - 3/16" higher; my port is just above the floor of the water passage in that area. Just beware, don't make the bottom of the hole on #6 any lower than mine is.
-
Same here, I really like the stuff. I like the earl's hose ends better, but the aeroquip and earl's hose have both served me well. Nice build, it's a monster for sure.
-
There's a core plug in the back of the cylinder head. Could you just pop that out, thread the hole, and screw in a custom T-stat housing? Then, make a simple block-off plate for the original T-stat housing location. My only question then would be, would the #1 chamber get enough water flow, or would we create a problem there?
-
A while back I came up with the idea of using the built-in tranny cooler in my JTR radiator as an oil cooler for my turbo oil feed line. This would help keep the turbo a little cooler and reduce the necessary cool-down time as well as the chance of coking up the turbo. I was talking with a friend who thought tranny coolers weren't meant to take much oil pressure, but wasn't sure. My question is: Does anyone know if the built-in tranny cooler in the JTR radiator can withstand 70-80 psi oil pressure? Also, does anyone know the size of the fittings on that cooler? They're definitely inverted flare fittings, but I can't find the thread size online.
-
I haven't updated this in a while. My biggest change has been my fueling system. I got rid of my 338cc barbed injectors for some 400cc o-ring injectors fed via a new pallnet fuel rail. The last picture of the old setup The new hardware Installed These injectors are a million times quieter than the others I had in before. I'm pretty sure it's because these are high-z injectors, while my old ones were low-z, so these don't snap open as hard. Also, I LOVE the Pallnet rail. Beautifully machined, top quality mounting hardware, and it sealed perfectly on the first try, no leaks, no resealing. It was worth every penny I paid and every minute I waited while it was on order. A piece of advice on seals: unless you have them already, just spend the $20 on his hybrid seal kit (if that's what you need). I needed the hybrid kit (14mm o-ring uppers, and stock datsun lowers), and it took me a few days, trips to three different parts stores, an online order, and over $20 to put them together. $20 seems a lot for the seals, but I would have saved money on gas and shipping if I would have bought his hybrid kit in the first place. When I order the -AN fittings for my cylinder head coolant rerouting stuff, I'll order -AN fittings for the fuel rail as well. I'm bring a P-79 back down from Phoenix tomorrow, which I'll be rebuilding, probably sending the cam out for a regrind, and modifying the coolant flow. I'll have pictures of the bypass ports for the #5 and #6 cylinders pretty soon here. It's going to be a pretty cool little modification. I'll detail the theory behind it a little more as I actually do it. Also, I've pretty much quelled my pinging problem by switching back to a 160 degree T-stat and pulling a little more timing. When I get the P-79 head on, we'll see what it does as far as ping. A random picture of three Datsuns in the bays. Front to back: My 240, a kick ass 510 with a KA24de, and speedgato's 240.
-
This is not what I'm talking about. I still have my heater core, so this line is staying in place for me. I'm talking about the internal passage between the block and the head in the very back, the one big enough to fit a few fingers in when the head is off. That's close enough to where we'll be tapping #6 that I would be worried that our tapped port would just draw lots of water from there if it were returned to the pump inlet. Routing #6 to the lower T-stat housing instead would reduce the pressure differential pushing the water, thereby keeping the flow through our #6 port within reasonable limits. I think your setup you just described sounds perfect, and I'm wondering if I should make mine exactly like yours (sans water-cooled turbo) instead of the way I was going to do it a few posts up (post #138).
-
Ah, gotcha. Yeah, that makes sense when you think of it that way. The -AN line will have less friction and restriction than going through the rest of the head, so it will flow through that instead. I think in my case, I'm still going to return both to the water pump inlet, since my single -6 line will total the same water flow as the original bypass system. In your case, you already have one -6 going back to the pump inlet, so the other needs to go through the radiator instead of being bypassed. Unless I should route mine like yours? Two separate lines, #5 back to the pump inlet, and #6 to the lower T-stat housing? This would make sense if one takes into account that #6 has that giant water port from the back of the block into the head there, so perhaps a line going from there to the water pump inlet might impart too much bypassed flow?
-
If I had (or when I get) a water-cooled turbo, that's what I'd do. Then return #6 straight to the pump inlet. I'm bringing my next head back from Phoenix tomorrow, so I'll start on this and have pictures probably Monday or Tuesday.
-
Nothing, but the fact that Tony D gets so worked up about it is entertaining. Edit: I've been thinking about what size to make those taps, taking into consideration total external bypass flow relative to stock, ease of plumbing, and of course cost of -AN fittings. I think I've come to a good compromise for myself: 1/4" NPT ports above #5 and #6, -6 lines coming off each one into a -6 tee, with a -6 line from the tee back into the water pump inlet. This way, the total flow of the ports above #5 and #6 would equal the capacity of a single -6 line, which is about the same capacity as the original bypass circuit from the lower T-stat housing (which I've had blocked for some time now). Therefore, I would not need to upgrade my water pump, as no more water would be bypassed than stock (a single -6 line is 9.525mm, stock is what, 10mm?). Thoughts on this?
-
We had one come through the shop today. Remembering this thread, I snapped a picture on my phone. The runners appear to be equal length.
-
The Dynomax turbo muffler is most definitely not a straight through. It'll be quite a bit quieter than a straight through muffler, which doesn't matter much on a turbo motor, but is important on an N/A. A straight through muffler on an N/A motor will definitely be loud (perhaps so much as to be illegal, which may be why MSA uses the turbo muffler in their kits).
-
:lmao: Quote of the day, right there. I'm getting ready to rebuild another cylinder head to put on my turbo motor, and am thinking very seriously about tapping 5 and 6 above their exhaust ports and returning both to the pump inlet, giving steam pockets a good place to go just as Tony D said. What does everyone think about the size these lines should be? I will be plumbing in AN line, but obviously a restrictor can be made to any proper size. Also, what about tapping #4 as well? On lots of blown head gasket pics where 5 is blown and 6 is way out of round, I see 4 is quite out of round as well, much more so than 1, 2, and 3. Would it also be worth the little extra effort to tap #4 as well, perhaps one size smaller? I think you're on the right track with #6, as it would be flowing fairly freely back to the pump inlet. As for routing #5 to the lower thermostat housing, I think that's not the greatest idea. While there would be a difference in pressure, the difference would not be very great, yielding less flow. Returning #5 back to the pump inlet as well would flow a lot more water (more on par with what the #6 tap would flow).
-
Alright, thanks guys. I know tons of the rc parts are anodized, but I never knew they were hard anodized.
-
Just how incompatible are methanol and aluminum? All the searching I can do on the net says that methanol will slowly eat away at aluminum (unless it's hard-anodized), but in the Nitro R/C world, aluminum is used in fuel systems all the time (fuel filter bodies, carbs, engine blocks, etc.), and Nitro R/C fuel is 60%-70% methanol. I have R/C carbs and fuel tanks and the like that I've used for years and the aluminum looks fine. I ask because plumbing a water/meth injection system would be a lot more inexpensive if one could use normal aluminum AN fittings instead of hard-anodized or SS fittings.
-
Autometers are 50 bucks. Not saying don't use the Neon gauge, but the name brand gauges aren't as much as you think.
-
What's everyone doing for the memorial day weekend?
X64v replied to dr_hunt's topic in Non Tech Board
I'm gonna go see some friends that just graduated from High School in Phoenix, and bring back another cylinder head for my turbo motor. -
I've got it close. I backed off the timing a few more degrees (loaded up the spark map I was running with the L24), and switched back to a 160* thermostat. Switching the thermostat helped the most. Now it will ping a single time in first (just once, every time), and then three or four times in second. I can't get out of second in town so I don't know what it will do in the higher gears yet, but so far it's much better. I still don't understand why this motor with lower compression is pinging more than the higher comp motor with all the same settings. Perhaps the E88 head just doesn't like the 86mm bore for some reason? I'm just about to call it good and throw on a meth injection kit I've been putting together. Edit in response to KTM's post: Yeah, timing is now back to ~24* at 7psi. When I originally started to try to deal with this, it would ping all the way back to 20*, where I had zero power, so pulling timing 'til the pinging stopped was not an option. And I did blow a head gasket when it knocked majorly, the light ping just won't do it on its own.
-
The whole cooling system is pressurized equally by the thermal expansion of the water (with that pressure being the radiator cap rating). Add in the water pump flow being restricted by the thermostat, and that means the pressure in the block/head should always be higher than in the radiator.
-
I don't quite think so. There is also an internal bypass in the engine block. It's not impossible, but I don't think it's likely.
-
Alright, this weekend I swapped in a set of 400cc injectors that are known to be good. Ping is still there, not changed at all. I'm 100% out of ideas. In the interest of full disclosure, I've had to re-tune with the new injectors (switched from low-z to high-z which messed with everything just a tad), so my tune isn't dead-nuts on like it was before, BUT the leanest AFR I see at WOT from onset of boost is 12.0:1, which quickly tapers down to the low 11s, so that should not be responsible for the pinging at all. Any last ideas?
-
Why would you inject an inert gas to cool the intake charge, when you can inject water/meth to cool the intake charge, reduce combustion temps, AND add fuel? Doesn't make sense to me.
-
That's what I was thinking, that depending on the injector design, the fuel pressure would either help or hinder pintle movement. And ah, I missed the section of the megamanual saying that that was their definition of opening time, which would certainly explain the differences in that number vs. z-ya's actual opening time. I do know the formula megasquirt uses to calculate pulsewidth makes all of this make sense though: Pulsewidth = (Req. Fuel)(VE)(MAP)(Enrichments)+(Accel)+(Inj. Opening Time)
-
I left the PWM settings alone. I use Z-ya's recommended settings for my injectors (1.4ms time threshold, 30% limit), and they seem to work very well. Yes, I have an innovate LC-1. That's how I came up with the .7ms opening time. At idle with the 1ms opening time, it'd go from 12.3:1 afr at two squirts to ~18:1 at one squirt. At idle with the .7ms opening time, the difference between one and two squirts is only about .1-.2. Switching between one squirt and two is how I came across this in the first place. I switched from two squirts simultaneous to two squirts alternating, which is only one squirt per bank per cycle, and then my afr's went to hell. So yes, that makes sense. The time between voltage start and coil saturation may be 1ms, but the time between voltage start and fuel flow is about .72ms. I'm guessing this number would also be at least slightly dependent on fuel pressure, but I'm not positive.