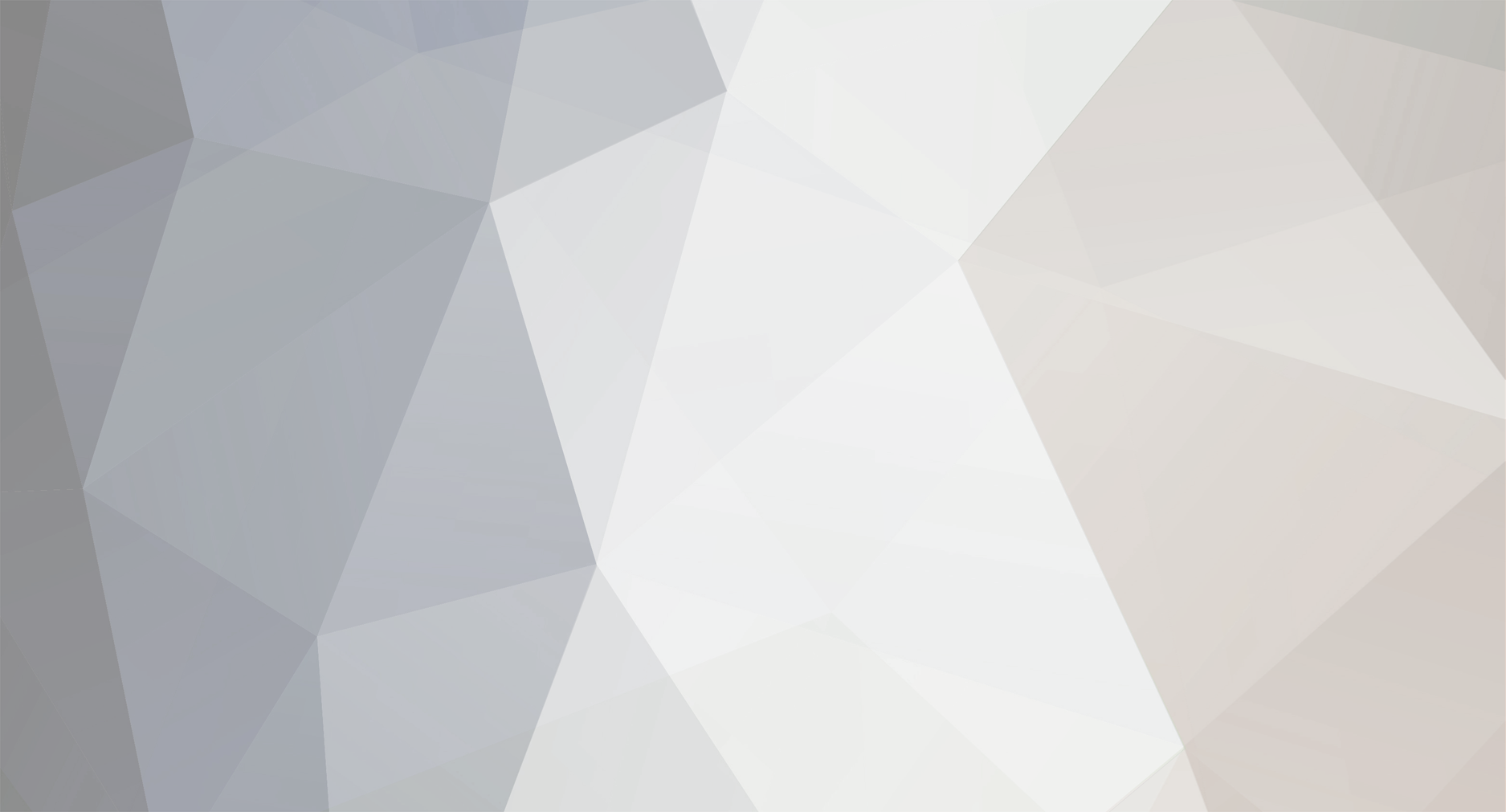
rsicard
-
Posts
889 -
Joined
-
Last visited
Content Type
Profiles
Forums
Blogs
Events
Gallery
Downloads
Store
Posts posted by rsicard
-
-
I have been there and done that. Do not buy a prewired universal kit. Get the wire fuse box seporate. This way you can get the correct length of wire were it needs to go with out splicing. I bought the 18 circuit kit from painless. You don't need that many circuits. I mounted the fuse pannel on the passenger side firewall. I used the original connectors. I will send some photos this weekend. Also go to ebay and get the color wire diagram 11X17 cant tell you how much that helped. My 1970 240Z has been on the road for 3 years with no electrical problems. I also converted to single wire alternator. This was the first time I have ever wired a car. So if you know a little about wiring it can be done.
With the Painless kit, what was done with the turn signal, high/low beam, headlight, wiper and washer switches stalks on the steering column? I am faced with fixing up the wiring on my 71 240Z. After studying the wiring diagrams the fixup solution is not all that bad. Purchased a separate fuse panel which will be positioned where the original is but has a better capacity. Also want to update running and turn signal lamps to LED types and the turn signal and emergency flasher need to be replaced with modern types to handle the LED bulbs. Designed a rewire of the headlight circuits to add relays to take the heavy current off the stalk switches which fixes the design deficiency of the original circuits. The same needs to be done in the ignition key on circuit by adding another relay.
-
Not trying to ruffle any feathers guys, sorry about that. I think gollum laid out all of the advantages and disadvantages, it just seems to me that when designing a compact motorcycle enigne, I would have used a more modern engine as the template, but that's just my opinion. Sorry.
More modern engines have 4 valves per cylinder, dual overhead camshafts, dual camshaft CHAIN drives. The pushrod engines have LESS parts to FAIL! Latest state of the art Corvette cylinder heads are VERY if not more efficient than any other cylinder head on the market by any manufacturer. Displacement for displacement, blown or Un-blown, the pushrod engines makes the same or more power and just as or more efficient than the overhead cam engines with LESS PARTS to fail.
Don't understand peoples thinking about modern engines.
-
The C channel raised part of the crossmember has been cut and the plan is to weld the tube to it and the bottom of the crossmember. Sounds like it's going to be too far back though. I could start over with the other crossmember and move the rack forward again. A 1" change in the rack position forward really won't change steering angles much at all and would actually be 1/8" forward from stock. The problem is that the center tube on this rack is a lot thicker than the Datsun part, so I'll probably be RIGHT UP against the firewall if I do that. I guess the other option is cutting the firewall to clear the head. If you cut (or hammered) yours just enough to move the engine back 1" from where it currently sits, would you have to modify both sides, or just one? Can I get a pic of the firewall where the interference would likely be?
Thanks.
How much of the "C" channel portion of the cross-member had to be cut to the rear of the member to fit the square mounting tube? The "C" section of the cross-member is spot welded at the factory to a formed and stamped plate which has a flange at the forward and rear portion of the cross-member. Would the mounting of the rack come out too far forward if the square tube was welded directly to the forward flange of an unmodified cross-member? Just wondering. Please advise. Thanks.
-
I made some progress and actually got the rack into the position the old rack was in after I moved it back, but now I'm at a point where I am a little worried about the position of the rack vs the crank pulley. I'm not using John's Cars mounts, but my main concern is whether I will be able to move the motor far enough back for the crank pulley to clear. I was planning on setting the motor back as far as possible, but I'm not sure how much room I have to work with. The top of the rack is exactly 1.5" taller than the crossmember with it sitting on 1/4" bumpsteer spacers. It will actually be 1/8" lower than that, so figure a total height from the crossmember to the top of the rack of 1 3/8". The stock crossmember has a raised section that is 2" wide from front to back. The rear part of my rack is 2 1/8" from the back of the raised portion of the rack.
In retrospect, the engine mount towers really did need to come off, so that wasn't wasted motion...
Jon:
Trying to visualize what you are talking and showing in the photos. The cross-member is made up of a "C" channel and contoured flat plate spot welded together. Does the 1.5" square tub get welded to the forward portion of the bottom flange of the cross-member? If not, how does the square tube attach to the cross-member? Please advise. Thanks.
-
old heads are crap compared to the new heads out there.
The best thing about a 327 is the 4 inch bore block which can be used to build a 350 or 383.
I would keep the 327 complete and sell it to a "327 lover", then buy a complete 96 to 99 350 vortec truck engine with factory roller cam.
There is nothing magical about a 327. A 350 or 383 will make more power.
Pyro is right in his recommendation of a 96 to 99 vortec truck engine. The vortec block is of the generation wherein CNC machining has been used. The castings are likely more consistent than earlier blocks and the lifter bores are taller for better alignment/retention of the lifters during running. All around a much better engine block. Bore it .030 over and get a cast 3.75" stroker crank, 6" rods and SRP Pro pistons and you have a good bottom end. Use AFR heads, a good cam and appropriate induction system and you have a VERY good engine.
-
Does the Air Supply Tube (#13 FSM Figure FE-9) simply vent from the Expansion Tank to open air? For SCCA Autocross and other track events, does one have to make any changes (like a catch can)?
That looks to be the fuel vapor return from the engine compartment.
-
yeah, i was going to buy rear end out of a turbo car from Z1 motorsports so it's good to hear that they hold up.i'm still a little lost though on the whole drive shaft thing. Are you guys getting made to custom length at the machine shop or what?
The custom made drive-shaft is a certainty.
-
yeah, i totally agree. based off my loose estimate so far, i'm looking at spending around 2500-3000 just on the rebuild of the 350 including the machine work and possible a different set of heads.. i'm planning on using a t-5 transmission or a t56(if i'm lucky enough to find one that's reasonably priced) so my biggest questions are, what rear end do people generally use and do people just use the stock rear and have a use a chevrolet drive shaft that's cut to length with a nissan style yoke?
I went with a R200 from a Turbo 300ZX. It is a Clutch Limited Slip Differential (CLSD) with 3.7 to 1 ratio. Then purchased Turbo 300ZX CV half shafts and beefy stub axles from Modern Motorsports. Shortened all 4 struts and installed adjustable coil overs and Koni adjustable shock inserts. JTR has the parts for assembling the drive shaft to the R200. Need the yoke at the back of the transmission. T56s are expensive. A T5 in good shape may be a better choice and much less expensive than a T56. I have a T56 and in retrospect a T5 would be nearly as good. The right ratios in the differential and T5 are important to the usage of the car. The more involved you get the more expensive it becomes. Cheaper for street use. Expensive for race purposes.
-
Tony warned me that the rack would be so much more powerful that I should beef up the frame rails to deal with the additional strain. I had already done some strengthening of the frame rails, but the Z crossmember is not the strongest looking thing and I don't really see a good way to increase its rigidity.
Just playing around with the rack and an old crossmember I figured out that the old 6 cylinder engine mount towers had to come off, so those got cut. No biggee as I need to fab mounts for the L33 V8 anyway. Then I realized that the horns that stick off the front that hold the stock rack had to get cut back just to get the rack in position, so I did that. At this point I was able to get the rack positioned essentially in the stock position, but about 1/4" higher. Moving the rack back to the stock position fore/aft negates the work I did to move the rack back, but after graphing it out on the Ackerman thread, the difference will be minimal, so I'm not worried about it.
The rack mount is my biggest dilemma right now. I think the most logical way to mount the rack is to weld two pieces of angle iron to the front of the crossmember so that the flat part of the rack sits right on them. This may improve the rigidity a bit over the long unsupported saddles that the stock rack used, but they're not exactly what I would call "overbuilt". I thought of using a long piece of angle iron all the way across the front and I think that would be sturdier, but then there really wouldn't be a good way to put the bolts in, unless I drilled a big hole in the bottom of the crossmember, although that's sounding like it will be the best option at this point.
About the only thing I can think to do with regards to the crossmember would be to add a folded sheet metal gusset like a taco gusset between the crossmember and the frame rail, so that the lateral loads imparted into the frame go through two sides of the frame rail, instead of just the bottom. If anyone has any other ideas or previous experience, I'm all ears.
It's easy to see that fitting the rack to the front cross member will be difficult. I also want a good power steering rack such as that which you have purchased. I want to road race my V8 240Z and will need a sturdy rack. That is why I am interested in your efforts with this custom rack. Your approach seems to be on track by first removing the engine mounts from the stock rack. The rack mounting points and engine mounting points will have to be integrated into a custom mount which can be bolted or welded back to the original front cross member. This may be a project for a good CAD person to visualize the custom mounting point bracket.
-
Perhaps someone can help.I am looking for the right mechanic. I have a 78 Z with a 82 turbo motor with Megasquirt syste,
I have had several mechanics hack it up. Does anyone know a good mechanic in the philly market.
I am willing to have it shipped if i know it was the correct shop.
Please help
Contact the folks a DIYAUTOTUNE.COM. Return the ECM to them for bench testing. You need someone with a good electrical/electronics, mechanical and EFI experience.
-
I just installed the delco cs144 alternator and the installation was no problem, but i do have 1 question, do i have to use my old factory sense wire t connection, are can i just bypass that and use the sense thats on my cs144 and wire it to my main fuse block or batt,
this is on my 72 240z.
The CS144 should only need two wires. One light and one heavy gauge. The lighter one goes to a small fuse and has power on it in the key on position for alternator field excitation. The heavier one goes to the battery though a fuse or fusible link. The return for both of these wires/circuits is back through the case and engine. Best to have a heavy gauge wire from the case of the alternator back to the negative post of the battery. Then there is no question about the ground path to the negative post of the battery. Also a wire should go from the battery negative post to the body for accessories. Hope this answers the questions.
-
Thanks for all the ideas guys. For now it seems that I've "patched" the problem with another new battery. The car no longer drains all it's power and starts on command every time.
One thing that I've noticed is the ammeter is pretty jumpy now. Anytime I'm moving at street or highway speeds, the stock ammeter reads a tad past the halfway mark of 0 and 45+. But when I come to a complete stop, it's back to 0, and will skip a hair below 0, I'd say -5 or so when I apply the brakes, turn signals, etc. I also noticed it skipping when it's reading it's high amp reading when I apply the turn signals.
I'm under the assumption that it's normal for it to tick slightly when applying brakes (brake lights) and turn signals, but I'm a bit worry about the high reading and what, if any consequences are in store for me that the ammeter is leading on to. What's your take on it?
Also thanks again for all the input, and the FSM's should do great for all the wire hunting I need to do. Rsicard, what part of Tucson are you in? I was stationed at DM for about 3 years, just left there May of last year.
If the ammeter is jumping there may be a WEAK connection between the alternator and battery positive terminal. At idle the ammeter should go to zero charge or negative in that the battery is being drained. When the engine is revved up the ammeter should smoothly go to a charge indication after starting the engine. Some time after the engine has been started and the engine RPM has been increased for a period of time the ammeter will have a decreased indication but still a charge indication on the ammeter which means that battery is being recharged. The battery is merely a storage reservoir of electrical energy. The purpose of the alternator is to refill the battery reservoir with electrical energy after starting the engine. Then during normal driving the alternator will likely have restored the reservoir and will compensate for other electrical loads on the electrical system such as the ignition system, any lights that are on, the radio, the heater/AC blower etc etc.
STRONGLY suggest installing a VOLTMETER in the dash to monitor electrical system voltage. During start a good battery should not go below 9 volts. After starting the engine at idle the voltage should bounce back to 11-12 volts. Then when the engine is revved up the alternator kicks in and the voltmeter should go above +12 volts indicating the alternator is charging the battery. Erratic reading indicate a bad alternator or POOR electrical connections be they field excitation to the alternator or heavy current wiring to the battery.
Live in East Tucson. Go past DM many times and for air shows. Many retired Air Force people here as good friends. Love the noise of fighter jets overhead as this is the sound of FREEDOM. Was involved in Aviation Electronics for 38+ years. Electrical systems are EASY in comparison. Several years spent at Learjet as successful Liaison Engineer fixing MANY electrical and electronic problems on Aircraft. Also twice qualified Navy Aircrew-man aboard P2 (Sonar) and P3 (Communicator) ASW aircraft. Now a Amatuer Radio Operator with all three licenses. Attend three different radio clubs here in Tucson.
-
i'm going to use a standard "built" carburated 350. i was thinking about making it a stroker but for the money it's not really worth it.i would go LT1 or LS1 but i'm really going for simplicity. i also think that i posted this on the wrong forum. hahha it probably should have been on the gen3 and gen 4 forums.
There is no advantage to the LT-1 or LSx over the Gen I Small Block Chevrolet 350. If the 350 needs to be rebuilt it costs little more to bore and stroke it to a 383 cuin. It is the cylinder heads, camshaft, pushrods, rocker arms and induction system that make the real difference. With the proper combination of upper end parts, displacement for displacement the Gen I matches the LT-1 and LSx engines. It all comes down to the performance of the components. More performance = more money.
-
Ok I gotcha, thanks for clearing that up for me.
Check the items as described. YOU WILL FIND your problem.
-
Ive had my 240 for almost 2 years now and I have numerous electrical problems. The fuse box heats up to the point it melts. The wiring under the dash does the same. The more i tear into the wiring the more crazy it becomes. The Harness is real piece of art. Thousands of different color and gage wire, Millions of random connections and plugs that go no where. At this point i don't think there is any point in trying to save it. The problem i am having is trying to find a new harness. Is there a company that makes a complete harness for the 240, or do i have to use the universal kit?
Thanks for the help!
I have a 240Z also and have to do something with the wiring. The weaknesses in the wiring are the mechanical connections and the switches. Nissan routed heavy electrical current through the steering stalk switches for the headlights and running lights. The headlights have two fuses. One for the left headlight and one for the right headlight. That aspect of it is GOOD in that with one fuse blown both headlights DO NOT go out. The bad thing about it is the heavy electrical current for the headlights runs through the switches on the stalks on the steering column. To overcome this DESIGN DEFECT insert relays in the positive or negative side of the headlight wiring and have them controlled by the stalk switch which has to handle MUCH LESS electrical current. Then have Dave (on classiczcars.com) in Washington state rebuild the switches for you. Then the system will be BETTER than new. Also replace the running and turn signal bulbs with LED replacements from Superbrightleds.com. They may be expensive but should last much longer than incandescent bulbs.
Additionally, I found BAD single contact male and female connections in the harness on the cabin side near the firewall by pealing back the wrapping on the harness. Then cut off the blade type connectors, stripped the wire, slipped on heat shrink tubing, twisted them together and soldered them with Rosin Core solder and then slid the heat shrink over the connection and shrunk them with a heat gun from Harbor Freight. The other area that may need attention is the underside of the fuse panel. Perhaps some soldering will reinforce or strengthen connection there also. All the above is easier than replacing all the harnesses. Just some suggestions.
-
Yes head unit refers to my cd player, and my apologies, digital gauge I meant my digital water temp gauge. I will try what you've mentioned now and see what happens, but however I have an ignorant question, by field terminal you're referring to the "power" terminal that the red/white wire connects to right?
The field connection on the alternator will have a lighter gauge wire with +12v on it when the ignition key is in the "RUN" position. The Red/White should be the heavier gauge wire that connects to the heavy post on the alternator. The Red/White wire is carrying the heavy charging current for the battery through the ammeter back to the battery. This is the wire which must be a very low resistance connection between the alternator and the battery positive connection.
-
I've been thinking about doing this swap for 2 to 3 years now but never really moved on it. After my little incident installing my worked head on my L28ET, I snapped. I could not believe how much money I had in that setup, enough to fully fund my LS1 swap.
I just picked up a complete 1998 LS1 and 4L60E from a Camaro SS with 80k miles for $2500 + shipping. It comes with all sensors, PCM, maf, harness, etc., a complete drop out. JTR headers and JCI mounts & driveshaft will be ordered on Monday. I've been researching this swap for a while now and am rather excited.
I hope to have it running by the end of July.
Man, I should have done this 2 years ago.....
KTM: Thank you for spelling out the TRUTH. Hopefully the other folks on this forum will read this post and take heed. As long as money is being put into the drive train of a 240, 260 or 280Z, the best bang for the buck without a doubt is the Small Block Chevrolet (SBC) V8 engine. Several GM transmissions fit behind the SBC V8's. The other concerns are what the car is going to be used i.e. race, drag or street. The SBC can be modified to output 500+ HP normally aspirated. With turbos or superchargers 800 to 1000 HP can be achieved WITHOUT winding it up to 8000 RPM. Overhead cam engines just have more moving parts to fail versus well proven push-rod engine with a lesser amount of moving parts.
-
I think you need to start your testing all over again. Check battery voltage without using jumper cables or a jump box connected to the battery. Battery voltage should be 12volts. If you don't have this have the battery charged. Get the car started and check the charging voltage at the battery. Should be more than 13 volts with the engine running. If not, figure out why the alternaor is not charging.
You don't check for a system draw the way your checking it, I would start from scratch. I think your confusing yourself.
First set the Multimeter on the resistance mode. Short the two meter leads together and it should read ZERO ohms (meter check). Then connect one lead to the heavy post on the alternator and the other on the Positive side of the battery. The meter should read near or at ZERO ohms. There should be a direct connection between the two with a fusible (low resistance fuse) link in-line. If that is OK then check for battery voltage on the field terminal of the alternator with the ignition key in the RUN position. The return path for both of these is the case of the alternator. If the return path is in question, attach a heavy gauge wire from the case of the alternator to the negative post of the battery and recheck the alternator heavy post/electrical terminal for something greater than +12volts with the engine running at say 2000 RPM or above idle if the two previous checks were OK. Suspect that one or both are NOT OK.
-
I had the same idea as you just a few minutes ago about disconnecting things. The battery read 13.30V this time with the jumper cables.
Before that though, I had the multimeter propped up still reading the battery while I turned ACC on and started disconnecting things. I disconnect power and ground to the head unit and wideband gauge. When I went from having no power applied, to power applied, the voltage would drop by around .08V and stick there temporarily. I then proceeded to disconnect power and ground to the head unit and wideband individually. I noticed when I had power connected to wideband, and connected the ground, voltage would drop by around .10 rapidly, then when I took the ground off, it'd climb back up, connect ground, voltage back down and it sticks at a certain voltage. I did the same with the headunit and it didn't have nearly the same symptoms. So I immediately thought the wideband to be suspect.
So I hooked up jumper cables again, started the car, took off the cables and monitored the voltage with the grounds taken off both the headunit and wideband at the same time, but with their power wires still connected, and the voltage was STILL dropping. I took off power to the headunit and same deal. I however didn't take the power wire off the wideband yet, but I figured that'd be a lost cause.
So right now, I'm at a standstill and more confusion. I'll start tracing more wires when I have more free time. But as off now, I couldn't visibly see any exposed wires.
What is the item that you are cooling the "Head Unit"??? Please use the proper terminology such that appropriate advice can be issued. It sounds as though the Alternator is good but the wiring is faulty and not connecting the alternator to the battery properly. Do you have the wiring diagram for the 240Z? What is the "Digital Gauge"??? What does this gauge indicate? The 240Z has the ammeter in series with the alternator and the battery to measure charge/discharge current. What is the ammeter indicating throughout all these exercises? An appropriately charged battery should be slightly greater than +12 volts. When cranking the engine for starting the voltage should not go lower than 8 volts DC. If it goes lower there are bad cells in the battery. When the alternator is initially charging after engine start, the alternator voltage should be +14.x volts. As the battery attains a charge the alternator voltage should taper off somewhat from +14v yet still stay above +12v. The newer alternators need only a small amount of current from the battery to provide excitation for the alternator field to cause it to generate 12 - 14 vdc. There may be an excitation return (2 wire excitation) to ground or battery negative to complete the circuit. Normally the case of the alternator is the return or ground path for both excitation and heavy current to charge the battery. The other heavy post or connection on the alternator connects back to the battery through a heavy current (low or no resistance to current flow) fused wire. Older alternator charging systems had more (complicated) wiring than newer charging systems.
Hope this helps. Will look at the 240Z wiring diagram to see which OLD alternator system wiring IS NOT NEEDED.
-
Provided the tachometer has not been damaged, I think that MSD ignition has adapters that go between the HEI and Tach that clean up the signal from the HEI to the Tach.
Talk to MSD product support and they should be able to suggest the proper adapter.
-
hello im vigo i have a 1975 280 with a sb 350 just installed a hei and now my tac dose not work i was runing a stock gm non hei with a unilight swap .... i have all the proper gauge wire ran and have checked the connections ... while im not new to working on this z ( my dad bought it new in 75 ) i am know trying to fix all the things that have gone wrong while the car has set up not being driven in the last few years the v8 was droped in 15+ years ago so now its up to me ( with the help of yall ) to figure out all the bugs
Provided the tachometer has not been damaged, I think that MSD ignition has adapters that go between the HEI and Tach that clean up the signal from the HEI to the Tach.
-
He will also need to do something about the turn signal indicators if he's going with a SpeedHut tach.
I probably would've used a GM HEI if I had the room, but I pushed my motor so far back a standard magnetic pick-up type barely fits.
If I were you, I'd look at a magnetic pick-up distributor (either mechanical or vacuum advance)a la MSD, Accel, or hell, you could probably get away with the $60 Procomp unit, that's what I'm using and it works fine (it's an exact copy of the MSD magnetic pick-up unit). Then run an external coil and a CDI box. Crane, Mallory, MSD, Procomp, whatever, they're all made in the same factory in China, now anyway. The basic 6A/6AL units, at least. $200 tops on eBay. I like magnetic pick-ups because you never have to worry about them, they're less finicky than optical units and worlds better than points.
Another option is one of the aftermarket units that's basically a Ford Duraspark inside (I think most companies call them like "ready 2 run" or standalone units). That way the only thing external to the distributor is the coil and you can run the tach off of the coil negative (or is the stock tach loop through, I don't remember)
Either way, depending on how your motor is mounted (as in my case) you'll probably have to remove the hood latch temporarily to install.
The HEI unit is nice, but it's basically just a way of integrating all three components (trigger, control unit and coil), which to me just makes trouble-shooting and maintenance a pain.
The Speedhut Tach already has turn signal indicators within the tach. Thats more than Autometer does.
-
I got paid, so I ordered some DEI "titanium" wrap about 100 ft. of it, so maybe I'll have some extra to do some other things with it and a set of those KMJ SS headers.
Looking into those phenolic spacers and spark plug boots.
I appreciate everyone's feedback. Ultimately, I decided against the jet-hot/swain option just because I'm going to end up getting new headers, wrap and heat shielding for everything else for the price of the cost of just the coating.
If I melt or blow a weld on these headers I might look into getting a set of stock manifolds, polishing and radiusing them myself and send them off to get some kind of heat treating. Although, with cast-iron I imagine it'd be less of an issue to begin with. :/
Let us know how the titanium wrap works out. Also order ARP stainless steel 3/4" header bolts with drilled holes for safety wire. Safety Wire has been used in Aviation for MANY years. If done properly the header bolts will not back out. Also use anti-seize on bolts going into the heads as it will be much easier if they have to be removed.
-
I do. You can send a PayPal payment of $55 shipped for each one you want. I have plenty available...
Thanks!
Richard
Richard:
Need your Email address for PanPal. Thannks.
Rolland Sicard
Tucson, Arizona.
Tweaking the ECU with resistor values.
in Fuel Delivery
Posted
"The article was written about the generic L-Jetronic system". The L-Jetronic is a BOSCH fuel injection system! This discussion is FAR from where it needs to be. Most EFI systems have an embedded computer system wherein the fuel and ignition curves are contained in memory devices in binary form.