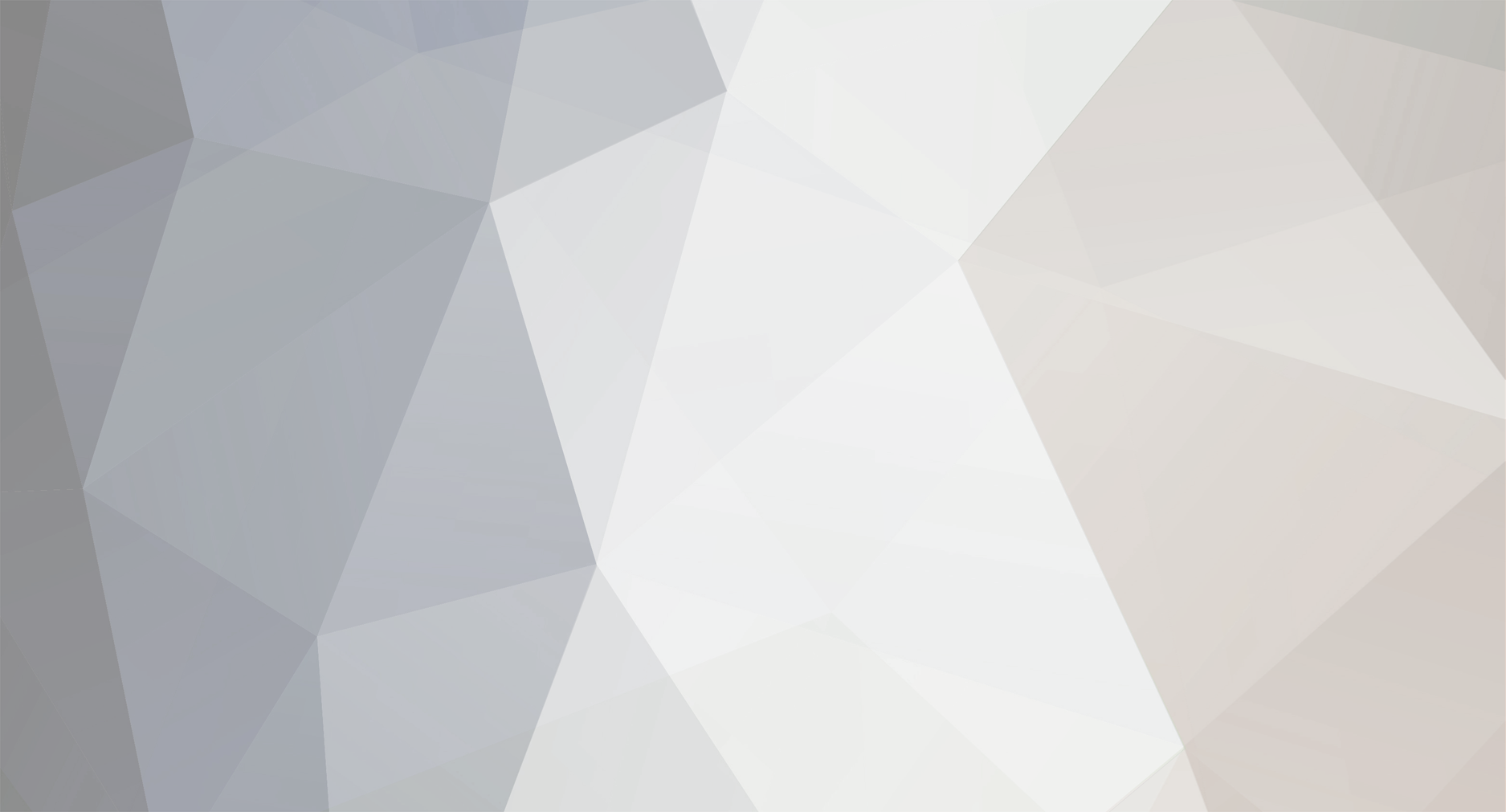
Oddjob
Members-
Posts
129 -
Joined
-
Last visited
-
Days Won
1
Content Type
Profiles
Forums
Blogs
Events
Gallery
Downloads
Store
Everything posted by Oddjob
-
Here are instructions on installing and calibrating an AutoMeter sender and gauge in the aluminum tank. The attachment at the bottom shows the installation procedure. This document is revised based on “lessons learned†from my installation. It should save you making some mistakes I made, because I was in too big a hurry. My mistakes can be fixed (essentially, I installed the float too high because I measured to the wrong place), but I will have to drain and pull the tank to fix it. I’ll get around to it, but not now. That said, I am still pleased with the results. Even as it is, the gauge reads better than it ever did with the stock tank, in spite of the many attempts at calibrating it. The essential difference this time is that this sender/gauge combination produces a linear output which is predictable, and can therefore be calibrated. The stock sender produces a non-linear (compensated) output, which cannot be properly read by anything except a stock gauge. Here is the present state of the new installation: Chart1a.pdf This is a picture of the type of wire I used for the run from the sender. It is a 105°C automotive wire, despite looking like speaker wire. The one in the picture is 10AWG (for the fuel pump), the one used for the gauge was 18AWG. Sender Installation Procedure.pdf
-
The 9/16" allen wrench finally showed up, so the tank was drained dry and the Earl's 3/4" aluminum plug was installed, replacing a temporary for the tank drain. Since the tank was dry, I used the occasion to find out what it really holds, and to begin calibrating the fuel gauge. Tank Capacity: 15.5 US Gallons, filled to a point 4" below the bottom of the overflow tube in the filler neck. This also coincides with the level of the floorpan under the hatch. I will post the fuel gauge calibration information separately.
-
Here's some technical grist for the mill, courtesy of a long Wikipedia article: "In theory, all fuel-driven vehicles have a fuel economy (measured as miles per US gallon, or liters per 100 km) that is directly proportional to the fuel's energy content. In reality, there are many other variables that come into play that affect the performance of a particular fuel in a particular engine. Ethanol contains approx. 34% less energy per unit volume than gasoline, and therefore in theory, burning pure ethanol in a vehicle will result in a 34% reduction in miles per US gallon , given the same fuel economy, compared to burning pure gasoline. Since ethanol has a higher octane rating, the engine can be made more efficient by raising its compression ratio. In fact using a variable turbocharger, the compression ratio can be optimized for the fuel being used, making fuel economy almost constant for any blend. For E10 (10% ethanol and 90% gasoline), the effect is small (~3%) when compared to conventional gasoline, and even smaller (1-2%) when compared to oxygenated and reformulated blends. However, for E85 (85% ethanol), the effect becomes significant. E85 will produce lower mileage than gasoline, and will require more frequent refueling. Actual performance may vary depending on the vehicle. Based on EPA tests for all 2006 E85 models, the average fuel economy for E85 vehicles resulted 25.56% lower than unleaded gasoline. The EPA-rated mileage of current USA flex-fuel vehicles should be considered when making price comparisons, but it must be noted that E85 is a high performance fuel, with an octane rating of about 104, and should be compared to premium. In one estimate the US retail price for E85 ethanol is 2.62 US dollar per gallon or 3.71 dollar corrected for energy equivalency compared to a gallon of gasoline priced at 3.03 dollar. Brazilian cane ethanol (100%) is priced at 3.88 dollar against 4.91 dollar for E25 (as July 2007)." Note: The energy content of ethanol is 21.2 MJ/l, compared with 34.8 MJ/l for regular gasoline (no ethanol). So trying to run ethanol in a non re-tuned Z would result in an extremely lean mixture and a very substantial performance penalty.
-
How to make autometer fuel gauge read properly
Oddjob replied to smoorenc's topic in Ignition & Electrical
I have tried to duplicate most of the suggestions in this thread on my ’71 240Z, which until recently, had a stock tank/sender and the Ford-spec Autometer gauge. I was unable to reproduce the results others have gotten building the resistor bridge using either their calculated or experimentally found recommended resistor values. I was finally able to get the gauge to read full and empty properly, but my resistor values were unique. I did figure out why this was, and in a word, it is grounding. Take a look at these posts for a technical explanation (fair warning, they are long and dense, skip them if you are not up for it): Star Grounding Scroll to Post #15 Grounding Scroll to Post #15 The fix was to run a new pair of wires from the gauge to the sender, one for signal, and one for ground. This removed the unique resistance the chassis ground scheme was adding to the resistor bridge, allowing me to reach a stable calibration. I also connected the gauge ground to the underdash ground buss from my star ground. However, this does not really give you an acceptable solution. The combination of the stock sender and the Autometer gauge is so non-linear as to make reasonable calibration impossible (see post #20, above). So, I got a bigger hammer: http://forums.hybridz.org/index.php/topic/96955-a-%e2%80%9cstock%e2%80%9d-fuel-tank-solution/ This is still a work in progress, but the combination of the Autometer sender and Autometer gauge is nice and linear. I expect I will be able to get this combination to work correctly in one of two ways. I will post the results in the above thread when I get there. -
This is actually a somewhat complex question, but yes, you have a good point. Take a look at this discussion Fuel Gauge Discussion. I have previously tried most of the resistor network changes shown, as well as a couple of tricks of my own (which I will post when I get time). At this moment, the Autometer sender/gauge combination I am using reads in a linear fashion. It is dead accurate for empty and full, but because the size of the tank varies in one step, the relative fuel level should fall a bit more rapidly to around a half tank, then a bit more slowly from half to empty. I am going to try it out this way, and perhaps test it to determine the actual gauge reading versus tank capacity. I am fairly certain that I am going to be happier with this combination than with the stock sender/Autometer gauge combination, which is so non-linear as to be nearly useless. In the event I am not pleased with the actual readings, with this combination I could 1) measure various tank capacities and re-mark the gauge face, which will work with linear readings, but would not work with the stock sender/ aftermarket gauge or 2) replace the current Autometer gauge with one of their programmable gauges, in which case I anticipate I could program it to account for the change in tank capacity at the tank step.
-
Again, these tanks are made-to-order, so you can add a sump and lose the 1/2" outlet no problem. My tank is internally baffled, to my specifications. They do have fuel cell foam, and will add it to your tank if you specify (I didn't, as I'm not racing, and wanted the extra capacity). So I guess you could have a fuel cell that mounted, fit and filled like a stock tank. The one thing I don't know is whether their fuel cell tanks are certified by the various racing sanctioning bodies. You'd have to ask them.
-
I'm sure they could, but I think it would create more problems than it was worth. The passenger side is also the tall side of the tank. You would lose significant capacity, as you would have to do more than "trim". The tank is asymmetrically mounted in the car, with a good deal of it literally behind the passenger-side wheel well. The filler neck is also on that side, which would make plumbing a problem. If I were doing the job, I would either cross the RH tailpipe over, and bring both exhaust tips out together on the driver's side, or "Y" the two tailpipes together after the mufflers and bring out a larger single tailpipe. Of course either of these options would mean mounting the mufflers ahead of the differential, where the stock resonator used to be. In your case, if you really want "true" dual exhausts, I'd say you would be a prime candidate for removing the spare tire well, and placing a rectangular tank more centered in the car. They do have a number of off-the-shelf rectangular tanks, and even a custom one to your specifications might cost less.
-
Here's the installation procedure I promised. I tried to stay in the middle of the road; more advanced enthusiasts will probably find it too obvious, and newbies will probably still have questions. Still, there is information on "gotchas" and lessons learned that everyone can use. You will need the "Brackets" PDF only if you are going to use hard point mounting. Installation Procedure.pdf Aluminum Tank Rear Brackets.pdf Here are a few shots of the installation area with the old tank out. This shot is looking from the driver's side toward the passenger side. The filler hose is clearly seen.The hose in the upper right corner is the vapor hose which is behind the tank, and hard to get to because of the rear valance when the tank is mounted. This one shows a view from the passenger side looking toward the driver's side. The hose in the upper right is the vapor hose which passes through the frame, and connects to the front of the tank. The braded steel line is the return. You can just see the pump output line over the top of the pump (also braded steel). The pump is bracketed onto the spare tire well. The fuel prefilter has been eliminated, replaced by the new larger filter on the tank. The pump had to be spun in its bracket to make the connections. You can also just see the third vapor line, hanging down by the tailpipe. This is a shot looking toward the rear. The diamond-shaped holes are the rear mounting points for the tank straps.
-
My pump is mounted on brackets attached to the spare tire well. It is directly in line with the filter, and at the same elevation, so it is gravity fed on the inlet at all times. Here's a few pictures of the installation (before the new tank): Rose's Ride, scroll down to post #24. Post #21 shows the brackets before mounting. Naturally, the filter and plumbing have changed a bit with the new tank. I'll take pictures when I finish up. You do make a good point, though. If the pump were mounted to the tank, you could hard pipe it to the filter and outlet, eliminating one soft line.
-
The three connections are really for the stock vapor recovery system, and the best I can say is that the Datsun engineers thought they were needed. That said, many guys remove the entire vapor recovery system, vent the tank, and suffer no ill effects. Either of the two higher bungs described above would certainly serve for a rollover-type valve and vent. Actually, the stock vapor recovery has a fourth line which goes from the filler neck around in a circle and into the vapor tank. Each of the other three lines also go into this tank. I did use all AN fittings on the new tank, and could convert to braded steel line anytime. It didn't seem necessary for the vapor lines, as they almost never have liquid in them, and are not under much pressure anyway. The outlet and return lines are braded steel lines and all AN connections. I have not thrashed the car at all, as it's only been done two days now. In fact, I probably won't, as it really is a daily driver. That said, I think it would perform fine in autocross with low fuel, as the inside of the tank is well baffled, and the very low-placed outlet has a siphon tube running along the bottom of the tank to the deepest part.
-
Well, my car is normally aspirated, and to tell the truth, I wouldn't know what changes to make specific to fuel injection. Please do jump in and outline what changes you would make for this use. Since the tanks are made-to-order, you could have most anything you want. The tough part was getting the shape and size right. After we installed the tank, Dave Boyd told me they had built two more tanks (and trashed them) before the one we installed. It apparently took some doing before they got it just right.
-
Here's the only "mounted" picture I have so far. I haven't had time to clean up the install and document it yet. Here's a nice clean picture of the tank completed, just before installation. The 1/2" bung in the lower left corner is the outlet, the 1/4" bung up the side of the tall portion is the return, the 3/8" bung at the top is part of the vapor recovery system on a stocker, which does serve as a sort of vent. The tab near the outlet is a hanger for the large -8 prefilter. This is a view of the rear-facing part of the tank. The 1/2" bung is again part of the vapor recovery. There are three vapor recovery connections in all. The third is a 3/8" bung on the end of the short part of the tank. Yes, the drain is a 3/4" bung on the bottom of the tank (I don't have a picture yet), located in the same approximate place as the stock tank.
-
Well, the odd behavior in the fuel supply system returned, despite all of the work detailed above. I got really sick of it, so I went completely back through every part of it, troubleshooting as I went. It turned out to be a multiple-failure sort of a problem, which meant I had been chasing it in a circle. The source of the problem was a failed coating in the stock gas tank (apparently done before I got the car). That was clogging the little siphon tube in the tank, which would get bad, and then clear at random intervals. This in turn was alternatingly clogging the two fuel filters. I posted the solution here A "Stock" Fuel Tank Solution , as it is of general interest. Here's a preview:
-
The fabricator has the prints on CAD, and has CAM/CNC files for the build. As I don't expect to ever need another tank, he was welcome to keep them. By the way, the tank is guaranteed for 10 years. Too late on weighing the tank. It's already in the car. We installed it yesterday. Since this was a "first article" build, we fitted the tank to the car in the weld shop, and then welded on the hard point brackets. The dimensions and locations of the brackets were then added to the CAD files.
-
Here is some more information on the fabrication: There were three major design goals, 1) the new tank had to fit the same space as the old tank, without cutting any sheet metal, 2) the new tank had to maintain the same ground clearance as the old tank, and the new tank had to utilize the stock filler arrangement. It met all of these goals. This is a nice-side-by-side comparison of the two tanks during fabrication. The new tank does not yet have its mounting points. This is the passenger side of the tank. Note the filler neck and the well for the fuel sender. Also note that the tank seems to be sitting at a wierd angle. As in the old tank, the rear part of the tank slants upward for ground clearance. You can see that angle better in the shot below. This shot is from the driver's side. The dimension of the tank coming toward you has been lengthened 2" to increase capacity.
-
I don't know, exactly. I filled it with 3 exactly measured 5 gallon containers when we were done. It took every drop, and seemed to be willing to take significantly more. The stock tank specification was 15.9 gallons capacity, but the stock tank I removed had previously measured 14.5 to the filler neck. It did not have any dents of any size. The aluminum tank fabricator could not estimate a capacity, due to the complex shape of the tank. However, in planning the tank, I had it built 2" wider on the driver's side (the shallow side) to increase its capacity. All of the other dimensions are exactly the same as the stocker. However, since the aluminum tank has square corners, and the stock tank has rolled edges, there is a bit more gain in capacity there. The only loss in capacity would be due to the square corner where the tank comes up to the spare tire well. In the stock tank, it bends around the well a bit. All-in-all, the aluminum tank is bigger, but I'm not certain how much. I will have to drain the new tank sometime in the future, as I was unable to put the Earl's drain plug in due to the lack of a 9/16" allen wrench. When I do, I will get a proper capacity measurement.
-
I knew someone would ask.... Like it sits*, $590. Could probably go a bit less, if you eliminated the bungs for the vapor recovery, and even a bit less if you didn't want the hard point mounts, opting to use the stock straps (which will fit). Of course, it could go a bit more if you added other options for your own use (say, an internal fuel pump). * "Like it sits" is probably misleading. As it appears in the second picture above, but with the hard point mounts added (one shows in the third picture). The fittings and sender were added by me as we were beginning final installation.
-
The Problems: 1. The car has had a long-running problem where it seemed to “run out of gas†at unpredictable moments. All of the usual suspects were checked and/or changed, all to no avail. 2. The car is fitted with Autometer gauges, including fuel level, and has had the usual difficulties in calibrating the gauge. Ultimately, the first problem was traced to a multiple failure situation. The stock tank has apparently been treated in the past with an internal coating, probably in an effort to repair rusting. Whether the treatment was the wrong product, was incorrectly applied, or just got old, I don’t know. I do know it is flaking off, plugging the siphon tube and both fuel filters. As to the fuel gauge, I have done all of the workarounds suggested elsewhere on the site, including a few of my own. I have concluded the situation can be improved, but cannot be completely fixed using the Datsun sender. The Solution: After some research, it seems that a stock tank is not a good option. Used units are all nearly 40 years old and likely to bring their own problems with them. New tanks are not made, and NOS seems rare-to-impossible to find. A fuel cell is an option, but requires a good deal of fabrication, including removing the spare tire well. As this car is a daily driver, and I have a use for the spare tire well, another solution needed to be found. The problem and the solution are shown in the pictures below. The new tank fits in the stock location, uses the stock mounting points, uses the stock filler components, does not require cutting any sheet metal, and has connections for the vapor recovery system, which I have elected to keep. It also has some key improvements. The tank is heavy-wall aluminum, completely TIG welded. The fuel outlet is no longer a smallish siphon tube, but a ½†NPT bung located in the bottom corner of the forward tank wall. It has a ½†siphon tube inside which goes to the rear, in the deepest part of the tank. It is entirely gravity fed (not a siphon at all) and directly floods an externally mounted -8 AN 100 micron prefilter, which in turn directly floods the electric fuel pump inlet. Note the filter mounting tab welded to the tank. I have elected an externally-mounted fuel pump for serviceability. All of the other tank connections are welded bungs, ranging from ¼†for the fuel return to a ¾†drain plug. The tank mounts are now hard points welded to the tank, and utilize the stock mounting locations on the car. The tank has enhanced internal slosh baffles inside. The fuel sender has moved to the top of the tank, and has been replaced with an Autometer 3262 sender (240-33 ohm). I elected to replace the existing Ford-spec gauge with a new gauge matching the sender, rather than trying to fit the early-model Ford sender to the new tank. Note the sender is placed in a shallow well, as the tank rests against the underside of the floor pan. Incidentally, the tank holds more fuel than the stocker. A word about the tank builder, but first, full disclosure: I researched possible tank builders, found these guys on the internet, visited their shop, was impressed, and commissioned the build. I have no financial interest, except as that of satisfied customer. The tank was built by Boyd Welding in Ocala, Florida. They specialize in building aluminum fuel tanks for aircraft, cars and boats. They can be found here: Boyd Welding The good news for anyone looking for a similar solution is that the 240/260/280Z tank is now a CAD/CAM/CNC file in their system, and you can get your own (the hard work is done). Since they build-to-order, and specialize in custom tanks, you can specify your own features if you don’t like my choices. I will post a more detailed description of the installation in a few days, along with many more photos, and will be happy to answer any questions about the project.
-
The item you think is the solenoid, is, in fact, the solenoid. According to my '71-72 manual, there is only one connection to the solenoid (besides the battery cable), which is a black/yellow striped wire. It connects to the ignition switch, and goes live (+12V) with the ignition switch in "start" position. If you have an automatic transmission, this wire goes through a "park" interlock switch on the way from the ignition switch to the starter. There is no ground wire shown. Your '76 should not be very different from the '71-72.
-
As mentioned, there are no emergency flasher switches to be had for this repair. Attached below in the PDF is the "fix" I ultimately used. This is a hybrid circuit to replace the OEM part. It has the advantage of consisting of readily available industrial components which are actually much higher quality than the original. The relay is rated for 10,000,000 operations, which should be good for something like 4,000 years of regular use. The switch is water and oil-proof, and rated for 15 amps at 12VDC (each pole). The major parts are as follows: 8002K34 oil-spray-tight washdown toggle switch, DPDT, on-on, 15A., quick disconnect terminals @ $27.33 69585K55 compact relay, 12VDC coil, 4PDT, 15A., @ $13.11 70205K26 switch seal and boot @ $3.54 These parts are from McMaster-Carr. The first photo is the stock switch (sorry about the bad photo). The wiring will be cut off the back of the switch, and new quick-connect terminals will be soldered and heat-shrunk onto the wiring. This allows you to connect the hybrid circuit directly to the stock wire loom with no modifications. You can then also remove it for service. The second photo shows the components before installation. There is no picture of the completed installation, as you can't get a camera up behind the dash to take a shot. The completed installation does work in the car, and has improved the brightness of the lamps, suggesting there was some resistance through the stock part. HAZARD SWITCH WORKAROUND 2.pdf
-
I can scarcely believe it has been nearly a year since I have posted to this thread. Some minor work has continued on the Z, and it has been driven pretty much daily. My project focus has been elsewhere. However, the emergency flasher switch broke, putting the car out of commission. As many of you know, this switch also takes out the turn signals and brake lights when it goes. Anyway, take a look at the posts here for a description of the fix: Hazard Switch Sticky Scroll down to #18, 19, and 20. This is a pretty good solution, if I say so myself.
-
As mentioned above, my original hazard switch is completely gone, and it has become unlikely that I will find an acceptable original part. The first step toward creating a hybrid replacement is to understand what the original does. So, I spent a couple of hours with a magnifying glass and drew the attached circuit diagram to show the logic of the connections. This drawing does make a bit more sense. However, please note that it leaves out the brake light and the turn signal circuits for the sake of clarity. Both of these circuits are downstream of the hazard circuit, which is why a bad hazard switch takes out your turn signals and brake lights as well. Emergency Flasher Circuit.pdf
-
As it happens, I've been trying to repair a broken hazard switch. I have learned so far that 1- Nissan doesn't make the switch anymore, 2- there isn't any NOS to be found, 3- used switches are nearly 40 years old and thoroughly picked over, and 4- the original wiring doesn't make any logical sense. I had intended to simply substitute an industrial DPDT and be done with it. At least on a '71, that isn't possible, due to the pervese switching logic of the original. Attached is a reproduction of said logic, copied from an original service manual. Perhaps it will be of some help to you. (Original uploaded file corrected 9/25/10) 71-’72 240Z Hazard Switch Logic.pdf
-
In truth, I don't think we can answer your question. If an electrician did the installation, and he wanted to use a white wire (which is reserved for neutral only) as a hot conductor, he is required to change its color at both ends (usually done with tape). A switched receptacle needs only four conductors: a ground, a white neutral, and two colored hots, one constant, and the other switched. The interconnection tab on the brass side of the receptacle is broken off, and gets the two hot conductors. If your receptacle is an old, non-grounded type, then you only need three conductors. The fourth should be unused. If this receptacle was wired by the previous homeowner, there's no telling what he may have done. The best I can say is that there is no "standard practice" reason those two conductors should be connected. As far as accomplishing what you are trying to do, you need only replace the receptacle or jumper the hot side together, and use only the "constant" hot for both sides of the receptacle. This will free your wall switch up for your fan.
-
You see mostly black and white because everything tends to be 2 conductor w/ ground Romex these days. However, per the National Electrical Code (NEC) hot legs can be any color except green or white (and some striped variations). By convention, the first hot leg is black, the second is red and the third is blue. Colors such as yellow and orange tend to be reserved for things like switched legs. Control and telecom wiring must be separated from high voltage (which is anything over 70V), so you are not likely to find them in the same box as 110V. A very common residential wire you may find is 3 conductor w/ ground (Romex), which is found in places like switched receptacles. This will have a bare ground, white neutral and a black and red hot.