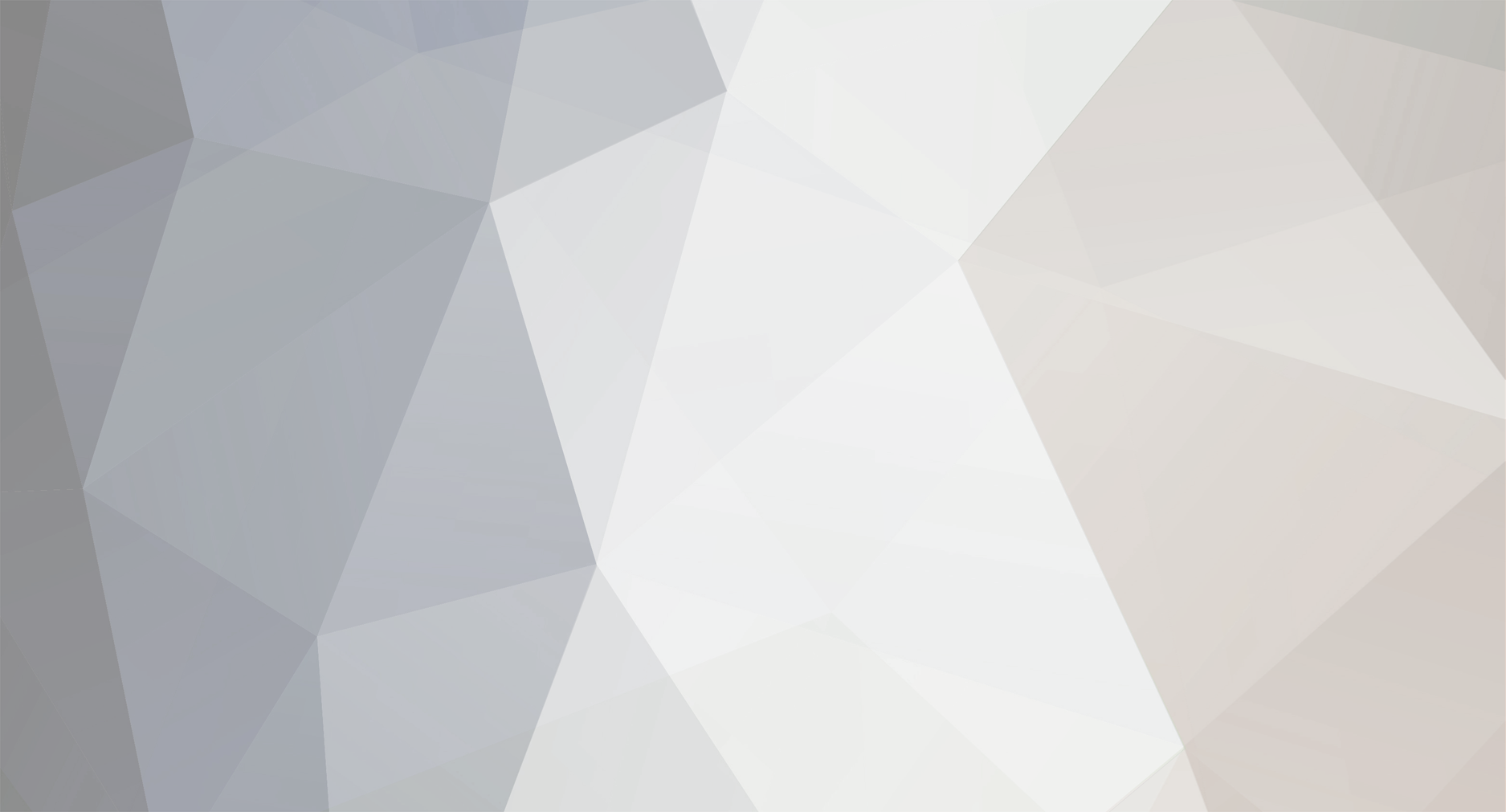
bryan01
Members-
Posts
206 -
Joined
-
Last visited
Content Type
Profiles
Forums
Blogs
Events
Gallery
Downloads
Store
Everything posted by bryan01
-
i recently bought a group of these from members on the board (4 from one and 3 more from another), just wanted to post a few pics of them completed. i disassembled them and took them to a wheel repair shop. got them all turned on a laithe to remove nicks, 2 of the lips needed welding and one minor straightening. then the lips went to a friend for polishing, and the barrels and baskets went to the powder coater for a mirror black finish. i think they came out well. the fronts are 16x8 (seller said 7.5, but they're only 1/2" different than the rears, and the profile of the lip/barrels are all the same where the tire sits, it's an 8" wide rim) and the rears are 16x8.5; i just ordered a set of 245/45/zr16 hankook r-s2's for them, should be here this week, and on the car by the end of the week (assuming i can figure out what to do w/ the stripped stud i've got on one hub.). http://uncutwelshman.com/gallery2/main.php?g2_itemId=2303 and below is a pic of the for sale post and what the wheels looked like before resto http://forums.hybridz.org/showthread.php?t=131154&highlight=HRE+sale
-
haven't posted in the fab/welding forum ever, but here goes i got a new welder, 240v/180a hobart, and now i have frame rails ... i was tired of borrowing and breaking/fixing breaking and fixing again a 140a one. oh and it's a )#*%^)#* to weld upside down ... i know the welds aren't the greatest in all places, but i can tell you w/o doubt that it's never going anywhere, here are some pics of the new rails (baddogz ... john delivered them personally, i live close by in CT apparently) ... i seamed some areas and stitched others. on the passenger side i replaced the entire floor last year, and it was really difficult to weld in the rail. on the driver side most of the stock rail was there and it was a lot easier to weld the new rail over it. and if you are concerned that the floor doesn't look completely welded, it's because i welded it from the inside way back when, not the underside ... those pics are in a previous album on the picture site. http://uncutwelshman.com/gallery2/main.php?g2_itemId=2250
-
it's coming along, finally bought (an awesome) welder to finish the piping with http://uncutwelshman.com/gallery2/main.php?g2_itemId=2194 ^ there's the link to the turbo install, i still have to modify the down pipe and make the intake piping, but JT's turbo setup is coming back to life!
-
http://uncutwelshman.com/gallery2/main.php?g2_itemId=2341 took 2 days to do, lots of cutting, but i was able to install a 240sx dash into my 280z without having to "bridge" a gap between the window and the dash ... fits great! (and yes, that's an r33 gage cluster that's going into the dash to be used w/ my rb engine)
-
rb exh studs/nuts and megasquirt for sale (RB25)
bryan01 replied to bryan01's topic in Nissan RB Forum
http://cgi.ebay.com/ebaymotors/_Car-Truck-Parts-Accessories__Megasquirt-1-v2-2-Full-system-tuned-for-RB25DET_W0QQitemZ250254276954QQadnZCarQ20Q26Q20TruckQ20PartsQ20Q26Q20AccessoriesQQadiZ2865QQcmdZViewItem?hash=item250254276954& oops, theres the link for the megasquirt, it's just sitting around taking up space on the shelf, someone make an offer, i hate for stuff to just go to waste. and the exh. studs/nuts i'm just selling on here, not on ebay yet. and i dont want to list the vendor but i know you've ordered from them before ... hopefully for their sake it was just a 1 time deal ... -
Due to an error, i got 2 full sets of exhaust manifold studs and nuts for my RB25. they're about 40$ per set shipped if anyone wants one. also i put my megasquirt (tuned for the RB) up on ebay finally, it's just taking up space and i could use the $ for other areas of the car. THANKS for looking
-
so there seems to be just as many opinions around my place as there is here ... i called the shop that's going to be tig-ing my intake piping, and they said egt's are awesome (maybe they just thought i might get it from them, i dont know) but for a street application actually they said they usually install them downstream of the downpipe. they said it could give you a "mis-reading" on the street if you were just sitting at a stop light and it was in the manifold or close to the turbo (even in the downpipe apparently) because of how hot they get, and yes i said "well isnt that the whole point?" ... they said it just depends on what i'm doing with the car and since i dont plan on racing every day, putting it in the manifold wouldn't give an accurate reading of the load on the engine ... any thoughts? stony? do you even have an egt? (most reponses were "i've seen" what are you guys actually doing?) i guess the shop is saying that for an all out racing application you'd be more concerned w/ a peak temp but w/ a street application you'd be more concerned w/ over all load and heat across the board, but not including the crazyness (high heat) that's going on near the turbo? zdrifter, know anything about all the egt's you've seen after the turbo? all aftermarket? were they put there for ease of install or because of wanting to read the temp there over somewhere else for some reason? warren, i have a 1/2" adapter plate between my turbo and my manifold, i'd be cool if i could fit the sensor in that, but i think the plate might be to thin for that. also along w/ that and where stony was saying to put it, install the sensor in the turbo itself? if it's so close to the exhaust side of the turbo, upstream of the turbo, wouldnt that affect flow into the turbo? or at the very least wouldnt the air be moving so fast and violently that it would increase the risk of a broken sensor ending up in the turbo? anyone ever hear of this actually happening? (i read a few posts during a search that people were worried about this with sensors pre-turbo).
-
well if i put it in later downstream of the turbo, then i don't have to worry about the shavings from drilling it going anywhere they shouldn't, and i can go ahead with my install right now ... mmm ... instant gratification ...
-
i'm installing a new-to-me turbo setup (that knot of a ss-tubular header that was JT's, 6-1 collector, etc). i've got a wideband (lc1) from when i had a megasquirt on the car (rb25), and now i've got an apexi fc ... once i get the turbo on and pipes piped it's going to the dyno my question is, should i drill and put in a bung (and plug it for now since i dont actually have the gauge/sensor) for an egt gauge now that everythings off? currently there are no gauges in the car, and i didnt have an egt before, but i'm thinking w/ the increased boost it's something i should look into. i've got a stock skyline cluster i'm going to wire in for the basic gauges, then add a few ... to EGT or not to EGT? if so, which runner (rb25, series 1) runs the hottest? i could put it after the collector, i searched and read about people putting them right after the turbo so that if the sensor broke it wouldnt ruin the turbo... ?? and a lot of people seem to say just to go w/ the wideband, or the wideband for tuning and the egt for street ... any experience w/ rb25 usage of EGt's out there? anyone know the range of temps for an rb25? also, if JT didnt need a egt w/ his setup, why would I? (he had a t4 running gobs of boost, and i'm adapting a large t3t4 for mine) ...
-
http://uncutwelshman.com/gallery2/main.php?g2_itemId=602 assuming stock mounts and good insulators come with your motorset ... hang the engine into engine bay w/ the motor side mounts and insulators bolted on the engine, sit the engine as low as you want it (you have to lower it more forward than you will when you mount it because the stock motor mounts will interfere with the car side mounts). get the engine at the right height and positioned front rear so that the engine side mounts are touching the front of the car side mounts (overlapping might be the word). mark the height that the car side mount will be to put the engine at the correct height, and the angle of the cut that you need with a sharpie against (following the angle/height of) the bottom of the engine side mount insulator. pull the engine out. cut the car side mounts. cut and drill plates that bolt to the engine side insulators and stick forward some (you will get a good idea of this distance based on the distance that your engine was from the firewall when it was hanging in the bay). this will offset your engine back some. bolt the plates to the engine side insulators, and lower the engine into the car (with tranny attached). once it's positioned perfectly, tack the plates into place, unbolt them from the engine side, and pull the engine. you may be able to do this w/o dropping the engine in, but we used it as a final check for the location of the engine (and tranny shifter point) in the car. weld the plates to the cut car side mounts, then drop your engine in and bolt it up. you'll have to loosen the bolts on the car side when bolting it up for the last time and finagle it in because the bolts (the way mine worked) were at an angle, so the tip (highest point) was more toward the center of the car than the lowest point where the insulator actually sat, so if they were bolted in tight the tips of the bolts wouldnt line up with the holes of the insulator. i had to loosen all the bolts and line them all up and drop it into place, then tighten all the bolts down. quick run thru, let me know if you have any questions.
-
broken exhaust stud help on rb25, part numbers?
bryan01 replied to bryan01's topic in Nissan RB Forum
oh man look at all that info, a picture even, nissan here in CT is NO HELP at all. one of the guys actually laughed at me the first time i called... but yeah, the process continues, i've got about 90% of the stud out of the one hole, there's bits left near the threads and b/c of the angle i'm having to drill at it's hard to get to ... i'm working on it thou, i'm trying everything i can not to pull the head or the engine just for 2 freakin studs ... -
broken exhaust stud help on rb25, part numbers?
bryan01 replied to bryan01's topic in Nissan RB Forum
after talking it over, that was the idea. i was just so pissed at running out of daylight and having to pack it up w/o getting both studs out ... but i'm going to keep drilling out the stud, try the bigger ez out, and if that doesnt work, finish drilling, including the threads, and heli-coil it ... it was such a pain in the *** thou that i dont think i'd want to redo ALL my studs that way. or do i risk(high risk?) breaking another stud when installing the new manifold? -
i've looked around and can't find the part number for an exhaust manifold stud for a rb25det. anyone know where to get one, or if it's on any other cars here in america? now, on to removing the stud. when i went to remove my manifold, i noticed that 2 studs were missing. when i pulled everything off, of course, i saw that they were sheared off just below the face of the head. i was able to pull one out with an easy out from sears (the square, hand held kind), but when i went to pull out the other the bit broke inside the stud. i then tried re-drilling it to no avail, the broken piece in the center of the stud probably stronger than the drill bit. then i whipped out the mig welder. i tried welding a bolt to the end of the stud, but it always broke off. i then tried just welding to the end of the stud, and it would always break off. the stud will move in the head, but it's like it gets up to the last thread and stops ... maybe the thread is destroyed? anyways, one time the weld broke off the broken piece of the ez out actually came with it. hurray, now i have a hole again, so i drilled up to the next size ez out and it stripped when using it, then i tried the next size with the same result. i'm running out of size to drill, so i didnt go any bigger on the ez outs. i was thinking of buying the reverse thread ez outs and trying that, but a friend told me how to make one out of a concrete nail, the ones that are about 1/16" sq at one end and are about 2.5" long, and transition into a rectangle at the other end, about 1/16"x 1/4" maybe ... anyways, i cut it short to the point where it stuck in the hole and started to grab, then i cut it a lil shorter, and grinded the sides to a point, so that it would grab in the counterclockwise direction, and it worked a little bit, but it snapped off in the stud ... _(*#^%(#% ... now i have to remove that attempt, but at this point i ran out of daylight and was too frustrated to think clearly so i packed it up for the night. any ideas?
-
cool, that means i'm at least right about the rb26's. the rb25's are high impedance and don't show a resistor pack inline to the injectors on the wiring schematic. the reason i'm asking all of this is because i'm finally setting up my apexi FC to run my low impedance injectors. the apexi FC is setup like the stock computer, which runs a high impedance system on the rb25. if i knew exactly what the stock injectors' resistance was, i could calculate the size of the resistors i would need inline, just like you said chris, to drop the voltage and run low Z injectors on a high Z system. i bought some resistors tonight online that should get me in the ballpark, and i'll test them out and post the results. who knew 25w resistors were so hard to come by.
-
i found that earlier too, but i was thrown off by the title of the page being "top feed injector". the stock rb25's are side feed. maybe i'm just being picky the rb25's are high impedance, just to clarify. i was saying that IF my r33 manual were correct, then the rb25 and rb26 injectors are the same, and they're resistance is 1.3 ohm's each. but it's not correct. EVERYTHING else online says that rb25's are high impedance and rb20's and 26's are low, including that link to that chart. it says that rb25's are 14.6 ohm's and rb26's are 2 ohm's. i found a different chart that was linked to some 550cc injectors being sold as rb25 direct replacements, and it's got 11.4 ohm's. it also only says there's 4 injectors, so i dont know how accurate it is (then again, i'm picky ) ... and they're not stock, but to be a direct replacement it'd have to be in the range that the computer could read, and thats a decent amount from 14.6 ... can the stock computer really support that range?
-
really quick, anyone know what this is? or can anyone do me a HUGE favor and go and measure it on their car? i don't have my stock injectors anymore, i found info for an rb20 and rb26 on here, but not the rb25 ... i also found info in a rb repair manual, but it said it was the same as the rb26, which would mean it's a low imped injector just like in the rb26, which it's not. i found a spec sheet for some aftermarket injectors for the rb25 that say they're 11.4 ohm's, so i'm assuming the stock ones would be around this level. just want to check to make sure, thanks.
-
nice z's! and talk about bringing a thread back from the dead, but i'm all about posting pictures ... i'll jump. http://uncutwelshman.com/gallery2/main.php?g2_itemId=17 i recently posted these, but i added another day for the wheel refurbishing.
-
http://uncutwelshman.com/gallery2/main.php?g2_itemId=1501&g2_navId=x82a4c102 added pics of the return/feed oil lines and fittings(thanks JT, note custom rb25 block fitting cut/welded in 1/2 so the -an return line simply bolts to the stock location), turbo, and profecB etc. the turbo is taped up b/c i had to drill/tap the exhaust downpipe flange holes on the turbine ... the turbo was used (although seemingly lightly) but the threads were different sizes (as in the previous owner must have tapped a few of them out slightly bigger, he must have cross threaded it during installation.) ... now they're all 3/8-16
-
i would call around and find out what other people are doing it for and go from there to give you a fair price. i would be able to supply everything paid for. and no, i'm a person not a shop, i'm a mechanical engineer working on jet engines from 9-5 and have done a rb swap before in a 280 (you can come up and see my car for yourself). look below for the thread i posted of rb project pics, it's got a dyno vid and lots of pictures of the process. PM me if you are interested.
-
i know you're excited, but try not to use all caps please. my first suggestion would be to do it yourself, but i know some people don't have access to tools or time to do such a thing. i'm not sure of any shops in NY, but i can do your swap for you, i'm about 2 hours north in hartford, CT.
-
lex - nooooo ... i moved outa atlanta about 6 months ago, now i'm stuck in connecticut of all places ... work is good, i only wish i could use some of the machines we've got at the shop for my car ... and it's cold. learning how to snowboard thou ... i MAAAY be driving the car south later this year depending on how reliable i get it, i'm in need of a long road trip. if i do we're going to have to get a group together in georgia ... but that's a ways away. i'll try to post pics of the turbo later tonight. triple b - thanks, it's taken well over a year to get this far, probably closer to 2 ... just takes time, sometimes i get tired of working on it, take a break for a while, then other times i cant get outa the garage. since i moved up here i havent been able to work on it much (started snowing in december and i had to put the car in storage then) ... all those parts are waiting to go on once i get it out in about a month.
-
precision se6152e, .63a/r turbine, .60a/r compressor, 63mm, 5bolt exh ... i've got pics of it but i haven't d/l them yet to the gallery site. and yeah, i had my eye out for manifolds and i saw his on ebay and JUMPED, i didnt even know he was selling it until i saw it in an auction and recognized the car. i'm also waiting for his oil feed/drain lines coming too ... then i got the apexiFC from dave (zul8tr) ... he's driving his 510 currently ... it's still got a long way to go, but it's getting there. here's the dyno vid w/ the megasquirt at stock 8psi if people want to watch that again too ... http://plaza.ufl.edu/bryan01/ and chris, my intake manifold is a greddy knockoff, you can pick them up for ~300$, fit great, the only problem i have is the injector ports are a few thou too small, so i ordered a special metric drill bit that's 12.00" DIA and i'm going to hone the holes out w/ it. (thats the size i need them to be for my injectors to really fit in, and not on) ... i'm also going to get the bung for the rad hose welded onto the manifold, b/c i was driving around the other day and it popped off. i thought the rad hose itself came off but no, it was still clamped onto the bung it's supposed to be on, the bung just decided to liberate itself from the press fit. it's currently jb welded ... seems to be holding ... i bought JT's exhaust manfold, he could probably tell you more about it than i, currently i'm using the stock manifold and turbo and boost settings. i'm going to use his manifold when i upgrade everything, it's made of SS piping, all tig'd, w/ a 6 to 1 collector ... it's a big knot of piping ...
-
i have had some time in the winter to hoard parts and get some pics together, so here are the pics of my progress over the last year or so from start to now (give or take) ... http://www.uncutwelshman.com/gallery2/ the link might change b/c i'm still messing around w/ the gallery and options, i'm not sure if i like the program i'm using yet. serious thanks to everyone who helped me out, (and you might recognize some of the parts on the last day ... JT and Dave ... ahem ... ) and the countless people who have answered my newb questions ... enjoy.
-
running low impedance injectors on high imped system
bryan01 replied to bryan01's topic in Fuel Delivery
http://www.megamanual.com/v22manual/minj.htm if you go down a lil more than 1/2 way it talks about using resistors and has a calculator for how much resistance you will need based on your stock setup and your current inj's ... it's designed for use w/ the megasquirt but should apply to any low imped on a high imped circuit ... i love answering my own questions ... i feel so proud ... now we'll see if it works -
running low impedance injectors on high imped system
bryan01 replied to bryan01's topic in Fuel Delivery
http://forums.hybridz.org/showthread.php?t=79407&highlight=low+high+impedance or no?