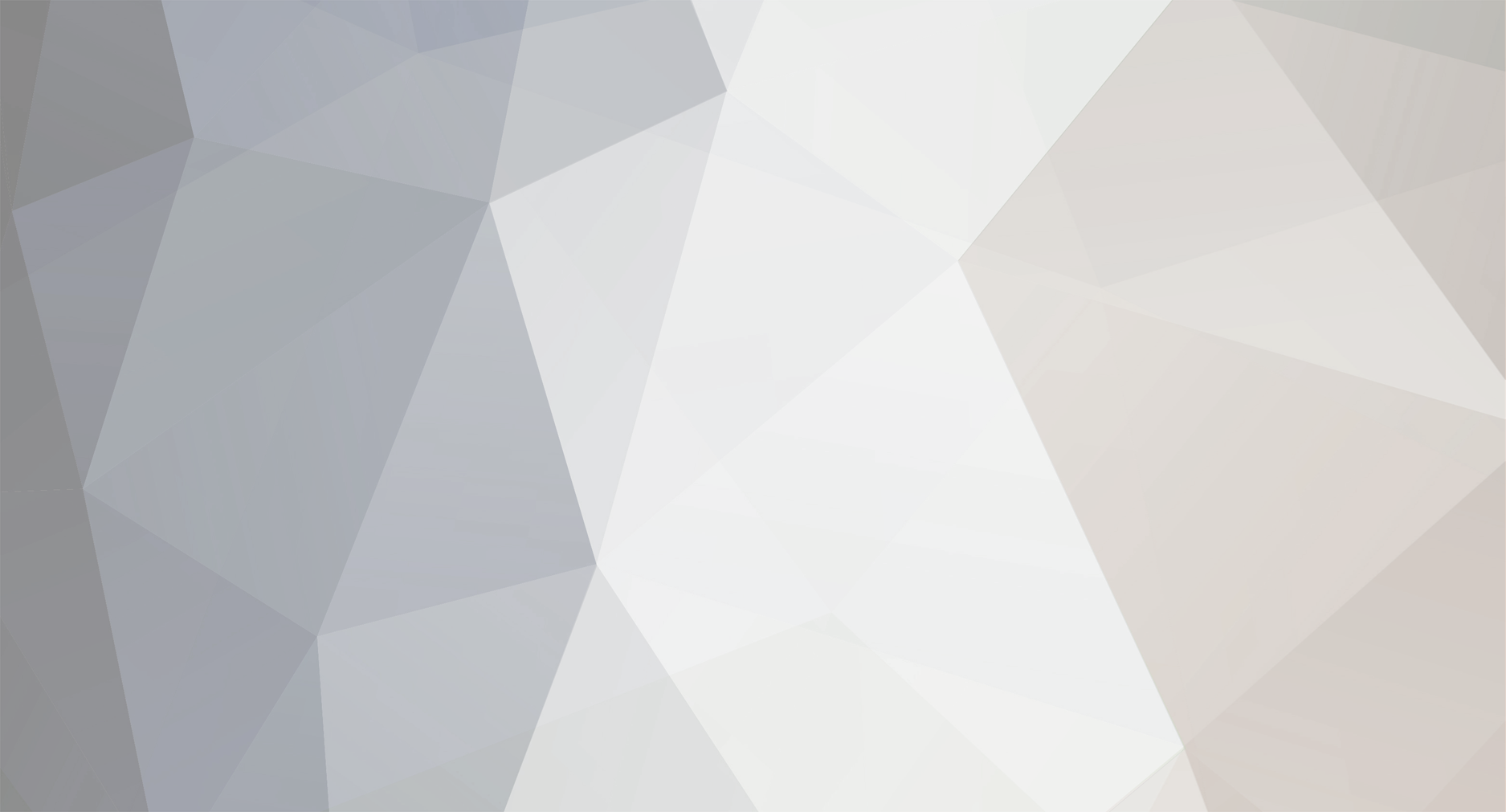
ktm
Donating Members-
Posts
1724 -
Joined
-
Last visited
-
Days Won
3
Content Type
Profiles
Forums
Blogs
Events
Gallery
Downloads
Store
Everything posted by ktm
-
Very nice. I gotta ask, what's with the holes in the inner fender behind the driver side tire?
-
The setup looks very clean. I've been following this thread and like how you've mounted it. I'll probably do the same. I see that you used one mounting bracket attached to the stock radiator captive nut. Where are the remainder of your supports? I you simply using the inlet piping as support as well?
-
I was simply exploring options. Gavin, it's interesting you simply cut the factory injection wires as that is what I was contemplating in this setup. I have decided to jump in with both feet and go with both fuel and spark.
-
Actually, the folks over at zcar.com are not Z car purists. I believe you may be confusing zcar.com with Classiczcars.com which does cater to purists. Zcar.com contains a bit of useful information, especially about stock and moderately modified setups. Unfortunately, it is also rampant with tons of useless, incorrect and dangerous information. You have to know what you are looking for and have some knowledge of the answer beforehand in order to get any useful information.
-
You can have a sump welded onto the bottom of the 240z fuel tank. While not as effective as baffling the tank, it is still better than a stock 240z fuel tank. A final option is to track down a tank from a 1975 or 1976 280z. These gas tanks are a bolt-on swap with our 240zs and are already baffled. Later model tanks will not fit.
-
The stock return will not work. If you use the stock return, chances are your fuel pressure will be high. Most folks use the stock feed line as the new return and plumb a new 3/8" feed. Another thing you can do (I am going this route myself) is to run a surge tank. You can use a low pressure carbed pump to feed the surge tank using the existing feed line. The return line from the surge tank to the gas tank can remain the same size as well. From the surge tank to the engine, you run a larger feed and return line as well as an EFI pump. The surge tank's primary purpose is to keep from leaning out under hard acceleration and cornering.
-
I see that some EMS are able to run fuel only as a piggyback to the stock ECU which is used for ignition. One such product is Microtech's LT4 system: http://www.microtechefi.com/microtech-products.php?product_id=2 Has anyone used such a system (not necessarily Microtech's) in conjunction with their stock ECU?
-
Turbo Swap Question - Do I still need the evaporative emission stuff....
ktm replied to ktm's topic in Nissan L6 Forum
It's funny you should say this Tony, as this was my exact plan. I have removed the flow valve and cut the line back to the trans tunnel, right before it crosses over to the passenger side. I am going to put the mini K&N filter there. -
Turbo Swap Question - Do I still need the evaporative emission stuff....
ktm replied to ktm's topic in Nissan L6 Forum
Thanks Pete. -
Turbo Swap Question - Do I still need the evaporative emission stuff....
ktm replied to ktm's topic in Nissan L6 Forum
The problem is that the line is actually connected to a flow (directional) valve. The line from the old air cleaner would supply the air when needed to the gas tank. It sounds like the carbon canister functions the same way. -
Turbo Swap Question - Do I still need the evaporative emission stuff....
ktm replied to ktm's topic in Nissan L6 Forum
I understand the requirements for the fuel lines. I am going to use the stock feed line as the return line and plumb a new 3/8" feed. On the carbeurated cars, there is an evaporative emission control system that consists of a flow guide valve, a hard line from the gas tank, a fuel line from the air cleaner and a fuel line to the crank case. It is used for controlling fuel vapors. The flow guide valve is located on the driver side. below the coil. -
You can run a pipe from the turbo straight out to get some clearance from the exhaust manifold and the turbo. Then you can run the hose from the end of the pipe to/from the inlet/outlet of the I/C. The residence time for the charge in the hose is very short. If you were concerned about thermal stability, you could run the piping from the turbo to the I/C inlet and then could run a hose from the I/C outlet to the intake. However, using a hose would benefit you most when running from the turbo to the I/C inlet, since this is usually a significantly longer run.
-
Matt, the hose you picked up is exactly what I was referring to.
-
I just had this thought while responding to my turbo build thread. Has anyone considered running a reinforced hose for their intercooler piping as opposed to aluminum or steel pipe? The hoses can take considerable pressure (much more than 15 to 20 psi) without pressure loss. The hoses are also fairly resilient in the temperature ranges they would experience. If you were concerned, they hoses could always be wrapped in a thermal blanket. For instance, many pumping systems are pneumatically operated. The air lines run great distances (>>1000 ft) and must be capable of sustaining sufficient pressure over the distance to operate the pumps.
-
Preparing for my turbo build, input is appreciated - parts list inside
ktm replied to ktm's topic in Nissan L6 Forum
Doug, your description of the sump configuration is very similar to how I saw mine. The remaining material above the sump would act as a baffle, keeping fuel in the sump during hard accelerations and cornering. I do not have a 240mm flywheel as my original engine is an L24 with an E31 head. This also means I do not have an electric fuel pump or FPR. I'll modify my plans and pick up a Walbro 255 pump but stick to a rising rate FPR. Since I need to get a new flywheel, I have decided to go ahead and pick up an aftermarket one. Clifton, thanks for your input on the intercooler. It's not that I only want the best for my car, but I am a firm believer that you get what you pay for. I live by the mantra if you are going to do something, do it once and do it right. Based on everyone's input so far, I think I can shave at least $500 to $600 off of my 250 HP build, and probably $300 off of the 350 hp build. Sounds good to me. -
Preparing for my turbo build, input is appreciated - parts list inside
ktm replied to ktm's topic in Nissan L6 Forum
I am leaning towards installing a sump on my stock tank. I will remove only enough material (maybe 4-in. in diameter) for the gas to freely flow into the sump. This way the sump should have a make-shift baffle above it. Again, thanks. -
Preparing for my turbo build, input is appreciated - parts list inside
ktm replied to ktm's topic in Nissan L6 Forum
I do not have a stock FPR (L24 with SUs). I put a rising rate FPR in there for now. I had forgotten about a wide-band O2 sensor. Thanks! -
Preparing for my turbo build, input is appreciated - parts list inside
ktm replied to ktm's topic in Nissan L6 Forum
Thank all of you for your input. I had forgotten about the electric fan (a mod I wanted to do) as well as the 240sx TB and spacer. Yes, some of the costs are a bit exaggerated, but I needed some idea about my potential budget. I am not going to say that money is no issue, but I am unfazed at the prospect of spending upwards of $3000. Joe, what kind of fitting are you running in your drain plug? I read about alternatives such as using the existing feed line as the return and running the new feed line from the plug (like yours), or installing a sump. Clifton, I am not really on a budget, nor do I feel the need to buy the best and most expensive parts either. ACT is on my list of clutches as well. I have been looking at both and only included SPEC in this list. I have a spreadsheet with various builds as well as parts suppliers and costs (and model numbers too). As far as the IC goes, this is one place not to buy a cheap part. I am looking at both cooling efficiency as well as pressure drops across the IC. Many of the cheap ICs may cool the charge air, but they may have a bit of pressure drop from inlet to outlet as well. -
Preparing for my turbo build, input is appreciated - parts list inside
ktm replied to ktm's topic in Nissan L6 Forum
Sparks, the boost gauge I referenced was an electric gauge. Mechanical gauges are $50. I am still debating whether or not I want an electric or mechanical gauge. On my old 2002 Audi S4, people were split between mechanical and electric gauges. The Audi use to have an oily blow-by in the intake piping which would make its way into the gauge tubing. Since the tubing goes into the car with a mechanical gauge, it could get a little messy. -
It's the rectangular block beneath the coil.
-
Could be a dead ballast resistor or that the resistor is hooked up incorrectly.
-
You adjust them by first measuring the gap between the lobe and the top of the valve assembly. The lash should be adjusted while the engine is 'hot', but as a first attempt, adjusting them cold is fine. The gap should measure 0.08 intake/0.10 exhaust when cold and 0.10 intake/0.12 exhaust when hot. Adjusting your valves is actually quite easy. I suggest doing a little bit of reading here, on Zcar.com (yes, there is some good basic info there) and Classiczcars.com for basic maintenance tips. Image courtesy of Blue from Zcar.com. You really, really do not want to be running 28 btdc with your vacuum advance hooked up. I had 17 deg btdc on my L24 at idle and 36 deg btdc (iirc) at 3000 rpm.
-
Preparing for my turbo build, input is appreciated - parts list inside
ktm replied to ktm's topic in Nissan L6 Forum
I've read that the Walbro pumps tend to be quite noisy. However, I am not so much interested in the brand at this time but simply if I have identified all the parts that I will need.