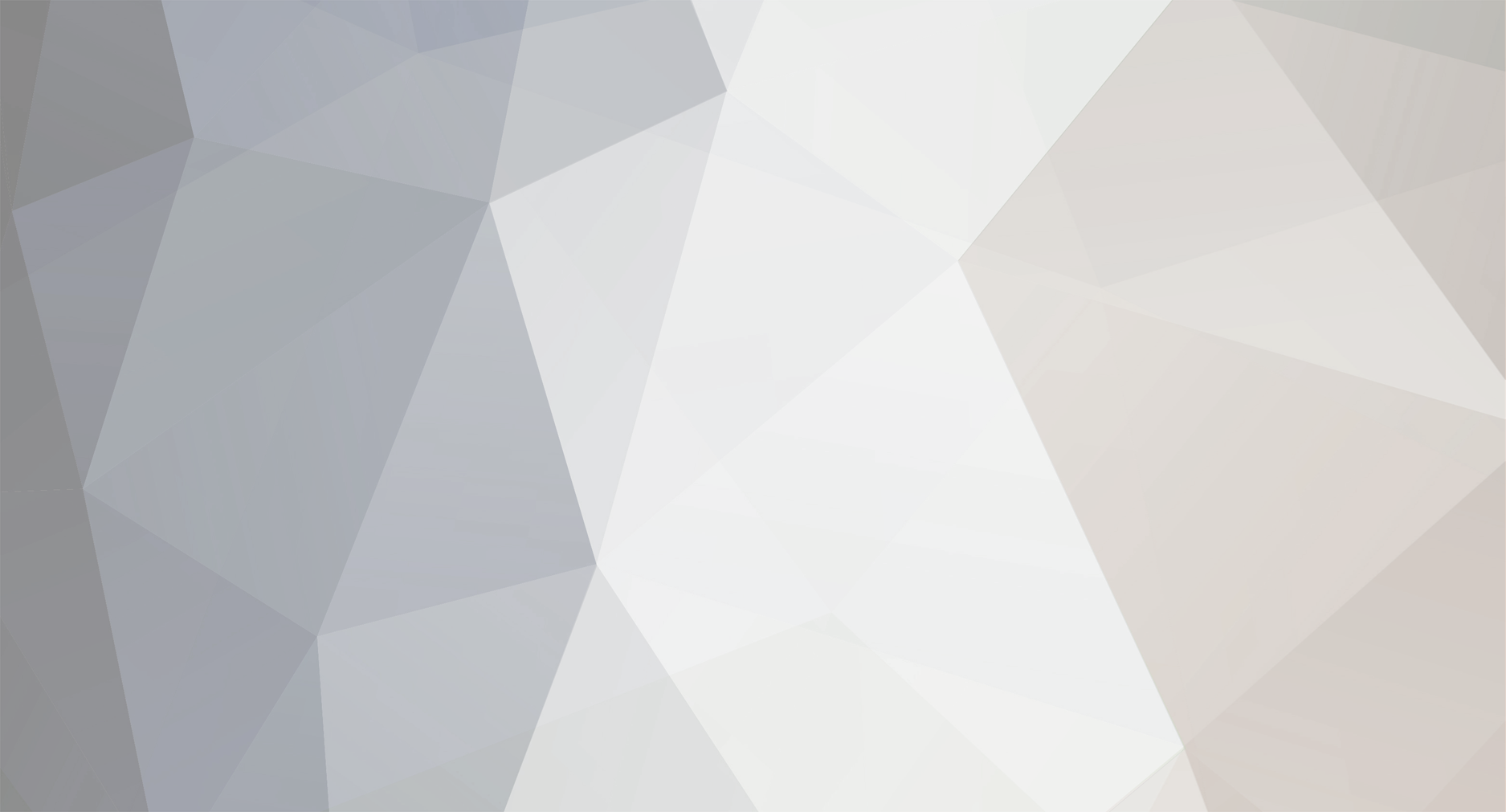
X64v
-
Posts
543 -
Joined
-
Last visited
-
Days Won
1
Content Type
Profiles
Forums
Blogs
Events
Gallery
Downloads
Store
Posts posted by X64v
-
-
i'd like to see...
http://forums.hybridz.org/showthread.php?t=126299
Not quite what you had in mind, but one could easily run a 4" or 5" pipe, pretty much making it just as good.
-
Shut off all the power to your house for the night and have a big civil war re-enactment battle in the morning...
Oh yeah, and "...party like it's 1899."
-
I'm thankful that the "hickup hickup BANG!" I got under boost on the highway last night coming home didn't mean damaged ring lands.
-
I ran my balance tube with those same set screws for over a year with not a single problem, never touched them after I put them in.
-
Leather wasn't factory on those cars. I'm not an expert on the various options that might have been given, but the stock seats are Naugahyde (fake leather). I guess they could feel like leather if you don't know what real leather seats are like.
And I would feel bad paying $6600 just to chop it up an unmolested original car. If what you're looking for is no rust, there's arizona cars that have no rust, but bad interiors and paint, that you could buy and have shipped for less than $6600. If you were looking for a totally stock DD or something, then yes, I'd pay $6600 for it.
-
Well, hot fuel it may be.
I did another test today. I went for a 20 minute drive, got everything nice and warm, on boost a little but not much, etc. When I pulled into my driveway (with a perfect 900rpm idle at 12.5:1), I took my fuel rail temps while the engine was idling, via a non-contact IR thermometer. The rail was 90°F, and the injectors were 110°F. I then closed the hood and waited 20 minutes. Ambient temp was 70°F, car was parked in the shade. The temps after 20 minutes were 130°F on the rail and 150°F at the injector. I then started the car, and it proceded to try to die at idle, as expected. After a good 45 seconds to 1 minute of revving lightly out of gear, I got it to idle stably, although it was 200 rpm low, and rough (again, like always). At this state, the fuel rail had dropped back to 90°F, but the injectors had only dropped 10 degrees to 140°F (I would guess the cause for my still rough idle, as the fuel isn't moving very quickly through them at those low pulse widths).
One should note that the increase in rail/injector temperature (measured in Kelvin, of course) is ~7%. The increase in pulse width needed to correct this stumble (1.4ms bumped up to 1.5ms) is ~7%.
If we really wanted to be accurate with our fuel measurement, perhaps one could install a fuel temp sensor into the fuel rail, and edit the MSnS-E code to account for this... A dead head rail would actually be an advantage here, as the rail temp would match the injector temp, instead of cooling down while the injectors stay hot.
Edit: It's also important to note that I have no heat shielding on my engine whatsoever. I also have a non-webbed intake, so all the heat from the exhaust manifold and turbo likes to just come creeping up. i have the original heat shielding for the n42 intake I have, I need to cut it up one of these days and get it on there.
-
Wow, I absolutely love that color!
-
Mario - You're on a stock turbo cam, right? What's your vacuum reading with it set like that? I'm pulling 16-18 in.hg. below ambient, or about 34kpa absolute.
I remember you telling me about that for big injectors, I may have to do that anyways when I move to 500cc's.
-
As many people do, I suffer from a rough idle after anywhere from five minutes to one hour after running the car, depending on ambient air temp. I fixed this by just richening up my idle, but this gave me about an 11.3:1 afr during a normal idle. My engine is happiest at about 12.3-12.5:1 at idle, but this brings back the hot idle situation. To try to analyze the problem, I took two data logs, one of a perfect idle after a drive, the other of the idle about 20 minutes after that drive, as soon as the engine started. The two logs below:
Smooth idle:
Click here for a full size version.
Hot start:
Click here for a full size version.
Both logs are attached in the zip file. For the smooth idle graph, go all the way to the very end of "woo 11-12-07"
What you can't see in the graphs:
Coolant was 171°F during both tests (no, warm up wasn't on, I run a 160°F T-Stat)
Battery voltage was 13.4V during both tests
Ambient air temps were within a few degrees of each other
Overall engine temps were very similar (hood was kept closed, so not a lot of heat was lost)
What you see in the hot start graphs will go on for about a minute while driving (won't idle at stoplights), and a few minutes at just idle. Everyone's thinking "Vapor lock, hot fuel," right? I'm not so sure. I'm running a non-metal fuel rail, and cycling the pump on five or six times before starting (basically getting the pump to pump cool fuel through the rail for 10 or 12 seconds prior to starting the engine) does not affect this. Running a 1.5ms pulse width at idle totally fixes this problem, it'll start up and idle at 900rpm with no throttle on a 100+ degree day after sitting in the sun for half an hour, but my afr's would be, like I said, in the low 11's.
A few people were talking about having their IAT sensors heat soaking and causing lean conditions, but my IAT readings were within 2 degrees of each other during the tests. I have not ruled out hot fuel as a possibility, but I'm not convinced it is, either.
One possible fix is to just run in closed loop at idle. With 12.5:1 as my wideband target, it idles alright, though it will hunt a little at times (switching between 1.4ms and 1.5ms).
Any thoughts either way?
-
Mr. rontyler,
Any news as to the Audi IAT sensor? Heat soak tests, usage, and so on?
-
http://forums.hybridz.org/showthread.php?t=125955
This downpipe was no small upgrade, especially at the amount of air that engine is flowing to achieve those numbers. You'll notice that at 4300rpm his torque only went up about 20ft.lbs. It's the ability to get the exhaust out as rpm's climb that gives the hp increase.
-
Wow, that thing sounds excellent!
As to the montage, I svear zee Germans are obsessed vith zee 80's.
-
I like it, it's pretty cool looking
Monzter, that's a great idea. You know how cool marker lights made out of that material could look?
-
That would be Baby Ray..dunno why I didn't think of that myself.
Similar indeed
-
Actually, I cannot speak for all 240's, but my '73 (which came from the factory with the electric pump) had some safety circuitry built in. There were two small modules under the dash. I referenced them in my '73 factory service manual, and if I remember correctly, one of them cut the fuel pump off under something like 300 or 400 rpm, and the other overrode that when the key was in start to run the fuel pump during cranking.
It is totally possible that this was all add in stuff at the dealer to help combat the vapor lock issue. The modules were wired into the fuel pump circuit with connectors that tapped into the little in line fuse under the dash, and the starting circuit was referenced via a wire running along one of the heater hoses to the starter terminal! The connectors were all factory, but the wire routing certainly was not.
And as of late, Megasquirt cuts off the fuel pump after two seconds when the engine is not running, so I'm good.
-
Ron - happy anniversary for tomorrow. Good statement, too.
I was 16 when I got my z running, 17 when I joined, and 18 at present. Be courteous and act mature, and most won't even realize your age until they look in your profile or meet you in person.
-
Mario is correct. The statement "Y varies directly with X and Z" (for k=1) gets you Y = XZ, not Y = X+Z
-
Quite alright, I was just about to post my conformation of your correction. After the thing wouldn't budge, I decided to pull the whole pulley/damper assy. off to use a puller on, and once I cracked the main bolt loose, voila, the third row was loose.
-
Ah, there we go, exactly what I was hoping for. My z came with dealer installed a/c, and I was wondering why it would be bolted on if it didn't need to be.
I'll work a little more at it, I didn't try too hard just in case it wasn't just bolted on.
Thanks a bunch
-
Well if that's the case, both extra rows are coming off.
Thanks guys for your responses.
-
It's certainly possible. I didn't want to pry on it too hard though, just in case I did need to unbolt the center bolt, or if it didn't come off at all. For what it's worth, the main and center pulleys spin straight and true, while this last row has always wobbled just a little, which would indicate to me that it is in fact removable.
-
lmfao! The different reactions people had were interesting to say the least.
-
Nice! One of my favorite movies.
Ditto on the thermal bandages suggestion:tongue:
-
As the title says, is this possible? I've got a factory 3 row pulley on the front of my '73 l24, and since I'm not using the last row, I figured I'd see if it came off. It appears to be bolted on, but removing the two bolts didn't free it up. Is it an interference fit, or do I need to remove the crank pulley bolt, or what?
Made it to the dyno
in Nissan L6 Forum
Posted
I politely disagree with the above statements. Force is dictated by the output of the engine, not the mass of the vehicle. Less mass equals less force for a given acceleration, but not for a given engine output. If you put 600ft.lbs. of torque through a tranny, it does not care what it's trying to move. You're not moving as much mass, but you're going to get better acceleration, making the stress on the tranny the same.
The lighter pistons analogy is not the same, as acceleration is held constant, dictated mostly by engine rpm.
The point is moot, as you're using that tranny no matter what, but none of us like incorrect information floating around.