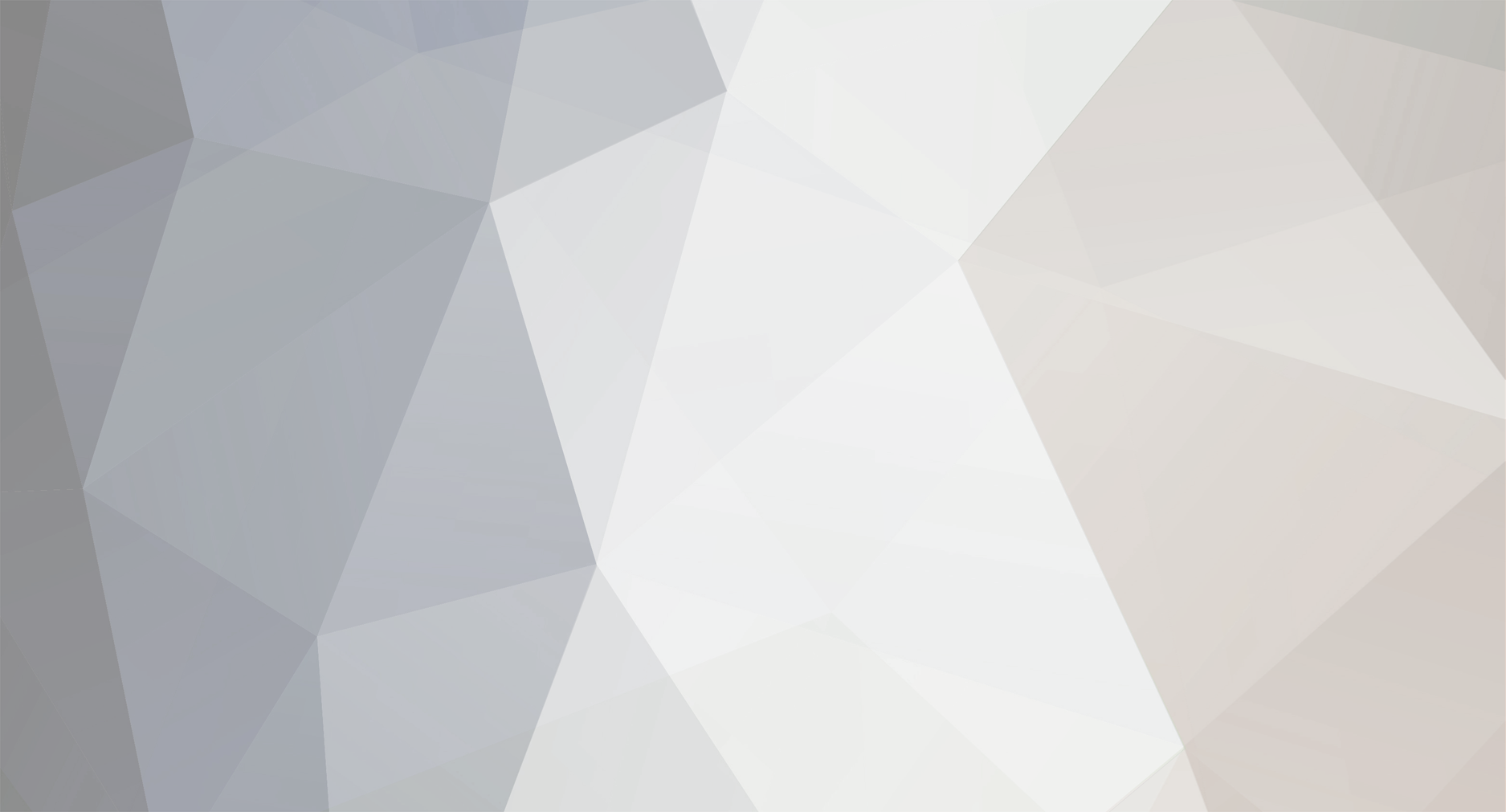
Pop N Wood
-
Posts
3012 -
Joined
-
Last visited
-
Days Won
5
Content Type
Profiles
Forums
Blogs
Events
Gallery
Downloads
Store
Posts posted by Pop N Wood
-
-
http://forums.hybridz.org/showthread.php?t=109413
http://forums.hybridz.org/showthread.php?t=124050
You also have a good deal of flexibility in adjusting the diff angle. Search on Ron Tyler diff mount. Also know you can drill out the washers on the mustache bar to further tweak the diff angle.
When I set my motor to match the stock diff angle it required a good bit of tilt in the engine/trans. This put the back of the trans way too low and/or the intake into the hood.
Leveling the rear diff let me level the engine giving it a much better placement in the bay.
Also keep in mind the trans/diff mounts will flex under torque. You can measure things to a nat's ass but who know what it will end up being under power.
-
You really need to look at it in person.
If the body is not rusted through than that is a good deal, motor or no motor. An uncracked 240 dash is worth half the purchase price.
If the battery tray and floor is rusted through than that is just $1000 worth of headaches.
-
My local Safeway sells dry ice.
-
Do you have any idea where the shifter is going to come out with the engine that far forward? Not to mention tunnel clearance above the trans.
I'd also be a little worried about hood clearance.
You really need to get your transmission on there and check drive line angles before you will be able to even guesstimate the final motor position. That motor seems to have a large number of interference points. Engine tilt makes a huge difference in terms of clearance pretty much everywhere, and it is the rear diff that will determine the engine tilt.
-
Let us know if you fixed the problem.
BTW, Taurus fans are under $20 at the local pick and pull.
They will even let you exchange bum fans.
-
You might contact the guys at MSA about buying a few dozen of these. I would think they could more than recoup there investment, and the added quantity count might kindle a little more interest from the guy making them.
Black Dragon auto would be another source of component count.
-
Don't try and use adapters to extend mounts. You would be hooking adapters to adapters then strapping 400+ HP to them.
Vinh's style cross member can be modified to work with the JTR LS headers. You have to remake the starboard side Corvette mounting bracket to move that mount forward 1" then offset the mounting bisquits to match. Also S&P makes a set of mounts that are a 10th the size of the factory vette units.
All in all the JCI kit is the quickest, most sure way to get the vehicle on the road.
-
I remember seeing that set of pictures over a year ago.
but yeah, stupidity is timeless.
-
I wonder how many G's those guys pull in the turns.
Would love to be a part of a hobby like that. suppose it is big bucks though.
-
I think that I will just rebuild the fronts with the 4 pistons up fornt and use a brake porportion valve to adjust the system untill I can get what I really want........I just hope that it will work.
4x4 calipers will not clear stock 14" steel wheels. At least mine didn't anyway. They would have worked with longer studs and spacers, but I didn't like that idea.
-
There was another thread about this a while back. Temp guages can be voltage sensitive if the internal regulator is starting to age. Are you sure it is actually getting hotter? And how hot, really overheating or do you just not like it going up?
If you still had the 3 wire I would recommend putting the sensing wire right at the fan. That way you would have a constant voltage regardless of RPM.
-
Shoot, man. You did everything I could think to do.
Do you have the fan on the low or high speed setting at idle?
Also do you have a 1 wire or 3 wire alternator? What is your voltmeter reading when all of this happens?
-
The fact is that Nissan put together an industrial engineering masterpiece from it's conception to delivery and for History. It would be unwise to assume they used poor quality materials at all. Everything was engineered to do exactly what it is supposed to do and nothing more.
You don't know much about the realities of engineering consumer items.
It's all about making trades. Using what's available and cost effective. I will bet money there wasn't an engineer on the original Z car design team that didn't have a list of things they would have changed if they had the power to do it.
Manufacturing capabilities and processes do mature as a country becomes more industrialized. That has nothing to do with race or politics. Just a fact.
-
$600 will buy you a brand new Power Brute LSD carrier for an R200. R200's themselves are almost give away items.
You don't say how old everything is. Used LSD's often require rebuilding, at which point just buy a new PB carrier.
$3600 is more than I would pay. There is something to be said for the convience of getting everything in one package though.
Get 20 brand new $100 bills and go talk to the man. Be prepared to walk away if he doesn't bite. Depending upon what the used Z market is in your area he might be still trying to recoup his money a year or two from now.
-
The pitting is no good and will need to be removed with a hone.
Just get a new one and be done with it.
-
This is not something people are likely to diagnois over the web.
Jack the back of the car up and turn the tires by hand.
Look for evidence of rotating pieces hiting non-rotating pieces. Like the parking brake cable, brake likes, CV boot clamps.
Everything else is just guess work.
-
You could always get rid of the poly and just use a piece of aluminum.
My MSA piece is made out of a solid plastic that doens't look too heat sensitive.
One Canadian member even used a hockey puck as a coupler. Pretty cool, eh?
I have seen guys who completely eliminated the coupler and bolted the two shafts directly to each other.
-
The poor quality materials theory is a no go.
I have to disagree with that one. Maybe true for a Z, but it certainly wasn't true for Japanese cars in general. There have been cases where auto sheet metal would rust from the inside out. That was true for domestic as well as foreign. I think there were a few law suits from it too.
Remember back in the 50's-60's Japan's manufacturing abilities were about as mature as China’s are now. They did use a lot of low quality, recycled materials and did produce a lot of low quality stuff.
Kind of scary to think where China will be in 20 or 30 years.
Also keep in mind cars didn’t use to cost as much as they do today. Car manufactures thought of them as throw away items, and since all car manufactures were doing it basically the same way, why dump a bunch of money in corrosion protection.
-
Or, like 99.9% of the people who install these, just bolt them on.
..
-
You guys are a little over the top. I have a 140 amp welder. It is a 220 volt though. It has done everything I have wanted it to. Can't say I have ever had a situation where I really had to have another 40 amps. I get perfect single pass welds on 3/16 mild steel. It flat tears up stainless with the same gas.
There are time where I have wished I could weld aluminum, but I have a oxy-acetelene torch if I really want to weld aluminum sheet.
I agree with tannji's advice
-
-
I keep going back and forth with this, but I keep going back to my original thinking that the weak point is the taper going to the threads and not the spline.
From the number of failed stubs I have seen on here I tend to agree with you.
and from this link you can see that getting rid of the taper moves the weak point to the splined area itself
-
The FAQ page has some stub axle failure pictures
http://forums.hybridz.org/showthread.php?t=116207
The 280 axle is a larger diameter right at the base of the threads than the 240 axles. There is a much better picture floating around the web showing more precise dimensions on the two axles. It use to be on Eric Neyerlin's site, but I can't find it anymore. You might be able to find it searching this site.
-
If you look at the part number it will tell you everything you need to know about the belt. The number of ribs and belt length are in the part number. If you have a belt that is too short or too long, then it is a simple thing to figure out what to add to the part number to get the correct length belt.
Newbee Screw Ups (bolts)
in Trouble Shooting / General Engine
Posted
I don't even trust the excessive torque method of checking bolts anymore.
SAE bellhousing bolts will thread right into an LS block using nothing but one finger on a 1/4 inch ratchet.
Ask me how I know.
After that fiasco I am flat out paranoid about mixing SAE and metric hardware. From now on I check for bolts sizes in a shop manual and put a pitch guage to everything.
And I sure as hell don't trust vendors to ship the right hardware with their bellhousings.