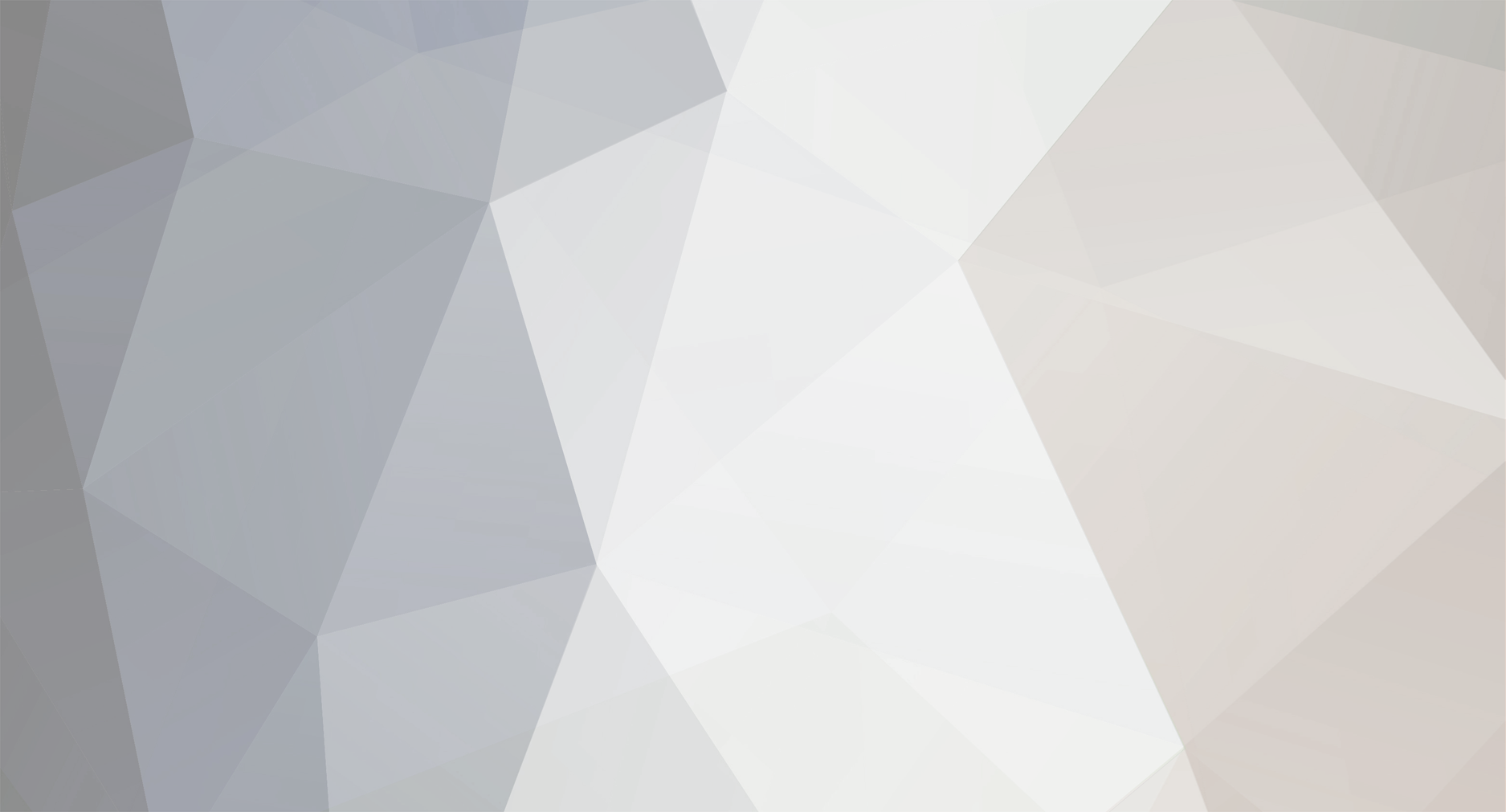
ZR8ED
Members-
Posts
967 -
Joined
-
Last visited
-
Days Won
1
Content Type
Profiles
Forums
Blogs
Events
Gallery
Downloads
Store
Everything posted by ZR8ED
-
Disclaimer. I am not a painter...at least hand painting..robots..another story. A decent Devibliss is MORE than adequate for an average or ameteur painter. Proper spray booth/booth conditions. (heat, humidity airflow filtration) is far more important than ANY gun you choose. As others have stated. Its the painter, not the gun. I have seen rattle can jobs that are high quality show car ready. Stunning really. I have a crappy compressor, that forced me to use a smaller detailing type gun, and with a spray pattern no bigger than 2" I managed to paint the back half of my Z in my buddies garage, and it turned out pretty good considering the conditions. Why I'm posting though is in another direction altogether. Becareful about spending big $ on guns for solventborne materials. There is a strong push going on by governments to reduce VOC emissions, and converting to waterborne technologies has already begun. Many OEM's have already converted to waterborne as they build new facilities (old solvent borne plants are exempt for now). Now the guns are not drastically different, but there are some differences with waterborne capable guns, so if you have not converted to waterborne paints, I would hesitate having big $ guns. BTW there will be little choice in this conversion to waterborne, as it will be illegal to mfg solventborne paints, and paint companies will eventually stop mfg/selling them altogether. I don't want to get into the politics, so I will just leave at that. Have fun painting! Scott.
-
Ok you know how I feel about black... But. Paint the flares/airdam/vents green. Lime green with black is too strong of a contrast. The black looks better with darker colour. I know Myron's car looks good, and its black and white, but black and white is a bit of a different situation. (both are neutrals) Black airdams on a non black car look "bolt on" unfinished, kinda low budget racer, old skool, rat rod. Pick your term. Not insulting, but it is a "look" Just like how I am removing my lawn edging air dam extension. Good luck with your choice Scott
-
ZR8ED Two Piece Belly pan project
ZR8ED replied to ZR8ED's topic in Windtunnel Test Results and Analysis
Ok still no help, so I setup a new "table lift" to hold the aluminum in place while I traced the front curve. With my "power fist" at the ready, I trimmed the pan into its final shape. I have all the flanges painted and installed, and I drilled the pan for the mounting points on the crossmember. Next is to finally paint the airdam, and attach the front pan. Then start work on the second piece of the pan. I have the general shape cutout, but need the main pan to be in place to plan the position of the mounts. I am going to try and work on it this weekend and get some fresh pics up. I should try and get it on a hoist and take a picture so I can show a before and after shot of the pans. -
How about dig a hole? Just kidding. You said not talking about lifts or big ramps. I have some 3 ton stands (I think) and I can barely get under the car with my creeper. Not too bad without. 5-8 and 180lbs. I would like to get one of those steel ramp kits, like some guys on this site use. It gets the wheels 12" off the ground. Plenty high enough for me. I had a friend that had a pit at home, and it was great for quick work on the car. Pits are illegal now (depending on your area) so its not much of an option. I had always though a "trench" could be useful..you know maybe 8-12" deep. Like Indy uses to make his way under the tandem axle army truck using his whip. hehe Scott.
-
ZR8ED Two Piece Belly pan project
ZR8ED replied to ZR8ED's topic in Windtunnel Test Results and Analysis
Hey Evan. The stuff I'm working with is 300micron/40 thou. Plenty strong enough. This is the same thickness as the previous pan, and it lasted very well. Once it was mounted, it was plenty secure and didn't flex while driving. I was working on it again tonight. It is still raining here, so too damp/cold, so I started the mounting flanges. I created cardboard templates and then fabricated them from the same 40 thou aluminum sheeting I have. This completes the flanges I need to mount the pan. I just need to trace the front curve the airdam, and then I can mount it all up. I will start the second piece of the pan once the main pan is fully mounted. Its amazing how long it can take to create 4 flanges! The second part to the pan will likely be a challenge to mount, as I will only be able to design the mounts once I trial fit the pan. -
ZR8ED Two Piece Belly pan project
ZR8ED replied to ZR8ED's topic in Windtunnel Test Results and Analysis
Well the paint got put off a bit. Too humid to paint effectively. I did manage to paint the backside of the airdam (not worried about a sag back there) to protect the new fibreglass. So I turned my attention to the shiny piece of aluminum in the corner that has been waiting patiently to be turned into my new pan. I bought the piece oversized (64" x 38"). I need some extra hands to help me trace the new curve of the airdam (I don't want to construct a new stand/table to help me place the aluminum so I could do it myself) The part of the belly pan that orginally stopped at the crossmember will remain the same shape, as I need the same clearance for the wheels to turn left and right, and the suspension to move freely. I will mount it in the same location on the crossmember, so I used my old bellypan to draw the template "up to" the airdam. I simply measured and laid it on top of my new sheet of aluminum and traced it out. This will give me the cutout required so I can place the new pan under the car in order to trace the new nose shape. (its a big piece of metal) Once I get some help to trace the front edge, I will get out my shears (which worked perfectly cutting the curves for the wheel/suspension clearance.) and cut the new front curve, and begin constructing the mounts. I have 5 specific mounting points so far, with 1 more I may try to give it some extra rigidity. Crossmember- 4 screws (like before) two imbeded SS bolts in the front edge. two tabs on the side of the airdam at the wheel well opening. I have an aluminum flange that is part of my radiator opening blockoff plating (I have a completely sealed wall at the front rad supports with holes cut for the rad opening, and i/c pipes) I can use this "flange" to mount the pan to as well. Then to keep the pan up against the lower airdam, I will use screws. they will not be to secure the pan, but more the keep the front edge uptight to the airdam. I'll post more pics once I get the pan cut and begin the mounts. -
ZR8ED Two Piece Belly pan project
ZR8ED replied to ZR8ED's topic in Windtunnel Test Results and Analysis
Ha ha ha. Just as I should have expected. Custom work on a car/project takes 3 times as long and 3 times as much money as planned. I've been pretty good about estimating the cost, but I should have known better about the time it takes. Well here is a new update. I have completed the flare/airdam extensions, and they are ready for paint. I ended up making them from solid fibreglass, as they are small enough, that it was just easier make a mould, and then sand the pieces to fit. I know its kinda cheating, but making custom shapes is not easy. I layed plastic wrap on the fenders to act as a release, then made a mould using carboard wraped in more plastic wrap, and then mixed up some resin and fibreglass strands, and used a putty knife to fill in the mould. I will paint a first coat on everything today, and start cutting the belly pan. As far as cost goes... Aluminum sheeting 90$ fibreglass supplies 60$ sandpaper supplies 10$ expanding foam 20$ Primer and paint.. 40$ This pic shows the extensions sitting in place. I will mount them to the aluminum sheeting backing plate that I made, that screw into the airdam, and the inside of the fender. I managed to figure out a way to make it "bolt on". -
Wow this is an old post! Still relevant though. My spreadsheets are still ongoing mine are not as indepth as others have stated about theirs. My initial problem was I attempted to capture using reciepts, hand written notes, and a few chats with my long time z mechanic friend, to go back in time. I built the sheet in the early 2000's, but I have had the car since 1989, so there was a lot of back filling as best as I could. I use a single tab for each year, and try to fill in "what was changed" "Was change a repair or repair/upgrade" and how much including labour if performed by my mechanic. I still use the same spreadsheet layout, but I should make it a bit more elaborate, as my excel skills are far beyond what they were when I built it. I don't use a spreadsheet to specifically capture "what I broke", but I do often write articles for my club newsletter summing up "what I broke this year" Some laughs at my expense..sometimes big expense, but I hope people find it amusing, and maybe learn from my mistakes.
-
Well I will post a "stick the l24". quickly swapping in a l28et, pluging hoses, cutting wires is just adding complexity to troubleshooting on the road..or the side of the road if it happens. Many "running" engines do not run so well right away after a swap. Broken wires, bad connections, stuck bolts etc all will play a factor, and you may not even know about them right away. There are a lot of things to get done, and a motor swap is not a priority (assuming the l24 runs/sounds ok) Holes in floor, lights, wipers, signals, speedo/or tach (watch out for state troopers) You don't want to get pulled off for an unsafe vehicle. Turbo motors are easy to sell, and bring $ to your project. I took my Z (with l28 with SU's on it) on my honeymoon 1200 miles roundtrip, with only one issue. A float bowl needle valve got stuck open. Pulled the cover, blew air through it to get the dirt out, and kept on driving. I should have replaced the fuel filter before I left. Doh! Lastly. Take it easy driving it. Suddenly flooring it could burst a hose/belt etc that "looked ok at the time" Final note. Bring a bunch of tools, some wire, ducttape, fuses, bits and pieces (nuts/bolts, screws, lightbulbs) It is amazing what you can jury rig to get yourself home, or at least to a parts store. Good luck! Scott
-
What makes you think that the "falling flat above 5k" is ignition related? Sounds like you have some tuning to do on those carbs. PM if you want some weber tuning help. Good job! Scott.
-
small flaps in front of the wheels?
ZR8ED replied to hoov100's topic in Windtunnel Test Results and Analysis
Small "flaps" like that would be easy to install on a belly pan or incorporate them into it (cutting and bending in an angle) Attaching them using rivits would be pretty easy, and you would be able to remove them if they didin't work out well. I would not place them at a 90 degree angle to the pan, but you could put a slight angle to it. If you placed them like in the diagram, they would be at the trailing edge of the belly pan, and thus close to the wheel, so the reduction in ground clearance would be less of an effect as it would be if the whole pan was lower all the way to the nose of the car. (does that make sense?) Might work pretty good on a street car that can't run a pan lower to the ground, though Mark is right about this not being fully utilized by a street car. So what. Want to add some aero to your street car, go for it. May not pass the "bang for your buck" mods, but it sure is interesting to work on. Scott. -
ZR8ED Two Piece Belly pan project
ZR8ED replied to ZR8ED's topic in Windtunnel Test Results and Analysis
Small update. The weather outside is beautiful, and it is easier to relax in the pool than get dusty in the garage. (It is going to be a lot of work to clean the garage after this) Dust is EVERYWHERE. I got some touchups completed on the airdam, and it is ready for me to reprime. I have the underside cleaned up and as smooth as I think it needs to be be. I have taken the car down off the stands, and it looks MEAN...er. I started to fab up the "mini" flare extensions that will continue the sides of the airdam up the fender. I am using cardboard for this part, and working on the mounting points as well. Once those two pieces are complete, I will breakout the spray gun and shoot some black. THEN I will build my aluminum pan template. I have used my old pan as a guide to help me visualize the new pan. I am going to mount it underneath the "lip" and bring it to the edge, and not extend it like a duckbill. My timeline is being extended with "while I'm at it" but I am seeing the light at the end of the tunnel. Not sure how I will paint the front end with the dusty condition in the garage. I may take it to a friends house, or maybe just "go for it" and do an early morning spray out front of the garage. I'll play it by ear because it would likely take me a day or three to get the garage acceptable again to paint in. -
ZR8ED Two Piece Belly pan project
ZR8ED replied to ZR8ED's topic in Windtunnel Test Results and Analysis
I can't mount it above the "new lower edge", but it would have been a good idea. I may consider a "duckbill". I will play with the old belly pan and check it out before I start cutting my new pan. Here is a crappy drawing of a sideview of the airdam. Black line is old, red line is the add on. I am looking forward to finishing off this part and get back to the sheet aluminum work (which I prefer because it is easier to hide any mistakes hehe) Anyone opinions of using rockerguard materials/paint? I already pick up chips easy with the fibreglass airdam, and I"m thinking of using some of this stuff to protect the lower edge...Now that I don't have my disposable lawn edging. -
ZR8ED Two Piece Belly pan project
ZR8ED replied to ZR8ED's topic in Windtunnel Test Results and Analysis
I got back to glassing the underside after reconsidering my design. In the past, the belly pan mounted to the back of the airdam. The "stock aftermarket" airdam did not have much of a lip on the underside. My mods have the "lip" with a smooth (working on getting smooth) underside, which is approx 2-21/2" wide. I was planning on mounting the pan to the backside just like before, which is why I was shaping the backside of the air dam to have a smooth edge to make my tracer. What i am thinking now is if I spend a bit more time on the underside, that flat edge would make a nice mounting point for the aluminum pan. In other words, the aluminum would butt up against this "lip" I will still use my imbeded bolts to secure it, but then looking up from the ground to the bottom of the car, the pan would cover the bottom lip of the airdam, and there would be zero gaps/transitions. The only concern I have is that water may get forced in between the airdam and the aluminum, and just sit there. I may not rust, but trapped water is not a good idea. Another minor concern is that looking from the front of the car, you would see the front edge of the aluminum pan under the airdam. This would force me to ensure the aluminum stays nice and flat and/or I may have to use a thin strip of moulding to give it a finished look. I have used some thin door gaurd edging with my aluminum metal work, and it looks pretty good. I will keep working with this in mind and fall back to my original plan of starting the pan just behind the lip if I can't get it to work. -
ZR8ED Two Piece Belly pan project
ZR8ED replied to ZR8ED's topic in Windtunnel Test Results and Analysis
Well I finally had some time to move ahead with the project. I've got the airdam smoothed and shaped to my liking. I have given it a shot of primer so I can do some of the final spot touchups. I am still glassing the backside of the airdam, so I can get an even shape to mount the belly pan to. Working on the backside has not been easy. Its very awkward, and I can only work on a bit at a time until it dries. Once I get it cleaned up, I will paint everything, and then build the "flare extensions" I've been planning how to build them, taking what I now know, and improving on it. They will be constructed from aluminum with more foam to make the shape, and fibreglass to make them solid. They will be "bolt on" It may not look like it has changed much, but here is an updated pic. -
Uh. The other way around dude. He wants to put 195/60's on his z and take off the 195/70's Equals smaller diameter, speedo reads higher than actual, a bit more zip off the line, and higher revs on the highway. Scott.
-
ZR8ED Two Piece Belly pan project
ZR8ED replied to ZR8ED's topic in Windtunnel Test Results and Analysis
Well this custom bodywork is tedious stuff. I have completed the glass work, and am working on filling and shaping, and sanding, sanding, sanding, whoops too much sanding, filling, sanding. Well you get the idea. Progess is slower than thought, but going ok. Getting the shape going up the sides towards the lower fenders is very tough. It is all curves, and is hard to get it right. I'm pretty busy with work this week (happy to be working these days) so I will try and get some new pics up later this week. -
ZR8ED Two Piece Belly pan project
ZR8ED replied to ZR8ED's topic in Windtunnel Test Results and Analysis
260DET: At this point in time, my suspension has a slight rake to it (lower in front) not much, but it is there. With that in mine, I am shooting to make the pan parallel, but using the assumption that the car is sitting level. I have the car off the ground, so I can't measure using the ground as a reference, so I am using the frame rails and crossmember to determine "level" with the crossmember. So once the car is back on the ground, it will be slightly lower in the front.. maybe a half inch (over the length of the car.) so the rake will be no more than 1-2 degrees (guessing) -
ZR8ED Two Piece Belly pan project
ZR8ED replied to ZR8ED's topic in Windtunnel Test Results and Analysis
No major updates. I finished laying the glass on the backside, and have a bit more to do on the underside. I can only work on a bit at a time, because I am working underneath the car, and I don't want any of it dripping on me, or me bumping into it, so I am only working on one half at a time. Just looking through my posts, and this thread so far looks like it should be titled "customizing an aftermarket airdam". But this aero stuff is like Mike Kelly described. It is a "system", and this is turning more into a "front end aero" project. But this needs to happen, so I can mount the bellypan at the correct height. That height is the main crossmember. The pan will pass under, and it is also used as an attachment point for the pan as well. The airdam as it was, is not close enough to the ground. This should be a note to anyone else who wants a belly pan like I originally had, or am currently creating. My original pan mounted approx 3/4 of and inch higher than the lowest point on my "lawn edging strip" I still laugh when I say that! That measurement, put it at the same height as my crossmember. The addition feels just about as strong as the rest of the airdam, so I'm getting close. I will probably pickup the aluminum I need this week. I have imbedded a few ss bolts into the airdam (sticking through to the backside. tightend with a nut and then glassed over just leaving a ss stud showing), and will use them to attach some kind of bracket that the pan will mount to. I am designing this to make removal for servicing the engine as easy as reasonable. -
I really like it. Simple and functional. Does this actually make them "canards"??? I'm doing something similar in the wind tunnel forum. See pics. I am doing mine in two pieces, as i am making mine from fibreglass, and want to be able to remove the airdam from the fender (don't want to bond them together) Yours needs to move up about two inches, then run it straight down (perpendicular to the ground) In other words, it needs to stick out a bit futher than your mockup. I love the makeshift template. Cardboard is our friend. If you are at all worried about the look, spraypaint the carboard and look at it for awhile...Then look at it some more. Don't rush it. Cardboard is easy to recut till it looks just right. Goodluck! Scott.
-
ZR8ED Two Piece Belly pan project
ZR8ED replied to ZR8ED's topic in Windtunnel Test Results and Analysis
I'm still laying fibreglass cloth. I have improved my technique, and I'm finding it a bit easier to "add on to" and "build up". Last night I cut the cloth into smaller pieces, mixed up more resin, and got underneath the car, and began glassing the backside of the air dam, and in a few sections, I was able to wrap the cloth all the way around to the front. I have not completed the underside (facing straight down) That will be fun. Oh I learned something as well. Test a larger area. It appears that activated resin kinda soaks in and softens up the foam a bit. Not a disaster, but I think I should have skim coated the foam with some type of filler/putty. Oh well not the end of the world. I haven't taken any more pics because it doesn't look like it has changed much. I will take more pics as I complete laying the fibreglass cloth. BTW use gloves when laying glass.. lots of them. I had the latex type of gloves, and I changed them often. It helped keep the work area clean, as strands of glass come off the cloth as you handle it, and you can change them quickly if you "need" (read run out of) cut pieces of cloth, and need to cut some more before the resin hardens. Sure is messy sticky stuff. I hope to be ready for paint on the weekend. I should have this wrapped up by the next weekend. I am only able to get out into the garage a couple of hours a day at best, but it sure feels great to work on the car again. -
ZR8ED Two Piece Belly pan project
ZR8ED replied to ZR8ED's topic in Windtunnel Test Results and Analysis
Well, I've called it quits for the evening. I've done the last of the sanding of the foam, and I mixed up some resin and laid a bunch of cloth tonight. It does look a bit messy, and I quickly learned to stop touching the cloth after placing it. Wrapping it around the edges, and going underneath proved tricky, but I found a sneaky solution. I grabbed some tacks, and used them to "pin up" the cloth to the foam until it hardens. I'll check it out tommorow. I haven't decided to keep up with the fibreglass cloth, or switch to the fibreglass strand filler. We'll see. I'm not sure how strong to make it. I will use the fibreglass cloth to wrap around behind the airdam to give it additional strength, and the rest will be supported with the belly pan. I will skim coat the entire thing with strand filler, to build up low spots, and then I will switch to a putty type filler (i haven't decided what to use yet.) Thanks for the support! -
ZR8ED Two Piece Belly pan project
ZR8ED replied to ZR8ED's topic in Windtunnel Test Results and Analysis
Stage 3. I have removed the table, and I now have a nice flat edge. I spent a couple of hours measuring, looking, sanding, measuring looking, sanding, and looking some more. The more I look at it though, I don't know why I'm so nervous. I have been looking at the original airdam, and it is not exactly perfect, so I don't feel as pressured to make it perfect to the millimeter. Plus or minus a mm or two is not going to be noticeable..at least no more noticeable than the less that perfect "bolt on" airdam. I have now added a bit more foam to some of the airpockets, and when cured, I will start laying the glass. I have tested the foam with some of the resin I will be using, and it doesn't appear to eat it, so it looks like it is a go. I was thinking of my options if the resin disolved the foam, but I lucked out. Something I have learned so far. I should have used the plastic rap to cover the platform to ease removal, and I should have also used it to wrap the cardboard that I used to make a backer for the foam to shape to. I needed to get creative to remove some parts of the cardboard, and i will have to shape the backside of the foam to make it look neat under the car. -
ZR8ED Two Piece Belly pan project
ZR8ED replied to ZR8ED's topic in Windtunnel Test Results and Analysis
Next update. I have begun shaping the foam using a drywall knife, which is pretty quick, and gives me a basic shape. I am now switching to heavy grit sandpaper to get it a bit closer. This pic is after using the knife. It is a bit more difficult than I thought. I'll keep sanding, and then i will refill any of the airpockets that are in the foam, and then sand sand sand. Then I will get into the glassing. It is much easier to sand this stuff, and get it as accurate to the shape I want. -
ZR8ED Two Piece Belly pan project
ZR8ED replied to ZR8ED's topic in Windtunnel Test Results and Analysis
LowCarbz. I did not construct that belly pan, but it is a copy of mine. I'm not sure I ever saw the final installed product.. It was a long time ago. Scott.