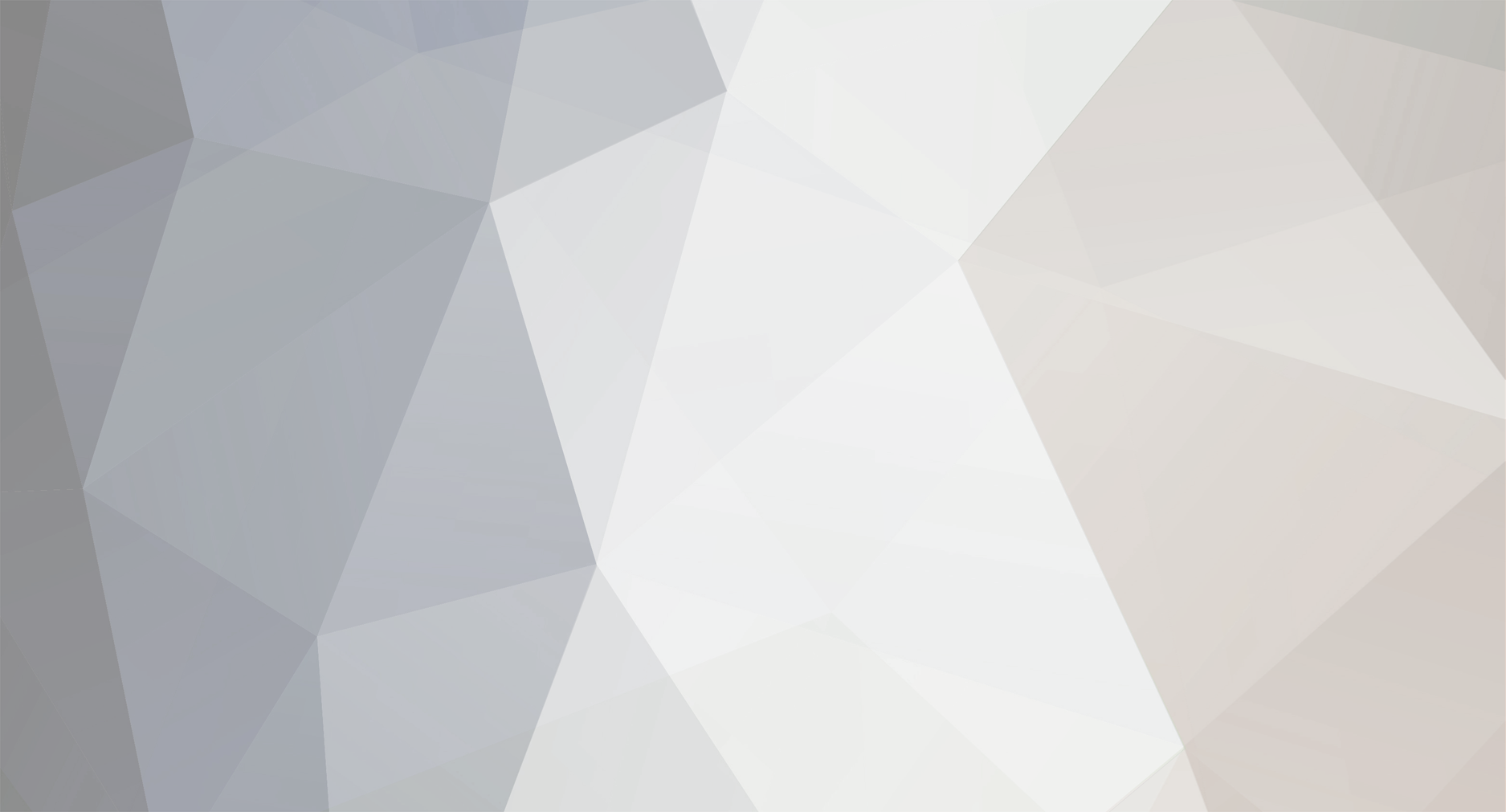
wingwalker
Members-
Posts
64 -
Joined
-
Last visited
-
Days Won
3
Content Type
Profiles
Forums
Blogs
Events
Gallery
Downloads
Store
Everything posted by wingwalker
-
Five years later--a 280Z project
wingwalker replied to wingwalker's topic in Gen I & II Chevy V8 Tech Board
rxx2rxx2 The JTR mounts placed the engine low enough for a stock hood (this one is off a 240Z). I fretted about it, but even with that rather large air cleaner, it clears nicely. JTR makes a pair of spacers that lift the front end in relation to the front crossmember for more under-hood clearance, and I purchased those. But I didn't need them. -
A little over five years ago I joined this forum, having just purchased a stalled project, a 280Z with a partially installed small block. When I started, I'd have guessed six months to a year until it was on the road. But as I dug into it, I found I'd have to undo much of what had been done. And I found rust--a lot more than I saw when I bought it. The transmission was an old-looking 350 automatic, a three-speed, and I wanted a fourth gear so it would cruise at a reasonable rpm, rather than scream. I bought a 2004R and rebuilt it over the winter--a nice project for the heated part of my shop. I bought motor mounts from JTR and scrapped the front mounts that the engine had been sitting on. There was no rear crossmember; the tail of the old 350 tranny had been sitting on the exhaust pipe! Along the way, I received a lot of help and good advice from folks on this site. Thank you again. All good advice. I did all the body work, which took a ton of time. The battery area was eaten up, so I had to rebuild that and part of the firewall. And acid had dripped down onto the lower passenger side of the front fender (on the inside) and eaten a hole there. I eliminated the side markers and holes from the rear bumper to smooth the car up (which required a lot more welding). Accompanying photos will tell the rest of the story. in other posts under my moniker, are write-ups on some of the efforts that went into this thing. I knew the engine was either a crate engine or had been built by a very good shop. It had never been run until I started it recently, but I have no other information on it. I pulled the rocker covers and discovered new roller-rockers, so that told me the heads had been done and likely the cam was an upgrade. Along with the car came a new (in the box) Holley 670 Avenger, and the intake was aftermarket. I was not, however, prepared for the aggressive cam in this engine. Yikes. Very lumpy, and it revs very quickly. There are still issues to sort out. The headlights didn't work properly, and after many hours I traced that to a loose wire in a relay socket. The turn signals didn't work, and that turned out to be because the new flasher unit had worked itself loose in its socket. The Holley 670 carb doesn't deliver enough fuel when I put my foot into it, so I've bought a larger accelerator nozzle to try to keep it from stumbling (but haven't yet put that in). The Holley website says that's an issue in lighter cars--that the accelerator pump system as delivered is dialed in for heavy vehicles. The Vintage Air air conditioner doesn't work, so I need to have the refrigerant pulled out in order to troubleshoot (I'm going to have a shop do it). And the tach doesn't work, so I need to pull it and see what's going on. Maybe another loose wire or something else simple. Other than that, everything else works fine. It's scary fast--too fast for a guy my age (I'll turn 80 this July). I'll post a few photos below. The bottom two are as it sat when I bought it. Lots more rust than meets the eye--all properly patched now. I have painted my recent projects until now, but this was done by a local body shop. I then did all the cut and buff (and it still needs a final buffing, then after it warms up and the paint has hardened more, I do one more swirl removal and wax it.
-
Yep, Rossman, it's a jokey name for what turns out to be a very cool town. We moved here in 2004 from California (and Mexico before that), where we had lived and cruised aboard a sailboat for two and a half years. In the mid-1970s two hobby wine-makers discovered that grapes grown on what formerly had been Walla Walla wheat land (and later on rocky hillsides) produced wonderful wine grapes. Now there are some 120 world-class wineries here. One recently had a red judged best in the world (in London judging). So, this has become the Napa of the Northwest, and with this has come fine restaurants and lodging. I ran a wire from the "tach" post on the HEI directly to the tachometer feed, and nada. Dead. Then I noticed that the needle is stuck at about the 800rpm spot. It should fall to zero, so I think the that gauge itself is toast. I'm going to move on. I don't need that input to drive, and I do want the car painted and the interior finished so I can use it this summer and fall. Later I'll likely replace the dead tach with a Speedhut gauge. Maybe the rest of the instruments at the same time. Thanks for checking out the book. I'm rather proud of it, since it has garnered some great reviews. And, along with some of the guys mentioned in the book, I've been invited to sit on a panel at the annual Tailhook Reunion in Reno in September. Theme of the reunion this year is the Vietnam Air War. I got in 137 combat missions, but the other pilots on the panel were all over 200 (and they managed to not get shot down). I have already purchased plane tickets for my wife and me, but I'm thinking it would be great fun to drive the Z down to Nevada from here--it's about a 10-hour run. I'll need to hustle to get her painted and finish the interior by then.
-
Fridge Gnome, I should respond to your post of last year. Urged on by you, I bought a 140-amp alternator. Then I went to a chart that told me I was way short on capacity of the alternator wire. And as mentioned, my alternator is on the wrong side (air conditioning considerations drove this). So this distance required far heavier gauge wire to the alternator. More wiring hell. Nothing is simple when you start making changes to these old cars (hot rodding, we called it back in my day ... and yes, I'm a geezer in his 80th year). At any rate, I was pleased to see the generator was charging properly after I started the car. By the way, one of the reasons for the extended length of this project is that I spent a great deal of time finishing a book on my exploits (and shootdown) as a Navy pilot during the Vietnam Air War. That book is finally out in hardback, paperback, e-book and recently as an audiobook. Reviews have been very favorable on both Amazon and Goodreads. It is titled Return to Saigon, and it is available through bookstores, Amazon and other outlets. Check it out. Like the 280Z V8, it's a project I'm proud of. I'll solve the the tach issue, then it's off to the body shop for paint. But, whoa, have you checked the prices for paint lately? Around here, all the shops are super busy with insurance work, so they are quoting prices ranging from $6,500 ("if it doesn't need any body work") to $10K. Yikes!
-
JHM. that does help. Now I just need to know where to hook up what. On the HEI there is a tach terminal, so I'm assuming a wire directly to the tach from that? Does it need to be switched or any other deviation from a straight line? Forgive me, I know little about wiring (even after wiring two cars--but then I always had my dad to advise me ... but he's gone). Is that one wire all that is needed (in addition to lighting), or is there a source of power involved? And if anyone wants to draw up a schematic, I'd be forever grateful--or at least grateful for a very long time.
-
I have made a bunch of progress and have the car running (and what a lovely sound that aggressive cam gives the engine as its exhaust blasts through a Flowmaster). Wiring is my weak area, so I was pleased with the following: 1. Started on first crank 2. Did not smoke anywhere 3. Did not blow any of the big fuses replacing the fusible links 4. And I was thrilled to see all the gauges actually working (I didn't try the lighting for them or the lights on the car). However, the tach doesn't work. Nada. I tried to follow the book as it pertains to HEI, but as I've written before, the wiring on this car had been butchered. This means I very well may have grabbed the wrong blue wire or the wrong black/white wire (or both). So I want to bypass the existing wiring and go directly from the HEI to the tach. And I know I need a 15k ohm 1/2 watt resister in there somewhere. Can someone please supply me with a simple schematic, maybe suggesting where I can pick up switched power as needed? Thanks P.S. I'm finishing the body work (block sanding in 100+ degree heat) and now trying to line up an affordable painter. The interior is all restored and ready to be installed after the paint--so the end is in sight. Whew. I started this in 2017--a long, hard process. But fun.
-
Front fender scraps from a flare installation
wingwalker replied to wingwalker's topic in Body Kits & Paint
Thanks to all of you for the generous responses. Walkerbk, you are closest, and since we get over to your side of the state a few times a year, I'll contact you before we make our next trip. I'm of course running slower than hoped on the body work, so it may be a month before I get back to you. Again, thanks to each of you for the responses. -
Do you still have the air dam for sale?
-
Front fender scraps from a flare installation
wingwalker replied to wingwalker's topic in Body Kits & Paint
Thanks, AydinZ71. I'm hoping to finish body work soon. Any chance you might move up the timeline for the front fenders? Or is there another Z-person out there who has recently done it and still has the trimmings? -
If you are installing flares on the front of your Z and have to cut away part of the fender. I'd be interested in your scraps. I have a 280Z that I'm doing body work on now, and find that a previous own cut away the edge of my front fenders to clear some aftermarket wheels with fat tires on them. I can't find patch panels, so believe your scraps may be my answer. I'm in the Pacific Northwest (Walla Walla), so nearby would be great. Let me know. Thanks.
-
I'm pretty sure my alternator has a bad diode, and it's only 65 amps, so I plan on replacing it. I just ordered a Vintage Air a/c and intend to add a hefty sound system--both of which will require more power than the stock 280Z ate (the a/c and heater uses electric servo controls rather than vacuum that the stock system used), so I'm thinking of ordering a 100-amp or larger alternator. The choices are overwhelming. Anyone care to steer me to the right choice? Cost is a facotr.
-
Rear end and driveshaft woes
wingwalker replied to wingwalker's topic in Gen I & II Chevy V8 Tech Board
The proper U-joint flange from JTR (the DAT-110-2 flange version) arrived in the mail--a nice piece, and I swapped it out for the improper one the previous owner had on it. Mated perfectly without any drama whatsoever. Tightening the four bolts that hold the flange to the differential is tedious, with two open-end wrenches achieving about a 1/16th turn at a time, but it's in . I finished rebuilding the brakes yesterday with the help of my son (who drove over from the Seattle area, about five hours from here). Wonderful father's day gift--two masked men getting grimy doing brakes on a car precisely as old as my son. When we flushed the brakes, we used up almost a liter of fluid until we achieved clear stuff--it was nasty stuff. Glad I replaced the master, the calipers and rear brake cylinders, along with flex hoses. Should be a tidy-clean system now. Miles, you asked if I have a JTR manual. I do, and it has been a great help. But on the drive-shaft issue I didn't refer to it, since all I was doing was putting a part I had taken off back on. I am still astounded that that the previous owner was driving and racing with a driveshaft improperly mated and fastened. It depended on nothing more than the shearing strength of the four bolts--not the strongest way to use a bolt. Also, the flange had to have been misaligned. Must have vibrated like crazy! But thanks for the reminded; I plan on going to the manual as soon as something seems amiss--even if the P.O. had been using it that way!- 13 replies
-
- companion flange
- driveshaft
-
(and 1 more)
Tagged with:
-
Rear end and driveshaft woes
wingwalker replied to wingwalker's topic in Gen I & II Chevy V8 Tech Board
Great help, everyone. Thanks. I measured carefully and then spoke on the phone with someone at JTR. It is the DAT 110-2 flange I need. So, another $85.00 into this never-ending project, and I should have the driveshaft and differential properly mated.The man at JTR said they have it on hand, so it should ship on Saturday. With new brakes on all four corners, that should take care of the moving parts needed to move this thing down the road. A close look at the differential reveals no bolts around the axle holes and a rectangular bar across the bottom of the cover. I hope the ratio will be good for highway driving. My transmission, a GMC 2004R, has a decent overdrive ratio in fourth--so I'm not worried. What I want out of this is a nice highway cruiser with pep. I still can't get over discovering that a previous owner ran this car on the quarter-mile, running fast, with only bolts in shear holding the driveshaft onto it. Ignorance is bliss, I guess. I want to get this thing on the road, then I can go back and pull stuff such as the differential, refurbishing what needs it, and cleaning up and detailing as I go along. I have welded patch panels into all the holes and indentations on the rear, so a day or so of body filler, sanding, priming, more filler, more primer, block-sanding and lots of dust lies ahead. Then I'll bolt the gas-tank in after all that mess is finished. I was happy to find that the tank was clean and rust-free. It was in the trunk of the car when I hauled it home, so I expected the worst. I pulled the sender and used a flashlight and mirror to see as much as I could, and was pleased. It's painted, and I have new strap-liners, so that should be an okay project. Next big issue will be the a/c installation. It looks like a lot of work, but all of it appears straight-forward. I have the dash out, so that will help. Thanks again everyone.- 13 replies
-
- companion flange
- driveshaft
-
(and 1 more)
Tagged with:
-
Rear end and driveshaft woes
wingwalker replied to wingwalker's topic in Gen I & II Chevy V8 Tech Board
Thanks, I'll go out and inspect the differential more closely--sounds as if the bolts around the axle holes are the clue. And I need to make some careful measurements to ensure that part is the one I need. Always a challenge working on these old things--especially when some PO had creative engineering notions.- 13 replies
-
- companion flange
- driveshaft
-
(and 1 more)
Tagged with:
-
Rear end and driveshaft woes
wingwalker replied to wingwalker's topic in Gen I & II Chevy V8 Tech Board
New Zed, Thank you. Both links are very helpful. Looks like I need the DAT110 flange, but before I order it I need to go back under the car (for the million and first time) to take careful measurements to ensure it is what I need. My 280Z is a '77 built with auto transmission. The u-joint does disassemble with clips, so it may be the converted Chevy part per the JTR manual. Your first link shows that the flange is on a spline, so I doubt it'll need a puller. And that's good. But nothing is simple. I have the rear drums and brake parts off, so I won't be able to set the handbrake to hold that shaft steady when I go to take the big nut loose. So, I need to finish rebuilding the brakes before I can fix this driveshaft issue. I've ordered a liter of brake fluid that won't be here until Monday evening. I want to use it to flush the lines before putting new hoses and brake cylinders on it. Every step hinges on another, Nothing is simple. Can anyone ID that differential?- 13 replies
-
- companion flange
- driveshaft
-
(and 1 more)
Tagged with:
-
I bought a partially done project--a relatively rust-free 280Z with what appears to be a rebuilt Vortec V-8. Those are the good things I can say. This car had once had another engine in it, the hood had a cutout section where there may have been a blower sticking through, and in the glove box were several drag-strip timing sheets in the 12s (so if there was a supercharger, on it it wasn't all that effective). The seller said that the original engine blew, someone bought it and was installing this engine and then ran out of steam. She bought it and thought her boyfriend could finish it, but from what it appears, he just had her order some expensive parts, including a new aluminum radiator, new Holley 650 carb, new fuel pump and a few other things. I've had to redo most of the boyfriend's efforts, and in other posts, you may have seen the issues I've faced. I am using a different motor-mounts and tranny--a rebuilt GMC 2004R--so the engine sets back. Therefore I had to pull the driveshaft and have it cut down. If fits, but doesn't properly mate with the differential. I've spent three long afternoons under the car, trying to get the companion flange on the driveshaft to properly mate with the flange on the diffy. Never could get the flange to drop in so that the two faces mated. And this is the flange I took off it, the flange that the dragster owner had in place. I'm certain that the machine shop didn't somehow swap out that part, because I marked one corner with a center-punch so I'd mate it as it had been. Finally in exasperation today, I pulled the shaft out for the millionth time and measured the male flange, then went under the car and measured the female cut-out. I was stunned! The driveshaft flange is 157+mm and the machined slot on the flange on the front of the differential is 49mm and change--they never mated! Must have been a vibrating ride--wild and noisy. So, this tells me that the flange is for a different rear end than mine. I am going to include photos with this of the flanges in question and of the differential. I think I read on this forum that a smooth rear cover might indicate it is a R200 rather than an R180. So, the questions are: 1. Can I swap out either the flange on the driveshaft or differential? And if so, which? The flange on the U-joint would be easiest. And I am not taking this to the strip, so it doesn't need to be the most robust. 2. Can you tell from the photos which diffy I have back there? There's the driveshaft--local shop did a nice job cutting it down Here's the flange on the U-joint. If that can be traded out with one that fits the diffy, it would be easiest. Here's the flange on the front of the differential. That machined well is only 49mm and change. If this is the flange that needs changing, do I need a puller? Here's a side view of the differential and below is a shot from the rear. Can you tell me which it is? Thank you in advance for the answers.
- 13 replies
-
- companion flange
- driveshaft
-
(and 1 more)
Tagged with:
-
Are you talking about something sold by John's or outlined in his book? I'm about ready to install A/C and have been looking at Vintage Air Gen. II mini units (the one with heat and defrost), but so far I haven't heard back from the nearby supplier on a few questions. So, I too would like to see photos of solutions and feedback on what works best.
-
Okay, out with the volt/ohm meter. I'll dig in and find something. And after that, on to the brakes. I'm getting close enough to visualize starting this thing.
-
Anyone have suggestions for sources of switched power other than cigarette lighter circuit? I kinda hate to pull that source out to the engine bay, since I may need it for something in the future in the cockpit.
-
Thanks, JHM. Good point about only cooling the fluid in the radiator. Maybe there would be some block cooling due to percolation (the strategy the early Model T Fords used), but for a big hunk of iron like the GMC V8, probably negligible. So it makes sense to look for switched power. I can pull it off the cigarette lighter circuit, but are there other sources folks use?
-
I'm back at work on this project, and nearing the end of wiring hell--but I have two issues hanging and would like advice. If this C-19 keeps me close to home for a couple more months, I just may get this thing on the road. I'll post a couple photos that show how I solved the earlier issue. I used a heavy-gauge wire and ran around the front. It's protected and out of the way. And I got rid of the fusible links with four robust fuses per some write-ups in this forum. I mounted four relays for high and low beams, ignition and starter. I was about the wire in another for the electric cooling fan, when my searching showed me that I'll need to tie in the air conditioning compressor--so I'll wait until the Vintage Air system is on hand.to do that. But I also should put a relay in for the fuel pump. I'm thinking of mounting that relay on the firewall and using the existing wiring to run power back to the fuel pump (and in fact I've mounted the pump and wired it into the existing 280Z fuel pump wires). I can tap into the ignition wire at the HEI (since it is switched) for that relay , but I also have a source of +12 that is always hot that I could use. And why I am thinking of using that constantly-hot source is that with the car shut down on hot days, the fan will continue to run until the thermo switch tells it the engine has cooled to the set temp. When it opens, the fan will shut off. My former fun-car, an Alfa Romeo, would do that, and the setup never ran down the battery. Thoughts on this? That's the first question. The second has to do with the electric cooling fan. I read somewhere that it isn't good to pick up power from the ignition side, and instead I should use the Aux feed (Cig lighter?). I think that the reasoning was that as the fan costed down, it would feed power back into the circuit and keep the engine running for a little extra time as it acted like a generator using its inertia). I could use that always +12 source mentioned above and depend on its thermo switch to shut it down. Let me know problems with either of those scenarios, please. And if I might throw in a third question, other than the cigarette lighter, where else might I pick up switched power?
-
These projects take time, so if you are paying the mechanic, and insist on doing all you've outlined, I think labor will eat up all that budget and still not be done--with the parts to come on top of that. I'm working on a 280Z with a 350 engine that someone had tried to drop into it (I've had to redo almost everything). I'm using a 2004R tranny (beefed up to handle a lot more horsepower than my engine will ever produce). I've had to refurbish the dash--they are all cracked, so expect that. I'm going to order a Vintage Air A/C this summer. I had looked for a car with the factory A/C, which mine has, but as I removed it, it was clear it would take a lot to bring it to life. I'm pretty sure the Vintage Air will be easier and probably no more expensive. Body work and paint will also eat deeply into your budget if you have that done. I'm doing some of my own (I have experience). Just to put this in perspective, my last project was an Alfa Romeo roadster. It had solid rockers and floors and appeared to be rust-free, but I still found rust. And after I stripped it, I found two past fender-benders that had been repaired with way too little body work and way too much Bondo. Those had to be bumped out and required some small patch panels. I'm not fast, so it took forever. But a body shop would have insisted on new panels and then would have spent many, many hours prepping and fitting (expensive). I painted it with a former body-shop manager, and together we put 40 hours each into the prep, sanding, masking and painting. I intend to do much of that to my 280Z, and still expect to pay a good paint shop around $4K to fine-tune the prep and shoot it. I'll color-sand and buff it. You haven't mentioned wiring, which will take time and will be expensive. My free advice would be maintain your vision, but do the car in stages. First take car of all the rust you find--and there will be some. I found far more than I expected under the battery tray and had to replace a big hunk of the inner fender and the firewall. Before dropping the engine in, you might just take care of the dash (you almost have to remove it to install new A/C). Then drop the engine and transmission in, upgrade the brakes and do the interior. Before dropping the engine in, you'll want to clean up and paint the engine compartment and do all engine wiring while you can get to everything. I'm thinking just that work would eat most of your budget, unless you do most of the work yourself--and for me, that's the fun of it. Seats are a fun area. There are so many choices. Sparco and Bride both make great seats--but you can spend anywhere from many hundreds to thousands on a pair. I had a good upholstery shop redo my stock seats. Cost was $750 for the pair--which is more than just using a kit--but they came out more modern-looking and very clean. Using the stock runners will save a pile of time and some money. That would get your car on the road. You'll then drive it and discover what you really want. It may be the body kit, and by then you may have the money for it (lots of body work to fit such a kit). You may want to go another way. But after driving it some, you'll know. Either way, you'll then face the expense of paint and any upgrades to the interior, suspension upgrades air bags and other fun stuff. And by driving it, you'll also know how much upgrade the rear end will need. And you do want it on the road. My own project has gone on way too long (life gets in the way--have you budgeted for that? So that's my free advice--worth every penny it cost you.
-
I just downloaded the Tremec Tool Box app. Terrific--saved me a pile of time. And I am certain it is more accurate than the magnet-base angle finder I bought at Harbor Freight. This should be a sticky.
-
Will this alternator bracket clear?
wingwalker replied to wingwalker's topic in Gen I & II Chevy V8 Tech Board
Michael, Thanks for the comments, but when I made one singe change, problems cascaded. I had spoken with someone at Vintage Air, the manufacturer of the AC system I will install, and he suggested that if the compressor is placed on the passenger side, routing of hoses will be easier. So without enough thought, I decided to switch the standard GM configuration. Main issue is that the valve covers are of course staggered, and it is the driver's side that is forward. I do have the long water pump and a newer, shorter version of the alternator, but at you can see in one of the photos I posted on Feb. 23, the back of the alternator hits the valve cover when I attempt to tuck it in. And from there the issue cascaded. Hindsight is wonderful. Had I stuck with GM's configuration--alternator on the passenger side and compressor on the driver's--my life would have gone easier. I have, I think, got it solved, but such is hot rodding--which is what we are doing when we swap engines. It has been far too hot in my shop to get much work done, but I am anxious to tackle the remaining issues and see what other trouble I have created for myself. I want to get this car back on the road. -
Will this alternator bracket clear?
wingwalker replied to wingwalker's topic in Gen I & II Chevy V8 Tech Board
The engine is in and bolted to the front mounts. And it appears my modified brackets will work. Whew! Here are a few photos.