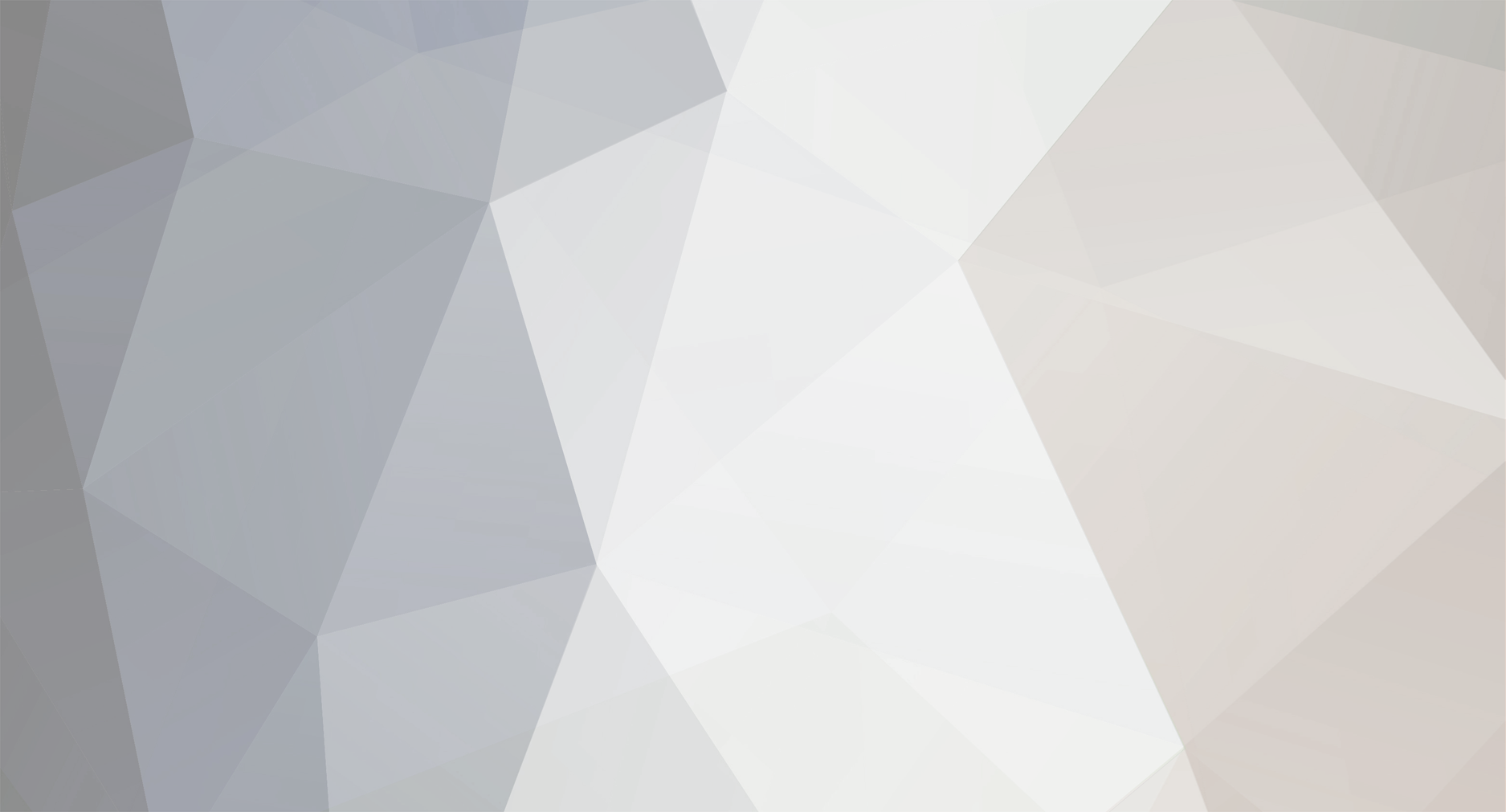
Jolane
Members-
Posts
351 -
Joined
-
Last visited
Content Type
Profiles
Forums
Blogs
Events
Gallery
Downloads
Store
Everything posted by Jolane
-
I noticed that MSA has a replacement rear lower valance panel to replace damaged ones. I did not know this, and only found it while browsing. It is pricey though, but may be well worth the cost compared to fabricating one from scratch ($250)! They also have the panel that goes around the hatch latch area! I wish I had known that a week ago, since I just fabricated half of mine that was rusted through, and was planing on doing the other half this weekend! Always a day late I guess. It is also kind of expensive at $131. At least it would look right and make everything new again! Just though I would let you know. Joshua
-
Floor pans glued in!?!?!? What do I do now?
Jolane replied to a topic in Brakes, Wheels, Suspension and Chassis
Not to insult you, but are you sure that the floor was replaced? The stock floor pans also had this liquid nails looking stuff on all of the seams (seam sealer). It seems odd, although I know weirder things have happened, that someone would have used something like that to replace the whole floor. If they were going to that much trouble, why would they have only glued it in? Again, I am not trying to doubt you, just curious really. Joshua -
Tim, That looks right to me. 16A/3.5HP = 4.57 A/HP 4.57A/HP * 5HP = 22.9A (just relating back to the numbers for 5 HP). Depending on the breakers, time delay seems to be rated for ~3X the rated current on the switch for ~10 Sec to account for starting currents. The starting current can be VERY high just because of the nature of a compressor. An aside. I looked for the PCF and Efficiency of my motor on the nameplate, and did not see anything. It does say 22.5A though on the side. For some reason mine draws more, maybe that is due to the pressure of the tank (as the internal pressure goes up, maybe the motor load also goes up slightly to overcome the tank pressure?) Oh, and mine puts out something like 15.5+ CFM at 175 PSI (on the label). Yes, the big current draw is worth it when running airtools or the plasma cutter for me. So is the noise. Joshua
-
Hood clearance ??'s High rise intake?
Jolane replied to Poundz9oh9's topic in Gen I & II Chevy V8 Tech Board
Silicon Boy, I have the Holley Stealth Ram injection system for my 383. I am not using the JTR mounts, but do have the engine positioned close to where I believe the JTR mounts put it. Although I have not actually put the intake on the engine with the engine in the car, it appears that there is pleanty of room under the hood for it! I have an airgap intake on the engine now. Using the god ol' tape measure it looks like there will not be any clearance problems. Actually, I think that the Stealth Ram will have more hood clearance than the airgap and carb. Eventually, I want to make my own plenum for the stealth ram base, but that is only for looks. If clearance would be a problem for you, you could probably make your own plenum to fit your application. Shouldn't be much to it (with the right tools of course). Joshua -
Crazycustom, I agree about TIG being fun. I just got my Dynasty 200DX up and running last week. I had never TIG welded before, and thoroughly enjoy it. It definitely takes practice though, but I think I have steel down very well now. Now on to aluminum... As for the TIG mate, I don't know what your budget is, but the Thermal Arc 185 (T/A 185) has gotten excellent reviews. It is ~$1680 complete with everything from AAAweldingsupply.com. They have also gotten great reviews. The machine is very portable, and draws little current even at maximum output. I have Miller's version and feel that the small size is wonderful for my garage. I know it costs more than the Tig mate, but you probably won't outgrow its capabilities, especially for auto work. Joshua
-
I think this depends on your own electrical, wiring, and soldering abilities. I bought the relay board and kind of wish I hadn't. I have enough knowledge to wire the connector directly. I can see though that for someone who is not confident in their wiring abilities, it would be worth the cost. It should also save some time. I think that the board itself is nice, but I did not care for the case. I really wish it was fully enclosed. I have not used my MS since I switched gears and decided to go with a Holley setup. I have the MS board, Stimulator, and Relay board (no coating on it yet) completely assembled and fully tested. It was assembled at home on my electronics workbench (anti-statis mat, soldering station, etc). I will not be using it now and am willing to part with it if you are interested. I do not have any sensors or wiring though at this point. Just throwing that out there. If you are interested, make me an offer. Thanks, Joshua
-
Pop N Wood, I broke down today and asked a very knowledgable EE at work about the induction motor thing. I will try to repeat what he said. Basically, there are two factors to an induction motor that have to be taken into account. The first you covered before, Power Correction Factor. He said that should be on the name plate on the motor, but guess that it might be ~85% for a single phase induction motor. The other is efficiency, which is not related to PCF, which is also ~85% most likely. So, 230V * .85 * .85 = 166 V 5Hp * 746W = 3730 W 3730W / 166V = 22.5A Again, the PCF and the Efficiency are factors of the motor itself, and the 1 Phase power. I am sure the HP rating varies with load, so it looks like either my motor is loaded more (Putting out 14+CFM at 175 PSI), or the PCF and/or efficiency are lower than 85%. I guess both are likely. Also, this is for a true 5HP motor, your results may vary. Joshua
-
Crazycustom, Although I have not shaved my drip rails, I have welded a lot on my body patching this, repairing that, etc. I have used a MIG until this past weekend, when I use my TIG. The MIG is much easier in terms of actual welding, but does require more grinding to get it cleaned up. The TIG is great for close fitting parts, but a real pain if there are gaps. I recommend using a MIG with .023 wire and C25. The way I did my patch panel and the quarter panel was butt weld the pieces using 100's of small tacks laid on top of each other. Be sure to tack all along the seems, start at both ends and work around to keep the metal from getting hot and warping. It will work, just go very slowly and have patience. If you use flux core, you will have to clean the welds each time before putting another weld on top. I would not personally use short welds, just due to heat. I would rather the job take 20 minutes longer and be straight than risk any warpage. I hope this helps. You don't really need a TIG for body work (just easier to grind and work with a hammer and dolly really, but fitup is very critical!) Joshua
-
I too am replacing my roll pan. Mine was torn up also, and the whole thing needs to be replaced. The approach I am taking though is a transplant from a good car. I found one in the JY that was good, and took my cordless sawzall with me. It took two trips (4 batteries worth) and some very long blades but I cut the back of the car off. I have since cut all of the structure away from the donar, so all I have it the skin. Hopefully this coming weekend I will cut into my car and make the transplant. I woudl be very interested in seeing pictures of how other people have fixed this area. I wish someone made a replacement panel for it! I guess you could always get a body kit with the right rear panel to replace it with, but I like the stock look on the back. Joshua
-
Jamie, How are you mounting your new hood? I am getting to the point where I need to either strip and repair my original hood, or buy a new one. I really like the one you have. I saw that a frame is available for it (maybe you bought that too) to use the stock hinges. Any comments (or even a picture maybe) about the hinge mounting area. I assume it looks like stock? Finally, if you are using hinges, does it come ready to use the stock holddown hardware? Since I have a SBC, I will need to relocate some holddown hardware (I don't want to use pins). I know this is just rambling, I guess, if you don't mind, I am looking for a picture of the back. Thanks, Joshua
-
Pop N Wood, I also understand what you are saying about the meth. I realize too that the math assumes 100% efficiency. I think though that what the math is missing is the affect of AC, versus DC. I think what you are calculating is for a DC motor. When you have a 1 Phase AC motor though on 220V, I think you only have power 2/3 of the time, since basically you have two legs going to power the motor out of phase by 120 degrees. This is my thought anyways. I relate this to welders. If the same welder is used on 1 phase and then hooked up to 3 phase, the power draw is less on 3 phase. As for being prohibative for most home shops, that may be true. I do have mine in my home garage though, and did not change out the main panel. I am just careful about what I am running at the same time. We use a gas dryer though, which essentially has been replaced with my air compressor load. We do have an electric stove though. I guess the total budget all works out in the end. I did not check the power requirement of my compressor before I bought it. It was a great deal, I jumped, only knowing it required 220V. I thought it would be easy to just use my 20A circuit I had installed for my table saw. What a suprise it was to see that I needed a 50A breaker! I never would have guessed that! Welders can be decieving too! It was also a suprise when I had to unload all 400# of my compressor from the back of my lifted Chevy Truck with little more than 2 wooden planks and my G/F! That was fun! Joshua
-
Hi, I am currently doing the body work on my 72, and would like to find a stereo antenna that is hidden, so I can fill the original hole for it. I never really liked the stock power antenna, and think the car looks funny with any antenna. So, I would like to find a mastless antenna, if possible, to use instead. I do not recall seeing an antenna on a newer Porsche 911, but they must do something right? Does anyone have any suggestions on what I might do about this? My Suburban has the antenna built into/onto the windshield, and I don't think I can get just the antenna separately. If I could get a stick-on to put across the top of the windshield or rear window, that would work great. If a regular antenna is not available, what about a satelitte radio (Sirius, XM) antenna. All I have even seen are the little black boxes. I would really like something hidden, or at least inside the car on the dash or in the rear area. Anybody know how I might accomplish this task of hiding the antenna before I fill the existing hole (I would like to plan ahead). Thanks, Joshua
-
Hood clearance ??'s High rise intake?
Jolane replied to Poundz9oh9's topic in Gen I & II Chevy V8 Tech Board
I am in the process of mounting my engine (actually, it has been mounted for ~6 weeks now) and currently have an airgap intake on it to use with a lift plate. I plan on using the Holley Stealth Ram EFI system for this engine, but that manifold did not accept a lift plate. I am not using the JTR mounting plates/mounts, but I do have the engine positioned as far back as possible and as low as possible (The 6" harmonic balancer is ~1/2" above the steering rack, the small HEI dist is ~3/8" from the firewall). With the engine mounted this way, there would be enough room for me to use the Airgap with my holley carb. I would definitely have to research aircleaners though, becuase it would take something that is rather thin (not a 3x14" style). It does look like it would work though with a stock hood. I know that this may not help, but this is as far as I will be going with the Airgap intake. Joshua -
Oh, I just found a table of motor HP (1 Phase) versus Current. At 5 HP, 230V, current = 28A. I measured my incoming voltage to be ~242V. That would explain why mine draws ~26A. Joshua
-
Pop N Wood, With all due respect, I do disagree about a true 5 hp motor easily running on a 20A circuit. I have measured mine running and it is ~26A continuous with the fluke current clamp. At startup, it is ~116A. I think that the part you are missing in your calculations is what the definition of motor horsepower is. There are vacuum cleaners out there that are rated in rediculous power ratings. True horsepower is what the motor will put out when in a normal running state. Peak horsepower (which most vacuums and compressors are actually rated in) is the horsepower of the motor when the motor is stalled. My compressor is rated for a peak HP of ~11.8 IIRC. I guess I just want to make sure that everyone knows that I have measured mine while it is running, and a 20A circuit would NOT be enough. The manual stated to use a 50A circuit, most likely for startup reasons. Joshua
-
First, Welcome! I will be polite as I am sure others won't. You should use the search function first as there are a number of posts about using a C4 rear end in a Z. It has been done, and has its complications (too wide I believe). Take a look around, and ask questions that cannot be answered by searching. Joshua
-
Hey Datsunlover, I had the rear diff mount break on my 83, and the rubber separated from the steel. I was not sure what the problem was at first, as it only made a thump when I shifted or used my engine for braking. I did not think it would make a big difference either, but when you consider the geometry of the rear subframe, it makes sense. The rear subframe is basically mounted with three points (a proper kinematic mount btw), the two subframe mounts on the cross member towards the sides of the car and the rear differential mount. The rear differential mount controls the fore/aft pitch of the diff and subframe, while the cross member mounts control the roll of the diff. All three contribute to the yaw of the diff. I will say that with my rear diff mount broken, it would slam into the floor and create a very load thump! If this is the problem though is yet to be seen, I think. Joshua
-
When my differential mount broke on my 83, it jerked a lot when letting off the gas, and when shifting, accelerating. Check that rear diff mount while you are under there. Joshua
-
As for coating the inside of the tubes, maybe an undercoating type sprayer would work well. I got one from Eastwood that included wands for getting into hard to reach areas. It also has a few different sprayers, one of which spray to the side of the wand... Just an idea on painting the inside if that was desired. Joshua
-
Congrats on the new addition! You will have a bunch of power to play with. On Sears website it mentioned 3 phase, but on Lincolns it does say that the ready-pak is 1 phase. Did you look at the other power requirements, such as what size breaker you will need? Just a heads up when you are out buying a bottle. Oh, and you might want to have a forklift ready to unload it with... I couldn't believe it weighed that much! I guess the shipping was reasonable then considering... Good Luck, Joshua
-
WOW!!! That seems to be a GREAT deal! Did you see the weight though, 642#? I wonder what shipping will cost on that. Plus you will most likely have to pay tax. Even with those costs though, that is a great deal. Now...what kind of power does that thing require? Am I reading it right that it requires 3 phase, or is that only at 460V? You may want to check into some of these details before ordering. I just got a Dynasty 200DX, and think it is awesome! I really wanted a 300A model, but the cost was too high. Ends up though, after playing with the 200DX, I am glad that was all I got. I will eventually buy a 210/251 range MIG, possibly spool gun, for thicker stuff. I really can't see needing any more power, especially for hobby use. The Thermal Arc 185 is close to the price of that PT275, and taking into account tax and shipping, is probably a few hundred cheaper at ~$1680 to your door. I would definitely look into an inverter if you want small, light, powerful... Joshua
-
Good Choice Iskone! MIG welding is not too hard, but will take some practice to start getting good results. If you are doing sheet metal, just use a bunch of spot welds layed on top of each other. Go slow, ans skip around, to keep the metal cool and avoid warping. What kind of wire are you planning on using? I am using .023 ER70S6 with C25 for the sheetmetal work I have been doing, and so far so good. Good Luck, Joshua
-
Iskone, Yeah, I just got the Dynasty a few weeks ago, and finally got the torch kit last night. Now that I can finally play with it, life is good. It really is a nice machine, well, everything but the price anyways. Now I just have to learn how to weld with it..although it is coming right along and is not as hard as I expected. I would feel comfortable welding steel parts for my car with it right now, up to maybe 3/16" or even 1/4". Aluminum doesn't seem too hard either, although I need to practice more before I feel good with it. Magnum, the 100 on the switch is what you care about. The 10,000 is something else. What size breaker is running your subpanel? That will limit your overall current draw. Compressors really use a lot more juice than I ever thought! I never expected to need a 50A for mine, but that was what the manufacturer specified, and now I see why. BTW, what kind of compressor did you get? Joshua
-
Okay, I will tell you what I am doing, although it may not be for you (I am not responsible either). Actually, you really should consult an electrician first. My setup is: 1EA 30Amp (10-3 Wire) Twist Lock plug outlet installed below my service panel. I then made up an extension cord using the same connectors, 30ft long out of 10-3 SO Cord. This is set up to run my table saw, my Dynasty 200DX welder, and my Spectrum 625 Plasma Cutter. I will never use all of them at once, so it is not a big deal to have to unplug one to use another. My Mig is just a little 110V unit, but when I get a nice big one, I will also run it off this outlet (most likely). I believe that I have overwired this outlet and extension cord. I don't think I had to use 10 gauge since the duty cycle of the appliances comes into play. My other 220V outlet is 50A, and is a separate connector coming out of the wall. This is dedicated to my air compressor. The 50A is required for the startup, which draws ~120A (measured with a current clamp)! Running though, it only draws ~26A continuous (true 5 HP). I decided to put a plug because I thought I might want to use this outlet for a welder later on. The Tombstone arc welders do require 50A I believe. I can see why you would have a large breaker for your welder, they can suck the juice! Without knowing your situation, I cannot recommend a method to hook you air compressor up. At the very least though, mount another box to make your connections to your compressor. Do not connect the compressor wire directly inside the service panel. I would recommend just using the welder outlet you have for your compressor. BTW, the breaker is NOT there to protect the welder or compressor, it is there to protect the wiring between the breaker and the outlet/disconnect! Make sure that the wire is rated for the breaker rating. I believe I used 6 gage for my 50A circuit. Better safe than sorry. As for protecting the compressor, that is the job of the electronics on the compressor (if there are any). Finally, personally, I would NOT use two breaker for you 220V circuit alone. Make sure that the two legs of the breakers are connected mechanically, such that if one legs trips, it takes the other with it. There are little link bars for this, usually preinstalled on the breaker when you buy one. I would highly recommend sorting out your wiring first, and making sure that everything is up to par. Be safe, be careful, as the power in the service panel is dangerous stuff!!! Good Luck, Joshua
-
I said the same thing about my Maxima...I am not going to work on it or mod it if I don't have to. Well, 2 1/2 years later I have changed the oil and added a K&N replacement filter (not cold air). That's all! I decided to spend any money I thought I wanted to use for the Maxima on my 240! It is hard...but it can be done. To me, the Maxima is just a daily driver until the 240 is done. Just an average day to day car... Joshua