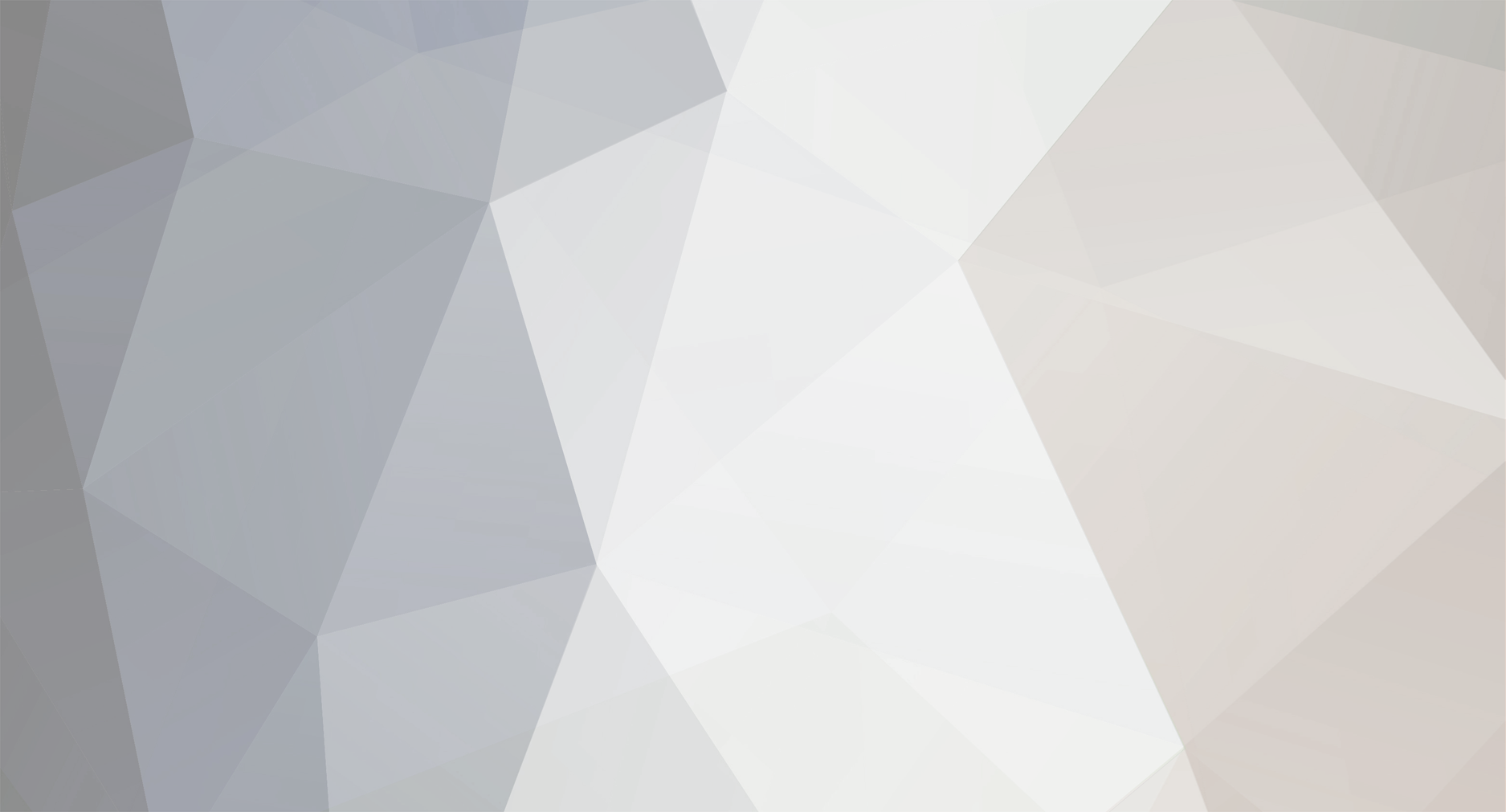
Jolane
Members-
Posts
351 -
Joined
-
Last visited
Content Type
Profiles
Forums
Blogs
Events
Gallery
Downloads
Store
Everything posted by Jolane
-
Thank you Dan!!! That drop down on the bottom is what I didn't notice! Joshua
-
I posted several items for sale in the appropriate places, but forgot to have the email notification option selected. I am subscribed to each thread. Can I now enable email notification for each thread that has already posted? If so, how? Thanks! Joshua
-
Oh, there they are! Thank you very much Jay.
-
I also want to echo the thank you. I now know how to remove and install the parts, and make the correct measurements. The last piece of information that I have not seen is torque specs. Does anyone have the torque specs for: 1. Bearing caps 2. 12 mm ring gear bolts Additionally, I assume I should use some sort of Loctite on at least the ring gear bolts. Is this correct? What kind? Again, thank you for all the help! Joshua
-
Unemployment Insurance: what a crock of $hite (rant)
Jolane replied to datsunlover's topic in Non Tech Board
Well, I can tell you this (and I don't mean anything personal by it). The Unemployment Insurance here in New Mexico, USA, is just as bad if not worse. When I was laid off a few years ago, I received a MAXIMUM of $276/week, minus taxes. There is also a waiting period here, and the application process is nearly useless (horrible website that is down most of the time). That is not even close to 55% of a small salary. It is a complete crock of crap! My GF was forced (coersced) to resign from her job in Nov, a few days before her 1 year probationary period was up. This was a state job, at a state run hospital. She never had a negative comment from any co-workers or her boss, great reviews, etc. Well, she was told that she would be fired (not laid off mind you) if she did not resign, and that it would go into her file and look bad for future employers. So she hand wrote a resignation letter on the spot, definitely not something would have done normally. Guess what, she was now NOT eligible and has not been able to collect UI. She has two kids (previous relationship) to take care of, plus all the normal bills. Absolutely rediculous! The system really is worthless! The honest person needing assistance between jobs gets completely screwed, even if they are doing everything they can to work. I feel for you! Good luck, and hang in there, you will be done with school in no time, and it will be worth it. Joshua -
I did the front and rear studs on my 280ZX once. Yes, it was a lot of work. I found that having several different lengths of 3/8" extensions along with at least one universal joint allows you to get several of the bolts under the intake. Then, you will need a 12 point wrench to get at the rear one (IIRC). I can also highly recommend that you get a wobble drive extension, and both short and long sockets. It is not trivial, but very doable. I was 'unlucky' enough to break a TAP off in the hole. I thought I had drilled the bold bolt out completely, but I hadn't, and a piece of the steel inside caught and broke my tap off. That was misery, but I was able to pound on the tap and break it into pieces, and remove the piece. It took several days of work. As a replacement, I used the next larger stud size, since the hole was buggered. A keensert would have been better. Good luck on your project, I feel for you! Joshua
-
Looky here at THIS ! Nicely done 3d engine animation
Jolane replied to Cruez's topic in Non Tech Board
That was very well done...except that the piston-rod assembly was in the wrong order... I would have thought the pistons should have been put on the rod first, then the crank into the block, then the pistons drop in. The 4-cycle running animation was very well done! A lot better than most of the weekend car shows, and those guys get paid to do it... Joshua -
I agree with Michael and Blairjj. I too have a MSME, and it was very worthwhile. A BS degree in any technical field is very common today. Don't get me wrong, it is a lot of work to get, but it is also too general. Consider you can be designing HVAC systems for large building or Aerospace parts all with the same degree. A Master's should help narrow down your field of expertise...so you can focus on the fun stuf and learn a lot more about it. Personally, I found grad school MUCH more fun that undergrad for that reason, not to mention that other grad students are normally more serious about school than the typical undergrad crowd. I would like to go back and get a TECHNICAL MBA in the future. The program I would like to go through is in another state though, and they require you are practicing in your field for 5+ years before attending. I too thought about a tech school (if for no other reason than it seems fun). In the end I figured that I could learn the information other ways and buy a lot of the equipment I would need with the money I would have spent on tuition. I like it this way... Hopefully this helps, Joshua
-
Front Suspension shock tube modification
Jolane replied to Careless's topic in Brakes, Wheels, Suspension and Chassis
Jon, Thanks for the travel. I guess this has been the long way on how to learn about the specific Z application. I guess if the stock length shock does not bottom out internally, then you might as well run that. If it does bottom out, the best option is to section the strut tube and run a shorter shock. Seems pretty straight forward now. Thanks for a good (at least for me) discussion... Joshua -
Front Suspension shock tube modification
Jolane replied to Careless's topic in Brakes, Wheels, Suspension and Chassis
Careless, Tanks for the diagram. I had this pictured in my head. The part missing from your picture though is the piston location inside the shock body. I guess the point I was trying to get at was that I don't think it is universally better to space the shock off the bottom of the strut. At some point the shock is too short in compression travel anyways, and the piston will run into the bottom of it. This stuff is important when building 4X4's as well. In that application, the rebound travel (droop) is usually less than compression by a good bit. Trying to cram the longest travel shock in there is important, but get too long a shock and the benefit is negated since the piston will bottom out instead. There is a balance to this. The longest travel shock is not always the best universally. In the end I think the best thing to do is section the strut tube and run a shorter shock. Joshua -
rear poly bushings on outboard end of CA
Jolane replied to blueovalz's topic in Brakes, Wheels, Suspension and Chassis
Terry, Exactly! The outers are also overcoming the twisting force of the strut, but with a shorter moment arm (both causing and reactionary). This is why I was curious if there was already an analysis of this out there. Joshua -
rear poly bushings on outboard end of CA
Jolane replied to blueovalz's topic in Brakes, Wheels, Suspension and Chassis
-
Front Suspension shock tube modification
Jolane replied to Careless's topic in Brakes, Wheels, Suspension and Chassis
Maybe what I said came across wrong. I agreed that you loose travel. I understand this as well. If you lower a car via the springs (regardless whether they are coilovers, cutting springs, etc), it brings the strut upper (pivot) closer to the strut lower (gland nut). I wasn't sure about the amount of compression left though. It is common for someone to lower their car 1" and still use the stock SHOCK and strut tube (sorry John C, I was in a hurry and used them incorrectly, although I did know the difference. I should have proof read). The part that I was unsure of was the amount of bump travel available after lowering. Certainly running into the bump stop after only 1" of compression is a bad thing...BUT, the bump stops are rather long. Why not just shorten the bump stop to gain additional clearance? I thought the other reason people went to shorter struts was so that the stock strut did NOT bottom itself. I thought this was the main purpose of the shorter strut, to keep the shock piston from hitting the bottom of the shock body internally. Anyways, I didn't mean to suggest that the T3 parts were the best solution, but rather was trying to understand whether it was really that bad. Consider a street car that has been lowered a little (not race car lowering mind you). I guess maybe just run a stock length shock then? BTW, is the stock travel really only 3" in compression, and 3" in rebound? Joshua -
Front Suspension shock tube modification
Jolane replied to Careless's topic in Brakes, Wheels, Suspension and Chassis
-
Front Suspension shock tube modification
Jolane replied to Careless's topic in Brakes, Wheels, Suspension and Chassis
I am confused. Why does everyone think that the T3 spacer/gland nut will reduce travel. I don't see how it is any different than sectioning the tubes and using the the same shorter insert. The only difference I can see is less clearance from the top of the strut tube and the jounce stop. Otehrwise, it is exactly the same as sectioning the tube, right? A sectioned tube also reduces the travel... Joshua -
rear poly bushings on outboard end of CA
Jolane replied to blueovalz's topic in Brakes, Wheels, Suspension and Chassis
Jon, Thanks for the link. I am not sure I like the rear control arms (if I understand how they are mounted). It doesn't seem like clamping those aluminum blocks into the stock locations would be strong enough! Welding permanent mounts though should work fine. Maybe I am wrong though on the implementation. As for the front LCA's, that is exactly the way I did mine... nice to see someone else do the same thing. Joshua -
Front Suspension shock tube modification
Jolane replied to Careless's topic in Brakes, Wheels, Suspension and Chassis
-
Front Suspension shock tube modification
Jolane replied to Careless's topic in Brakes, Wheels, Suspension and Chassis
I agree with Terry about cutting the tube as high as possible to lower the load on the welded section. I will offer a different perspective as well though... If you cut the tube really low, say maybe an inch from where it enters into the cast spindle, then you can actually put a doubler piece of metal around the welded joint and weld that up too. I have not seen anyone use that method (I am not sectioning mine as it won't be lowered enough to require it) though. Just my 2 cents... Joshua -
Dr. Hunt, I have a Dynasty 200DX that I love. I live in Alb. and you are right, the local welding shops here are smoking crack! I bought my MIG (MM210), TIG (D200DX) and Plasma (Spectrum 625) from Cyberweld.com. They are great to deal with and have very good prices. Remember, most of the TIG's do NOT come with the foot control/torch/etc. A Dynasty setup without bottle is ~$2800 +/- online! The TA185 is a great little machine also, at about $1650 or so. Check with B&R Welding, they are also a great online retailer who sells TA. After looking around locally for welders I finally gave up and ordered online. I know someone at Trigas who could get me a better deal that MSRP, but even he could not come close to the online prices. Quite often shipping is free as well, and no tax. The nice part about the D200DX is that it is portable and will weld on 110V. The bigger TIG's can weigh a lot. The Lincoln Precision 185 is supposed to be a nice machine too. I presonally also like the Miller Syncrowave 200, but it is heavy and large (and needs a large 220V circuit). The Dynasty only requires a 30A circuit, I think the others are in the 60A+ range. I hope this helps, Joshua
-
rear poly bushings on outboard end of CA
Jolane replied to blueovalz's topic in Brakes, Wheels, Suspension and Chassis
Jon, As Terry said, nice work. This does look like a nice solution. Are you planning on using adapters for on the car adjustment as someone mentioned previously, or are you just screwing the heims straight into the adapters you welded in? Also, did you decide to use the stock pin or a bolt through each heim? For most people I guess the additional angle and sway bar mounts will be unnecessary as well. I personally would not cut out the flat sheet though as you asked earlier, that is acting as a shear plate to keep the arm from changing shape in the flatest orientation (fore/aft that is). Please post pictures when you get it mounted up. Thanks, Joshua