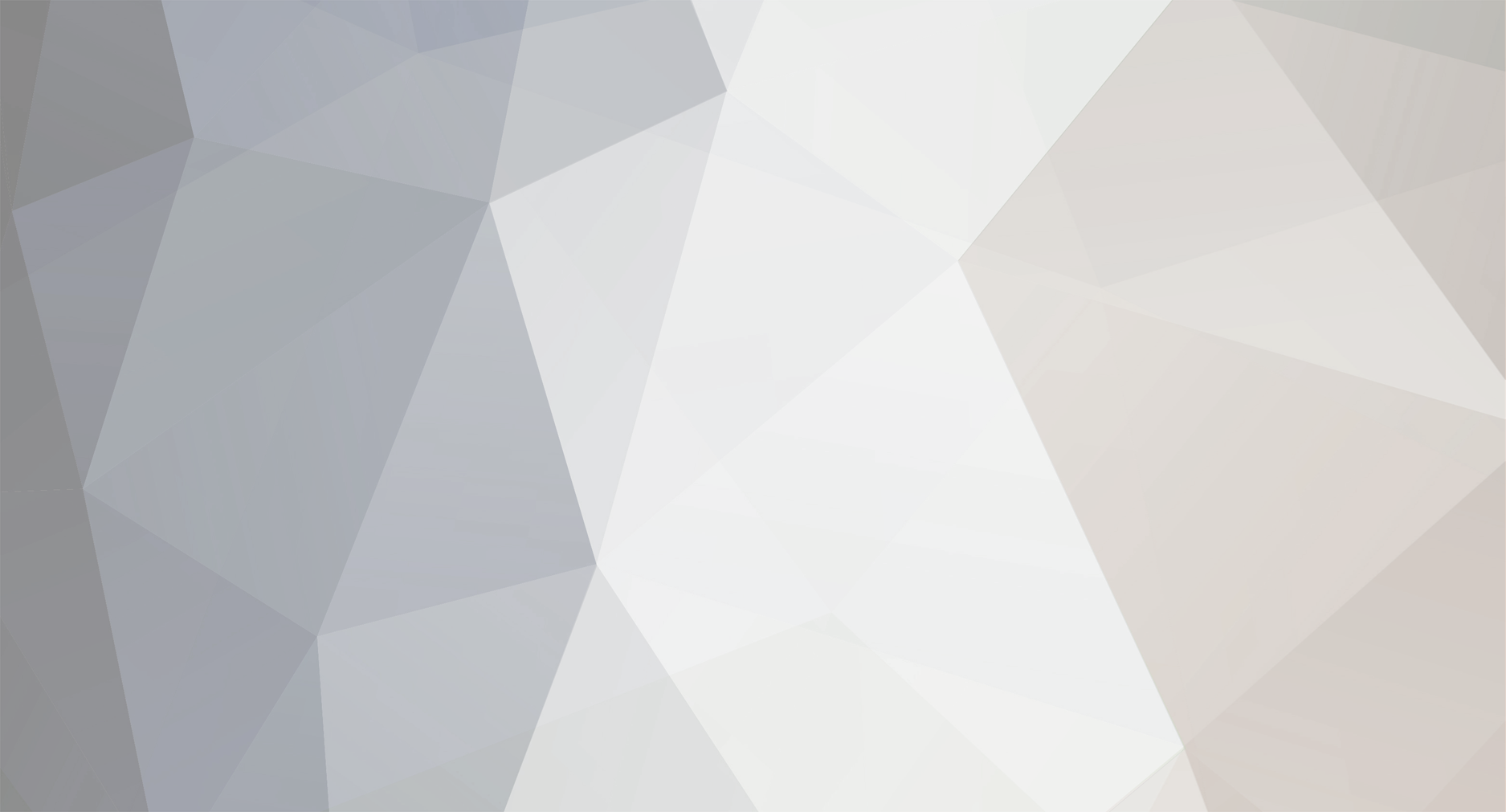
zuhow
Members-
Posts
38 -
Joined
-
Last visited
-
Days Won
1
Content Type
Profiles
Forums
Blogs
Events
Gallery
Downloads
Store
Everything posted by zuhow
-
It's an AEM 30-4110 with the bosch LSU sensor. No, the auto tune is not on. If there is some specific info you would like, please ask. I know you to be extremely knowledgeable, I would gladly welcome your help most appreciatively. But if you just want to be a d*ck, I'd prefer you just ignore this thread, thanks.
-
Forgive me gentlemen, frustration posting. I was looking for a more general cause. I have an electromotive tecGT on a turbo application. I've checked the sensor and it will read rich or lean as appropriate in free air or a gas soaked rag. It's a new sensor. It's maybe had a half dozen hours of run time at idle to 2500rpm. I've just gotten the engine started and I'm now trying to get to a point where I'm able to take it for it's initial drive. I've had a little bit trouble getting a decent base map using the tuning wizard. I've been following the Clewett tuning instructions as a guide. So what seems to happen is I bring it up to 2500rpm and get the AFR to 14ish, then bring to idle and try to adjust there. Everything will be looking fine. But eventually the AFR meter will drift off to full lean. The car is loud, so I'm not hearing an exhaust leak, but that doesn't mean it's not there.
-
I'm just getting this beast on the road, and I can't seem to figure out this issue. After a while, say maybe 15-20 minutes of warm up, my car starts to read full lean. I can add fuel to the point it wants to stall, and that sensor still reads lean. Starting from cold it behaves as expected, but at some point that stops. Do you think it's a leak in the intake or exhaust that open up at operating temp? I've looked for both, but haven't had any luck. Do you think it's just that AEM controller is junk? I'm at a loss, any direction would be appreciated.
-
I would say to you " it comes apart a lot easier than it goes back together". What I mean by that is, don't touch anything you don't have to. Trust me on that. I started this project as a young man of 20ish. I just turned 51. I still haven't driven it.
-
>I think you're mixing metric and English units. Totally possible, and I would be happy to declare that I am, in fact, an idiot! Standby for results.... **edit** Yes boys and girls, I AM an idiot. rossman, send me your next bar tab- It's on me....
-
Ugh. This project has been on hold for a very long time, and now I'm getting somewhere, or so I thought. This is such an ugly issue that I'd like some input from you guys. After getting the engine started and getting ready for a test drive, I decided to check the valve lash. I've got about half of what I should have (0.016" measured v. 0.030" spec). I'm all the way down on the post- the lock nut is tight to the post. I've got the standard 0.120" pads in there. What I think happened is that the machine shop set the valves too deep. I was smart enough to not trust them, and I did a wipe test on each and every rocker. What they had sent back to me would have definitely self destructed. I've run the engine maybe 10h between break in and assorted testing. All the lobes and rockers look fine. So my question is "now what?" and I fear the answer is that I'm pulling that head and sending it out for a rework. Your comments are appreciated.
-
-
I did pull the valve cover, everything is in order. I doubt that the tensioner has fallen out of place, but maybe it's possible. Do you think that air in the cooling system could be cavitating in the water pump? It does have that 'pumping marbles' sound to it. It'll see if I can get a good clip of it. So far the recordings don't seem to capture the sound well. Thanks
-
Hey there, I've been here a long time. Somehow 21 turned into 51 in the blink of an eye. But now I've got this project going somewhere again and I'd like some input from you guys. I just started this engine up after it's rebuild- it's been sitting a long time. It fires right up, and runs great. It's just that it seems to make more noise from the timing chain area that I'm comfortable with. The water pump turns freely with no slop, as does the alternator. Is this normal and I'm just paranoid? Any ideas/advice? Should I just run it and hope for the best? There's no sort of grinding or bad mechanical sounds- it's just uncomfortably loud.
-
280zx turbo motor with stock turbo $300 around Baltimore/DC https://baltimore.craigslist.org/pts/d/columbia-1982-nissan-datsun-280zx-turbo/6938347603.html
-
Best craislist ad ever (datsun related too) Click it before it's gone http://easternshore.craigslist.org/for/3020885291.html copied just in case: Jack Russel/datsun mixed - $50 (Chestertown, MD) I have a 2 1/2 year old Jack russel/ Datsun mix. ALL shots are up to date and he is neutered. Great dog just have to get rid of him. Would like to recieve a $50 re-homing fee. He will come with new crate, food and all paperwork from the vet. His name is boo-boo..... call or text ONLY (redacted) . ask for mike If you want to see him just call and i can send you a pic through text or you can come here to see.... Thanks
-
s30 240Z 260Z 280Z lower Fender Repair L AND R Sections
zuhow replied to J240ZTurbo's topic in Parts Wanted
I've got new Victoria British fenders, L & R that you can cut up or use. PM me, I'll let 'em go cheap. -
I have a MSA Stage 3 cam , new with cam card for $135 shipped
-
I have the 81 pulley and you can have the pick up sensor as well. I ship it to you all for $55 as well.
-
Drill press recommendations? Either cheap/used!
zuhow replied to Evan Purple240zt's topic in Fabrication / Welding
I love this little grizzley press that I have, and you really can't beat the price. http://grizzley.com/products/5-Speed-Bench-Top-Radial-Drill-Press/G7945 -
Redo My Brake Line Shopping List
zuhow replied to JustinOlson's topic in Brakes, Wheels, Suspension and Chassis
I did this a while back- get (2) 25' rolls of the stainless. I looked at the AN fittings and it's just way too much cash- it think it was over a $100 in just adapters. That stainless is hard- I quit using the tubing bender because you almost can't crush that tube. I ended up making single flares on the tubing ends because there was no way to double flare the tubing- I was working at an aerospace company at the time and even their production tubing flare machine wouldn't make the double flare. -
For a shingle roof, you need minimum 3' fall per 12'. With wet snow you might have some problems, but I've got 4/12 and haven't had any problems. You should have a permit, but really that depends on your neighbors. I'd look into a standing seam metal roof if I were you. It won't be cheap, but much cheaper than new engineeringed trusses and a what not.
-
I second the Jeff Hartman book- How to tune and Modify EMS
-
are you kidding me? I signed up for my local 'freecycle' (freecycle.org)- it's the greatest thing since 2 ply TP. I had some one give me a n/a 280zx once!! also I can post things I dont want and SOMEONE COMES TO GET IT- no more trips to the dump. I highly recommend it. everyone here should check it out
-
....i dont have anything to measure mm...... a simple desk ruler will work: 240 mm =9.45" 225 mm= 8.86"
-
I think 1 is a NO if I remember correctly, the N42 doesn't have an opening for the mechanical fuel pump that runs off the cam gear eccentric.
-
I'm REALLY not a fan of site with flash intros and sound....please make it as user friendly as possible. good luck!
-
I like it. the problems I see are: 1) I don't think it will fit 2) If it does fit, I think the turbo will need some support. That moment arm from the cylinder head surface to the turbo surface looks to be way too long- I'm guessing it's about 16" as shown. 3) I'm thinking it's better to group 1-2-3 and 4-5-6. Scavaging isn't going to be such a big factor before the turbo. 4) you're going to lose a lot of heat in those long tubes, so you'll need some insulation 5) that's going to be expensive to make
-
since no one else has chimmed in, i'll give you my 2 cents. IMHO, it's certainly not what you want. Will it be ok? Most likely. The corrosion is only a couple of microns thick, and will probably be removed by the wiping action of the rings. That said, you'd be better off if it didn't happen. Just get it as clean as you can- then clean it again. Mechanical stuff is suprisingly tough- I once work at a steel mill that had (and still has) a 1898 reciprocating air compressor in use- and that thing ran 24/7 with less than ideal upkeep. If it were mine, I'd be PO'ed at myself and then I'd put it together as best as possible and run with it. What are your other options- not much I'm afraid to say. You MIGHT be able to hone it to remove it, but that will open up your bores- might not be so bad, but I dont know if you're willing to take that risk. Have you mic'd the bores and do you know what your clearances are? You could assemble it and crank it around by hand a few dozen time to see if that will polish the rust off the bores and then dissasemble it and clean and reassemble (this time keep ALL water away- use laquer thinner or mineral spirits). I think you'll be OK, but damn, that sucks......I know how you feel.
-
yeah just one from my expierence, bring more money