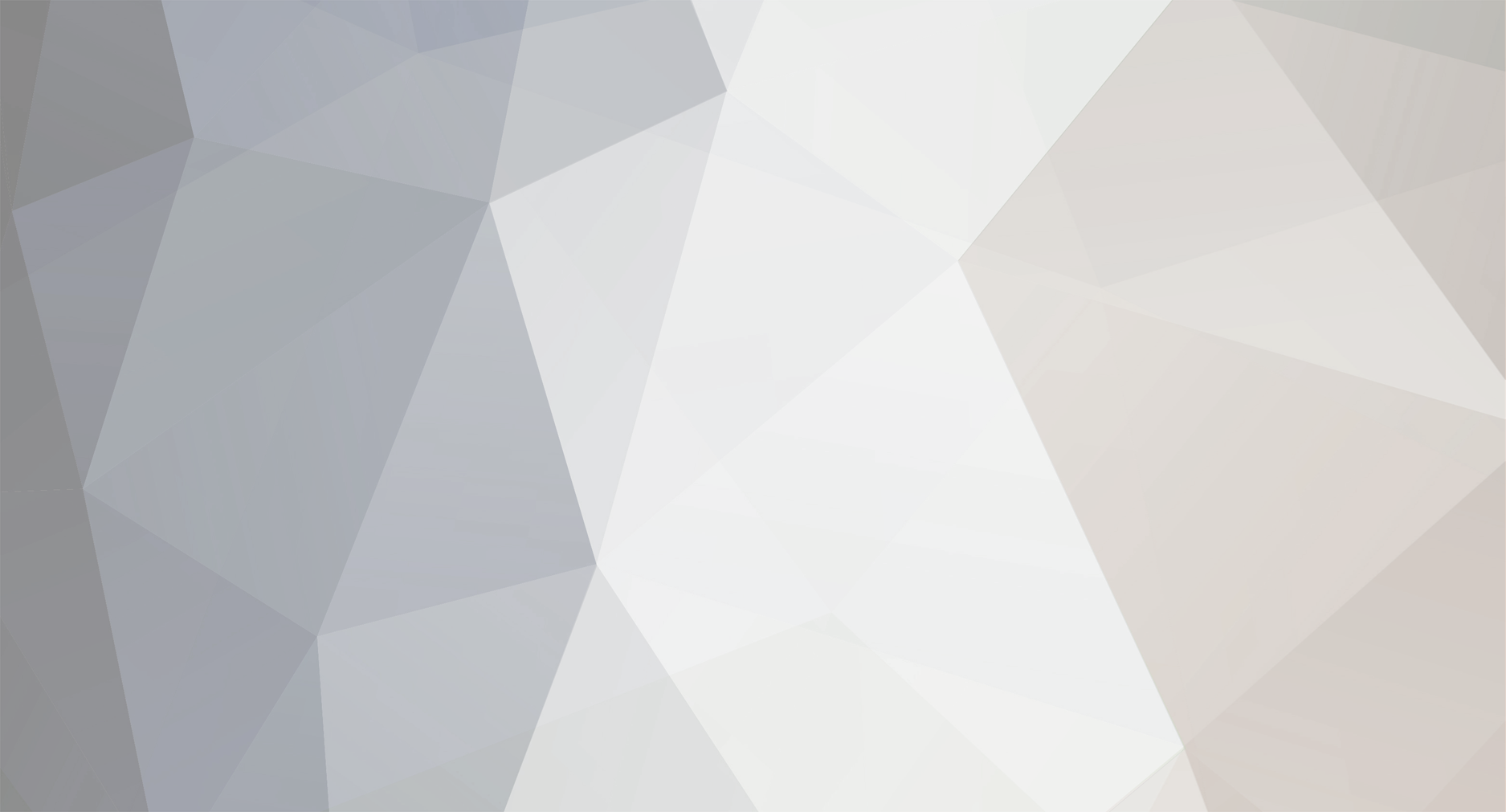
Here comes trouble
-
Posts
656 -
Joined
-
Last visited
-
Days Won
2
Content Type
Profiles
Forums
Blogs
Events
Gallery
Downloads
Store
Posts posted by Here comes trouble
-
-
The laws of Oregon would define what happened as an assault upon you as Mike Kelley addressed. I would imagine about everyone present witnessed an old fool antagonzing a young man who kept his cool and was not at fault (to your credit with all the children present). My theory is from years of experience (57) that a lot of foliks over 55 are just plain nuts and on occasion can make complete fools out of themselves in public trying to prove they still have "IT" when there is nothing left to prove. The first words out of his mouth really were: "I am Mr. Important" - who was going to win that serious race competition and be the local winner honoring the returnning heros. Take it for what it is worth: a confused old silverback still trying to compete with the pack and taking himself too seriously at having fun. Who do you think what age group all those prescription medication commercials are aimed at......the baby boomers who do not know how to age gracefully looking for the fountain of youth..my opinion.
-
Vapor lock is the old school term you fellows are describing and has been a perpetual problem plauging the internal combustion since conception.. Actually wooden clothes pins connected onto Ford Model T fuel lines would radiate heat out of the fuel line. Summer temperatures and any source of under hood heat, exhaust and even the road blacktop near the fuel line can cause this problem. I had a Dodge truck that was suceptible to vapor lock that i fitted an auxillary electric fuel pump to. When vapor lock occurred, I switched on the electric pump momentarily which cured the problem (and most likely cooled the fuel) Insulating fuel lines or fitting radiator type fuel line sections should work. When gas gets warm it wants to evaporate and that is why there was always an insulator between the Datsun carburator and the manifold to keep the fuel temperature down while the carburator vaporized the fuel correctly..Cold air intake is another term....The air filter on an EFI Z is right out front in the breeze to suck in the coolest air... Check your air intake and fuel lines and insulation between vaporization and the manifold.
-
The racks are probably interchangeable... which does not mean yours has been changed. Nissan would slip in older parts whenever they could to their product line .... (why did some 280 z's get 180 rear ends while others had 200's) Probably one of the few reasons to change out a rack and pinion on a Z was due to a front end collision. They do not seem to wear out if lubricated and the pinion can be shimmed for better adjustment. Unclamping one side of a boot and slapping some grease on the surface of the exposed rack teeth is less trouble than fitting a metric zerk to the steering gear pinion housing.
-
Your second pictures shows that your marker is directly above the correct mounting holes ...the smaller hole closer to water pump and the larger hole connecting the timing chain cover to block... about 2 inches appart
-
If it is a first gen or early Datsun ..file down an old Datsun key a little. May work. You would be surprised at how many other Datsun keys work in a Z. I take off the steering lock mechanisim (had one lock at speed once) and then can use the ignition wiring harness to start until replacement arrives
-
go with the cat massage since it is better to have a little drippage.... overuse of muscle relaxants can cause chronic constipation
-
I read in Newsweek that the tires were tested in Hong Kong over a year ago and there are reported birth defects among Hong Kong motorists who were determined to have a chronic history of following too close. The EPA and FDA as well ATF agents are following these events very closely, a White House spokesperson reported (unofficially).
-
I called the Powder Coat Institute @ 1-800-988-coat and was told engine blocks could be powder coated and should not cause any undue cooling problems. Apparently not many engine blocks have been known to them to have been powder coated. caveat emptor qui ignorare actor (beware dude it is now your responsibility)
-
manifold nuts/bolts tightening tourque is at 10-13 foot pounds for size 8m and 25 -36 foot pounds for size 10 m fasteners... not much torque for the average manifold fastner but the exhaust fastners get hot and could lose strength over time. Stainless steel or black oxide should help with corrosion problems and grade 8 would almost be unbreakable for manifold applications, Brass exhaust nuts and black oxide studs rated at 125,000 # as previously suggested maybe an excellant combination from a reputable or reliable source
-
Jody....Thanks!!!!!!! that solved my problem with the Harbor Freight pipe bender I have... My bends were dimpling right where the couplings should have been fitted... Great improvisation.
-
As for making original parts..... there were some some good hints on foam and plaster material that I found enlightening. I have used eheet metal roll sheathing to extend surfaces in making parts. Fiberglass does not adhere to the sheathing that is electrically galvanized. Also if you can find finished fiberglass parts that have been discarded by a manufacturer for a flaws. I bought a flat section of a fiberglass motor home roof panel that I cut up and utilized.
-
funny, funny, funny..................What an excuse: " I can do anything cuz , I ain't child raper"! Getting harder and harder to be an outlaw these days
-
since my riding lawn mower is all tore apart, I might as well get one and do the job right this time with the electrical system because I am tired of hot wiring and jump starting... too much belt sloppage for a tow start and my bumper does not match the grass bag for a push start. The wife refuses to assist if I do not let her operate the tow vehicle pulling the lawn mower.
-
I just checked a rack/pinion system off a 1977 and there is no provision for a zerk. If it is right size for a Zerk.. then do it
-
You can use pre bent 90 degree (1 1/2 x 1) sheet metal flashing from Home Depot for a temporary flange for two part molds. The actual flanges will be of fiberglass construction. Pumber's putty in the string coils can be used for your clay needs to fill in the gaps on the preliminary sheet metal parting flange. Decide where your parting line is to be placed on the part to be copied. Cut an apropriate length of the flashing and lay it on the item you want copied. Use tin snips to cut slices in the sheet metal to conform to the surface of the piece to be copied. No need to remove sections of the sheet metal. # 8 by 1 1/4 self tapping screws with large phillips screw heads can be found at Home Depot to fasten the sheet metal to the work piece. With proper snipping the sheet metal flashing will comform to the work piece and the large head self tapping screws will pull the flashing very tight to the work surface. Any gaps can be filled with the plumbers putty to keep resin from seeping thru to the other side of the flange. Your parting line flange is in place and sealed with the plumber's clay putty. The screwed down part of the flange will always face away from where you start laying fiberglass. You lay the fiberglass up to and on the sheet metal. This will be your first parting line flange. When this entire side of the layed fiberglass is cured, trim the excess fiberglass that extended beyond the sheet metal flange to make a good clean edge with a cutting wheel grinder disc. Then remove the screws and sheet metal flange and discard the sheet metal, the screws can be used for another project. Fill in the screw holes on the work piece. Secure with clamps the cured layed up fiberglass first part to the work piece so no accidental movement takes place while laying up the second part to the work piece. Re-touch the other side with release "green wax" which you should have obtained from a fiberglass supplier. Rub the wax into the new fiberglass parting flange and lay the fiberglass to the unfinshed side to mate it to the work poece surface and the first parting line flange. Let cure and then grind off any excess fiberglass at the second parting line flange so both parting line pieces are even and straight to each other. These parting line flanges should be at least 1 1/2 to either secure together with clamps or bolts. With the two pieces secured to gether... you have a two piece mold. Any gaps in the mating surface of the two fiberglass flanges can be filled with plumber's putty which rubbed vigorously with finger to become very smooth. Thoroughly wax the new mold, spread on the gelcoat and then fiberglass . Shred the fiberglas mat to lay in tight spots and the shoulders of the first fiberglass flange that was created by the aid of the now discardedsheet metal flashing. Cure and crack! Do some research in this section and for Terry Oxendale (Blue Oval Z for previous threads.
-
Unless repair is needed or adustment is absolutely required, leave the pre-load adjuster alone.Ths unit is shimmed,the locking nut is tourqed at 29-43 foot pounds and if disturbed requires sealant around locking nut to prevent grease seepage besides any adjustment could disturb the amount of tourqe to turn the steering pinion gear..and cause premature wear to the entire steering gear............. Next to the steering gear, Slip the dust cover boot back exposing the rack. lubricate the rack and then turn the steering gear to spread the grease inside the steering gear housing. This is about the quickest way to do this without taking apart critical adjusted parts. If you have provisions for Zerks --use them.... If your system is not leaking grease and the boots are retaining the grease..then the prior lubrication should last and last.....Do an inspection at the boots. All you want is ample grease on the rack slots and pinion gear
-
Before I went away.... I managed to obtain some wide flared full fiberglass front fenders on eBay out of Wisconsin that a great Hybrid member there picked up from the seller and shipped UPS to me cut in half which I immediately spliced back together. These were a couple of the items that did not grow legs and walk away while I was gone. I planned to duplicate them.
-
KYB GR2 whch will probably not over compensate your approximate 110 (f) -125 ® pound springs..... around $50.00 or less apiece
-
yes yes yes
-
Non flared cars seem to be the custom these days as less chrome also seeme to dominate many car's appearance. Your car looks great as it is but.............. there is that mindset with some of us will never abandon for that big-badass wide look that common sense cannot control when building a hot rod....You need another Z to work on.
-
stock S30 1978-280 Z specs: rear sprlng : 127 pounds to inch, free length 15.43 inches..... Strut assembly:..0.98 ft/sec: damping force at piston speed........... Expansion :121 pounds .... Compression:66 pounds front spring: 115.4 pounds to inch, free length 15.71 inches strut assembly: 1.0 ft/sec: damping force at piston speed Expansion: 121 pounds Compression: 66 pounds
-
A vice and a careful selection of sockets will work. Use a socket slightly smaller than the u-joint to push the u-joint out of the shaft's yoke with the vice. On the other side use a socket large enough and long enough to entirely accept inside the u-joints opposite cap. Remove the u-joint retaining clips that holds the u-joint at each end to the shaft's yokes. Place the u-joint/shaft in the vice and align the correct sockets on each side of the u-joint caps and tighten.. The small socket will push the u-joint cap thru the shaft's yoke and the other side of the u-joint will be pushed inside the larger socket. Once the caps are about halfway out... they will come out easy..... to replace is more difficult since the u-joint caps contain needle bearings.. Press in one side of the cap with the ujoint and shaft in the vice.. Have the u-joint seated as much as possible inside it's cap that you are pushing in to avoid damage to the needle bearings. Once you have the cap pushed into the yoke as far as possible. Align the other cap to the shaft yoke and press in slightly . There should be enough of the U-joint caps in the yokes to align the caps to the joint ends without damaging the needle bearings. This last step is critical due to damaging the needle bearings and is where I have made mistakes such as " kinking" by not taking time. a needle bearing or (twwwo) As mentioned before.... a shop may be your safest bet.... especially if you got some $ in the joints and some auto part stores may do it for free if it's their parts and you can observe how it is done on a press which is similar to a vice.
-
UPS does not ship Z fenders... too long.... after market fenders can have "fit " problems. I would guess that a steel fender weighs no more than 10 pounds more. I have some fiberglass front fenders and I would be more willing to pack those around than the steel ones. I doubt if there is that much structural strength difference and with modern paints... you should not have any real finish problems.
-
Drinking like that since 1992, not only is the liver gone but the brain is also damaged which may account for being unable to avoid the police and conflicts.
What am i doing wrong on timing?
in Nissan L6 Forum
Posted
Wag Z has the right marker.. If you cannot find one.. contact me with private message and your addtess. I wiil send you one off a 1977 Z