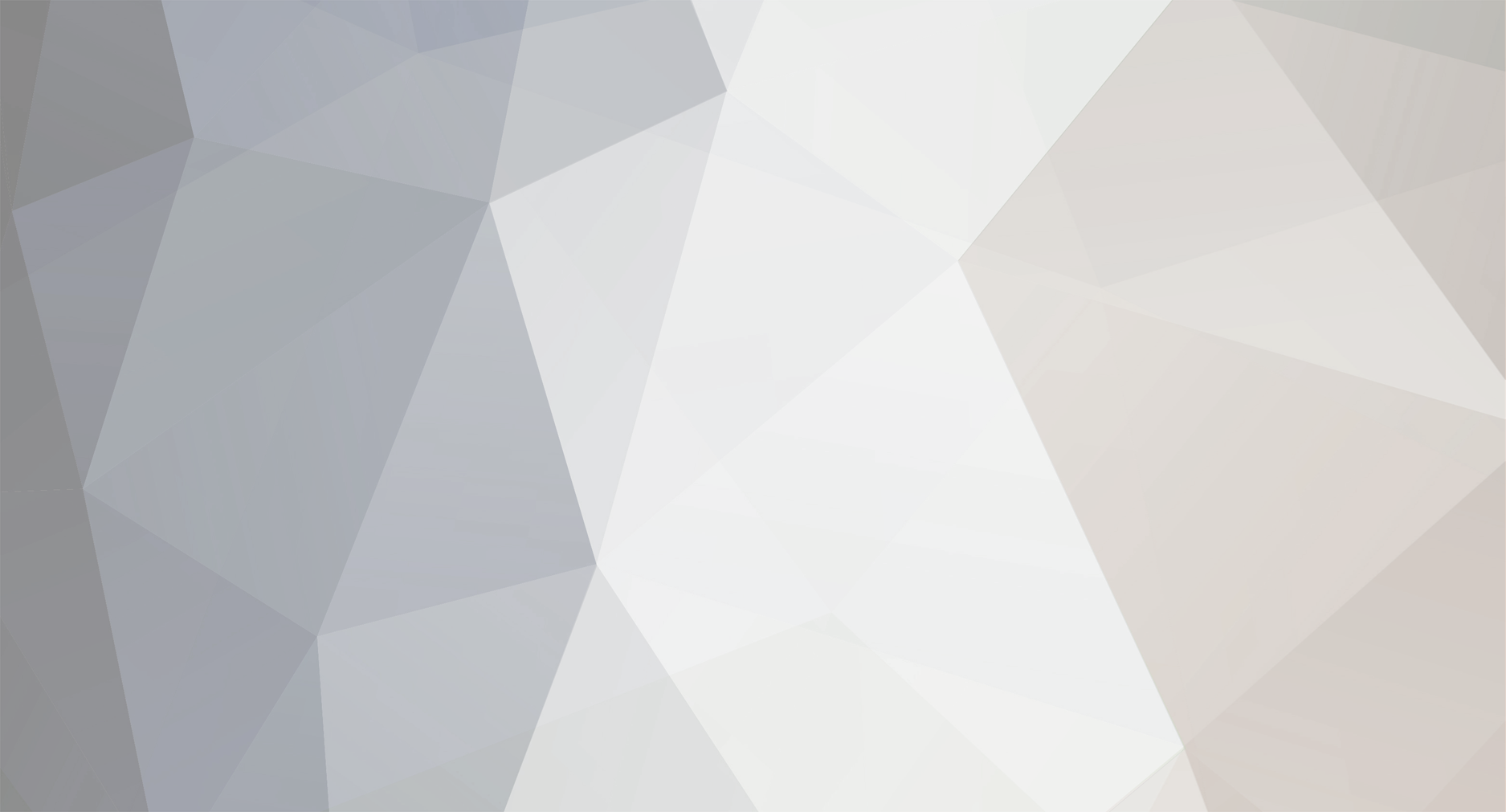
toolman
-
Posts
546 -
Joined
-
Last visited
-
Days Won
14
Content Type
Profiles
Forums
Blogs
Events
Gallery
Downloads
Store
Posts posted by toolman
-
-
-
Patch had to be held in place with Cleco clips for welding. Sheet metal screws were also used.
Quote -
First picture is the completed radiator core support. It is welded to both sides of the front fenders and to the square tubing frame. Picture 2 show the rear of the support.
I drill holes in the inside of the front tubing to lighten it and for looks. The third picture shows the front area where the bumpers and hood hinge are located. Spacing of core support and
hood hinges are critical to prevent interference of moving parts. Check clearance before welding support in. Next step was to strip the engine compartment and weld up any small
unnecessary holes. But I discovered the area under the battery holder was corroded. So the holder was cut out. Photo 4 shows the corrosion. Pic #5 is corroded area is to be cut out. The last pic is the top view of the patch to be installed .
-
Yes, the ducts in the radiator support are constructed with sheet metal. I followed the basic pattern of the factory panel. Those extra holes will probably used for AC
condenser hoses. Larger holes may be necessary if I go to a PRO-CHARGER supercharger for the intercooler. In that case. new grill would be constructed too.
-
First pic is the "before" of left radiator support. Second is the paper template for replacement section. Third one shows the replacement mocked in. Fourth is of the"before" pics of the
right radiator support. Fifth shows the replacement section mocked in. The last photo is the overall view of the radiator support awaiting welding.
-
-
-
Thanks for the support. Sometimes these projects become bigger than anyone can predict. While the ribs were off, I double checked the front area in front the both struts and found the left side was 1" higher than the right. I called my friend who has a 70 240Z to take measurements off his car. I confirmed that the right side was correct and left side was high by 1". Since I didn't have a frame machine handy, I decided to section the left side and raise it 1". See photo 1 welded a 2" sheetmetal strip to reinforce the joined area on the inside, This area will be covered by the new radiator support. Pic 2 show the rib rewelded in and new section above the rib to provide a smooth transition between altered section and old area. Pic 3 show additional sheetmetal strip welded in to reinforce the outer section. This was necessary as this panel has handle the hood hinge and bumper brackets.
-
Wheeler, Your frame rails look great. Are you going to race the car? I started to do detail work on the engine compartment and decided to work on the radiator support instead.
While measuring the areas in front of the radiator-area where the bumper and hood hinge attach to) needed straightening. First picture shows the old radiator support. Second pic is of
both areas stripped of paint and cleaned. The third photo has the right side with the reinforcement rib removed to fix under it. Fourth pic had the rib replaced and ready to rewelded
on. The fifth photo is the left side with the rib removed and damaged area repaired. Sixth pic show the rib replaced awaiting to be welded back. The vehicle was in an accident before
I bought it and the area( crush area) was not repaired as that would require rib removal. Next to be done will the construction of the replacement radiator support.
-
First photo is the left side stabilizer bar mounting holes( a plate with corresponding nuts welded to it will be installed in the frame rail later)
Second pic is the right side stabilizer mounting holes.
Third picture shoes mocking up in preparation for welding of the tension rod bracket.
Fourth pic is the completed left side bracket. It is constructed of 3" x 1"x 1/8" steel tubing (same as frame connectors) The angle section is set at 20 degrees.
Fifth photo is the inside view of the bracket.
Sixth photo is the outer view of the right side tension rod bracket.
Seventh pic is the inside view of the tension rod bracket. Both left and right tension rod brackets will have 20 gauge plates welded to
inside and outside of them. This will replicate the factory appearance.
-
First photo is the "before picture" of the left side of frame rail. Notice 1" gap.
Second pic is 3/4" X 2" right angle 20 gauge sheetmetal welded to subframe and existing sheetmetal
Third picture is outside view of right angle connecting pice welded to subframe and wheel housing.
Fourth pic is an additional 20 gauge 3" wide and about 48" long welded to the subframe and existing sheetmetal. This will provide additional strength and looks better.
Fifth photo is right side frame rail with connecting right angle support plate.
Sixth pic shows welding the right side "cover plate'" to sheetmetal and subframe.
Seventh photo is engine compartment view of the subframe and connecting piece. All the mig welds will covered with urethane seam sealer after
media blasting. Next step is construct tension rod support brackets for both sides.
-
First photo is the left side frame rail with the frame connector welded to the firewall.
Second picture is the passenger side frame and frame connector welded to the firewall.
I was glad that put a 16 gauge reinforcement plate under the frame rail. Otherwise, welding 1/8" frame to 23 gauge firewall
would be extremely difficult.
-
The first picture show a better view of the plumb line. The second photo show the left suspension mockup. The third picture is of
the right side suspension mockup. The fourth photo is a closeup of the left side crossmember. Note the two 1" assess holes in the top of the
frame rail. The holes will capped off later to prevent water and debris from entering.
-
Labor Day Weekend gave me extra day to work on the Z. Unfortunately the holiday also meant most of my neighbors headed
the beach and were not around to me carry the heavier stuff. The first picture of the new subframe on the ground. Had to drag it under the
car and lift on the jack stands. Second and third pictures show aligning the subframe to existing body using datum line(center line and plume
line(vertical line).
-
-
I researched all methods of mounting the engine crossmember to frame rails(both untilized or steel tubing construction. Everyone notched
the frame rail to mount the crossmember. This method requires a lot of time and effort so I decided on a simpler method. I relocated the two
mounting bolt holes about 3/4" inward. See photo. This method does require two holes drilled on the top of the frame rail to install frame bolts.
I drilled two 1" holes directly over the crossmember bolts(inside the frame tube). Caps will cover the assess holes to prevent water from entering
in.
-
-
Left side rail checked levelness too. Both rails were also checked for squareness. This is done both measuring diagonally the opposide cotners of the frame rails.
-
-
this gap.the filler piece consists of 6" strip of 16 gauge sheet metal connecting tubing with existing wheel well housingplate was made with about 3 /16" edge around it. This was to allow easier welding the tubing to the firewall.frame connectorsOne of the most difficult potion of the front frame construction will be connecting the crossmember to the square frame rail.The connector will need to be smaller than the width of the square tubing.
-
Rear section was welded to existing rear crossmember. Rails were also spot welded in the middle sections.In preparation for engine compartment rail construction, the engine compartment was boxed to prevent body shifting while cutting off the front rails.to sidewards level. The car must be set level before any cutting can be done.
-
Waiting for magnetic starter switch for my air compressor so I decided to finish the floor reinforcement plates. These 16 gaugesteel plates are located inside the vehicle at the bottom end the firewall and front section of each side floor panel. They willreinforce the floor and firewall directly above the frame rails. The plates are about 4 inches wide about a foot long. This shouldspread the frame load over a wider area of the floor sheet metal.
-
My Z Project has been delayed by a deal that I could not pass up on. One of my customers had a C-Aire 7 1/2 HP twostage compressor with 80 gallon tank. It wasn't running because of a broken inlet valve. The price was $500 so I said "Sure"and load into my truck. Had to wait for couple weeks to get the compressor head rebuilt kit. I spent the time cleaning andchecking the parts. The parts came in last week and I reassembled the compressor. Everything is ready to go except thewiring and control devices. Should be only a weeks more before I can get back to my 240Z project!!!
-
I was delayed for couple of weeks as my air compressor broke down. As usual. all the necessary parts had to be ordered from the Mainland. Finally got the parts in and compressor fixed. Sure was difficult to work without a air compressor. Hope to get back on track now.
Heavy Duty frame rails and connectors
in Gen III & IV Chevy V8Z Tech Board
Posted
First pic is top view of restored battery holder. Second is the bottom view of the holder. The third pic is the battery holder "test fitted". I still have not decided whether to
install the holder or a marine type of battery box in the rear of car. The last pic is the firewall after I plugged unnecessary holes.