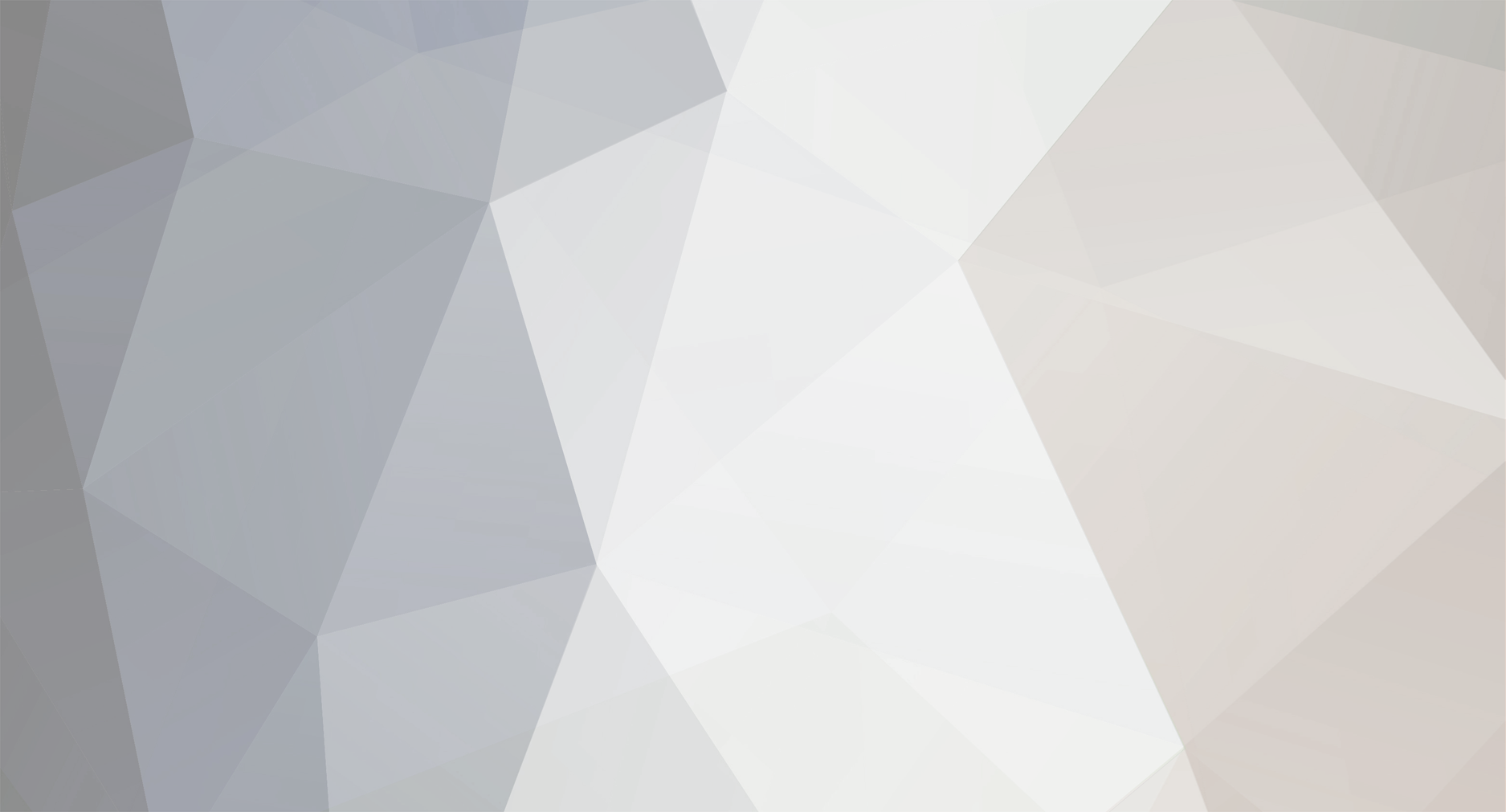
toolman
Members-
Posts
546 -
Joined
-
Last visited
-
Days Won
14
Content Type
Profiles
Forums
Blogs
Events
Gallery
Downloads
Store
Everything posted by toolman
-
Detailed Videos on Complete Bodywork of S30 Datsun
toolman replied to toolman's topic in Body Kits & Paint
More Good News, as of today Feb 24,2023, I posted Two More Videos #43 and #44 on my Chevy V8 Gen III and IV postings. Number#43 goes into more detail on Door Alignment and Fitment. Number #44 shows how to create Body Lines and repairing Door Gaps. Developing the "Feel Metal"(feeling High or Low Spots on the sheet metal usually takes a little time to acquire but some people never acquire this skill. Bodywork is mostly learned from experience. These Bodyworkers make their work look easy but it isn't. Toolman -
Detailed Videos on Complete Bodywork of S30 Datsun
toolman replied to toolman's topic in Body Kits & Paint
Good News-There is now a #42 Video Episode of The Complete S30 Body Restoration. It seemed that Japanese Body stopped working on the S30 when they painted the Under Carriage of this car. But I think a Emergency Job for the Tokyo Auto Salon Show (This show is Japan's Version of the US SEMA Show) in early 2023 was squeezed in. But anyway, there should be at least a couple more videos coming down the road. Enjoy! Toolman -
Heavy Duty frame rails and connectors
toolman replied to toolman's topic in Gen III & IV Chevy V8Z Tech Board
Kwik Performance Compressor Mounting Kit# L10291 Kwik Performance Kit sits high above the Passenger Side Valve Cover. Sanden Air Compressor($250) Designing the Card Board Template Trial Mounting of New Mount Front View of Mountront View of the Mountt Bolt Arrangement of Alternator Mounting Bolts Comparsion between Old Corvette Water Pump and New Camaro Water Pump Vintage Condensor#03701-OVA 12' Tall x 20" High x .83Thick was utilized($100 Amazon). It was bolted to Front Core Support in Front of Radiator. . New Foam was installed around Outlet Opening of Evaporator Core Unit for sealing purposes. New NAPA Expansion Valve on Evaporator Core was used. Factory Interior Wiring Harness had to be relocated to the Right Interior Panel to create space for High and Low AC Pressure Hoses entering the Core from the Firewall. Pic of the ARA Air Con Unit installed to Factory Heater Unit with Pressure Hoses to the Firewall. A !/2" Rubber Hose was also installed to allow Core to drain water out of vehicle. A High and Low Pressure Valve installed in-line to turn off Air Compressor to prevent its damage. top view of Kwik Performance AC Brackets Next-More Air Conditioning Work -
While in Tokyo, I came across these Videos which shows in great detail show a Complete Restoration of a S30 Datsun Z. The videos even show what tools,equipment, paint, primers are used. The only problem is that the initial videos are in Japanese without subtitles. However, due to popular demand, later videos came with English SubTitles. I posted telling the general subject of repair so you can skip videos that you are not interested in. Go to V8 Z forums ---To Gen II& IV Chev V8 ----to Heavy Duty Frame Rails---Go to Page 17---Go to Posting dated December 22,2022. I hope you enjoy them. Tap on Arrow below to go to my site to view all 49 videos. Toolman
-
Heavy Duty frame rails and connectors
toolman replied to toolman's topic in Gen III & IV Chevy V8Z Tech Board
Japan S30 FairLady Restoration Video- Part 21-Repairing Engine Compartment Panels Part 22-Applying body Filler and Sanding Engine Compartment. Part 23-Repairing Core Support and Head Light Doors Part 24-Repairing Upper Engine Compartment ----------------------------------- ENGLISH SUBTITLES NEXT PART------------------------------- Part 26--Connecting Rocker Panel and Floor Pans Part 27-Repairing Right Side Rocket Panel Part 28-Rear Quarter Panel Patch Part29-Tail Light Housing Repair Part 30-Rear Panel Repair- Part 31-Changing Right Door Panel Part32-Repairing Rear Inner Wheel Housing Part33-Repairing Right Floor Pan Part 34-left Rear Floor Pan Repair Part 35-Rear Deck Repair Part 36-Body working the Rear Deck Lid Part 37-Repairing the Car Roof Part 38-More Repairing to Roof and Rear Deck Part 39-Body Filling Interior Floor Panels Part 40-Installing Seat Mounting Brackets Part 41-Rust Patching through out the car Part 42-,Seam Sealing, Priming the Chassis and Undercoating the Bottom of Car I thought there might be additional videos on replacing the doors,hood,and hatch but it seems that the shop is finished with their portion of the job. So this is the Final Video of this 240Z restortation. 2-17-2023 Good News, I was wrong about the previous video being the last one in this series. This video #43 covers more Rust Repair around the Front Windshield. So it seems that there should be maybe one or more videos on this 240z Fairlady Restoration. Video #44 Assemble and Alignment of Right Side Quarter Panel and Door. Also. the video describes in detail how to create Body Lines and repairing Door Gaps. Part #45 Body Working Rear Body Panel, Correctly Right Fender Gap and Right Body Lines #46 Repairing Front Radiator Support #47 Finish interior bodywork #48 Exterior Bo #49 Detailed installation of Asphalt Floor Insulation. I never seen replacement of the Asphalt Insulation in any Restored 240Z before. This video gives a Step By Step Explaination of this process. -
Heavy Duty frame rails and connectors
toolman replied to toolman's topic in Gen III & IV Chevy V8Z Tech Board
ShawnM, I glad you enjoyed the videos. Did you notice that a lot of the metal fabrication tools (such as sheet metal bender, bead roller, English Wheel, etc) are brand new. The videos even show the boxes that they came in. The equipment was Made in USA, too. As my Father owned a Body Shop, I can tell that their workmanship is High Quality and would recommend that Body Shop to restore a 240Z. Please bear with lack of English Subtitles, later Episodes will have more English Subtitles!!! Toolman -
Heavy Duty frame rails and connectors
toolman replied to toolman's topic in Gen III & IV Chevy V8Z Tech Board
. I just returned from Tokyo, Japan today. While there, I found this video on YouTube.com-JP It was one of the Best Video Restoration of S30 Datsun Fair Lady car . Although it is mostly in Japanese, the video shows in great detail of the restoration process. The videos comes in 39 parts so I will try to divide the videos up into sections. Then you can just go to the restoration part that you may be interested in. Part 1-Painting Stripping, Abrasive Blasting (normally 80 Grit),Epoxy Priming the Bare Sheet Metal. This process gives the Bodyman the True Condition of the Car Body. Then he can start ordering either Repro Parts or Junk yard parts. As this car is over 50 years old, finding even Junk yard parts would lucky. So, a lot of sheet metal must be fabricated by hand. *NOTE-Press "Escape Key" to exit end of video. PART 2-Test Fitting of Replacement Panels and Hand Fabricating the Parts that could not be found. Part 3- Abrasive Blasting Individual Parts and Replacing Floor Panels Part 5 Welding Front Frame Rails A Professional Induction Spot Weld was used to weld up the Front Frame Rails. A 180Amp Mig Welder could be used as a substitute. This would be a good time to think about using a good welding primer that will be welded(spot or mig) to prevent corrosion caused by welding. This treatment should be followed up with a corrosion resistant spray after finish painting the vehicle. Additionally, Drilling Rust Proofing holes and plugs will allow the spray to go where the factory box panels didn't. Part 6-Fabricating Wheel Housing Panels Part7- Replacing Front Door Skins and Lead Soldering Small Rust Damage Part 8-Repaiing Front Fenders and Rear Quarter Panels Part 9-Repairing Rear Quarter Panels-interior and exterior Part 10-Repairing Rear Back Panel Part 11-Repairing Inner Hatch Deck and Taillight Housing Area and Repairing Wheel Housing Part 12-Repairing Side rocker Panels and Tail Light Housing Area - Part 13-Replacing Side Rocker *NOTE- After watching these videos, you may think Japan Body Shops are primitive compared to American Body Shops. The real reason is that Japan has a very strict Vehicle Safety Code. It is so strict that most cars have only a 5 year life especially in urban areas( Tokyo, Osaka,etc). Scrap Yards in Japan are full of seemly good condition vehicles that can not driven on Japanese roads. Japan Body Shops have a huge supply of ":used parts". So much, they can order replacement parts such as car door in the exact factory color needed. As most cars are only 5 years old and under strict safety standards, there is no market to do corrosion repair except for those people will to pay the big dollars to restore popular cars. I could not believe this fact till I saw stacks of "perfectly good cars" with no collision damage on them in the junkyards of Japan. Part 14-REplacing Rear Quarter Panel Part 15-Repairing Rear Panel. . Part-16-Reparing Front Crossmember Part 17-240Z on Frame Machine to check Frame Alignment and pulling the Frame to put it in specifications. The Left Side (Strut Tower) is bent in about 1/2" so they pulled it with a Hydraulic 10 Ton Ram. This was only small damage to the frame but would affect Toe -in, Camber and Caster Specifications. Part 18-Repairing Front Frame Rail Inner Structure Part 19-More Frame Repair Work Part 20-Fabricating Front Crossmember Panel This Video demonstrates creating Contours on Sheetmetal with only Hand Tools. - -
Heavy Duty frame rails and connectors
toolman replied to toolman's topic in Gen III & IV Chevy V8Z Tech Board
SEMA SHOW LAS VEGAS ,NV Nov. 1 to Nov. 4, 2023 I went to the Sema Show from Monday to Thursday. Because of Covid, I missed going to Two previous Shows. This years Sema Show was Huge in size. The Show now occupies the whole Las Vegas Convention Hall area plus all the outside area of the major Halls. Also, They built a Giant Building called the West Hall that was the Convention Hall Parking Lots. So the Hotel Shuttle Buses dropped Attendees about 400 yards from the Convention Property. I was so tired from walking around the Show and must have walked 4 miles each day. I tried to take pics of Nissan and some other JDM Cars for you guys. Please forgive me if I could not remember all the car descriptions to go with the pics. Pics from the outside of the Main Show Halls: Crowd of people watching Live Burn Outs and Optima Street Car Races, Inside the Halls Computer Guided Upholstery Sewing Machine Lowered Nissan 370Z Dodge Charger with a 392 Late Model Hemi with Twin Turbochargers Electronic Controlled Mufflers which Driver could control the Exhaust Sound. Drifting VIDEO- 1500 HP 5.9 Cummins 24 valve turbocharged motor Drifting Demos in Exhibition Area ttps://www.youtube.com/shorts/IgrRcIZNwas Custom Made 4 Rotor Mazda Race Car Driver Seat area This Mazda puts out 2000 HP and costs $500,000 to build!!!!!!!!! Skyline with Full Liberty Walk Body Kit Skyline with RB30 with Huge Turbo Traxxas had a huge Rock Climbing display where people could try driving RC Four Wheel vehicles on it. B is for the Build had a Lambo wit Twin Turboed LS motor with Carbon Fiber Body Panels. This Purple 240Z with LS9 Sugercharged Motor was one of about a dozen cars in the Optima Ulimate Street Csr Races. an Older Nissan Skyline Beautiful Leather Interiot in the Toyo Tires Booth 240Z Motor Compartment exerior of the 240Z Another Build for the Build Project Formula Race Car BMW with a one of its kind V-12 motor Mercedes V12 motor. A Wild Custom A Single UTV Built on Top of Two Big Jet Skis Closup up the Frame between the UTV and the Two Jet Skis !970 Datsun Restro BRE Race Car Another LS Swaped JDM Race car Hand crafted all Alumunim BMB with Suicide Frant Doors Artist used Marker Pen to decorate this car. Next-Back to Finishing Air Condimtioning Installation I will be heading to Tokyo so the next posting maybe after Xmas so Happy Holidays to You and Yours111111 -
Heavy Duty frame rails and connectors
toolman replied to toolman's topic in Gen III & IV Chevy V8Z Tech Board
Before I go to Air Conditioning Installation. The construction of the Rear Tow Bracket will be covered. A Rear Tow Bracket is a necessity to hold the vehicle securely when towing the car with a Flat Bed Tow Truck. The Bracket also comes in handy if you ever end up in a ditch. Started off by Constructing a Card Board Template . The Bracket will be cut out of !/4" Mild Steel Plate with a Plasma Cutter. Then Finished Shaped with a 4 1/2" Angle Grinder. The Bracket was then Powder Coated RED. It was installed on top of the Factory Rear Bumper Bracket. Rear View of the Rear Tow Bracket. Air Conditioning Installation There are many ways to install Air Conditioning in a 240Z. Since I had constructed my own engine mounts, most After Market AC Compressor Mounts interfered with my Custom Made Motor Mounts.. Dirty Dingo Mount Kit was one example of these kits. ITC Billet was another kit that would not work with my mounts. Kwik Performance #L10291 Air Compressor Mounting Kit that located the compressor in front of the Right Side Cylinder Head. Also, the Location was not too high like many After Market Kits. Because of the 240Z Low Hood Configuration, clearance would be a problem. But, using the Kwik Performance Kit would require replacement of the Water Pump and Harmonic Balancer(about $236 additional cost on top of $230 Kit cost). These parts were required to move the Serpentine Belt ! 1/2" Forward. AC Delco Water Pump # 252-976 from $156-Amazon was used. Note- 1 1/2" height differance AC Delco Harmonic Balancer #19300488 from Amazom $85 Also, Note - 1 1/2" height differance LS Harmonic Balancers require a 3 Jaw Type Puller to remove the Balancer from the Crankshaft. This is because LS Balancers do not have any Pulling Threaded Holes and also require a Spacer Rod under the Puller Screw. If you do not have one, some Part Stores have them to Rent Out. Also, A Harmonic Balancer Installation Tool Note-Spacer Rods under Puller A Harmonic Installation Tool will be necessary to install the New Harmonic Balancer on the crankshaft. Using a heavy hammer to install the balancer can damage the Rubber Inert Ring in the Balancer. i will continue this AC Installation Process later as I am leaving for the SEMA SHOW in Las Vegas this weekend. I will post pics from the show when I return. -
Heavy Duty frame rails and connectors
toolman replied to toolman's topic in Gen III & IV Chevy V8Z Tech Board
calZ, Thanks for the Complement. Rushing to make a Deadline can be exhausting but getting complements make all the work worth-while. Toolman -
Heavy Duty frame rails and connectors
toolman replied to toolman's topic in Gen III & IV Chevy V8Z Tech Board
Preparing for Local Car Show- There was a Local car Show in my area on Labor Day. Everybody was encouraging me to enter my 240Z in it. But, there was still a lot of work to make it even decent. Installing the Interior Carpet- Interior Innovations provided a Full Eight Piece Precut Carpet for about $700. The fitting was good and was made of Good Materials. I had to decide which method to fasten the carpeting to the metal floor. Went to Home Depot and found Double Sided Industrial Grade Velco tape (cost $30). So No Drilling and Screws were used. Epoxy Adhesive was used the hold the Velco Tape down. Passenger Door Panel- Driver Side Door Panel- Passenger Side Carpeting- Fabricating Front Tow Hitch- As this car is lowered, In case when the car would need to towed, the normal method of sliding a tire lift under the car would not be possible. The Fiberglass Air Dam is in the way. So Towing on a Flat Bed Towing would be mostly likely method available. But, you still a way to hook up the car to winch it aboard. So I decided to fabricate a Front Tow Hitch. the Hitch was constructed of !/4" Steel Plate and bolted to the front frame rail. Hitch was bolted to the Frame Rail The Tow Hitch sticks through the Front Air Dam under the Bumper. The Labor Day Car Show- There were about 400 assorted cars at the Show. Everything from 32 Roadsters, 57 Chevys, Cobra Cars, Blown Gassers, VWs, Camaros, Corvettes, Vipers, Hell Cats, Low Riders, etc were there. I spent most of the time there, telling people "What kind of Car it was? - !971 Datsun 240z What is a Datsun? Nissan introduce their Brand New Car Line as "Datsun". There were even some Japanese Tourists asking questions about my "FairLady"( name of the.. 240Z in Japan). I did not have time to even walk around and check out the other cars at the show. But my car and I were luck to be filmed for an upcoming Local TV Car Show. Here are some Black and White Versions of the Pics. Black and White Photos really gives a Restro Mod Feeling. Next-Air Conditioning installation -
Heavy Duty frame rails and connectors
toolman replied to toolman's topic in Gen III & IV Chevy V8Z Tech Board
Sorry for not posting in a while but I was rushing to get my 240Z finished enough to put it in a local car show. There were some more things to do in a short amount of time. Anyway, back to posting- Door Panel Repairs- Both Door Panels needed to refinish the original Horizontal Chrome Trim on the upper side of the panel. See pic below. To repair this, I purchased 1/4" Chrome Pinstriping Tape from Amazon( for $6). First, I used a small paint brush to apply a layer of Contact Cement on the Trim Piece. Allow the Contact Cement to dry to the touch before applying the Chrome Tape. Apply the Tape lightly first then checking it for straightness before pressing it down with your index finger. Trim ends with a Single Edge Razor or Razor Knife. Closeup view of the Repaired Chrome Trim Moulding. This repair method can also be used on Door Arm Rests. Using Velco Heat Sleeves- Velco Heat Sleeves were used to protect electrical wires near the exhaust from burning, Cutting the Sleeves will allow the Velco pieces to unravel as they are only sewn on. so I use a Hot Glue to fasten the Velco Tape on. Heat Velco Sleeve put on Starter Wiring near the Exhaust. Velco Heat Sleeve on Oil Pressure Sensor Wiring. Holley 3.5" LED DISPLAY SCREEN-one of three possible screen layouts available. ELECTRIC POWER STEERING in OPERATION- Note - Easy turning of Steering Wheel with 11" wheels and 285/17 tires. LS3 First START UP-Sounded Great! Next-CAR SHOW APPEARANCE -
Heavy Duty frame rails and connectors
toolman replied to toolman's topic in Gen III & IV Chevy V8Z Tech Board
Removing Fuel Sender unit- To Check your Fuel Tank Sender Unit Electrically, you must remove the Unit from the Fuel Tank. First, you must remove the Passenger Side Strap as it is right over the sender unit. If the Tank is relatively empty, the Drive side strap alone will hold the tank up. Now, you can remove fuel from the tank so when you remove the sender, fuel doesn't leak on you. To remove the sender, most people use a screwdriver and small hammer to tap the sender tabs to release the locking ring. I decided to make a Sender Removal Tool as the tool will make installation easier. Using a Hacksaw, I cut about 1 1/2" section from a 2" exhaust pipe. Then,I cut Four Slots into one end of the tubing. Sender Locking Ring and Removal Tool The slots were cut and bent 90 degrees to fit the Locking Ring. A crossbar was added so a 3/8" socket could welded on to aid in sender installation. Fuel Sender Removal Tool was painted Gloss Black. Testing the Fuel Tank Sender Unit- The Sender Unit can be tested tested electrically using an OHM Meter. Place the two Leads on Sender- Yellow and Blacl-ground wires. Empty Reading should have about a 3.7 OHM reading Half Tank Reading should have about a 32.0 OHM reading Full Tank Reading should have about a 86.4 OHM reading Adjusting the Fuel Sender- Id the Fuel Sender has to be Bent alot, the Arm can be removed to prevent unit damage. Loosening this screw with a Phillips Screwdriver. Bending the Upper Arm Stop will effect the Full Reading Bending the Lower Arm Stop will effect the Empty Reading. Next-Starting Car Up -
Heavy Duty frame rails and connectors
toolman replied to toolman's topic in Gen III & IV Chevy V8Z Tech Board
Walkerbk, Yes, I had to trim the back area of the Tocket Bunny Flare to provide tire clearance when turning. I tried to maintain at least 1/2" clearance between flare and tire during the full tire movement. I think this tire clearance also allows for body roll too. Toolman -
Heavy Duty frame rails and connectors
toolman replied to toolman's topic in Gen III & IV Chevy V8Z Tech Board
WHEELS AND TIRES- The Wheels that I selected were custom made by Love20Bee in Los Angeles. They specialize in custom wheels especially for JDM cars. I wanted Watanabe Insets with deep offset wheel barrels. The owner has several 240Z himself. The Front Tires are Nitto G2 285/40/17 with 11" Tread Width. The Rear Tires are 315/40/14 with Thread Width of 12" The Wheels are Custom Made with Watanabe Inserts(with Dark Grey Metallic Spokes) with 11" Wide barrel in the Front and 12" Barrels in the Rear. Checking for Leaks. Wheels and Tires Installed. Rear Wheel l Front Wheel Cutting Rocket Flares for Tire Clearance- The Greddy Rocket Bunny Flares had to be cut because of the Deep Wheel Offeset for Tire Clearance. Front Flares before Cutting. Note-Without cutting, Tires could not turn. Inside view of Front Flare before Cutting-clearance. About 3" had to removed for Clearance. Rear of Front Tire Clearance After Frontr Cutting View of Front Tire View of Front Tire View of Rear Tire Rear Tire Front View Rear View of Rear Tire Top View of Rear Flare Rear Tire Clearance with Muffler/Exhaust Pipes. Inside View of Tire Clearance. Full Right Turn Side View of Car Four Watanabe Wheels (Polished lips and Gun Metal Spoked Face---$4000.00 Love20BEE 2nd Day UPS Freight 240.00 Four Nitto G2 285 and 315/17 tires (Amazon) 860.00 __________ Total $5510.00 -
Heavy Duty frame rails and connectors
toolman replied to toolman's topic in Gen III & IV Chevy V8Z Tech Board
Finishing the Exhaust System- The Two Rear 2 1/4" Exhaust Pipes make Right Angles heading to the Mufflers. Midway to the Mufflers, V-Clamps connect the pipe to the Mufflers. Rear View of Rear Exhaust Pipes with V-Clamps. Exhaust Pipes are welded directly to Mufflers to provide clearance for the rear tires. I welded the Two Thrush Hush Turbo 2 1/4" Mufflers together. Note the straight 1/2" Steel Rods are the Upper Muffler Hangers. The Forward Muffler Hanger is bolts to the Rear Deck Floor Pan. Two Rubber Mounts are used because they will be supporting Two Mufflers. The Rear Muffler Mounts are also bolts to the floor pan, Two Rubber Mufflers Hangers are also use to support the mufflers. Pic of the Rubber Hangers seperately. The Two Mufflers can easily installed by pushing the Steel Stud into the Rear Mufflers. Then, lifting the Mufflers upward and pushing the Forward Rubber Mounts into the Forward Stud. Then lifting the Mufflers and insert the Flat section of the mounts onto the Floor Stud Bolts. With the Mufflers hanging from their mounts, you just have align the Two Muffler Exhaust Pipes to the Straight Exhaust Pipes under the Differential. Then, install both V-Clamps. Both Mufflers Hanging up. Rear View of Mufflers Installed. The Muffler Rear Exit Hole was completed with a little bodywork. A 3/16" Brake Tubing was bent to form the Muffler Exit Area shape. It was tacked welded to the body then Polyurethane Seam Sealer was applied to seal the both edges of the brake tubing. Body Filler was applied to smooth out the edge of the Muffler Exit. After sanding the body filler, the area was painted with White Polyuretane Paint. Repairing the Brake Light Socket in Dash Board The Brake Light Socket has a problem with its Grounding Connection. It consists of a Tiny Strip of Brass that contacts the socket hole to make Ground. This Ground Strip usually breaks off or becomes loose. I used the Terminal Retaining Strip on a 6.3 Brass Terminal(See Pic below} Note-Small Terminal Retaining in the Terminal. Using a Small Electronics Soldering Iron to solder the brass strip to the bulb socket. I tested the bulb on a piece of sheet metal with a 15mm hole to stimulate the dash board. Testing the Ground Connection. It Works!! -
BBK and wheel choices?
toolman replied to LooseRocks's topic in Brakes, Wheels, Suspension and Chassis
Robo, Have you tried wheel spacers to overcome your caliper interference problems? Baer Brakes has 4 X 114.3 spacers(.25",.375",.500",.625",.750",.875", 1.00") available for $70. The inner diameter is 2.50" so you so might need give a little machining for original Z front hubs. They made of Billet Aluminum so you can use them for racing if necessary. Also, you would have to use extended wheel studs. The total cost still would be minimum. Toolman -
Heavy Duty frame rails and connectors
toolman replied to toolman's topic in Gen III & IV Chevy V8Z Tech Board
Led Flasher- I think I forgot to mention that if you are replacing the vehicle's incandescent light bulbs with LED Bulbs, you must use a LED Flasher. If you don't. the turn signal and hazard lights will not blink and will stay solid. This is because the LED bulbs will not draw sufficient amperage to cause the Flasher to heat up and blink. I got mine from Amazon for about $12. The Led Flasher came with an external ground lead too. Front Fiberglass Bumper- The Greddy Fiberglass Bumper that came with the Rocket Bunny Body Kit has just been laying on the bumper waiting for the finishing touches. Bumper reinforcement frame built from with 1" square steel tubing. The Fiberglass was first aligned with the front body panels. Locitite Tile Foam was used temporarily to hold the bumper in alignment so I could fill it with Pour Foam. But the bumper with reinforcement had to be placed in a level and vertical position with the front of bumper facing downward. Shooting the Foam to just hold the Bumper and reinforcement in alignment. Pic of the Tite Foam after expansion, it was trimmed down. Now. the Bumper was ready for the Pour Foam purchased from the local Marine Supply Store for $30). This Polyurethane Foam will fit the space between the reinforcement bar and the bumper. This will create a solid bumper instead of just a hollow fiberglass shell. To use, mix equal parts( one to one ratio) but you have only a very short time before the mixture will expand-only minutes. The foam will expand to 5 or more times the original amount. I would suggest that you mix only one spoon full to see how much the Pour Foam does expand for the first time. I made several pours instead of doing a single pour. Once the Pour Foam fully expands, you can still immediately make the next pour. I used a old hacksaw blade to trim the expanded Foam as it works better than a knife or razor blade. After triming and sanding the Foam to 3/4" from the edge of the bumper, I poured Finishing Figerglass Resin over everthing inside on the bumper. This will seal everthing up so water can not enter. This process also will strengthen the bumper although it will create addition weight. Then exterior of the bumper was painted with Gloss Black Polyurethane Paint then buffed. Back View of Left Side of Bumper Back View of Center Section of Bumper Back View of Right Side of Bumper Made two Wooden Stands to hold the Bumper in proper position for putting the Pour Foam into the Bumper Cavity. Front View of Finished Bumper Finished and Polished.. Wilwood 1" Master Cylinder Installation- The Factory Master Cylinder had a 7/8" bore and Wilwood 1" Master has a 1" bore. Its front reservoir is behind the rear reservoir so I fabricated new Master output lines. I used Napa Bendable 3/16" brake lines because the lines had to be bent in a "U" shape to go under the Brake Proportioning Valve. It is made of Nickel and Copper Steel . Also, the Wilwood Master output lines are SAE 3/8NF so I used NAPA Bendable 3/16" lines with 10mm brake nuts. Then, I cut off one end of the line and remove the Metric Line Nut and replaced it 3/8NF Brake Line Nut. Then Double Flare that end. Now, you have a Brake Line with Metric Brake Line Nuts for the Proportioning Valve side and SAE 3/8"NF on the Master cylinder side. Note-Nickel and Copper Lines different color While I was working there, I decided to construct a Heat Shield for the Brake Lines. As usual. I made a Paper Template for the Heat Shield. It was constructed out of 20 gauge Aluminum sheet. Made a Trial Model of Key Hole Bolt Hole View of Shield from bottom of the frame. Put a fold on the Shield on the bottom to add strength. Then the Shield was buffed and polished. Finished Shield. Note-A simple "KEY Hole" mount design was used. Loosening the Proportioning Valve Mounting Bolt and moving it outward slightly. Align the mounting Bolt with Round Section of the Key Hole. Then slide the Shield downward over the bolt. Tighten the bolt. A Simple Method but effective for tight spaces. Firewall Forward View of Shield Backward view of Shield. -
Heavy Duty frame rails and connectors
toolman replied to toolman's topic in Gen III & IV Chevy V8Z Tech Board
Dome Light Repair- The Original Dome Light Assembly was found to be defective when I tested it before installation. The problem was the Light Switch was not functioning. I found a 12vt Micro On/ Off Switch on Amazon for $12 for six switches. The defective switch was removed and prepared for new one. Disassembly Preparing base for new switch New Micro Switch Attached to Base with JB Weld. A LED Bulb will replace the Incandescent one later. Closup Pic of Dome Light Modifications IMG_4187.MOV Dome Light in Operation Transmission Floor Shifter Boot Cover- The Transmission Shifter Boot Cover will actually consists of two covers -Rubber and Leather ones. The Rubber One will stop Heat and Hot Air from entering the interior. The Leather One is' more of decorative reason. The Shifter Mounting Plate was constructed of 22 Gauge sheetmetal. Test Fitting of Shifter Mounting Plate Reverse Lockout Solenoid Switch- I decided to keep the Reverse Lockout Solenoid but simplify its operation. A Momentary On/Off Switch would be mounted rignt behind the Shifter. It would be located a {olished Aluminum plate on the Center Console. Operation is simple-when you want to shift into Reverse Gear, Your Left Hand will press down on the Reverse Lockout Momentary Switch( activating / openin the Lockout Gate. The Right Hand will shift the Shifter Lever to the Right Direction and Up into Reverse Gear. 12vt Water Resistant Momentary Switch (Amazon $12) Reverse Lockout Solenoid Momentary Reverse Lockout Switch on the Center Console Note-Leather Shifter Cover covering over the Rubber Shifter Cover. Note-Extra Room on Aluminum Console Plate for Future Switches( Fog Lights, Nitrous,etc) Problem with Precision Door Weatherstripping- Some other Z members also had problems with Precision Door Weatherstripping. The Precision Door Weatherstripping was made of Thick and Hard Rubber materials. When it comes across Tight Fitting Contact areas, it does not compress enough. Thus, you had to slam the doors until the weatherstripping compresses. Later model car weather stripping are made of very soft and large air pockets for compressibility. I found that major problem was at the top of the door edge meets the rear quarter glass. The Weatherstripping is squeezed into very tight area but can not compress enough to function properly. So you can replace the weatherstripping with a much softer material or increase the door gap. Since my door panels were worn and I was thinking of constructing the door panels out of 22 gauge Aluminum sheet, I tried to do some metal working on the panel. Taking off the interior covering of the upper rear corner of the panel, it was constructed a steel metal. Upper top corner of Drivers Door So if I could "flatten" this area, it might give enough room for the weatherstripping to fit. The Large Hump would have to be "slit' in couple places to allow the flattening process. A Dremel with Cut Off Wheel cut the slits. Cut another Slit on the bottom edge. Pound the area "flat" with Hammer with panel on a flat hard table. A third Slit allows more flattening. The over lapping slits were tack welded. On the Door Side, I replaced the Door Glass Vertical Upper Mounting Bolt(6mm) with a Counter Sink Phillips To gain even more space. Note-Flattening allowed the door to shut now. -
hatepotholez, I had a similar problem with new Precision Door Weatherstripping as you. I fixed it in one day and did not spent any money on the repair. I will post how I did it in my next post -V8 Z forum Gen III & IV Chev V8Z coming soon. Check it out! Toolman
-
Heavy Duty frame rails and connectors
toolman replied to toolman's topic in Gen III & IV Chevy V8Z Tech Board
Sorry for the delayed posting, I had to do some house repairs. More Wiring to do. Starter Solenoid- My AC Delco Starter#1266257 was one of those Mitsubishi Gear Reduction ones and I was having a difficult time finding the correct Solenoid Wire for it. I ordered three different Solenoid Wires for it and all of them didn't fit. I finally found the correct one on Ebay. It was specifically for 2019-22 Camaro with a LS3 6.0L. It costs $59.00 but at least it fits. The Solenoid Lead Wire is fully insulated too. Pic of Starter and Solenoid Fuel Pump Relay- As my Holley In The Tank Fuel Pump is far away from the battery, I decided to to run a Dedicated Fuel Pump Relay. It is rated at 60-80 AMPS. I already ran a 12 Gauge Wire from the battery to the Relay in the harness. The Factory Electric Pump "Green" Wire was used to trigger to relay which will then send Full Battery Voltage to the Pump. So If I decided to upgrade the Fuel Pump to a bigger one, eveyrthing is done already. Rear Tail Lights Repair- Upon inspecting the Rear Tail Lights(Left and Right Sides) , I found corrosion on Sockets and Ground Wires on the sockets and related wiring. Disassembly of the Lamp Sockets so I decided to repair the ones that need repair or replacement. Amazon has Socket Repair Kits which contain the necessary parts and wire leads. Make to get the correct dimensions for the socket and type of sockets( two wire, one wire, two contacts one contacts, straight ears or offset ears. If the new sockets are loose in the plastic holder, you put some Hot Glue on the sockets to make them fit tight. Original Factory on Left and Replacement on Right The Single Contact Lamp Socket replacement To be used, the flat bracket must be cut off. Before connecting the Lamp Sockets to the harness, all of the Lamps were tested. Note- I went to LED Bulbs for the whole car. not just the Rear Lights. Led Lights will also lower the Amerage draw compared to the original Incandescent Bulbs. I found some White Turn Signal Connectors discolored Brown because of Overheating. Incandescent Bulb LED Bulb Finished Repaired Harness Still More Electrical Work Coming Up. -
Heavy Duty frame rails and connectors
toolman replied to toolman's topic in Gen III & IV Chevy V8Z Tech Board
mutantZ, No, the lower section of the steering column is not made of plastic. Both factory and Silvermine columns are constructed with metal components. All modern steering columns consists of both collapsible exterior housing and steering shafts. The methods to accomplish this task may differ but the end result is the same. Collapsible steering parts must be replaced if damaged to provide same degree of protection. Even when working on these components, care must be used not to damage them (excessive force like hammering,etc). -
beton, Looking at the pics that you posted, Maybe this damage properly occurred previously and was then repaired. Most common repair on this type of rack and pinion is worn out INNER TIE ROD ENDS. The RACK travels in a very straight line if not. you will definitely have a "Bind" when turning the steering wheel. In this case, the Rack would be replaced. The cause could be from hitting a rock damaging Rack or Bad Accident. I am including copies of Factory Service Manual -Serving the Steering Rack pages. Does this help? Toolman
-
Heavy Duty frame rails and connectors
toolman replied to toolman's topic in Gen III & IV Chevy V8Z Tech Board
MutantZ, Here is a pic comparing Factory Steering Column vs Silvermine Power Steering Column. Note-the Collapsable Section on the Factory Column Here is pic of the Factory Column with Internal Parts Exposed. Does these pics give the information that you need? Toolman -
Heavy Duty frame rails and connectors
toolman replied to toolman's topic in Gen III & IV Chevy V8Z Tech Board
Constructing FUSE / RELAY AND JUNCTION BATTERY PANEL Because of limited engine compartment space, I decided to build a Fuse/ Relay and Battery Junction Panel in the Passenger Side of the Transmission Tunnel. The Panel was made from 1/4" Black Sheet Plastic. The Dimensions were about 7" x 10 1/2". The Legs were made to provide 1" space underneath to run wiring . The Plastic was bent by using a straight edge and 1000 Watt Heat Gun. The Basic Layout Plan for the Panel. This Diagram show wiring for Speedometer Convertor and Electric Power Steering. I use Four 80/ 60 Amp Relays as the relays will be powering more than one circuit at a time. This 4 Pin 80/60 Amp 12vt DC Waterproof Relay comes with 12 AWG insulated wires. Costs $38 for Four Relays from Amazon This pic show a 40 amp In Line Fuse Waterproof Housing with 10 Gauge wire. This In Line Fuse will used as the Terminal Fuse Block was rated at only 30 amps. This Fuse was utilized for the Electric Power Steering Motor. This Dual Rows Block Terminal Strip from Amazon costs $8 for two. This 6 Way Fuse with 5 Fused Circuits with seperayte Postive anf Negative Bus Bars costs $17 from Amazon. The top 12gauge Red Wire has a inline waterproof 40 AMP Fuse. This Fuse protects the Electric Power Steering Motor. I could not use the Fuse Block as it was rated at only 30AMPs. The White Relay wires trigger powers the Blue12vt wires that connected to the Positive Bus Bar. Then the 12volts exit the Relay through the Red Wires. Then the 12vt crosses the conection to the Output wires. The Vertical Fuses protected each circuit. The Black wires on the Right Side connect to Negative bus bar(Ground). The Top 1/4" threaded stud connects to Battery Positive terminal. The Lower 1/4" threaded stud connects to a Negative Ground strap. The Panel with the wires all connected. Note- Wires when possible are run under the panel to provide a clean appearance. Majority of the Output Wires were required Key On Operation. Some Devices like the Holley Terminator Computer, Silver Mine Power Steering required straight Battery Power but still ran thru a Fused circuit. k The Relay Panel was mounted to Transmission Tunnel with battery cables attached. A Marine 12vt Battery Cable holds cables from the Relay Panel,Alternator and Starter Motor. The Negative Cable attaches with a Post Master Quik Disconnect Switch. It can be disconnected with just a twist of the Black Knob. Costs $14 from Amazon More Wiring to come.