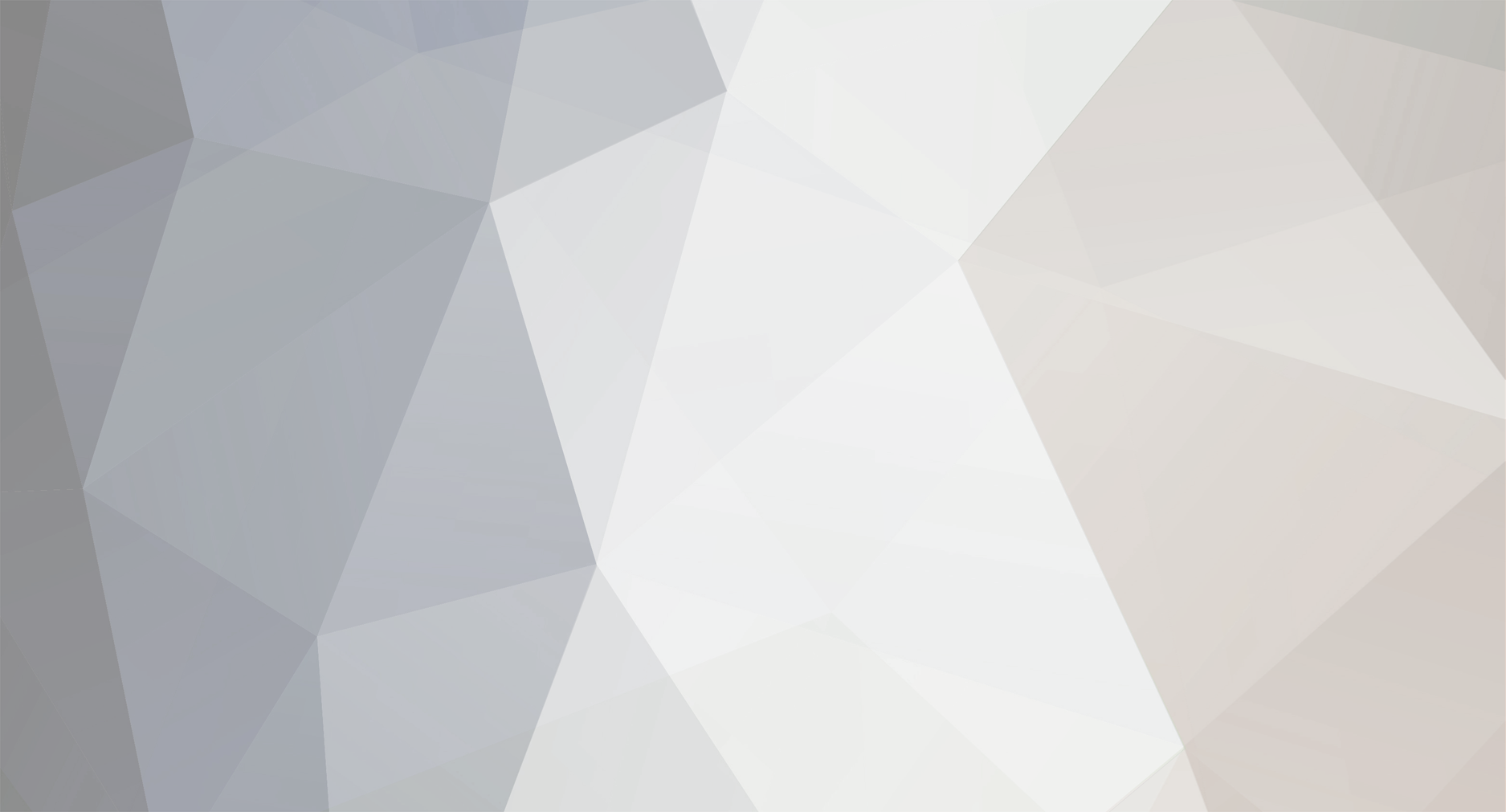
toolman
Members-
Posts
562 -
Joined
-
Last visited
-
Days Won
16
Content Type
Profiles
Forums
Blogs
Events
Gallery
Downloads
Store
Everything posted by toolman
-
Heavy Duty frame rails and connectors
toolman replied to toolman's topic in Gen III & IV Chevy V8Z Tech Board
I had planned to assemble the Front and Rear Suspension to the Z but decided to work on the interior parts first. Door Glass Regulator was cleaned and lubricated. The Door Glass had a lot of Water Spots from being parked outside. These Water Spots were removed with #000 Steel Wool and Hand Rubbing Compound. Rub in a Circular Pattern to remove all the spots. Looked like Brand New Door Glass. Before Disassembly and Rebuild. Tools used to rebuild the Quarter Glass: Plastic Glass Tool. Rubber Hammer. Tire Lube Brush. and 1/8" Nylon Rope. One area of reassembly was the 1/4 Window Glass Frame. Because of the New Weather Stripping. squeezing the Frame together posed a problem. This was solved by wrapping a 1/8" Nylon Rope around the frame and 3/8" x 6" Bolt. Twisting the bolt between the rope will cause the rope to get tighter and tighter. This action will squeeze the frame together and allow the installation of the frame screws. Now, check the corner of the 1/4 frame with the long ends. Note-A strip of Rubber added to the Frame. This Rubber Strip fills the gap so the Outer Weather Stripping Gasket does not leak. Check the Old OEM weather stripping. It probably has a similar rubber strip that is not included with the replacement weather stripping. The Outer !/4 Glass Weather stripping was attached with Contact Cement , Use a Acid brush to apply the Glue. Apply the Contact Cement to Both Sides (gasket and the Frame). Make to allow the glue to dry for 10 to 15 minutes before sticking them together. Wrap the1/8" Nylon Rope tightly again around the Weather Stripping and then knot it so it holds till the cement dries. Installation of the Assembled 1/4 Glass on the car usually requires two persons. As the Glass must be pushed both rearward into the body and inward to attach the mounting screws. Installation Complete. The 1/4 Glass Frame was painted with Sem Products Trim Paint Black to match the Race Car Theme. In this case, the Bumper Guard and Bumper Rubber Strips Holes were going to be welded closed to provide a more Clean Look. !/8" Steel Plugs were cut and fitted into the holes before welded. Welded Holes after Grinding Bumper Parts Poly Urethane Primered. Single Stage Black Polyurethane Paint was used to paint the Bumper Parts. Bumper Installed on car Side View Center View -
Heavy Duty frame rails and connectors
toolman replied to toolman's topic in Gen III & IV Chevy V8Z Tech Board
Thanks, Guys After getting the Air Compressor parts, I did a complete overhaul on the FS Curtis D96A compressor pump. Replaced Intake and Exhaust Valves, new Head Gasket, new Piston Rings and new Con Rod Bearings. After the Compressor was repaired, The Greddy Rocket Bunny Flares were installed. On Ebay, Z Spec Design had their Rocket Bunny Kit Installation kit for $90. These tools were used to install the Flares. The Cleco Clamps were utilized to hold the Flares in place while drilling. The Drill drilled the mounting holes into the Flares. Also, it drilled the Body side for the Threaded Nutserts. Drilling the Flare Drilling Body for Nutserts. I added a 11" extensions of 1" square tubing to the Nut Setter( lengthening its arms gave it additional leverage). Threaded Nut installed. I recommend all insets be rethreaded. Sometimes the inserts are distorted during installation. Installed The Paint and Materials for this car was about $2000(Jobber Cost). Sherwin Williams Ultra 7000 Poyurethane paint(Basecoat) and CC2000 Clear Coat were used. I also used the 3M TRiZ Sanding system which consists of P1000, 1500 and P3000 Velco Sandpaper was utilized too. This method reduced the polishing times drastically. Next thing to do: Installing Front and rear Suspension on the car. Happy Fourth of July Holiday to everyone!! -
Heavy Duty frame rails and connectors
toolman replied to toolman's topic in Gen III & IV Chevy V8Z Tech Board
The Whole car was recoated with the Final Poly Primer then completely block sanded again. After the Final Sanding, masking of the car was next. As the car had no front windshield, door glass and rear hatch installed, there was nothing to tape to as in regular masking. So Back Masking was utilized. Back Masking is masking from the rear or from the inside out. To begin with, 3" Masking Tape was applied around the edges of the Front Windshield Opening(from the inside) so the sticky side of the 3" tape protruded outward about 1". Two or Three Vertical 3" Back Tape were added to provide support for the Masking Paper. Add 3"Horizontal stripes of tape on the Vertical Tapes to make them tight as possible to support the masking paper. Masking Paper was added from the top edge of the Windshield to the bottom edge of the windshield. Make the masking paper a little larger. Lay the masking paper to the tape on the windshield edges and the vertical tapes. Don't press the tape and masking paper together yet. Using a new razor blade to cut the excess paper allowing for 1/2" of sticky 1" tape exposed. When you finish cutting the excess paper off, apply 3/4" masking tape to the 1/2" area. So your masking paper will squeezed between the Back Masked 3"tape and the 3/4" masking tape and be really secure. This view shows the Masked Widshield looks like from the inside. The Door Widow and Rear Side Glass was also masked with Back Masking. Since, the Rear Hatch was a large area to mask, a slightly different procedure of masking. I used a Welders Tie Wire to provide more support for the masking paper. Welders Wire A piece of cardboard also added to give support when pressing the masking paper and tape together. Otherwise, since the hatch area is closed off at the back, you can't stick your hand under the masking paper to press the masking paper and tape together. Note-The Hatch edges are Back Masked as the Front Windshield. The Engine Compartment was masked using the same as the Rear Hatch procedure. Used a X pattern with the Welders Wire in this case mainly because the availability of body holes. Now, I went about to mask the car for a TWO COLOR paint job. Note-Blue !/4" Pin Stripping tape was utilized to produce a sharper line than regular masking tape. Red Top White Bottom Rear Hatch and Hood being painted. Made a Paper Template for Racing Stripe. Flip Template over for the Opposite Side. Racing Stripe with Datsun Logo After Striping and Clear Coating Rear View Side View Unfortunately, after I clearcoat the Z, my garage 7 1/2 HP air compressor broke down. When I tried to start it the next morning, the air compressor would not build pressure. Lucky me, it did not happen when I was Clear Coating. So any way, I took the compressor pump apart. So, Come Monday, I will order the Master OverHaul Kit which has new piston rings, rod bearing and valve parts plus gaskets and various seals. Then I can Clear Coat the Flares, Soiler and Front Panel. -
Heavy Duty frame rails and connectors
toolman replied to toolman's topic in Gen III & IV Chevy V8Z Tech Board
Nelsonian, Thanks for the tip. I will post my solution when it happens, Here is a pic of the Right side Rain Gutter finally primed. Came out real smooth. I had constructed a frame to hold the Spray Booth Exhaust Flilters but got rid of it as it took up too much space. So I came up with a much more simplified method to the filters. I just screwed a dozen clothes pins to the garage door. Inside view Simple and but Effective. Outside view of Exhaust Filters. Now, Back of Body Work: I utilized Black Primer in a spray can to locate Low Spots in the bodywork. Only a Light Coat of Black Primer Spray is necessary, Use Sanding Blocks( short and long) Long one is for large areas (roof and hood). Start sanding in a Diagonal Direction then sand over the cut in Opposite Diagonal Direction to create a "X" Pattern. Using this method, the low areas will show up as dark spots. Hood with the Low Spots covered with a thin layer of Body Filler. To Restore the Body Lines on the Doors, Apply 3/4" Masking Tape with its Lower edge run the new tape top on the Body Line. When you finish sanding along this edge, you end up with a nice straight body line. The 240z body line have a sharp edge so you cut the sharpness with the sanding block. creating a Body Line. The Cowl Panel sprayed with Low Spot Finder, Cowl Panel masked to prevent overspray. Cowl Panel with Low Spots filled. R/Quarter Panel and Door Sprayed. Right Fender ready for more sanding. This fixing low spots and spraying HD primer filler can go on for a couple of times. The 240z thin Sheetmetal (.023") body lends itself abundance of small dents. As a lot of you are "stuck at home " during this Pandemic and can't work on your 240Z, here is a solution: Hot Wheels 71 Datsun 240z Rocket Bunny car. Hot Wheels has several versions of Datsun 240z -completely stock to Radical Race Cars. Collect them or modify them. I will modify mine and post my progress. -
Heavy Duty frame rails and connectors
toolman replied to toolman's topic in Gen III & IV Chevy V8Z Tech Board
A Reinforcement was constructed for the Front Rocket Bunny Bumper. It was made of 1" x 1/8" square tubing with 3/16" bumper brackets. First, a template of the reinforcement was made out of cardboard. Bumper Brackets were made 3/16" Plate Steel and cut out with a 4 1/2 Angle Grinder. Pics of both Front Bumper Brackets Pic of Bumper Reinforcement Bar Reinforcement Bar mounted. Attempts to use Insulation Foam to attach the Fiberglass Bumper to the Reinforcement Bar failed. The problem was the difficulty to get the Foam evenly between the Bumper and Reinforcement. Because the Corona Virus, the solution to this problem will have to wait until more stores open up. Unsuccessful for now! I constructed Four Flat 16 Gauge plates of 16 gauge Sheetmetal to fasten the Front Flares to the Front Valance Panel. Note: The Plate is folded on the outside edge of the the Plate. This Fold greatly increases the strengthens the Plate. A Right Angle Die Grinder and a Tight Fit Drill Attachment were used because of the tight space. Inside Front Wheel Housing, pic of the Reinforcing Plates "sandwiching" both fiberglass parts together. Outside View of the "sandwiched" parts The Roof Rail Gutters were seam sealed with Fastline #FS2SL. It is a self leveling sealer and made for car rain gutters. Working Time is 10 minutes so you got to rush. It can be painted in 30 minutes and fully cures in 2 hours. It flows like water so don't forget to "dam" both ends of the gutter. The next day, the sealer flowed so much that I had to apply a second coat. If necessary, you can sand the sealer smooth. The Front and Rear suspension were removed to prevent the parts from overspray even with masking. The plastic curtains opened up and work area was cleaned in preparation for car painting. But, there is a lot of preparation(a whole lot of sanding and masking) before actual car painting. -
Heavy Duty frame rails and connectors
toolman replied to toolman's topic in Gen III & IV Chevy V8Z Tech Board
The Left Rear Flare was mocked on by creating a template of the completed Right Rear Flare. The Rocket Bunny Front Valance Panel mocked on the car, . Pictures of the Greddy Rocket Bunny Front Valance Mounting points. Note-the original holes were only 3/16". It was at this point that I decided to add additional mounts from the car frame to fiberglass front valance panel. Otherwise, it would not be strong enough for even a street vehicle. The mounting brackets would be constructed with 1/4"solid steel rod and 1/8" steel plate. Center mount was mounted to the frame extending to center of Valance Panel. Mig Welding of the side Valance Mounts The Valance mounts would extend to both L/R sides of the grille and marker lamp areas. Left and Right Mounts before Powder Coating. Left Valance Mount powder Coated installed The Front Flares were mocked on using Cleco Pins. Inside view of Left Flare The Grill was disassembled for sand blasting and powder coating. The Grille consists of 6-Horizonial grille blades, 4-Vertical mounts and 4-3mm x 8" Long Bolts. So I took a lot of pics so I would not forget where everything went. As the Grille is about 4 feet wide, it would not fit in my Powder Coating oven. So I constructed 2' x 2' x 4' box out of 3/4" plywood. It was lined inside with Aluminum Foil to retain the heat. A 2000watt Infared heat lamp provided the heat. Powder Coating the Grille parts. The Grille was powder coated with Flat Black Powder then assembled. -
Heavy Duty frame rails and connectors
toolman replied to toolman's topic in Gen III & IV Chevy V8Z Tech Board
I had planned to work on installing the front suspension parts on my Z but I discovered that my supply of Gold powder was almost gone. So while I waited for the Gold Powder to arrive, I decided to finishing cutting the Right Front fender for the Rocket Bunny Flares. Like the Rear Flares, I made a Template of the already completed Left Front Fender. Note- I use almost all the fender edges( top, back, front and bottom) to create the template. The more reference points that you use, the more accurate the template will be. Side view of template Put template on the Right fender then Transfer the trim lines using a Black Marker pen. A Tin Snips was used to trim the fender. It was used as cutting thin metal like the front fender, vibrates a lot and making it hard to control. Note- make sure to grind all trimmed edges to prevent future sheet metal cracks. Next thing to do was to clean all of the Front Suspension parts in preparation for painting or powder coating. The rear stub axles were prepped at the same time to conserve paint materials. All the parts were first cleaned with cup wire brush on a 4 1/2 electric grinder to remove the heavy grease, dirt and paint. Then a Heavy Grease Removal soap ( was used straight without dilution) was used. First, with the parts cleaning brush then with a air solvent gun shooting the degreaser( now diluted) to get those hard to get to areas. Blasting away Stub axles after paining with Black Polyurethane paint. Note- the rubber joint boots were masked off otherwise the axles would have been disassembled to remover them. The other suspension parts after Polyurethane Painting. Before Powder Coating After Powder coating A flange bolt powder coated Front crossmember mounted Note- new Camber adjusting bolts were installed. Front to rear view of Front Suspension. Note -The Powder coated parts gives a nice contrast with Gloss Black suspension parts. Side view of the Right Side Suspension It took a lot of cleaning, grinding, painting and powder coating but I think it was worth it. Next, installing the Wheel/Tire Fitment Tool on the Front Suspension to check it out, is next. -
Heavy Duty frame rails and connectors
toolman replied to toolman's topic in Gen III & IV Chevy V8Z Tech Board
Sorry for the delayed reply. My 87 HONDA TRX350 ATV transmission shifter was jammed in gear. As it required me to split the outer left and right cases, the repair took two days to complete. It had to be repaired as it occupies the garage opposite of the 240z and there would be no space to work. This Front Loader Conversion to my Honda ATV was done before I started the 240Z restromod. I scratch built on a 87 HONDA TRX350 ALL WHEEL DRIVE ATV IN about a year ago. It can lift 400lbs in the loader bucket and has a 30 gallon water tank in the rear for ballast. The conversion was made to be Bolt On Accessory and can be removed in about 30 minutes. Now back to the Z Project. All Four of the Flares were painted inside and out with Polyurethane Primer. Had problems removing silicone from the mold release on the flares. Had to use Wax and Grease Remover and HD Water base soap several times to get the silicone off. Due the Windy conditions, I had to paint the parts in garage so had the cover the 240z with Plastic Sheeting to prevent overspray. The Plastic Sheeting can be gotten from automotive paint suppliers. Wheel Fitment Tool Finally get to use the Wheel Fitment Tool that was made coupe of months ago. This was the closest size tire that I could find to use-225x 45x 18. The wheel that I will be simulating is Rota RKR 17 x 9 1/2 with 20mm negative offset. As the sample tire is not large enough, it will be used with the majority of the tire will be facing outward to check fitment. As I running lowered coilovers, the inner clearance with strut is not a problem. First, install the Fitment tool with two lower legs set to 18 " diameter and third leg retracted. Now, adjust the two lower legs tire width adjustors to fit securely. Now, Adjust the upper third leg to obtain the 18"diameter and adjust the tire width adjusters for a snug fit. The only wheel that I found that had specifications came close was ROTA RKR 17 x 9.5 with -20MM offset. I put its specifications on a wooden paint mixing stick. Remember that this tire is only 18" so the 9 1/2 tire will stick more inward. This stick show the wheel offset. The "C" line indicates the center line of the Rota wheel. The inner end of the stick indicates the width of a 274/45 tire. Front tire clearance shown Front to rear view Side View of the Wheel/ Tire Fitment Tool on the car. As the car is on a dolly and there is almost no weight in the car, something had to be done to set Ride Height. So I removed the upper strut spring section to allow upward movement of the suspension. I set the ride height setting the center of the wheel hub to the lower body line of the car. From most pics of street driven lowered 240z cars, the center of the rear hubs were in line with the body line. This is not perfect way but I think it is close enough to demonstrate ride height until I can actually load the suspension after the complete swap. For those of you, that wanted more tire fitment information, I bent a 1/8" wire shaped to match the tire cross section that you wanted to check. In this case, a 274 x45 tire cross section was created and bolted to one of the wheel legs. . You just rotate the simulated tire cross section to check any clearance issues with body and strut. Check Front Clearance of the flare. This rear view demonstrates what a 274 tire would look look like. Remember the 275 tire would extend to the end of the stick or about a inch more inward. The next thing to do is to put the Tire/Wheel Fitment Tool on the front suspension and see what tire/wheel combination could work on there. -
Heavy Duty frame rails and connectors
toolman replied to toolman's topic in Gen III & IV Chevy V8Z Tech Board
Rear Suspension Overhaul: A Threaded Steel Rod with nuts and assorted washers were used to install rear control arm outer bushings. This method was used because although slow, it has less chance of damaging the steel metal bushing housing on these control arms. Ordered ZDepot 50mm extended wheel studs and Muteki extra long wheel lug nuts from EBAY. They maybe necessary to gain proper wheel fitment later. The old wheels studs were removed by hammering them into the large metal tube. Hub parts were powdered coated. Lisle Tools Wheel Stud Installer only requires a 1/2 impact gun and lug socket to install the new wheel studs. The Hub Outer Bearing was pressed on the hub. The Outer Hub bearing was then packed with grease. The whole assembly was pressed into the strut housing. Now, by looking into the inner bearing bore-check the two casting cutouts to determine if the bearing is properly seated. After which. the bearing cavity and spacer is packed with grease. I used a paint paddle to spread the grease into the cavity. The Inner Bearing(non sealed one) is packed with grease. To install this bearing, you can use the old bearing to tap the new one in. Don't worry the old one won't get stuck in. Keep tapping it until a solid feeling and sound occurs for proper seating. id Coat the inside of the seal with grease especially the seal lip. Tap the seal with hammer( can use old bearing also) to about 3/16" below edge. Then, the flange. washer and locking nut are installed. A Dial !/2 Torque Wrench was used to torque the Locking Nut. Specifications call for 180 to 250FT LBS. The reason of the range is the Bearing Preload cannot be determined by Foot Pounds alone. So you slowly torque to 180 ft lbs then check turning torque and keep doing this till everything is right. The Hub Shaft nut turning torque is about 4 inch pounds. The shaft endplay is 0 to .0059. You will need a Dial Indicator to do this but not necessary. So you try to achieve all these parameters to get a accurate bearing preload. 1/2 Dial Torque Wrench A Dial Inch Pound Torque Wrench checking Turning Torque( about 4 inlbs) A Dial Indicator can be utilized to check for 0 to .0059" End Play After completing Bearing Preload, I flattened the Locking Nut tab to prevent the Hub Nut from loosening. Next, the Rear Flares will be attached. The Wheel/Tire Fitment Tool will be installed to check fitment issues. -
Heavy Duty frame rails and connectors
toolman replied to toolman's topic in Gen III & IV Chevy V8Z Tech Board
Richard, Thanks for complement. The cowl area was masked for seam sealer spraying for added protection. Sem Products Sprayable Seam Sealer Using Sem Sealer Spray Gun Central cowl area sprayed right side of cowl Left Rear Wheel Housing interior area sprayed. Seam Sealer was sprayed in between the quarter panel and wheel housing area( the patched area) too. Note-the 3/16" steel rod between the quarter panel and wheel housing can be seen. This view shows seam sealer coverage on the inside of the front of the wheel housing. View of the bottom of the fuel filler area sprayed. Upper area of the fuel filler area. Note-the back side of the fuel filler compartment was also sprayed. The Right wheel housing was sprayed with White Raptor Bedliner after Fusion Seam Sealer was applied over all patch seams. Front view of Right Wheel housing sprayed. Right rear Wheel housing sprayed. Pic of my garage work area. Suspension parts painted with Gloss Black Single Stage Polyurethane Paint on my driveway. R200 differential was also painted. Rear Strut housing painted. Next thing for me to do is replacing bearings and bushings suspension parts and the reassembly begins. -
Heavy Duty frame rails and connectors
toolman replied to toolman's topic in Gen III & IV Chevy V8Z Tech Board
Replicating the Left Rear Wheel Housing to the Right Side. To do this task, will require making a paper template of the newly modified Left Rear Flare opening. A large piece of paper was placed over the L/R flare opening. The major reference lines to be traced are: #1 The Front Edge of the Rear Quarter Panel. #2 is the Wheel Well Opening Edge. The distance between the Top Center of the Wheel Opening to the one of body holes for mounting the Rear Quarter Glass. The measurement will be the height of the flare opening. You may have to darken your Guide Edges if their ink is not visible on the opposite side of the template. Remember you have to use the opposite side the template for the correct orientation. Using the edge guide line and height measurement to align the template on the Right Side. Make sure to securely tape the top edge of the template to the quarter panel as you don't wanted the pattern moving. The Orange Lines in this closup show the areas to must be filled in because overcutting from previous flaring. This provides pattern for the filler panels. Creating the Rear Filler panel. Note- guide lines help to keep filler aligned. The Front Filler Panel being created. Pic of the Inner Wheel housing to Quarter Panel Filler patch Template. To make this Flare Opening a little easier to weld the quarter panel and wheel housingtogether, 3/16" Steel Rod from Home Depot( $13 for 8Ft) was used. The rod would weld between quarter panel and wheel housing filler. It prevents burn through especially with .023 sheet metal. On the Front Side of Quarter Panel (Dog Leg Section), there are some curves in the panel so you must bend the rod to follow the curves. That task is accomplished by holding one end of rod with vise grips and using a torch to soften the 3/16" rod. Then bending the rod until the required shape is obtained. Note-I have used this technique of welding round steel rods around flare opening on many cars. You can use 3/16" to 3/4" steel tubing or even brake lines to outline the tire openings. But solid steel rods don't kink like fuel lines would This method really reinforces the edge and prevents tire damage in case there is contact. For those of you who are tired of getting burnt by hot sparks while welding in confined areas, I would recommend getting this welding gear. The Tight Fitting Welding /Grinder Automatic Darkening Hood Gear. Regular Welding Helmets were never made for tight confined areas. After trying this welding gear at the Sema Show, I ordered one for myself. The Rear Filler Patch mig welded in place. Pic of the Front Wheel Housing patch template. This patch was created using Left and Right Cut Tinsnips. They make cutting curves easy. Front patch after hammering and metal shaping. The area to be filled in. Patch test fitted. Top Wheel Housing Filler patch Rear Wheel Housing Patch Rear Housing Filler patch The Next Thing to do is spray Raptor Bedliner over the inner wheel housing for extra protection. Then Top Coat it with Single Stage Polyurethane paint. -
Heavy Duty frame rails and connectors
toolman replied to toolman's topic in Gen III & IV Chevy V8Z Tech Board
Thank you Nelsonian, Here are additional pics of flaring modifications. After sealing the inner top section of the wheel housing, area was painted with polyurethane paint. Bottom view of wheel well housing after painting. Overall view of rear flaring modifications -
Heavy Duty frame rails and connectors
toolman replied to toolman's topic in Gen III & IV Chevy V8Z Tech Board
Left Front Fender modifications for Greddy Flares. After placing Rocket Bunny flare against the fender then mark the area to be removed with a black marker pen. A Electric shears was used to cut the major removal cuts. Always cut carefully to prevent "over cutting too much". A Hand Nibbler was used in the Finishing Cuts. The Finished Product Rear Wheel Housing Modifications for the Rear Flares- Like the Front flare. the Rear Rocket Bunny Flares are mocked against the existing quarter panel. The Outer edge of the flare is marked with a Black Marker Pen. In my case, I had already removed the original wheel opening edge when I constructed metal flares previously, there was a little less of the quarter panel to remove. Bottom view of the wheel well(looking upward from the ground) As the photos show the gap between the quarter panel and wheel housing was only about 3/4". So I could have just squeeze both panels together and mig welded them together. But I decided to cut an additional 3" higher to give more tire clearance and allow more body drop. Better to do it now instead of later. Side view of additional cutout. But now, the gap between quarter panel and wheel housing increased by about 2 1/2". So fillers had to made to fill these gaps. Patch being mocked up. The Sheetmetal Roller was utilized roll the metal to match the wheel housing. making gap fillers Overall view of the gap fillers An Air Punch/Flanger is used to flange the edges of the fillers to make the filler surface smooth and stronger. Cleco pins and vise grips hold the gap filler plates in place for welding. The front of the Left wheel well housing needed a patch so a paper template was created. Note- the bottom of this patch had to be "rolled over" by making a slit on the bottom then hammer welded the slit closed. The patch started as a flat piece of 20 gauge sheet metal that heated with a torch to soften it. Then was hammered with a Shaping Hammer on a Leather Shot Bag to shape the patch. Additional pounding with a Ball Peen Hammmer. The Patch fitted into place then tack welded in. The inside portion of the wheel well patch was covered with Fusor Seam Sealer. Inside of the wheel housing, EverCoat Epoxy Seam Sealer was applied over all welds and all seams. Polyurethane paint will be spray painted over all of the repaired areas. The inside wheel well areas will also be covered with Urethane BedLiner for additional protection. -
Heavy Duty frame rails and connectors
toolman replied to toolman's topic in Gen III & IV Chevy V8Z Tech Board
Just returned from vacation in Tokyo. While travelling the rural area, I manage a get a picture{not a good one though} of a Japanese Snap On Tool Truck. I think it is only about 12' long box van. Tiny in US standards. Snap On Tools in Japan sell for double of US prices too. However, when I returned home. there was a Big Surprise for me. The Greddy S30 Rocket Bunny Full Body kit was waiting for me. The shipping box was about 18" x 24" x 8 foot long thick card board. It was packed very well also. These kits are only manufactured when you order it. It took 9 months before I received it. But as the pictures show the quality and workmanship was top notch. The Rocket Bunny Kit consists of one- Front Lower Panel, one Front Bumper, two Front Fenders, two-Rear Fender Flares, one Rear Spoiler and bag of Miscellaneous Mounting bolts/ Fender Gap Inserts. I am including detail pic of the individual fiberglass parts so their quality workmanship can be seen. Front view of parts Rear View of Parts Inside of Front Lower Panel( note-the smooth figerglass layout and finishing sanding of the edges.} Backside of Front Fender Inside of Rear Flares Outside view of Front Lower Panel Note-very detailed with Turn Signal mounting holes. Exterior view- smooth and detailed Inside view 0f Front Bumper Note- Front Bumper Mounting insert Top View-Front Bumper Rear View-Rear Spoiler Front view-Rear Spoiler The real test of a good body kit is its fitment. Those cheap Chinese kits usually require a lot of manhours to make them to look decent. Front bumper and lower front panel Left front Flare Right Front flare Left rear flare(note separate door flare Side view of Rocket Bunny Body kit Front view of Rocket Bunny Kit The Front Flares only require trimming the fender to make it work. The rear flares will require more manhours to fill the gap between the inner and outer quarter panels and the outer flare. -
Heavy Duty frame rails and connectors
toolman replied to toolman's topic in Gen III & IV Chevy V8Z Tech Board
The original door glass molding was in terribly shape. First thing to do was removing the old weather stripping. The old weather stripping is attached using staples. The best way to remove the molding is to twist the weather stripping with pliers to continue to "roll up" the weather stripping. If the stainless has scratches or small dents, repair them first. Then, sand with 400 grit sand paper then slowly progress to 1000 grit. Then, use a cloth buffing wheel prepared with Stainless Steel Polishing Rouge to get it to look like new. I tried using pop rivets to hold the weather stripping on the molding but the rivet head protruded too far inward. Instead, 3M spray adhesive was applied to under the weather tripping and on to the molding surface. After waiting 30 minute for adhesive to dry, the weather stripping was installed on the molding. Cross section view of the weather stripping glued on the molding. polished molding and new weather stripping. Molding installed on door Used Chrysler Christmas Tree clips(from Ebay} to hold lower fender flap. -
Heavy Duty frame rails and connectors
toolman replied to toolman's topic in Gen III & IV Chevy V8Z Tech Board
A problem occurred with the weather stripping that was glued to the rear inner fender deflectors. The adhesive was strong enough to hold the weather stripping on. The solution was to use "T" type weather stripping clips( from Chysler) to do the job. Got them from Ebay. 3/16" holes were drilled into the deflector plate. A small scissors was used to create a "Diamond" shaped hole in the weather stripping above the corresponding hole. Twist the "T" clips into the hole In the weather stripping. Push the "T" clip completely into the mounting hole. Pic of the "T" clip fully installed. The Lower fender flap was installed using two "Christmas Tree" type retainers(from Ebay). The retainers replace screws which tend to fall out. -
PapaSmurf, Try going to CR Laurence website. They are one of the largest glass and glazing product supplier in the USA. Go to their Automotive Section then to Search-type in Sun Roofs. They have all the parts(even the replacement glass). I did not see exact size that you were looking for (33 1/2" X 14") But they had 35" X 15" gaskets so you would have cut 1 1/2" off. That is, if the cross section of the gasket was similar. If it is similar, cut the gasket a little larger( 1/4") so if it shrinks, it would not leak. Also, put the gap of the gasket in the rear of the sunroof to help eliminate wind forcing water in as you drive at high speed. I hope this information helps. Toolman
-
Heavy Duty frame rails and connectors
toolman replied to toolman's topic in Gen III & IV Chevy V8Z Tech Board
Finishing under the front fenders Decided to make the upper front fender splash deflectors. Bought garage door bottom edge weather stripping from Home Depot for $12. Used a knife to remove both vertical edges to end up with a flat rubber strip. I bent strips of 2" wide sheet metal to create a "S" shaped clip to hold the deflector on the fender support. As I was making the clips, I could adjust the holding tension of the clips by adjusting their gaps. Fender upper side deflector installed. Closeup view of clips Note- The clips edges are bent up slightly to prevent sharp edge from cutting the rubber deflector. I ordered a set of Dimple Dies consisting of sizes from 1/2", 5/8", 3/4" and 1". Using these dies make flat sheet metal a lot stronger and looks "real cool" too. The 240z uses this type of metal forming on its inside rocker panels ,strut supports,etc. First, thing to do, is drill a pilot hole in the sheet metal. In this case, the 1/2" Dimple die requires 5/16" pilot hole. Next, assemble the Cutter blade and bottom die with the 10MM head bolt. As you tighten the bolt, the Cutter blade also turns and cuts a hole into the sheet metal. Continue to tighten the bolt until the Cutter cuts through the sheet metal. Once, the 1/2" hole is made, you reassemble the forming die with the bottom die. Tighten down the Forming Die until it is flush with the surface of the sheet metal. Disassemble the tool and inspect the Dimple Form. If it's not formed enough, reassemble the die and tighten it down more. Bottom View Side View of the finished !/2" Dimple. I will probably use the Dimple Dies to create some support brackets in the interior and maybe construct a Triangular Engine Compartment Support with them. -
Heavy Duty frame rails and connectors
toolman replied to toolman's topic in Gen III & IV Chevy V8Z Tech Board
Ebay has a lot of portable China Spray booths that run from $1000 to $2000. Most are a little more than inflatable bounce things. The one at the SEMA is manufactured in Texas by Mobile Environmental Solutions. Single booth 23' x15' was $9995.00 and twin booth 23' x 48' was $19995. They seem to be made of material similar to those auto paint shop curtains that divide up shop areas. According to them, the booth is made of materials that pass NFPA (National Fire Protection Association)701 test methods 1 &2. TV's Garage Squad show is shown using their booths. But I would check with your local fire department first before purchasing one. -
Heavy Duty frame rails and connectors
toolman replied to toolman's topic in Gen III & IV Chevy V8Z Tech Board
That was the price that they quoted me. The major problems with this portable spray booth is it is made out plastic and it does not have a fire suppression system. Most local fire departments would not allow such spray booths to be used. If some one was caught inside in one that caught fire, they would be trapped under a collapsing structure. -
Heavy Duty frame rails and connectors
toolman replied to toolman's topic in Gen III & IV Chevy V8Z Tech Board
Just returned from the Sema Show 2019. The Sema Show gets bigger and bigger every year. This 240z took part in the Optima Ultimate Street Car event. It had a Webber carbs and slightly modified suspension. Early Datsun Roadster with a Honda twin cam motor conversion with fender flares. Four passenger dune buggy A 240Z racer with carbon fiber body parts. Powered with a Chevy LS motor. With this kit, you can pull dents without grinding your paint -Glue Dent Repair Kit for $600. Water jet Cutting Machine-Note the cutout samples on the table. The very popular John Force 300mph Funny Car I had Lunch at one of the many Sema Food Trucks. the long line of customers Spicy Ribeye steak with rice for $12. Ymmmm! 1970 replica of Pete Brock's Datsun 510 The spec sheet of the 510. Harbor Freight introduced their new tool line. Their lifetime ICON tool box costs $10,000 but remember Harbor Freight usually has 20% discount coupons at their stores. The box was very well made and about half the price of a Snap On similar one. Also had ratchets,sockets, wrenches,etc. Their line of tool carts. Their MIG and TIG welders were low priced too. Their Full Function Scanner with Blue Tooth was only $999 perfect of the Do It Yourselfer. Floor jacks and jack stands Beautiful Old Datsun Roaster With a late model Nissan Twin Cam motor. Mobile Spray Paint Booth Had fresh air intake and exhaust filter system for $20,000 for average size booth, A neat Rat Rod '59 Chevy El Camino with supercharged motor Super Low!! Chopped and Shortened This booth has all sorts of Illuminated Car Signs. Toyota Nascar race car 2020 Toyota Supra 370Z with carbon fiber parts NISSAN NISMO Skyline All Wheel Drive Front view Full Functional Race Car Simulator at Supra booth Beautiful Honda Z50 Mini Bike Another Honda 50cc Monkey bike A Wild 65 Ford Van with supercharged motor. Supercharged motor with long headers Old Honda S80 with flares JooTool is a specialized small polisher for restoring small car parts. Also, sharpens knives. 3M provides various grinding, sanding and polishing discs for this machine. Outside the halls, more booths and cars This van had Four Wheel Track drive so it could go almost everywhere. Robot sanding machine made by PRO SPOT. Even had vacuum system to catch the bondo dust. Plastic welding machine with Nitrogen gas to create strong plastic welds plastic welding made by urethane Supply. more cars & people Ford Mustang one wild ride with tire burning etc. More trucks Monster trucks,too Its motor and suspension huge too. Hurst Hemi under Glass Barracuda was there too. Skelton car its supercharged motor High and Might truck 4 x 4 James Dean Replica Porsche covertible Hoogan Pit area and Burn Yard Hoogan put on a Wild Tire Burnout Show but I missed it as I thought it was over. When I was on the top of the Monorail Platform, the Burn Out Show happened. But if you want to see the Show go to: https://www.youtube.com/watch?v=NAzAI8pxyLs Hoogan guys did a preshow walk through and did crazy Burnouts and Drifting there!!!! Now, Back to working on my 240Z -
Heavy Duty frame rails and connectors
toolman replied to toolman's topic in Gen III & IV Chevy V8Z Tech Board
Back home to get working on the Z. From Epoxy Primer to Body Filler. Body Filler used to cover minor imperfections. Sanding Body Filler Then paining Polyurethane Primer Sealer on top of that bodywork. Not to forget the inside of the front fenders, the sealing of them was next thing to do. The wheel well deflector plate stripped and painted. I decided to use rubber weather stripping. I found 3M "D" shaped weather stripping on Ebay for $13 for 8 feet. The hollow inside made very soft and a good weather stripping for the wheel well. front view back view Previously I had planned to use Dynamat or similar foil type of insulation for the floor and roof. However, I decided to use Lizard Skin Ceramic Insulation paint. It can lower the interior temperature 20 to 30 degrees. One gallon costs $100 on Amazon. They also sell sound insulation paint(costs $100 gal) but it must be applied first(before heat insulation). Had planned to spray it on with a Schulz under coating gun but the coating was too thick for the gun. So I used rollers and a brush to apply it. A cordless drill was utilized to stir the paint. Use low speed and in Reverse so the particles are not damaged while mixing. Application was done in two .020 coats allowing the first coat to dry to the touch. Curing will take possible a week to completely cure depending on weather conditions. All holes must be masked off to prevent over spray. Areas to be painted are scuff sanded and all threaded holes are plugged. After painting Ceramic Coating was not difficult to apply. Cleanup should be done quickly as the insulation dries relatively fast. Pic of roof coated Pic of seat area Passenger side compartment After the Ceramic Insulation is cured, I will probably top coat it with Polyurethane White Single Stage Paint for added protection. -
Heavy Duty frame rails and connectors
toolman replied to toolman's topic in Gen III & IV Chevy V8Z Tech Board
I just got back from Tokyo. I managed to go Japan's Largest Automotive Store in Japan Autobacs Shinome located near Tokyo Bay. The garage is on the bottom of this three level store. The main store is on the Second floor and has a coffee shop there. the third floor is the high performance stuff. Snap On tools on display in glass cases. Snap On Tools tools sell for twice the US price. That Snap On tiny tool box toy sells for $140!! Snap Tools on display. On the third floor, the high performance parts and accessories were on display. They had the latest GPS., stereo ,DVD, and LED lights. And, of coarse, the garage downstairs could install whatever you purchase. Helmets, gloves and gear. the Black one cost about $5600 USD Steering wheels (Momo one was $300 USD. Racing suspension parts-NHW strut was $1350 USD There was a rear driving simulator that anyone could try for a price. It had loud speakers 3 TV screens and air shocks to give the real.feeling of a race car. I think the price was $50 for 30 minutes. Unfortunately, I found about the simulator too later as I had to get back to Shinjuku before the afternoon rush on the trains. Passengers are really packed like sardines during rush hour!!!!! The store is located near Odiba theme park by Tokyo Bay near Tokyo Disneyland. Front Entrance of the store The Garage Area is Super Clean and well lite. Mechanics even wear white gloves when working. Only High End Wheels no China Stuff here. !/6 scale Skyline motor very detailed. Bicycle and accessories Aisles of assorted stuff There is a large area with only automotive books and magazines next to their coffee shop. Everthing automotive under the Sun is here. Leather jackets Kids $500 electric cars. Kids seats more seats and seat covers $1000 Mavics RC Drones This Skyline motor sells for $300 but is well detailed. wiper blades Pet accessories Snap On floor jacks-the silver one sells for$200(about $100 in US) Can't wait to start back to working on my Z. SEMA SHOW 2019 is less than a month away. Viva Las Vegas!! -
Heavy Duty frame rails and connectors
toolman replied to toolman's topic in Gen III & IV Chevy V8Z Tech Board
The door hinges for both Left and Right sides were top coated with Polyurethane paint. Shop Tip- Removing and Installing a 240Z hood by yourself Place a Plywood on top of the Left and Right fenders. Put hood in the closed position. Put card board or padded mat under plywood to prevent scratching the paint. Raise hood to open position. Loosen all four hood bolts but do not remove. Remove both hood front bolts. Now tilt the rear of the hood downward till the hood contacts the plywood. Then remove the rear hood bolts as the hinge and plywood will support the weight of the hood. The hood can be lifted off from either side of the car. Hood installation will be the reverse procedure. The next thing to do to spraying Raptor Liner in the fender and wheel wells. This Raptor liner was the 2 bottle kit with Liner, hardener and color toner.. This kit costs about $100 including freight on Ebay. Masking the hood to prevent overspray going all over the place. The interior sides of the hood and fenders were sanded with 150 grit sand paper then wipe down with paint prep solution. view of Left side Wheel Well Housing afterspraying. Right side Wheel Well Housing after spraying Liner Right side fender interior view Inside Right Door view Closeup view of the Raptor Liner on Wheel Hosing Inside Right Fender Note- Liner even covers patch area. Left side Wheel Well Housing The Raptor Liner can be applied by hand roller or sprayed. A Schutz gun is most commonly used to apply the liner. HLVP spray gun with 2.0 nozzle can be used if liner is reduced by 20%. This method would provide a smoother finish( not as rough}. After one hour, the liner is dry to touch. It, however. takes a full week to completely cure. I used only one bottle of Raptor Liner so far. The remaining bottle will be used for the rear wheel housing after I finish flare modifications. -
Heavy Duty frame rails and connectors
toolman replied to toolman's topic in Gen III & IV Chevy V8Z Tech Board
PROJECT TIP: I am posting this tip as it may be very helpful to a lot of people. RESCUE BIT is a high speed cutting bit that will cut through broken taps, extractors just about anything. Check the video out at https://www.youtube.com/watch?v=FkIH7DhQJzA In my case, I was tapping out the bolt holes of my struts. Of course, while tapping the last bolt hole, the 6mm x 1.0 tap broke. Pic of the Broken tap This is a picture of a 1/8" RESCUE BIT with cutting edge on both sides. The 1/8" version must be used with a 1/8" adaptor to use it in a 1/4" die grinder. Pic of 1/8 to 1/4" adaptor. Rescue Bits also use to have 1/4" burrs (single and double cut version) too. Now the Rescue Bits can be found on Amazon and Ebay but only here and there. I don 't think the company still exists. I do keep one around for emergencies like this one. After drilling a hole in the center of the tap. I use a small sharp punch to collapse the walls of the tap inward. Here is one the larger pieces of the tap that was removed from the hole. After removing all remains of the tap, I carefully tapped the hole with a new 6 x 1.0mm tap. Success-bolt was threaded in!! It is important to carefully follow the instructions that come with the Rescue Bit. Also. the die grinder must be capable of 25,000 RPM. High speed and the bit design is what allows the Rescue Bit to do what other bits can not do. I hope some of you find this tip helpful. Rescue Bits costs about $60 online.