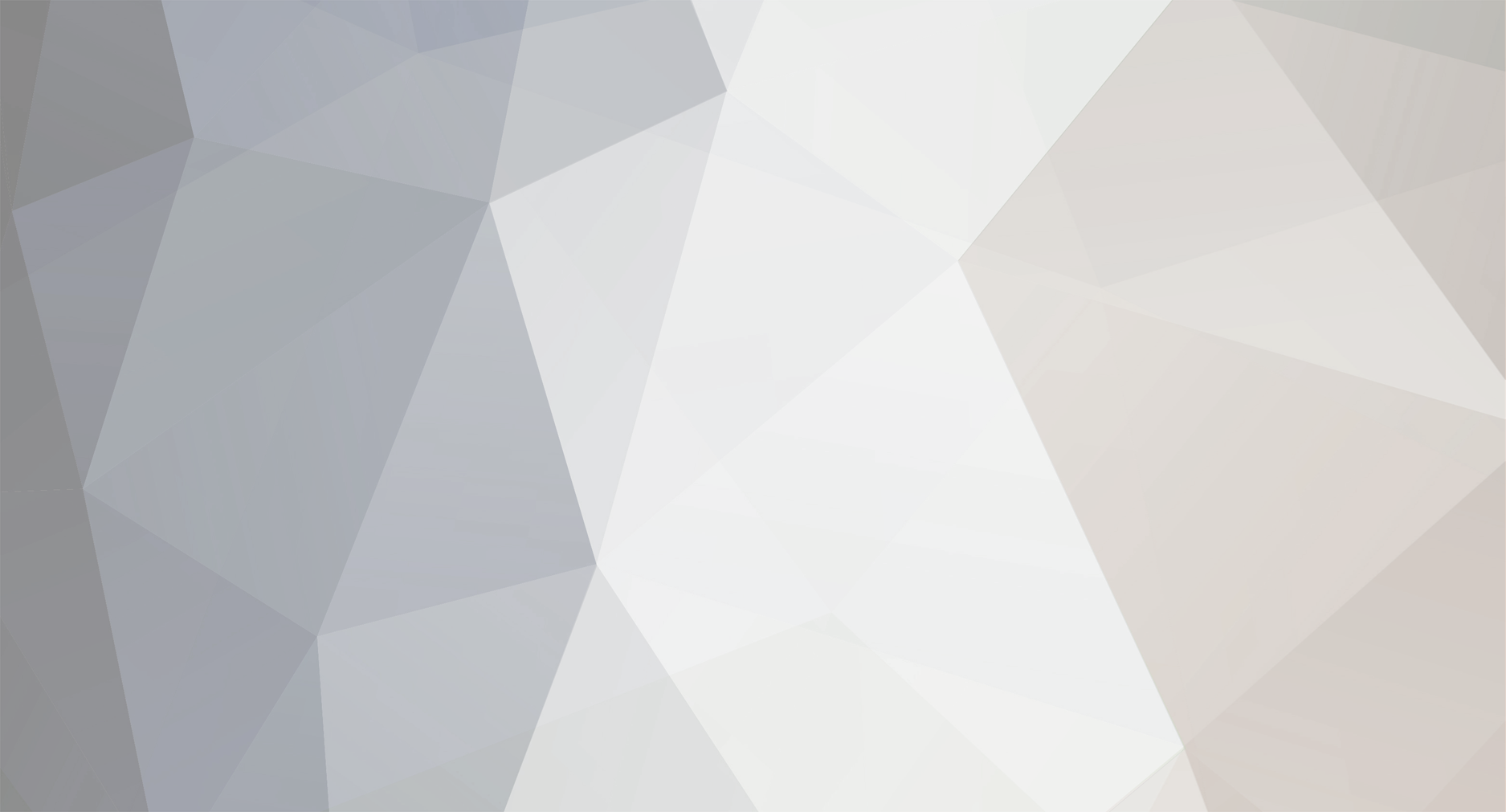
disepyon
Members-
Posts
1199 -
Joined
-
Last visited
-
Days Won
1
Content Type
Profiles
Forums
Blogs
Events
Gallery
Downloads
Store
Everything posted by disepyon
-
First I use my die grinder with a flap disk on it to knock most of the welds down, the thicker stuff for the most part, then use my small air powered belt sander to knock the the welds even more to try and get it close to flush with surrounding metal but not entirely, finally use the air powered angle grinder with a sand pad on it to blend in the weld with the surrounding metal. For the sanding pads/belts I used 80-120 grit and while I sand only use very light pressure, keep it constantly moving and attack from all angles. Thinking I may need a higher grit pad, 120 grit is still a but ruff. I prefer tig welds for stuff like this because it is more malleable than mig, allows me to hammer and shape the weld with out it cracking and there isnt so much weld to remove, I control how much filler metal to put in, not only that if you tig it there really isnt a need to leave a gap between the work pieces to allow for penetration, for me anyways. I am still working on heat control, I still get warping but its not very bad. I just need to actually spend time practicing all this stuff, been pretty lazy about it, which is why I havent started on the rear quarter panels yet because that is something that needs to be done right since everyone will see that.
-
Replaced the rusted part of the fender well and got it tig welded and the welds smooth out. Section that got replaced. This is what the frame with the support plate looks like on the car before welding on the new sectioned fender well. Replaced section tack welded and tried my best to get it flush as possible. All tig welded. I welded most of it from the outside, not on the engine bay side. welds penetrated pretty good. Smooth out, Not sure how people get the welds smoothed out perfectly flush without noticing anything was welded in place. Guess just takes practice. I think part of my problem is that I need to start moving the weld puddle in a circular motion or just need to spread out the weld, that way it would give me a larger surface area to smooth out better and blend in, maybe... what it looks like with the frame back on. I also removed the radiator support, going to make one myself.
-
I think a major part of it is due to the fact that sheet metal work is still new to me. Learning is frustrating for me but it seems like its paying off. I figure while im at it, might as well give it all I have and try to do the repairs somewhat correctly while adding a few things. So I tried to order a baileigh 4' magnetic brake from a couple of stores but those units are on back order until mid May. I cancelled my order cause didnt want that much money in limbo incase something happens and i would need that money before then. So when those brakes are back instock ill submit another order. Sucks cause I am about to start on making the floor rail and while the bead roller I have bends metal, its a pain when working with 16g especially when I just want to make straight bends. Guess ill just make do.
-
To be perfectly honest, Ive about had it with repairing rust. Probably only completed about one thrid to a half just on the driver side, havent even started on the passenger side. Just how I feel right now in my current mental state with this project. There have be many days already I flat out didnt want to work on this car just because I dont like rust repair, hehe. Just be glad your car does not have as much rust if any from what I can see in your thread. Nah mine doesnt compare to your project and others on this forum, so far everything I have done is boring/restoring work, hehe.
-
Sirpents 260Z / C32 AMG Powered RS30 - Australia
disepyon replied to Sirpent's topic in S30 Series - 240z, 260z, 280z
Well then my hats off to you cutting with the angle grinder and producing those perfect looking cuts. So do you have an estimate of when you think this will get finished? People are always asking me and I really dont have an answer for them, just one of those projects ill work on when I get time and feel like it. -
Sirpents 260Z / C32 AMG Powered RS30 - Australia
disepyon replied to Sirpent's topic in S30 Series - 240z, 260z, 280z
Starting to give me ideas, hehe, looking good. Was just about to ask how you get your plates/brackets so perfectly cut, now I know. I just use my plasma cutter and a straight edge, would like to jig something up though for a machine like cut. -
More progress, not much but something. Made a new bracket for the tension arm since the original bracket wouldnt fit my newly made frame rail. I started the downward bend to early and should had started it a little be later. I opted to make a whole new bracket in lieu of hacking up the stock one to make it work. Cut out a good chunk of rust on the fender well area. Made the support/stiffening plate for the frame rail. Not welded on yet, just snugly fitted for pics. Also made the mounting for the sway bar, kind of went over kill. I decided to have the bolt go through the entire frame. only thing left is wondering what I want to do for the tow hook mount...
-
Thanks, The radiator is supposed to be for a 1970 Pontiac Firebird-Trans. Bought it back in 2014 for $365 shipped from PWR with the manufacturing date of 2011. Since it didnt come with any brackets welded on, it will allow me to create my own to fit the Z, which is what I wanted. I think PWR does that on purpose since they know everyone whom buys these will fit slightly different for their setups. If i remember, most of the rads they sell dont come with brackets. I bought this exact radiator due to the dimensions so it would fit in between the frame rails and not hang down so low. Now that I am doing all this fab work on the body/frame, kind of wish I had gotten a wider radiator, oh well though, still plenty of rad for my setup.
-
Cool, but please stop using the word JDM... What kind of V8 is it? I like that you kept the original gauges, most people like me take the easy route by replacing them. Looks good.
-
Worked on the frame a little more today. Had to notch the front part of it so the radiator can fit. I notched it out just a little bit more than stock to allow more clearance. Also filled it that triangular hole on the bottom side.
-
Small update, not much accomplished. Started on the driver side Front frame rail today. This was made out of CRS 16g sheet metal. Still needs some work but thats what it will pretty much look like. Will be adding in a stiffening/support plate that will run along the whole length of the frame rail. partially kind of put on the car to see what it will look like, seems like it will fit good. Friend called me over to his place to discuss getting some stuff fabricated on a couple of his cars. Every time I go to his house, he has a new toy to add to his collection. Its like attending a car show at his house. He has more cars at his airplane hanger. Another friend was there as well and wants to get some stuff fabricated for his BMW 135i. Anyone know what bolts on top of the driver side frame rail at the front? There are a couple of holes there with nuts welded on the back side. I cant remember what goes there. I know the tow hook bolts to the bottom, but unsure what goes on top.
-
S30/LS/turbo/Powerglide/Tex101/9"SRA build diary
disepyon replied to RebekahsZ's topic in S30 Series - 240z, 260z, 280z
200-220mph is fast, id feel much safer being in a tube chassis Z. Then again a beefed up stock z chassis I would think be good, though I know nothing about the limits of the stock Z chassis. Guess just comes down to budget, if your willing to open your wallet depending on cost to fix the front or tube it. Either way this is going to be a crazy cool build. -
Yeah I would think some one would had noticed besides you and me. I may contact them about it. My work is going to keep me busy for awhile which means ill be spending less time on this project. Hopefully I will have the energy to nibble at this a little each day.
-
~73 Turbo L28 to N/A RB25 240z Project~
disepyon replied to ~KnuckleDuster~'s topic in S30 Series - 240z, 260z, 280z
Your interior is so freaking clean!! That new seat is classy. -
Thanks, sheet metal work is new to me, but welding is something I have known for a while, believe me I still have a lot to learn. Drive side engine bay frame and floor pan frame off. Had to take off the bottom portion of the radiator support because the front of the frame curves outward. Just realized how much I hate removing spot welds. A picture of the passenger side frame looking inside. Looks to be in worse shape than the driver side. I am actually looking forward to making this, looks pretty simple to make...hopefully
-
Made the roller frame today. Just kind of made it as I worked on it. I may or may not add in supports directly to the engine bay strut towers. It is pretty stout the way it is. Didnt want anything inside the engine bay/around the frame since that will be the area of focus. Just wish I did this before working on the car, so much room when it sets high like that.
-
Looking forward in seeing how your diff mount turns out, still need to do mine.
-
Thanks, I'm sure there are a lot of things not correct with mine if you were to ask a professional. This is all new to me which is why my progress is so slow for the rust repair. POR15 and rust preventive coating/weldable primer put on. Hate the spray can when spraying the primer on, should had bought by the gallon and brush it on, would be a lot cleaner. Finally all welded up, feels super stiff. I wanted to see how bad the front frame was in the area that was compromised by rust. I cut out the rusted sheet metal that is part of the drive side engine bay. You can kind of see it in this picture.
-
Yeah pictures definitely helped me along the way from browsing around the interweb, although I have a couple of restore datsun books I never used nor looked at. Now that I think about it, I may just go grab them and browse through them, might provide some helpful stuff. More pictures of miscellaneous repairs. Should be it for the rocker panel area. I left extra material for the outer wheel well section on purpose just in case I need to weld more material or reshape it in the future for when its time to work on the rear quarter panel. Not too worried nor trying to be a perfectionist in smoothing out the welds. wont be seeing this part of the car and will be coated in a black color. Also I dont have a tool with a precise and fine enough edge to grind in some areas either. So the Tabco outer rocker panel had a crack in it, guess is it formed due to that area being too thin and stressed out since these are pressed when made I am also guessing. Just glad I caught that and fixed it. Best I could do in getting the welds to smooth out. I may go back over it with my tig torch to even out the weld but I really dont care, thats what body filler is for, to fine tune it. Picture of the simple 1/8" thick plate with a nut welded for the seat belt. Sprayed some Bloxide aluminized weldable primer before I weld it tomorrow.
-
Some pictures of miscellaneous repairs. Bunch of sheet metal (16g, 18g, 20g, all CRS) and square tubing to brace the front of the car for when its time to work on the frame.
-
Small update, not much accomplished. cut some more rust out on the front side of the floor. As I thought, the front frame isnt any good. Looks like ill have to make new frame rails. Thought about buying them but after seeing how poorly fitted the Bad Dog floor rails fit, I am assuming the same for the front engine bay frame rails by whoever its made by. Got the support plates welded in. So I made these out of 18g cold rolled steel when the factory thickness is 22g. Oh well, as long as my welds penetrated, which they did. Inner and Outer rocker panels fitted in place and trimmed. Still need to add the seat belt hole and nut on the inner rocker panel and get these suckers coated before welding. But before i do that, I need to do small repairs in various areas, however I need 22g metal. Will buy some tomorrow. Tomorrow I will be buying some metal to support the front of the car for working on the frame, sheet metal to make the frame rail, doing small repairs and floor pans. Decided to make my own floor pans.
-
Made the rear section of the support/tie in plate for the rocker panel. Worked on making a replacement sheet metal section for the seat belt mechanism. Need to work on it a little more, but good for the most part. I needed to know the shape of the rocker panel where the replacement section meets up to it, so I temporarily clamped the inner rocker panel on. It isnt trimmed for a final fitment yet.
-
Looking great! What kind of sheet metal brake and english wheel do you have. I want to buy a brake, but so far havent really had a need for it yet since I can do a lot of bending using my bead roller. Though it cant do anything thicker than 16g and even 16g would be a b**ch to bend. English wheel is a tool i really want, been kind of shopping around, but just havent pulled the trigger on one yet.
-
Thanks for the kind words RebekahsZ. Got some things accomplished today such as getting the transmission tunnel mounts spot welded on to the car and made the support/tie in plate for the front of the inner rocker panel. Pictures of the tunnel mounts. Originally I started making the front support plate for the inner rocker panel like the stock one, but that didnt go so well, not sure why. Anyways I decided to just make it my way and it worked out. Picture of the stock front support plate. My version, could add a few beads to help strengthen it, or maybe even go about it differently, but i think it should be alright. The rear support plate for the rocker panel I have no idea what it looked like, guess I will just make it my way. Will do this tomorrow. Edit: For got to mention that when I spot weld, I use my Mig machine. Below are a couple of pictures of some testing to see how strong my welds were. As you can see the weld itself ripped/tore the 18g sheet metal, which is a good thing.
-
Here are pics of the driver side inner rocker panel finally made. Spent all day making this. Most likely will be a little trimming around the edges for when i install it. I left a bit of extra metal on the edges just in case. Also need to figure out the seat belt mounting, not sure if I want to copy the stock design or not. Another panel to add to my collection, this time one made by me.