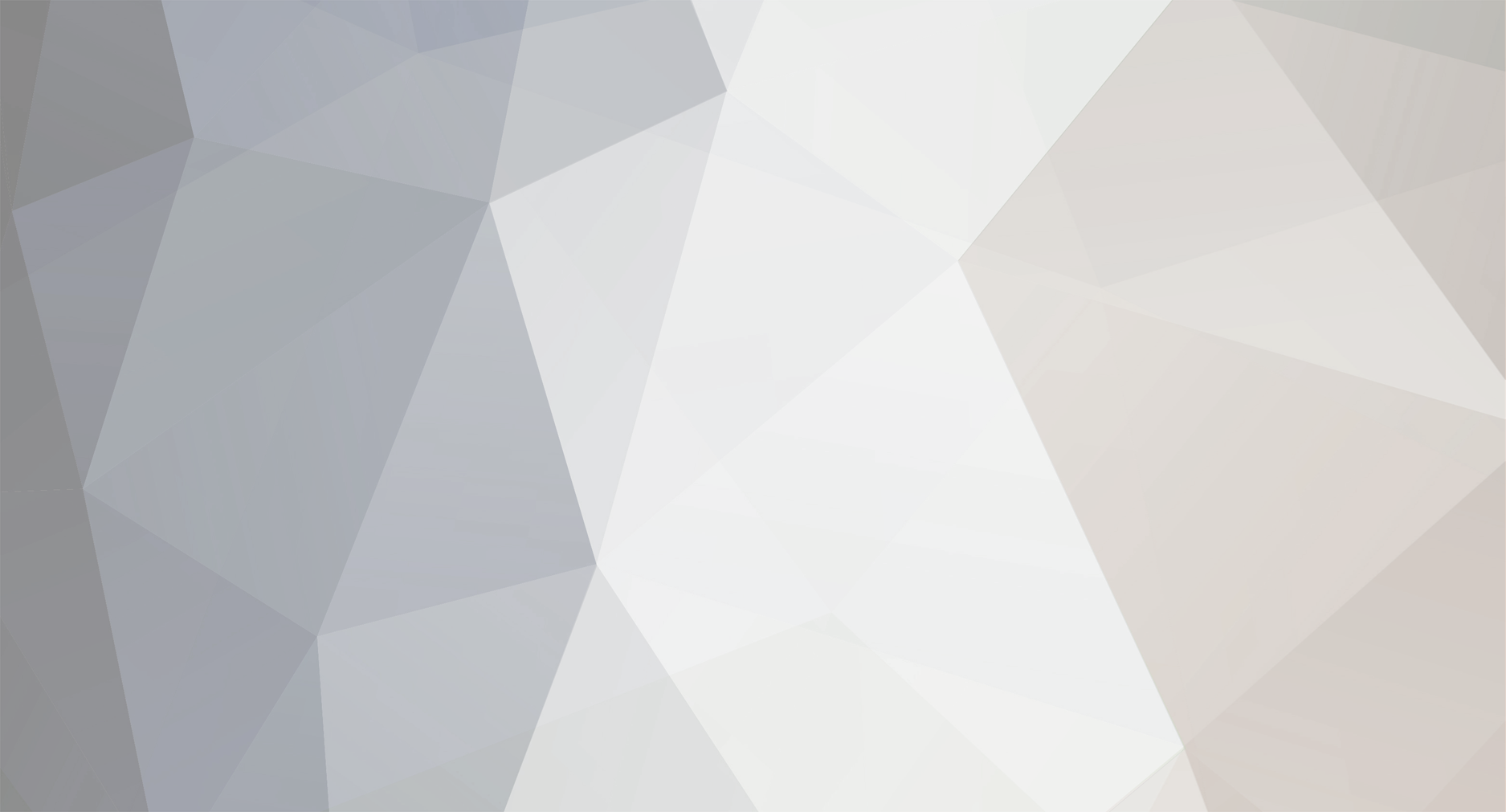
ktm
Donating Members-
Posts
1724 -
Joined
-
Last visited
-
Days Won
3
Content Type
Profiles
Forums
Blogs
Events
Gallery
Downloads
Store
Everything posted by ktm
-
Where are people mounting ECUs in S30s (not 280Zs)
ktm replied to z-ya's topic in S30 Series - 240z, 260z, 280z
There is gobs of room behind the glove box if you remove the blower and heater core. I mounted mineup high for the same reason you cited, the prospect of moisture draining to the box was not appealing. -
Where are people mounting ECUs in S30s (not 280Zs)
ktm replied to z-ya's topic in S30 Series - 240z, 260z, 280z
Pete, this is exactly where I mounted my Wolf V500 unit. I installed a 280z glove box liner (plastic) in my 240z and cut out a port in the back for the cables. I have a serial extension cable connected at all times to the Wolf output and I keep it curled up in the box on top of the ECU. I still retain enough space in the box for small items and my registration and proof of insurance. -
Wilwood versus 4x4 vented .. pro's vs con's
ktm replied to proxlamus©'s topic in Brakes, Wheels, Suspension and Chassis
I am running 16x8 +10 Rota Grids with the S12W setup. I used a +10 mm spacer to clear the brakes. Of course that required longer studs, but they are cheap and it only takes an hour to install them on both sides. Wheels may be hub-centric, but the front hub of a 240z is setup for lug-centric wheels. Hub-centricity is moot. Whenever I tighten up my wheels, I have to make sure they are off the ground and tighten in steps to make sure the wheel is centered. -
Does anyone know if there is a difference between the N/A and turbo speed sensors for a z32 300zx? I know there is a gearing difference and hence different pinion gears, but I am talking about the sensor itself. The N/A sensor sells for $110 and the turbo sensor for $155. I've been searching for a while and can't seem to find any differences in the sensor itself. Thanks.
-
AC Delco/GM Alternator Swap Part 2 - CS144 Installation
ktm replied to ktm's topic in Ignition and Electrical
The spacer idea is a good one. I wound up "shimming" it with washers and had to use a longer bolt as well. I really like that extruded turnbuckle. I did not see it at the Home Depot near me. I'll have to check again. -
AC Delco/GM Alternator Swap Part 2 - CS144 Installation
ktm replied to ktm's topic in Ignition and Electrical
I posted about that modification too! As I wrote in this thread, by going to the turn buckle design you elminate the need to trim the alternator tabs since you are mounting the adjustment arm in the front. -
Edit: Found my answer. M16x1.5 is the diameter and pitch of the water temp sensor on the thermostat housing.
-
Was this anyone here - 240z, turbo'd, white, ZG flares, OREGON plates
ktm replied to ktm's topic in Non Tech Board
I bet you were regretting that decision! God that was some awful traffic. I head down to SD regularly and that was the worst I've seen in a while. I was at the show for 2 hours but I did not bring my car. I was heading down to SD (El Cajon) afterwards and did not want to drive the Z. -
Was this anyone here - 240z, turbo'd, white, ZG flares, OREGON plates
ktm replied to ktm's topic in Non Tech Board
Yep, right befoe the accident. It was dark out and it looked white to me in the lighting. I was in my Subaru. I passed you on the far right lane. What brought you that far south? -
....sporting the shaven look. You had a passenger and were fixated on the cars in front of you while we were stuck in that horrendous traffic on I-5 north (coming up from Oceanside/San Diego???) near San Onofre. I tried to get you to look over but you were quite focused and your passenger was talking to you. Nice car!
-
Wilwood versus 4x4 vented .. pro's vs con's
ktm replied to proxlamus©'s topic in Brakes, Wheels, Suspension and Chassis
Zmanco, the Porterfield R4S is a street pad as is the KVR. They are fine when cold. I have not had a oh sh** moment with them. -
Correct. Another solution is to simply install a union there and then install the bias valve up by the master cylinder on the rear circuit before the brake bias switch. This was my main concern when installing my setup. I researched for hours about the 240sx/S12W combo and heard people complaining about bias issues when using the same pad compound front and rear. I have Porterfield R4S' in the front and KVRs in the rear. If I open the valve fully, the rears lock up. I need to back off 1.5 to 2 turns (IIRC) in order for the fronts to just lock before the rears.
-
Wilwood versus 4x4 vented .. pro's vs con's
ktm replied to proxlamus©'s topic in Brakes, Wheels, Suspension and Chassis
I have the S12W and 240sx setup and can dial in front-rear balance. I am using Porterfield R4S in the front and KVRs in the rear. I got my setup for considerably less than the Wilwood setup. I bought all my parts from members here save for the front brackets. I did the entire setup for around $450, front and back. -
All of my reading has lead me to the same decision, plate over tube and fin. I read a thread over at a Corvette forum with Z06 owners who track their car that discussed a ~12x5x2 cooler. Setrab's unit that measures this dimension has 19 rows; the unit MSA sells looks like s Setrab and has the exact same dimension (13x3x2) as their 10 row unit. I like the fan setup as well and I've been looking at Earl's, Derale's, B&M's and Setrabs units.
-
I replaced the aforementioned head gasket in January 2008 and continued to refine my tune. In February 2008 a little old lady zooming through a parking lot in a Lexus helped me to realize that I did not quite like the Kaminari air dam (in other words, crunch!). I always like the Bre spook and picked up a carbon fiber version from Motorsport Auto in March 2008 in preparation of MSA. I also purchased an IMSA 3 piece spoiler and painted it the same color as the center stripe and knock-offs, Duplicolor's Iron. By this time I finally had a good understanding of Wolf's boost solenoid control. I spent the better part of a month trying to figure it out. It is a PWM controlled solenoid that is mapped across RPM. I have it configured so that as my RPMs pass peak torque, it will increase boost to help flatten the curve more. It is also controlled by a methanol pressure sensor discussed below. I also purchased and installed an FJO Racing (www.fjoracing.com) 700 cc/min methanol injector. The injector is pulse-width modulated (PWM) controlled with Wolf. It is fully mappable across RPM and manifold pressure. I am using the Wolf V500 ems to control the high speed injector. I am also using their 200 psi pressure sender has a fail safe and a means of controlling my methanol tune. Wolf uses the pressure sensor as an input. If the pressure is greater than 90 psi (pump operates at 110) then Wolf will allow up to 25 psi of boost, pull fuel and add timing. If the pressure is less than 90 psi, then the boost is limited to 15 psi, fuel is not pulled nor timing added. Wolf also controls the pump which operates at 100% duty cycle. I turn the pump on at 2 psi of manifold pressure to keep from boiling the methanol. I found this out after logging my methanol pressure sender. I have a series of 6 LEDs (I'll discuss them later on with a better picture) that are warning/information lights. My methanol pressure sender is hooked up to one via Wolf. The methanol pressure sensor LED would start flickering for no reason and then go out all together, this was when the pump operated all the time. The LED was configured to turn on when the pressure was at least 90 psi and go off when less than 90 psi. The pump deadheads and would get incredibly hot when the methanol was not spraying. Methanol has a low boiling point and the short of it is that the pump was boiling the methanol. This problem drove me nuts and took me about 6 weeks to figure out. By turning the pump on only when I am at 2 psi of manifold pressure solved that problem. In addition to this, I installed an Innovate LC-1 wideband with a G3 gauge in January 2008 when I replaced the head gasket and an Innovate LMA-3 aux box in March 2008. I can not recommend the LMA-3 enough for those who do a lot of datalogging. Aside from all of that, not too much happened to the car up to MSA, it was just waiting until after the show to throw a tantrum. Below are a few pictures taken at MSA 2008. You can see the methanol container located next to the brake master cylinder. The 700 cc/min injector is located under the IC piping right past the radiator core support by before the BOV, and the pump is located on the inner fender right below the BOV. As you can also see, I converted the throttle linkage to a cable setup that utilized the stock linkage on the intake manifold. I highly recommend using a throttle cable from the pedal forwards as it resolved all of my low speed driveability issues associated with sticky linkage and the pedal-linkage design.
-
I forgot all about my little LED conversion for the dash lights. I completed this work in June-August 2007 when I got tired of working on the car. I won't go into the gorey details as I prepared a write-up as well which can be found here. Here are two pictures of the final product:
-
I am going to install a oil cooler but I can not find out what is the recommended dimensions for the oil cooler itself. Some of the coolers are huge while others look like they won't do much cooling at all. Any recommendations would be great. Thanks.
-
While I was tying up some of the minute details, I picked up a set of spinner center caps and a Kaminari air dam. I bought the air dam from mad kaw and the spinners from AKH Wheels. I also decided to paint the center stripe down the hood and top of car to see how it would look prior to finalizing the body and paint. I also installed a pair of early 1990s Mazda Miata seats I painted the spinners, air dam and center stripe all the same color: Duplicolor Metallic Iron. I really liked how every thing came out. In all honesty, I regret selling the Turbines and spinners as they really gave the car the "period" look I was going for. Hindsight and all you know..... The car was terrorizing the neighborhood for the month of November and December while I was attempting my first tune. Attempting is the key word as I ultimately popped the head gasket in December 2007. Following are some pictures of the finished product as of November 2007.
-
In August 2007 I had Vildini Motorsports fabricate a custom 3-in. exhaust using a Borla XR-1 muffler. I wanted to minimize the number of bends from the down pipe all the way back to the muffler. Alex did a fantastic job and the exhaust was exactly as I was envisioning. I don't have an pictures of the exhaust unfortunately, but it can be seen in this short Youtube clip I posted in September 2007. This clip was taken shortly after my first start-up. I am still ever so grateful to Ron Tyler for helping me trouble-shoot my start-up. Over a period of a week I was on the phone with him almost every day. I'll never forget the day when it finally fired to life while I was talking to Ron on the phone. Sure, it sounded like a motor boat (as Ron described it) as it was only firing on 3 cylinders, but it was alive. I found the problem 2 days later. I was afraid it was a wiring problem, but as it turned out if was simply a sequencing issue in the Wolf software. One I got the sequencing sorted out she was purring like a kitten. I was still 6 weeks away from actually driving the car at this point. While it did run, I needed to finish up some of the last minute details.
-
Now the fun could really begin. I thought I was on the home stretch and would have the car up and running by mid to late July. I was wrong. I spent the next 2 months installing Wolf as well as all of the ancillary components. Prior to the engine going into the car I ran -6 braided stainless steel fuel lines from the fuel pump to the engine bay. I still had the intercooler and intercooler piping to address. I endured countless hours staring at the engine bay trying to figure out how to run the IC piping. The T03/04E turbo requires a 1/2-in. spacer on the exhaust flange for clearance. This pushes the compressor housing and outlet very close to the driver side strut tower. One day while under the car I happen to glance up and saw that the compressor was right inline with the gap between the oil pan sump and the crossmember. I rotated the compressor until the outlet was pointing down and mocked up the piping. Sure enough, a perfect alignment! I posted a thread a while back showing my routing and it illicited a good discussion. The thread can be found HERE. By the time I had the IC and piping installed in the car, Wolf was 90% installed as well. I was truly down the home stretch.
-
I pulled the old L24 out of my car in February 2007 and spent the next 4 months either working on the Wolf harnesses, stripping all of the undercoating off the bottom of the car back to the rear riser, or stripping and painting the engine bay. I painted the engine bay and tranny tunnel with POR-15 after stripping them done. I then painted the engine bay with Rustoleum textured black spray paint after painting over the POR-15 with their paintable primer. I used PORs automotive undercoating top coat over the POR-15 for the tranny tunnel Yorgee (Jorge) and his father came over on a Saturday in June 2007 to help me install the engine and transmission into my car. We had a little emergency when installing the rear main seal. It was a Nissan OEM seal and when we installed it, it went in too far. When trying to extract the seal, we wound up destroying it. I was immediately on the phone trying to find a new one as MSA was already closed. I got very lucky and located a OEM Nissan seal at Irvine Nissan (now OC Nissan). It was their last one and the last one within at least 100 miles. We all hoped into their Mazda MPV (in pristine condition by the way) and drove down to Irvine Nissan to pick up the seal. One hour later we were back home and back to work.