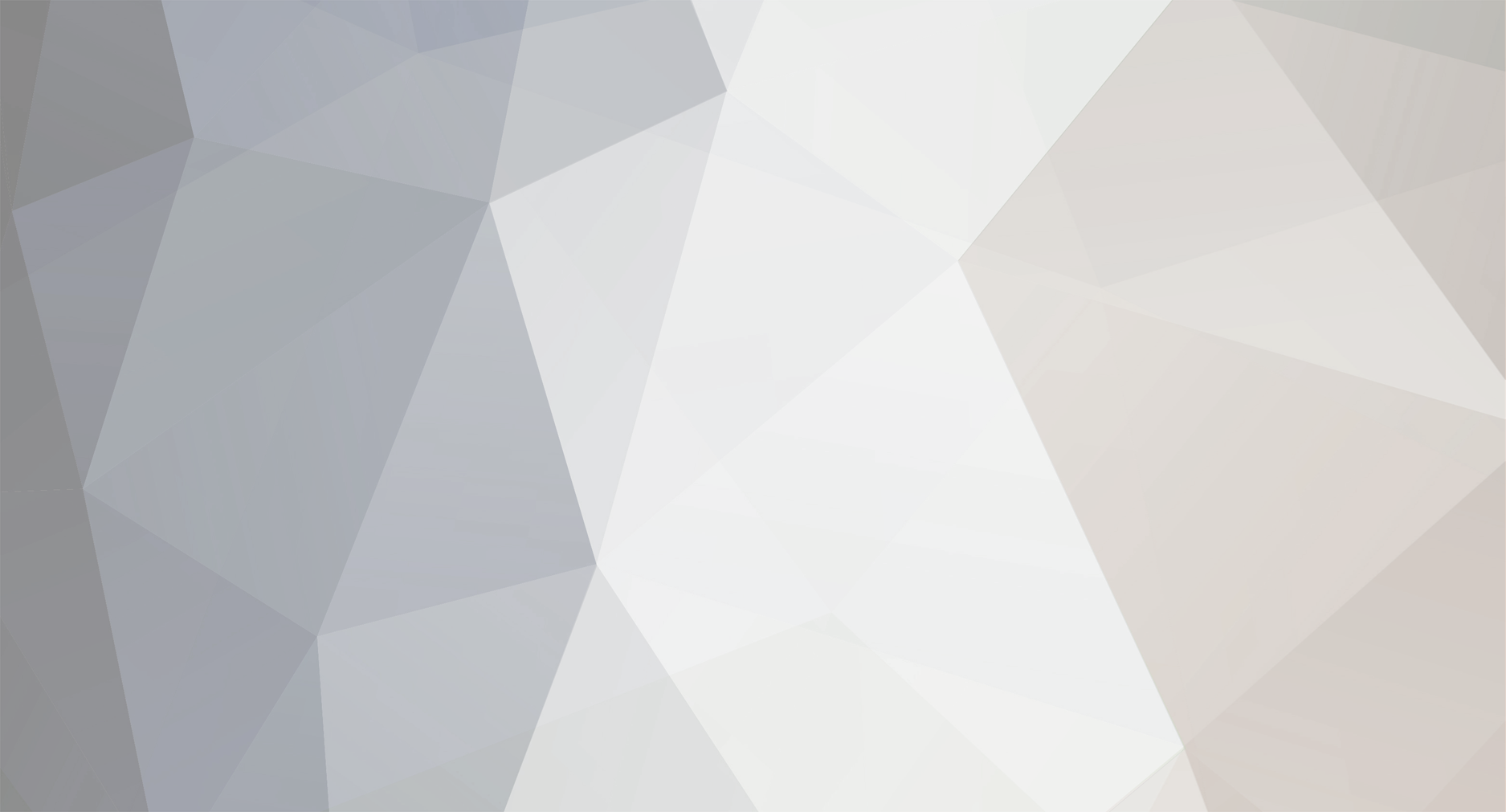
X64v
-
Posts
543 -
Joined
-
Last visited
-
Days Won
1
Content Type
Profiles
Forums
Blogs
Events
Gallery
Downloads
Store
Posts posted by X64v
-
-
If the 240z tach will work based on simply uneven flow then it would work. I don't know if it needs that full stop of current or not.
As far as modern systems changing dwell, I don't know if any other system does it, but if Megasquirt is running the coil or coil packs directly (as I plan to do) then the dwell will be fixed as long as it can pause for the minimum discharge time. So a wasted spark set up would most definitely overlap charge times when run directly by Megasquirt.
As to the stock dwell, it's not fixed in milliseconds, it's fixed in degrees of crankshaft rotation (I believe 30-35 degrees is what the FSM called for for my 73) because of the way a points distributor works. Not sure how the 280Zs do it.
How's this for a test of the current-sensing tach: Ground a low-ohm resistor off the coil positive and run the car (I've got a 5ohm handy that will handle the power). This will pull 2.8 amps through the tach at 14v with the coil off, then 12.1 amps with the 1.5ohm coil charging. This won't perfectly simulate the conditions with edis coils (which are at most 1.5ohm, so one charging draws at least 9.3 amps), but if the tach doesn't work this way, it surely won't work with the edis coils.
Edit: I just performed the above test on my car (5/73, but it does have the current-sensing tach) and the tach indeed kept working. It's not a perfect test, but it's a good sign.
-
With the current sensing tach (70-72) you just need to power all of the LS1 coils from the same black/white wire that powers the original coil. It will count the current pulses from all 6 LS1 coils.
Sure, that would work for the lower rpm range, but what about when you get past 5714rpm (assuming 3.5ms dwell) where their charge times begin to overlap? Then wouldn't the tach go dead, as there would always be current flowing through the wire?
-
I've got a super-trick, super-simple way of running the 240 style current-sensing tach on MSI/MSII with EDIS, a magnetic crank trigger, LS1 coils, any setup that doesn't use a single coil. I'll post it up when I test it out.
-
4:04am MST. Ugh, still in the university library (been here since 5pm), currently writing a paper explaining how Achilles' transformation through The Iliad 'mirrors a transformation in the social concious of humans'. Browsing HBZ for inspiration, of course.
No point in going home, really; Dynamics at 8am, Thermo at 9.
-
Does anyone offer this same choice selection for someone who doesnt want to run coilovers or am i SOL?
No, you're pretty much SOL. The stiffest combo I've been able to find is the Tokico drop springs for the 280z. If you use them on a 240 you just cut them for the desired ride height, which will stiffen them up a little as well. I did something like that, giving me 200lb/in. front and 215lb/in. rear.
I hear it's possible to use 2.5" springs with modified stock perches, but come on, that's pretty hack. It's definitely the wrong way to do it.
-
Ha, I worked for the guy who built the car in the last two pictures.
-
I don't even know how many threads there are on this. Here's a good one:
-
Fixed it.
I looked up the schematic for the LED circuits (here) and found that it's a very simple circuit switched by a transistor that's controlled directly by the processor. So, I pulled the processor and powered up MS, and the LED still came on, which told me that the transistor had shorted out or something. Replaced the transistor, all is well.
Hopefully this fixed the problem of dying when it rains, but I'll be putting a desiccant pack in there just in case.
-
Yeah, the weatherstripping leaks all over the place, but the box doesn't get wet.
-
However - you changed the function of LED16 and yet you said "no change". No change = it still won't run, or the LED was still on?
Both, the LED was still fully lit, the rpm read zero during cranking, and so it would not run. Also, I can connect my lap top - MegaTune says that accel enrichments are off. I usually run in MAP-based accel; switching to TPS-based accel doesn't change anything.
Also I connected it to my friend's Mercedes, light stays on. Connect his MS to my car, accel light stays off on his.
I will probably add a desiccant bag, but I wonder why I have to when no one else does.
-
Alright, well I've had this annoying problem where when I drive the car in the rain (L28et, VR dizzy, MS I V3.0, MSnS-E), it will sometimes die, and the car won't restart until it 'dries out'. When this happens, Megasquirt won't read any rpm signal, and usually the LEDs are just all off. This happened for the third time ever yesterday, but now the accel LED (far right, LED16) is always on, and it still doesn't read the incoming rpm signal, so the car won't start at all. The box didn't get wet at all, nor has it ever been wet. The circuit board looks great, no cold/broken solder joints. It did start and run for a few seconds, but the accel LED was still stuck on, and the pulsewidths were super rich. I reflashed the firmware (029y4) and reloaded the .msq, no help. I changed LED 16 from accel to spark output B, no change. I tried plugging the ecu into the harness on my friend's megasquirt'd Mercedes, the LED still stays on. Likewise, his ecu plugged into my harness works fine (no LEDs on).
Main problem/question: What could be wrong to always keep LED16 lit/not read rpm input?
-
Warning for mild language.
-
...then air pressure should be all the same just like with liquids and hydraulics...
False. The water pressure in something like the ocean or a bath tub or a cup of water is proportional to depth, just like air pressure.
...the air closer to the ground is slowed down by trees, building, mountains, etc. causing it to be a high pressure...Also false. Yes, the air closer to the ground is under more pressure, but it has absolutely nothing to do with fact that mountains and trees are slowing the wind down. In this situation, the amount of pressure a fluid is under (air is a fluid) is dependent only on the weight of the column of fluid above it.
Edit: Don't take any of that personally, I'm not trying to rain on your parade, just to help you understand.
-
That thing sounds amazing.
The narrator opens by saying that it lapped Nürburgring Nordschleife in the record time of 7:59, breaking though the 8:00 barrier for SUVs, which was previously thought nearly impossible. Hans says it's wonderful to drive, that it doesn't overstear or understear. It's a V12, I'm pretty sure the narrator said 700 HP.
-
A Bronx Tale. Sonny said that, but it was 16.
I just DL'd it last night and watched it. Excellent movie.
-
S30s are perfect for this. Most have not been converted to keyless entry, and the lock pull is right there, easily reachable across the narrow cabin.
-
Does anyone know of any 6 cyl. wasted spark coil packs with built-in ignitors? I'm going to have MS run my coils instead of using the EDIS-6 module, but the Ford and GM wasted spark coil packs that I know of don't have ignitors/drivers built in. To run those, I'd have to put 3 BIP373s (the new VB921s) in the MS box, along with perhaps an extra connector, which I don't really want to do. The LSx truck coils would be perfect, but they're out of my price range.
My other idea was to use a separate ignitor pack, something like the Z32 PTU. Does anyone have a pin-out on that module, or know of another one that might work?
-
This is really neat, but also kind of creepy...How does google do this?
They drive around with cameras on top of cars and just take pictures of everything in view from the road.
-
Where specifically are you looking to measure distances in inches? It could be done for specific applications using simple trig.
-
The Haynes Manual lists it at 100ft.lbs. for the '70-'78 S30s. I don't have my other books handy but I bet it's about the same for the L28et.
-
The tricky thing about welding these bosses is getting them aligned if you want to use a fuel rail.
That was my thinking. The advantage of grafting the EFI manifold flange on is that one can use readily available o-ring fuel rails. I think that'd be a cleaner look than welding in all those big clunky injector holders.
-
Along the same lines, I think I may need to play around with simultaneous instead of alternating injection. The car fires off very well, but no matter the warmup settings, I have to give it throttle to keep it running above 500rpm, and it's still rough till it warms up. Even introducing a vacuum leak as a manual IAC didn't help much.
I'm not sure what's causing the first problem you describe, but as for what's quoted, switching between simultaneous/alternating injection will have no effect on your idle speed or warm-up characteristics. When I switched from simultaneous to alternating I made no adjustments to my warm up or idle speed settings, and the way it runs cold didn't change at all. If you have no IAC or fast idle (I don't, either), it's simply going to idle very low while cold, plain and simple. I have my hot idle set at 1000rpm, and it won't idle above 500rpm until the water temp is above 80 degrees or so.
-
They are the same size and piston count as the base 2006+ 350Z brakes.
Gotcha, I didn't know they changed the base brakes in '06. I was comparing them to the early base 350z brakes.
-
it needs 14" rotors all the way around with 8 pot wilwood calipers up front and 5 pots in back with a tilton 3 pedal setup using 1" M/C's and an adjustable brake balance bar, then a 1 1/4" front sway bar and 1" rear bar using solid links, then we need a 3 way adjustable rear LSD and some BBS 3 piece 18" road racing wheels with 11" slicks all the way around.
Haha, you had me going for a second there.
Tach with EDIS and MSII
in MegaSquirt
Posted
A 240z points-type ignition, or the electronic 280z?
And that would be wonderful if it would work directly through the stock tach.