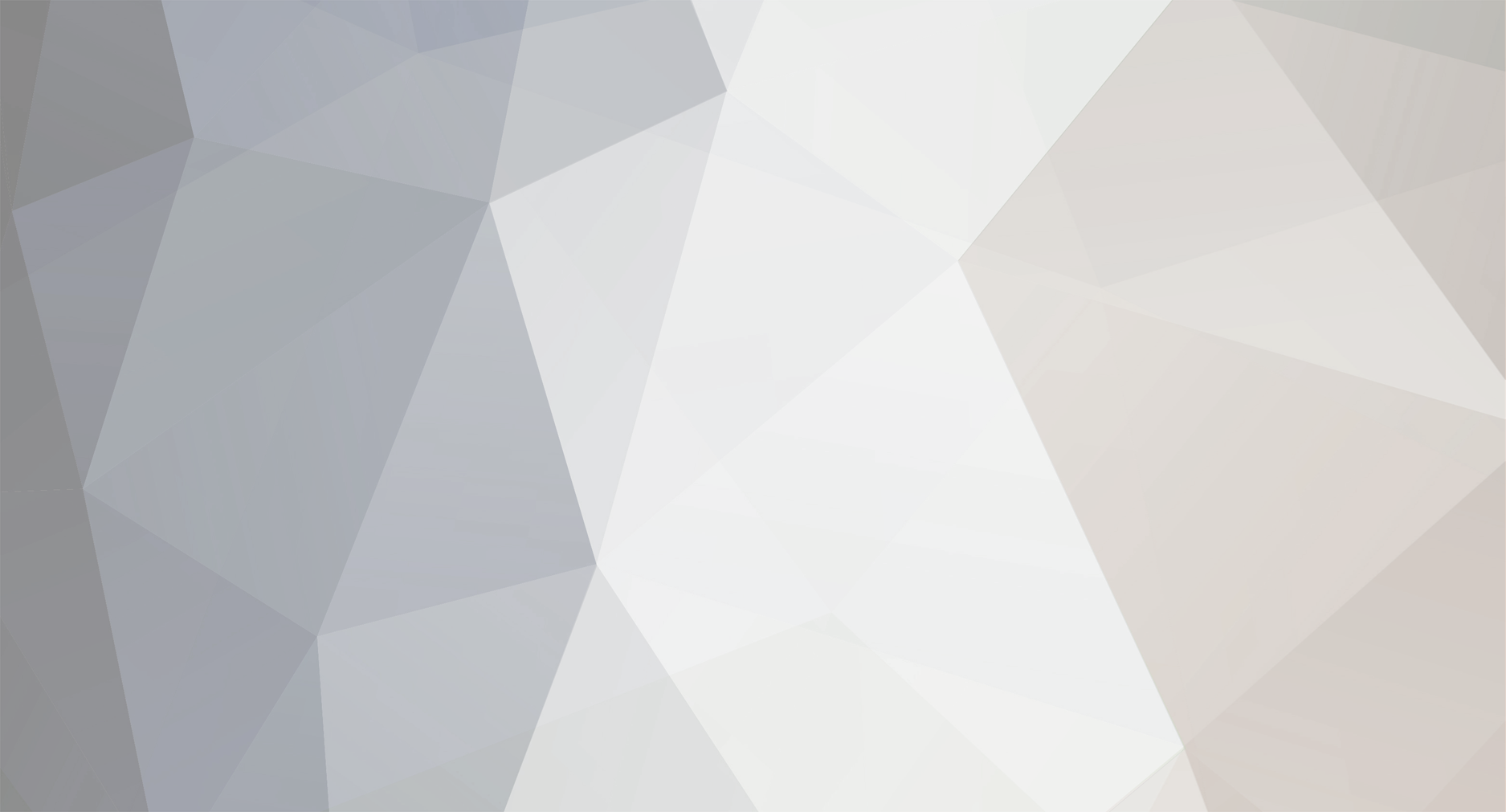
Sam280Z
Members-
Posts
395 -
Joined
-
Last visited
-
Days Won
4
Content Type
Profiles
Forums
Blogs
Events
Gallery
Downloads
Store
Everything posted by Sam280Z
-
-
I'm in the process of attempting to get better gas millage out of my 280Z. It seems the best I can do is 16mpg, but I usually get more like 13.5mpg. I have triple 44PHH Mikuni carbs on it. Right now I have 52.5 primary jets in it. When I lean the idle mixture screw about 1 3/8 turns out I get good idle mixture (~14:1 on my WBO2). But I get lean mixture (~16:1) and intermitent miss and backfire through the carbs at part throttle cruise. I can get rid of this if I richen the mixture screws up another 1/2 - 3/4 turn. But my idle mixture is then 12:1 - 13:1. I think I need to richen the idle jet, but do not have an assortment of jets to try. I'd also prefer to not have to buy a bunch of sizes, because when I get it right, I'll have a bunch of jets I'll never use. Any opinions on what size idle jet I should try first? If anyone has a collection of jets, or some slightly richer than the ones I have, I would be interested in them. If there are many people here who have Mikunis, what are the chances of setting up some sort of jet exchange program?
-
-
http://www.amazon.com/exec/obidos/tg/detail/-/1931128049/qid=1092748638/sr=8-1/ref=sr_8_xs_ap_i1_xgl14/103-6227244-0491845?v=glance&s=books&n=507846 http://www.amazon.com/exec/obidos/tg/detail/-/1555611591/qid=1092748817/sr=1-1/ref=sr_1_1/103-6227244-0491845?v=glance&s=books The L6, being an overhead cam engine, has many things to consider during a rebuild that other engines do not... Sam
-
Monster Stroker Motor SOLD AND PAID FOR
Sam280Z replied to RB26powered74zcar's topic in Non Tech Board
I'm the guy that bought the motor from Joel. I payed for and took delivery of the motor on Sat July 31. It is not up for sale again. I have been out of town for the past two weeks and have just became aware of the situation with this SCAMER. Lets find the bastage and pull out his toenails... Sam -
Monster Stroker Motor SOLD AND PAID FOR
Sam280Z replied to RB26powered74zcar's topic in Non Tech Board
Thanks Yasin. I think I got an excellent deal on this motor. Joel took me for a spin before we pulled it. He didn't get a chance to take anyone else because he shredded his right rear CV joint on the third time he got on it. The thing revs up so fast you have to start thinking about shifting before you put your right foot down. Now I just have to get the car on the rotisserie painted and back together... Sam -
More progress = More questions
Sam280Z replied to JMortensen's topic in Brakes, Wheels, Suspension and Chassis
I would repair the stripped captured nut with a thread insert (helicoil)... -
More progress = More questions
Sam280Z replied to JMortensen's topic in Brakes, Wheels, Suspension and Chassis
I would repair the stripped captured nut with a thread insert (helicoil)... -
Why can't we use deisel fuel in our high compression engines
Sam280Z replied to olie05's topic in Miscellaneous Tech
http://auto.howstuffworks.com/diesel1.htm What is not spelled out on this page is that diesel is injected at or near the point of max compression. I would guess that deisel would tear up a high compression engine through detonation because it would be available to burn throughout the compression stroke... -
use LPS3 http://www.lpslabs.com/Products/CorrosionInh/Lps3.asp You can get it at Enco: http://www.use-enco.com/CGI/INSRIT?PMAKA=505-1296&PMPXNO=943635&PARTPG=INLMK3
-
What is this component of a 83 ZXT harness?
Sam280Z replied to Sam280Z's topic in Turbo / Supercharger
What do it do? I assume it modluates the fuel pump but why does the fuel pump need modulating? Sam -
Does anyone know what the small metal box in the upper right hand corner of this pic is? I pulled one with my harness, but do not know what purpose it serves. It has a JECS sticker that reads: 17001 P9000 A63-00 030.
-
You can get a cheaper TIG if you go with a straight DC machine. They have some pretty small ones. Check state auctions. Here in Louisiana, I know a guy who got a $3K machine for $300. Remember for TIG, just the torch can run over $100. Gas bottle ran me ~$160. What do you want to weld? Material, thickness, joint type? This will determine what type of welder you should get. Unfortunaltly $500 is not much to spend on high quality / versatile equipment Maybe you can find something used. There are some good deals out there, but most people know what this stuff goes for new and price accordingly. Sam
-
If you are thinking of going with a TIG, you should do a BUNCH of research. What you buy is really dependent on what you want to do. The cheaper models will stick metal together, but come with less features that make welding easier. For instance: For welding aluminum you want AC (preferably square wave) with high frequency. The AC alternately cleans the oxides off of the base metal and penetrates the base metal. The high frequency stabilizes the arc as the polarity switches and the voltage crosses through zero. Without HF, you can have trouble keeping and controlling the arc. For welding steel you want DC with high frequency start. High frequency here keeps you from having to touch the tungsten electrode to the base metal and risk contamination on starting the weld. You also want to make sure that the machine offers low enough amperage settings for welding thin material. Most low cost machines have limited amperage range, no high frequency, and no square wave AC. IMHO, the best bang for the buck out there right now is the Miller Syncrowave 180SD. I just bought one and am extremely pleased with it. Check the Miller web page… Other things to consider include electrical service. I had to run a 60 amp sub-panel in my garage. This ended up involving changing out my entire electrical service which added ~$700 to the cost of setting up the welder. Also, TIG supplies are not real cheap. They won't break the bank, but you will go through a bunch learning. You will also need a good helmet. IMO, it is worth buying a high quality auto darkening one, especially if you are learning. You will also need a small bench grinder for sharpening electrodes. The HP book on welding is good as a start, but it is a little out dated in some areas. The book that came with my Miller has better info, but is harder to follow... FWIW, Sam
-
I've never worked on a 76. On a 77 (if I remember correctly) it is under the dash on the driver's side. It is hard to miss. It looks like a plug capping the end of two wires together. Sam
-
need to buy or build rotisserie and engine hoist
Sam280Z replied to tannji's topic in Body Kits & Paint
Here is what I did for my 78: 2 X $40.00 Harbor Freight engine stands 1 Chopsaw 2 pieces metric square tubing (from when my neighbor tried to lift an entire plymouth sports fury and bent the lift arm on my hoist) This would be the hardest part to get. Metric tubing is not readily available. I'm sure something else could be made to work. Various square tubing and large angle iron (to bolt to chassis) Front bolts to bumper shock mounts (you have to notch the anfle iron to clear some tabs. Rear bolts to tie down mounts. Both are basically two pieces of large angle iron drilled for mounting holes and welded to heavy guage square tubing. 4 exhaust clamps (to ties chassis maounts to rotisserie heads) Modified engine stands to have casters at all corners. This has supported the entire chassis + suspension (including diff) and allows 360 deg of rotation. And, I can roll it anywhere there is smooth concrete. -
Joel, The picture doesn't show. But if it is a bearing cage as Greimann says, then you need to go easy on that transmission. I can only guess as to the HP you are making. The cage keeps the ball bearings spaced. Without it, it is possible for them to all find their way over to one side. The center of the carrier can then move towards the side without as many ball bearings. Not good when giving it lots of power... I didn't see the pic, but you may still have enough of the cage there to prevent damage for a while. Sam
-
4 wire is same as 1 wire. It just has a more reliable ground and a heater so you can vary the location in the exhaust.
-
Guys, Don't waste your time with these O2 sensors. Do a google search for "wide band o2" or UEGO. Others have explained it much better than I can. This page has a good explanaition: http://www.fjoinc.com/automotive/WBO2details.htm#wbo2rpm I am in no way affiliated with FJO. In fact I built my own wide band o2 based on the design available at www.diy-efi.org HTH, Sam
-
A few months, HA! I've been working on that damned thing since 98. That's when I pulled it off the road. Most of the work has been done in the past 8 months though. I finaly decided that I would do it right and spend whatever it took to that end. It also helps to order something for it every couple of weeks. A new or improved part coming in can get you fired up all over again. Sam
-
If you want to see pics of my rotisserie, check out www.songne.net. Follow the link to Sam's 78 280z. These pictures were taken a few weeks ago, I'm quite a bit further along now... Sam
-
I think Nissan reversed the front and rear circuits around 72. You can use the later MC, but if they are reversed you will want to swap the brake lines front to rear. Just make sure the brake lines that lead to to the front brakes go under the reservoir with the larger capacity... Sam
-
No prob Jeff. Glad to see I'm not the only one crazy enough to do this. Another thing, cut the stripping pads into small pieces off the bat. Easier to rinse the gunk out and the pad will last a lot longer. It also makes you pay more attention as to exactly where you are scrubbing. I've noticed that a lot of nasty thinner and stripper has run down inside some of the channels. I plan on cutting 7/8in holes in them with a hole saw and cleaning out in there. I already cut two hole in the very front of the car at the radiator support looking straight down into the frame rails. With a flashlight I can see that the metal is solid inside, but begining to show some surface rust. I want to wash out inside all the rails and use metal prep and then spray epoxy primer in there as well. I plan on using a garden pressure sprayer with a 360 deg spray head to do this.
-
I forgot to mention... Get 3M stripping pads instead of scotchbrite. They don't fill up as easily, even with gooey undercoating. Sam
-
First I have to say thanks for the reducer idea. Not only does it work well but you get a nice buzz as well. I am doing the exact same thing to my car. And I am in about the same place as you, except for the small nooks and crannies. I was fighting those pretty hard, but the reducer works awesome. I wouldn't sandblast. Been there done that (on another car). Sand gets everywhere. You will never get it out of everything. I recommend using a chemical stripper to remove the primer and get it down to bare metal. I noticed that the reducer softened the primer quite a bit. On places that had stripper applied it even would wash the primer away. I too haven't decided what the finnal coating will be. I do know that it will be primed with an etching primer and then an epoxy primer (after treating with some sort of metal prep). I guess I should tell y'all what Ive tried so far: Easy Off oven cleaner: apply thickly and cover with a plastic garbage bag, let sit 24 hours. Undercoating and primer sluff off easily. Do not allow to dry because it only seems to work once. Charcoal lighter fluid: soak a rag in it and lay over undercoating, cover with plastic and let it sit. The undercoating gets real soft and scrapes up easily. Heat gun: just heat and scrape. Chemical stripper: tried quite a few. Some didn't work worth a damn. The sprayable (comes with a squirt bottle) works really well, but the spray bottles don't last long enough and the only other spray bottles I could find only lasted a few squirts. Finaly, I have been washing with mineral spirits in a spray bottle and lots of shop rags (from teh big box). All of these worked well for large smooth areas. Its the nooks and crannies that kill you. Another thing that worked well was a cheap set of wood chisels. They come in various widths, and are sharp and plenty stiff.