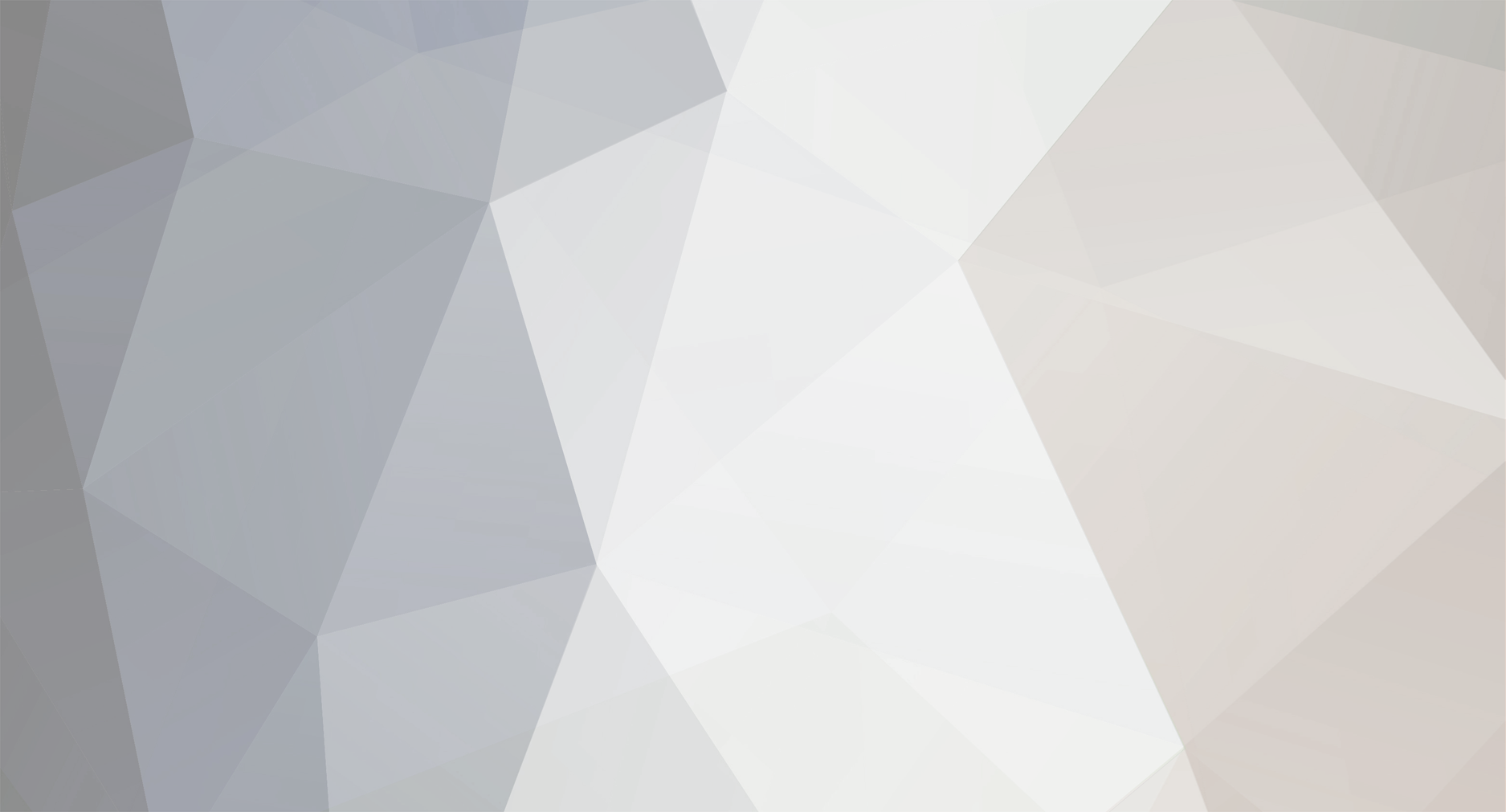
Sam280Z
Members-
Posts
395 -
Joined
-
Last visited
-
Days Won
4
Content Type
Profiles
Forums
Blogs
Events
Gallery
Downloads
Store
Everything posted by Sam280Z
-
John C is right. You shouldn't worry about holding pressure. The real issue with plenum failures is fatigue. Every time the plenum goes from vac to boost it flexes. This can eventually lead to a failure. The key is to avoid stress risers and design the plenum to be stiff such that it doesn't flex much.
-
Welder delima, help, bought two welders...
Sam280Z replied to RB26powered74zcar's topic in Non Tech Board
You won't regret keeping the miller. How are going to get the craftsman? The eBay add says he won't ship. If the miller fits the craftsman cart, you have made out like a bandit... Also, if you make over to Baton Rouge I'll let you try out my miller 135 before you decide... Sam -
Joel Soileau's trick is to use washers of various thicknesses to get the pattern right. Then measure the washers total thickness to know what size lash pad to purchase.
-
A cheaper and readily available wax for the cutter wax Paul refers too, is toilet seal rings. They are about a buck a piece and available at every hardware store. I've never used it on a carbide cutter, but it works great on the sandpaper wraps.
-
Before you go the ebay or online route, check with your local welding supply. I don't know what you have in lake chuck, but I went with national here in Baton Rouge for my 135. They quoted a price that was right at what I could get online after adding taxes and shipping. So I got it from them. I had to tell him what I could get it for before he came down on price. While you are there you can figure out the bottle cost. It is high upfront, but argon is cheap and it lasts a long time. While you are there I would cost a oxy/acetylene rig. Mine has saved my but more often than the mig. Oh, and it will take a while to go through the consumables that come with the welder. I would also get a roll of flux core for welding dirty stuff (not the z of course). I agree that the 135 is plenty of welder for a z car. Sam
-
I just did this: this past weekend with 3X1 tubing.
-
I'm pretty sure that is normal
-
Brake pedal works until you start the engine
Sam280Z replied to Z24O's topic in Brakes, Wheels, Suspension and Chassis
check for leaks everywhere very closely. Make sure the calipers are installed such that the bleed screws are pointed up. -
steering knuckles are heat treated. That is why it is killing your bit. If you weld it, you will need to get it re-treated. If needed, I would drill it to a standard size and bush it.
-
Does this need to be a close tolerance hole? If so, you should drill it smaller than 5/8" and ream it (or get it reamed) to 5/8". A 5/8" drill bit will make the hole slightly larger than 5/8" and not quite round.
-
If the bit is jumping around, it sounds like you are turning the bit too fast. Try slowing it down. Make sure to use a cutting fluid. Lard or beef tallow works well on steel with the added benefit of smelling like a BBQ... EDIT - I just realized you were drilling out your steering knuckles. Those are hard as hammered cat turds. You need to turn the drill slow. A solid carbide bit would work best. Prodigious use of cutting fluid is called for. I don't think you have dulled it as much as burnt it up. If you overheat the drill, it looses its temper at the end. It won't cut worth a damn after that.
-
I would go get a grinding wheel dresser or a new wheel. The problem with using the side of the wheel is that it weakens it. It will work once or twice, but is not a long term solution... Sharpening drill bits by hand can be a challenge. The larger they are, the easier it is. But if you try it out and it doesn't seem to cut well, re-sharpen and try again... Sam
-
Anyone done away with Strut - Spindle pins?
Sam280Z replied to gearheadstik's topic in Brakes, Wheels, Suspension and Chassis
I'm not saying that this won't work, but... I would be concerned about that bolt turning inside of the strut housing and wallowing it out. I would try to find a way to ensure that the bolt / spindle pin does not turn. The tips of those threads will be under much more pressure than the surface of a round bar... I'm assuming that the bolt is completely threaded... Sam -
The rack bushings are split. You will need to have the machine shop bore a piece of stock to the same size as the rack housing ID. Then press in the bushing. Have them bore it to 25mm (that is the rack diameter). You can then use 320 sandpaper wrapped around foam sponge to take off just enough for the rack to slide through easily. Use a bolt and nut as a mandrel for the foam and spin it with a hand drill.
-
I managed to re-use the seal. I cleaned it up and saw no problems. Your sloppy steering is either from the rack bushings, pinion/rack wear, inner tierod end wear, and/or outer tierod end wear. Ball joints and strut bearings may also contribute. You said that you had rebuilt the suspension. Did you replace everything but the rack components? You should be able to take the rack out and judge the wear w/o disassmbly by trying to rock the various components. I don't see a kit as viable right now. Sam
-
Worked on it again this weekend. The rack bushings from Nissan have plenty of material to machine them out. I made a holder that is the same ID of the rack, pressed the bushing in, turned them on my lathe until they were a nice fit on the rack. It did take a little cleanup with 320 grit sandpaper wrapped around a piece of foam sponge and spun with a hand held drill. I re-used the original seals. After cleaning them up, they looked brand new. One rack is worn out. This can be determined by engaging the pinion with the rack and trying to rock the pinion. all of the rack is real tight - the pinion doesn't rock - except for the part where the pinion rides when the wheels are straight ahead. Sam
-
It looks like that I will have to do that. The TC5 style seal is just not available. I did find out that is is relatively cheap to get a seal made (on the order of $1.00 per seal). But you have to get a lot made. I will look into getting a standard bearing. For a bunch of info on seals, I found this: http://www.rlhudson.com/Shaft%20Seal%20Book/index.html Thanks, Sam
-
I found the zhome article: http://zhome.com/ZCMnL/tech/StrRack.htm I'm not sure if the rack bushings are supposed to be enlarged. I'm pretty sure they are for a 240 which supposedly has a smaller diameter rack. The 280Z microfiche shows the bushings on the exploded diagram, but they are not called out on the diagram with a key number (http://carfiche.com/fiche009/s30/?6:b:11). The bushings consist of a steel shell with a copper lining. A hone (stone) will not do a good job of enlarging them (the stone will fill with copper and stop cutting. Sand paper wrapped around it would work, but there appears to be quite a bit of material to remove). An adjustable ream would work if there is enough thickness of the copper before you get into the steel. I will check this out and post what I find. I could turn a holder that is the same ID as the rack housing and press the bushing in and turn the inside on my lathe. Again, the issue is having enough copper bearing material thickness. I see very little wear on the rack itself. I can still see the tool marks from where it was machined, but I will machine the new bushings to be the tightest sliding fit I can manage... I still have not sourced an oil seal. Also, could someone measure the outside dimension of a valve-spring shim and see if it is 35mm? Thanks, Sam
-
Thanks again. You are right, I had misread the fiche. I don't think the 280ZX seal will fit if it is 35mm OD unless I machine out the bearing retainer and find some way to preload the bearing. Did you have to modify your valve spring shim to fit in the rack? I pulled a shim from a box of parts I have and it is considerably larger than 35mm. The valve spring itself is nearly 35mm. I'm wondering if I got a head that had been reworked with aftermarket shims or something? Thanks again, Sam
-
Thanks Steve. This is excellent information. Especially the valve spring shim idea. How did you come up with that? I do have a question about the 280ZX seal though. Just by looking at the drawings in the microfiche, it appears that the 280ZX rack bearing preload is set with different thickness snap rings. The 280Z rack bearing preload is set with shims under the retainer. The 280ZX and 280Z racks both use the same part (48018-E8700 NLA) bearing. Since the bearing has to fit in the rack, the hole is slightly over 35mm. It appears from the drawing that the 280ZX rack seal rides in this same hole (no retainer). The 280Z seal rides in the retainer and has an OD of 28mm. From the drawings, it looks like the 280ZX seal would have to have an OD of 35mm. Am I interpreting the drawings correctly? I guess I'm lucky with the pinion gears. None seem to have appreciable wear. They are shiny where they ride on the rack, but I can still see the tool marks from when they were originally made... Thanks again for all your help... Sam
-
I have a 78 280z and have completely disassembled the steering rack (actually rebuilding 3 racks). I have attempted to obtain the parts required for a rebuild: 1) 2 angular contact bearings (15mm ID x 35mm OD x 12mm thick) 2) 1 oil seal (15mm ID x 28mm OD x 8mm thick TC5 style) 3) left and right rack bushings 4) left and right inner and outer tie-rod ends. I ordered the above from Courtesy Nissan, but only the rack bushings and tie-rod ends were available. I could only find angular contact bearings that were 11mm thick, so I turned 1mm spacers on my lathe out of stainless steel. This seems to work well. The rack bushings that are available are evidently for a 240Z and the rack will not fit through them. I intend to machine some SAE 660 bronze bushings. The oil seal is NLA from Nissan. I am attempting to source it now. Any suggestions on where to find this seal in small quantities? If I can only source a large quantity, is anyone else interested in them? Would anyone be interested in spacers for the pinion bearings or rack bushings? If there is interest, I might put together a kit. Has anyone successfully completed a rack rebuild? If so, any advise? Sam
-
Silicon dioxide (silica) is sand. http://en.wikipedia.org/wiki/Silica Silicon is a common constituant of metal alloys, esp aluminum. Compare to the difference between carbon and carbon dioxide. Carbon mixed with iron is steel. I don't have any experience or advice with this issue, sorry.
-
What type of head is it? My best guess is that the back of the cam lost oil which wiped the old cam and tower. Replacements were sourced from another engine and it had to be shimmed to align the cam bore.
-
The free Google tool bar has a spell checker that works awesome. It checks every form field on a web page. It highlights misspelled words and when you click them provides options that fill in automatically when you choose them. It identified four errors in this post, which I have corrected.