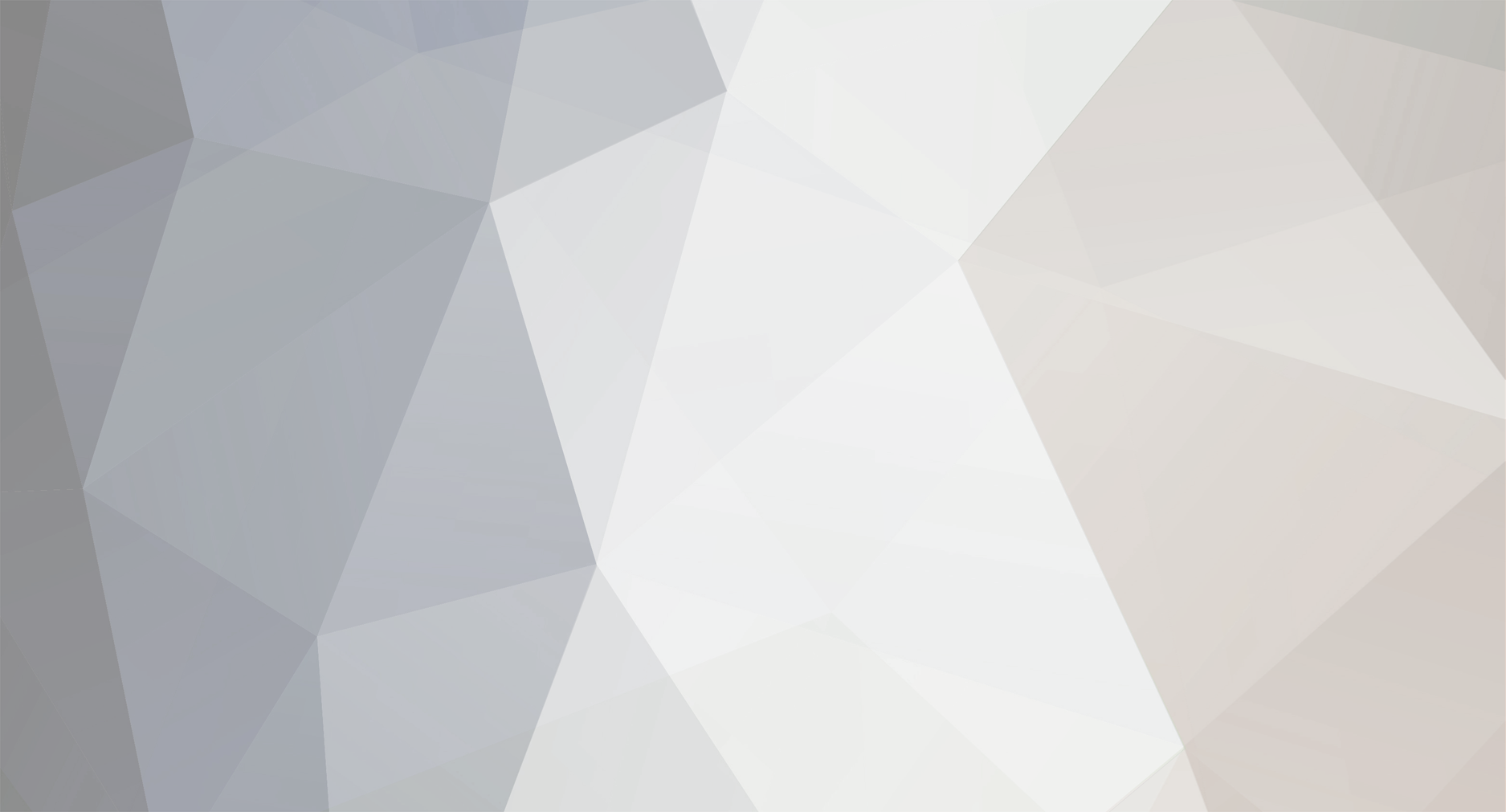
Pop N Wood
-
Posts
3012 -
Joined
-
Last visited
-
Days Won
5
Content Type
Profiles
Forums
Blogs
Events
Gallery
Downloads
Store
Posts posted by Pop N Wood
-
-
Holy chit! And I thought I was just annoying everyone!
I've had my HF helmet for a couple of years with no problems. Good weekend helmet.
-
The stock tank is 16 gals. Looks like he has a stock tank with a sump, that's what I have too. It works great with EFI, I have never had a problem.
What's it like welding on the stock tank?
I once tried to fix a busted tank and had no luck getting a weld to stick. Any tricks? Use a MIG?
-
The JTR manual covers this topic. They even give the type of filler rod to use with your stick welder. They did say it must be a stick welder.
Will be anxious to hear how you like the welded diff the first time you try to accelerate on a curving, wet on ramp. Have heard bad things about how tail happy welded diffs can be on a wet street.
-
I have seen pictures on this site where someone used identical looking ball joints in just this application. I thought it was one of the better solutions to the TC rod issue.
-
My stock suspension car looks like that with 225/50/15's.
One possilble solution is a taller wheel/tire combo. which sucks because that size wheel/tire is suppose to be a good autox configuration.
-
The 95 has an OBDII computer, but is only required to meet OBDI regulations. This is good because the OBDII computer is flash reprogramable (i.e. use a laptop vs. burning new chips). But OBDI regs are good if you are subject to smog laws and inspections. OBDII requires the after cat O2 sensors and possibly the ABS wheel sensors, depending on how big a prick you are dealing with at the referee station.
-
You could even go with a lighter R180 if you weld the diff.
-
Try pulling one out and you will.
-
I have that booklet. I didn't find much useful in it toward my pending swap.
-
There was an internet scam story about this going around a year or two ago.
Sure thiis is real?
-
When it comes to removing spindle pins I have one simple rule:
Just say no.
-
They are suppose to be pretty harsh riding parts. More race then street.
I looked seriously at them some years ago (before I was married
). They are a lot of money, but you get a hell of a suspension for all that dough. would be hard to duplicate for less.
-
2000 and on F body engines are suppose to have some worthwhile oiling changes. 2001 and 2002 engines have better heads and the more desireable LS6 intakes. LS2 engines out of the later GTO's have all of the above and a 4" bore. More potential there, but there are come changes that will need to be done. Look up a member called Ulissies (sp?). His GTO/LS2 powered Z should be about on the road now. Truck/Escalade engines have iron blocks and the same 4" bore, and make better forced induction platforms. But they have issues with intakes and oil pans. The aluminum blocks from the vettes, f bodies and GTO's are probably a better choice for a Z.
The JTR book will give you some good ideas on suspensions, transmission cross members and exhaust. It also has much needed info on guages, cooling and rerouting the brake/fuel lines. Worth the 35 bucks or so even though it won't let you cook book the entire swap like it does for a gen 1 SBC.
-
Not a bad price for a whole car. I called on one out of a 2001 Camaro and the wrecking yard wanted $4500 for the engine, $2000 for the trans, but for me only I could get a package price of both for only $6100.
-
If you want cheap, get a used American made. Japanese models command too high of a resale value. Cavaliers actually have pretty reliable engines and trannys. All of the other body parts will fall off before 100K. But if you just need it for a year, then why pay the markup of a Japanese make?
The above comments are only my, worthless opinion, and in no way are intended to start a flame war about American vs. Japanese cars.
-
You are going to get thumped if you don't make an effort to answer your own questions with the search function.
-
The top hat is suppose to have a D shaped hole that locks to the D shaped strut rod. If the strut rod is turning inside the top hat, then the top hat hole is most likely worn into a round hole.
If this is what is happening, then you REALLY NEED to replace the top hat so it locks the strut slider properly. My old Z had a knocking noise in the front end when I got it. Didn't find the source of the noise until I upgraded the struts. Good thing too, because with that hole being oversized, the strut rod moved enough in the top hat that it wore half way through the rod.
If you can't get the strut rod to lock to the top hat, then there is no way you will be able to torque that nut to the proper torque. If the nut is at all loose and allows the rod any wiggle room, then it could start to wear. That is the only thing holding that whole corner of your suspension to the car.
-
I would think one rated just above the amp rating of the link.
-
Pop' date=' you know johnc does this stuff for a living right? Why would the SCCA say you have to notch your tubing for a cage if butt welding it would be just as safe? Sure it may get you by but why half a$$ something like a rollcage?
Guy[/quote']
Exactly why I didn't argue with him. Just wanted to learn what he, and others like him, know about this issue.
But, I am still not convinced the assumption that not notching the tubing makes the cage unsafe is a good one. More prone to failue? Probably makes sense. Unsafe? I still don't have enough information to make that leap of logic.
Not disrespecting anyone here, but I have noticed people get very adamant in their opinions about safety equipment. I always wonder if they really know something that make their way the only safe way to do things or if they are just making things up.
Good to know about the SCCA rule. Didn't know that. Guess if you build a cage then better follow the rules of whatever class you intend to race.
As for the SCCA, my impression of them is they have to deal with people with a wide range of varying skills. Their rules are applied after the the cars are built. They can't spec the construction process, so the only way they can assure any quality control is by basic rules that can easily be verified just prior to a race. As such one has to wonder how many of their rules are written for the lowest common denominator, or as a reactive response to some past problem. Who is to say a cage built with investment cast fittings and some exotic alloy wouldn't be safer than an SCCA spec cage? Certainly not a trackside SCCA inspector, because all he rightfully has to go by is the published SCCA rules that exist.
I know a few things about weld quality control. I have seen welds performed that were so cruicial, that the required welding certification tests expired after only a few hours. If the set up time took longer than that, then you had to wait for the next shift for the welder to be recertified.
Does that mean I know anything about notching cage tubing? Obviously not. But just blindly regurgitating internet chatter won't make me an expert either.
BTW, when I built my workbenches out of 2 1/2 inch scrap yard fire sprinkler pipe, I butt welded the joints becasue it was massively easier to size and fit the pipe than using a hand grinder to notch the joints. Still came out about a 1000 time stronger than needed. I don't think I will ever own a car with a cage, but if I did I would probably take the time to notch all the joints if for no other reason then to impress the type of people who are obsessed with pretty, rather than effective, welds.
-
I can't find the link, but somewhere on here there is a detailed dimensional comparison of a 240 and 280 axle. Besides the splines the neck of the 240 part just before the bolt threads is shown as being narrower than the 280 part. It is my understanding that that is where they usually fail
Also like Jon said, I need the 280 stubs, so more like $600 with JY parts and well over $1000 with new billet parts.
BTW, go to google, select images and search on 240Z stub axles. Comes up with links to Pete's alterdZ site and jerimio's site.
True fame there.
-
My problem is I want to get rid of the 240 stub axles. They simply are not as strong as the 280 ones. That means Ross's companion flanges at $300 or more for his billet ones. Add to the the price of the 280 stubs (Ross's billet stubs at $700 pair) and CV shafts and you are quickly down a grand or more.
-
How do you figure 65-70 to go CV's?
-
Actually I am not kidding. I see people going through all the work to fit pipes like this and have wondered just how necessary it is. I was hoping someone would come back with something less anecdotal and more quantitative. Just challenging people’s assumptions to see what I can learn.
There is no doubt you risk quality control issues when a weld is used to fill in a gap and I know it is always a good idea to do things in a workman like manner. But I don’t think it is intuitively obvious that a butt weld is less strong, let alone so much weaker as to be unsafe. Start throwing in variables like using the next larger size tubing or adding cross braces at critical joints and one might end up with a cage that is stronger, albeit heavier, than the 100 hour cage.
To pass on a story, when in the Navy I watched them cut a 10’ by 20’ hole in the side of a nuclear powered cruiser sitting in drydock. Something like 1†thick HY80 steel. 2 years later, after the ship was floating next to the pier, I watched them try to weld the original piece of steel back in place. The ship had flexed so much that there were 4 to 8 inch gaps and overlaps where the steel plate no longer lined up with the original hole. I then watched a crew of welders spend 2 weeks filling in the 8†gaps with stick welders and electric heaters. They then used these carbon sticks to “air arc†the welds to look like big, fat 3†beads. I took a closer look at the hull and that was not the first time they had done that to this 30 year old ship.
If that was good enough for a warship, hard to imagine a cage with some 1†fillet welds becoming a liability rather than a asset.
-
You might want to take a look at the ad for the LT1 before you start criticizing it. It really isn’t a bad deal when you look at everything that comes with it.
Not arguing the performance potential of a 305. My post originally included a suggestion of going to a marina to trade a boat anchor for one. No kidding. But I stand by what I said. You seem to keep missing the word “economicalâ€. It is because no one wants a 305 that makes them such a deal.
Also weren’t you the one who suggested going speed density and retuning after every mod? Adding $300-$500 to every bolt on could really add up after awhile.
Fuel tank modification for SBC
in Gen I & II Chevy V8 Tech Board
Posted
How did you guys actually build a sump? Just a low point, or is there any type of one way baffling to help keep the fuel around the pick up tube?