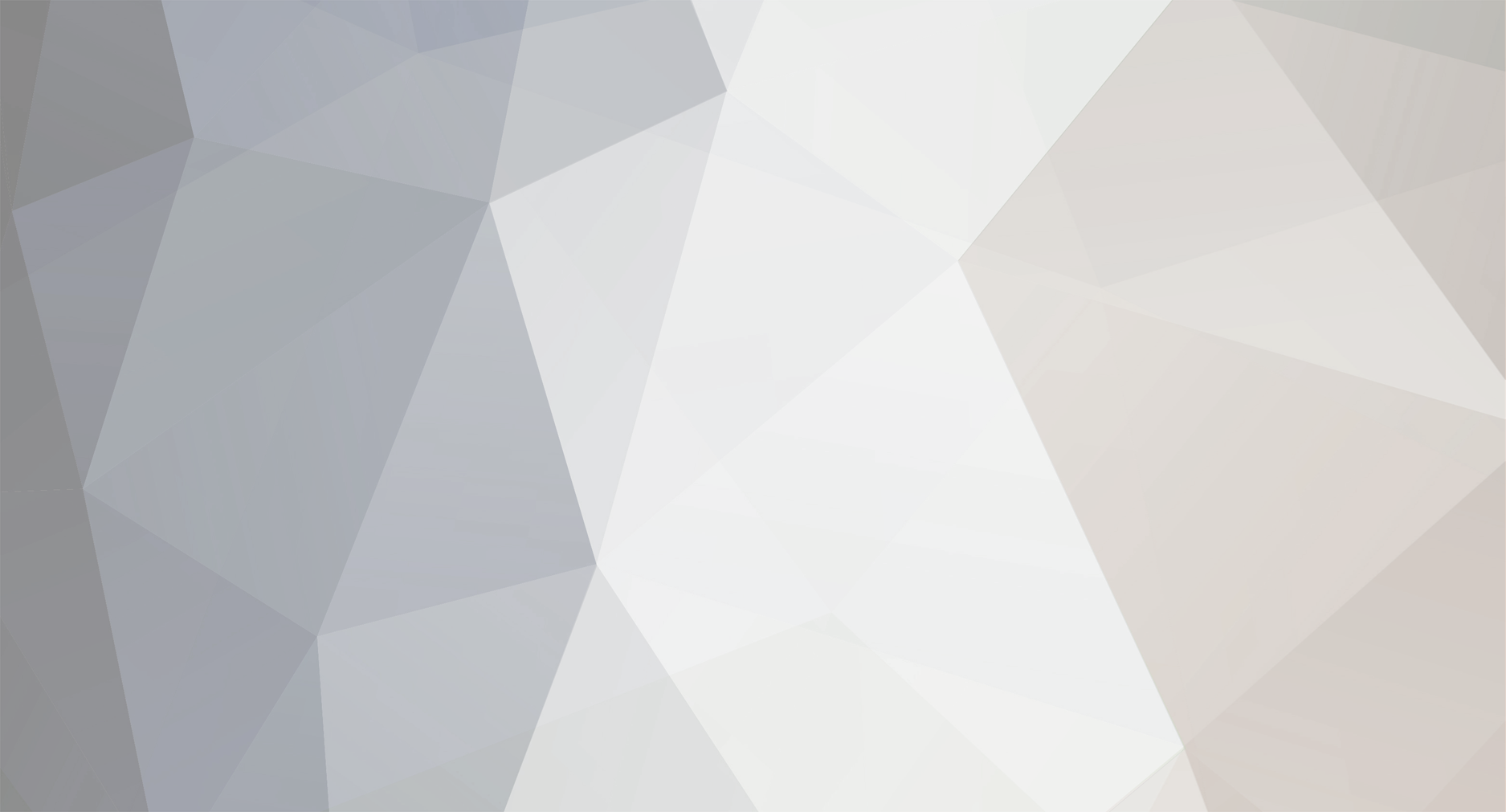
SATAN
Members-
Posts
194 -
Joined
-
Last visited
Content Type
Profiles
Forums
Blogs
Events
Gallery
Downloads
Store
Everything posted by SATAN
-
I just wanted to point out the fact that I am an idiot! The bolts out of the 88 z31 turbo diff ARE 12mm. The bolts that came out of the Q45 diff are 13mm. I could have swore that I measured them before, but I guess not. I actually did this time. It is 12mm for the z and 13mm for the Q. Sorry guys.
-
There are some models of the z31 from Canada that came with manual racks. The goal is to find them.
-
The difference is in the diameter of the bolt threads. See... If you have 29 spline input shafts then the diff Jason mentioned should work just fine. You can either make the spacers to fit around the 10mm bolts to take up the 2mm of play. OR, you can tighten the bolts down to the appropriate specs. I have READ that that is good enough. Or you could have custom bolts made with the 12mm shoulder. Tapping out the ring gear is something you might not want to do. I was thinking of having this done and decided against it for a couple reasons. I would have to take it to a machine shop to have it done since the ring gear is hardened. SINCE it is hardened it would most likely cost a ♥♥♥♥ load to have 10 holes tapped. They would have to have a tapping method to where the tap would not go all the way through the other side into the actual teeth of the ring gear. I just decided to torque mine down and hope for the best. With 10 of them holding that bitch, I really dont see it breaking. The other thing that has been bothering me is that everything that I have read says that the 84-89 r200 ring gears all use the 12mm bolts. I along with others have pulled them apart to find they are actually 10mm bolts. Mine was a CLSD out of an 88 turbo z. I'm wondering where all the info came from that said they are supposed to be 12mm.
-
In order to wear down the pinion or the ring gear inside of 200 miles, you differential should have been making horrible noises! Was there something else going on that you just did not hear it or did you not know that the sound was abnormal? That and I'm with Jmortensen, your ring gear should never have actually moved to wear out the pinion. Did you move shims around inside or something that would cause this? Bearings were fried too right?
-
Funny, right as I was coming to check on this, I realized I didn't even mention that it was a z31:ugg: Do you mean down below like under the radiator? Or under the hood latch brace? I have to keep it accessible because of the filler cap. While at the track, I block off the small supplying pump and fill the surge tank with race gas. This keeps my street gas and race gas completely separated. I cant put it under the hood latch brace due to the big radiator and the fan that sits on top of it. Not much room now. I guess I am torn between hatch area and engine bay. Hatch area means more line for the fuel to be pumped through AND I have to build a box around it that can be removed to get to the filler cap, but in the engine bay means the fuel will just sit there and soak up heat. Grrrrrrr.
-
Ok, I am in the process of installing my fuel system. Well, I should say, in the process of installing the surge tank as that is what determines the rest of the system. I have read in the 2006 NHRA book that I have that I can have it anywhere in the car I want as long as there is xx" thick barrier between the tank and the driver. Does this mean that I can bolt it in the hatch area and then build a box to go around it that is xx" thick? The only other place I can put it, would be the engine bay. I am not a big fan of that since there is so much heat. Not to mention the fact that my return line would be so short and the fuel would not have ample time to cool down before going back into the surge tank. Then it will just be hot and have to go through the pump which will heat it up again. I can run a cool can, but that puts me in a different class. Anyways, where do you guys have your surge tanks mounted? Mine is not small enough to put under the car anywhere just so you know. It is a 1 gallon tank. I would like it as close to the injectors as possible so the big pump doesn't have to work as hard to supply the injectors. Anyways, enough rambling, what are your thoughts? Did the rules change since 2006? I cant find anything on it on the web. here is the surge tank.
-
I just had to take an OSHA class at work and the instructor informed us that welding galvanized causes NO long term effects. No cancer or anything like that. Once removed from fumes within 24-48 hours you should feel fine. But in those 24-48 hours you feel like you have the worst flu you have ever caught. Now welding stainless is another story when it comes to cancer. Again, this is according to the OSHA instructors.
-
Welding stainless and Cancer. You need to know!
SATAN replied to SATAN's topic in Fabrication / Welding
I know this is off topic, but what are you welding ti for that is car related? Typically the only Ti stuff I see being welded is for mountain bikes. When you are welding Ti for cars.... You know the customer is dumping money. -
Ok, figured out how to make the viscous coupling from the Q45 solid. I had to buy special tungsten carbide drill bits. Cost about $30 for 5 of them. Not TO bad. But I drilled out half of the splined section and half of the spider gear section with a 3/16" diameter hole 9/16" deep. Then I slid a hardened steel pin in the hole and tack welded it in place. This makes it solid. If you install it like this, you will have an open diff. Now is where you need to weld the spider gears in order to have the solid diff. I'll post a picture shortly. Also, the links to my other pics are dead because I shuffled my photo bucket account around so... To drill one hole takes about 7 to 10 minutes. You have to go very slow at a low RPM due to the fact that tungsten carbide is very brittle. Very hard, but very brittle. Here are the pics. They look like they are welded a lot, but keep in mind, it is only a 3/16" pin, and it is only welded on the surface. I didn't weld a lot because I didn't want to mess up the heat treatment in the hardened steel. The tack weld is just to hold the pin in place. One of the holes I drilled slightly to far, and viscous fluid started leaking out. Not like it matters, I dont need it anyways. You can also see the failed attempt on the right, when I tried to use a regular drill bit. Yeah that was dumb. Now all that is left is to weld the spider gears, and install it into the diff. here are some other pics that dont show up anymore up top.
-
Chances are very good that you will not find any other headers for the z31 other than what you have mentioned. If you do they are most likely a custom job. Aftermarket support is not large for the z31. This is why so many people custom make their own stuff.
-
That is not that bad. It's when you start pulling out chunks is when you need to pull it apart. Metal shavings are normal. Its just wear. It also depends on how long it has been since you last checked it too. If it has only been a couple days since you checked it last, then yeah, you have problems.
-
When you say you did the standard stuff with the plugs, what exactly did you do. I have seen plugs that need to be gapped down to .020" or EVEN LESS sometimes. How far down did you take your gap?
-
Sand blasting and Silicosis. What you should know
SATAN replied to SATAN's topic in Fabrication / Welding
Yes, until they find something wrong with that blasting media. LOL. Either way, it is good insurance to grab a N95 or better mask that is good for about 40 hours of breathing and only costs about 3-5 dollars. -
Welding stainless and Cancer. You need to know!
SATAN replied to SATAN's topic in Fabrication / Welding
Which one give a better quality weld on stainless, yellow or grey? I can wear a mask not feel like less of a man so... The one that gives the best weld is what I want. I usually just use the red tipped like I do for mild steel... But I will use the other if if yields better quality. -
Couple of things here. Think of your fuel injectors like jets for a carb. If you up your jets in the carb to a huge size, its gonna flood out, This is the same with larger injectors. The ECU has no clue what size injectors it pulsing. It just knows to pulse x amount of times a second. That could be a huge difference on injectors that are twice the size of the previous ones. Also. High impedance vs. Low impedance. Its not the injector you have to worry about burning up. It is the injector drivers in the ECU. Think of it like this. You have an audio amp. It says do not run anything lower than 4 ohms impedance. It says this so you dont burn up the amp from it pushing more power than it was intended to. If you knock it down to two ohms, the amp is now flowing more juice due to the lack of impedance/resistance. The same thing holds true for injectors and ECU's. Its not the injector that can get hurt. It is your power supply/ECU.
-
There is a lot of controversy out there about Innovate and the LM-1. Other companies say "Ours don't need to be calibrated!" But I like to believe that Innovate knows their ♥♥♥♥. They have their own forum with MASSIVE tech support. I will trust Innovate and calibrate my LM-1 every three months. It takes a whole 2 minutes to do.
-
Sand blasting and Silicosis. What you should know
SATAN replied to SATAN's topic in Fabrication / Welding
Probably, but lots of people do sand blasting on their own. If you dont know what to look out for, you may just go buy some regular sand and try to blast with it. That could potentially be very bad. This warning could also go for anyone who grinds on glass. I used to be a glazier. We would cut up mirror and grind down the edges. The sand that is used for glass IS silica sand. So grinding that and breathing it in = -
Welding stainless and Cancer. You need to know!
SATAN replied to SATAN's topic in Fabrication / Welding
I like this part..."Do not eat your work clothes." -
"Welding Stainless Steel The fumes contain carcinogenic hexavalent chromium, sometimes written as CR(VI). Respirator Procedures for Welding Stainless Steel When you are welding stainless steel, wear a 1/2 facepiece respirator with a filter that has a “100″ rating. If you are working within 10 feet of welding, or if you are grinding or sweeping, wear a “95″ rated disposable respirator or 1/2 facepiece respirator. The dust is much less toxic than fumes but should be treated with care. Burning and smoking it should be done with caution. Recognize that the bother respirators cause is worth it. They keep scratchy throats and lung cancer away. They can be slightly uncomfortable. It is difficult to be heard when speaking through a disposable respirator and you have to really speak up to be heard through a 1/2 facepiece respirator. Always work in an area with excellent ventilation. Outside is best. If not possible, open windows & doors, push (or pull) fumes outdoors with a fan or fume extractor. Alert people nearby what you are welding and of the danger. If indoors, alert everyone in the building and suggest they wear “95″ rated respirators. After being near welding for a long time, be sure to shower when you get home to get the particles off you. Keep your work clothes separate from your other clothes. Do not eat your work clothes. Get your own disposable and 1/2 facepiece respirators. They will fit better, you’ll know that they’ve been cared for, and they won’t smell of someone else’s copious sweat and snot. When you’re not using them, keep your respirators in a plastic bag. “OV” filters will slowly degrade if left in the open air, decreasing their effectiveness. Also, the plastic bag will keep potentially toxic shop dusts out of the insides. Replace the filter in your respirator if you detect a funny taste or smell through it or if it becomes difficult to breathe through. Those are signs that it’s useful life is over. There aren’t any hard and fast rules about this but you should get 4-40 hours of actively breathing through the respirator. About Respirators You must use at least an “N95″ or better respirator to protect yourself from stainless steel dust and fumes. It’s a very good idea to use a better respirator because the better fit and filtering will ensure safer working, especially for people that are less experienced (like myself!) with such work environments. The literature from 3M and OSHA says that a 95 rated respirator should be enough to protect you from dangerous levels of CR(VI). Scientists simply haven’t figured out exactly why people in the welding professions have higher lung cancer rates."
-
Sand blasting and Silicosis. What you should know
SATAN replied to SATAN's topic in Fabrication / Welding
Not just any dust mask. You want to get a mask/respirator that is a n95 through n100. This catches 95% of particles for the n95 or up to 99.9% for the n100's. -
I wanted to post this up and hopefully have it stuck in the beginning of the fabricators safety, since it obviously falls under safety for... well... fabrication of sorts. I pulled this from the following site. threadhttp://www.silicosis-injury-attorneys.com/pages/sandblasting_risks.html "Sandblasters Are at Special Risk Often abrasive blasting with sands containing crystalline silica can cause serious or fatal respiratory disease. The National Institute for Occupational Safety and Health studied 99 cases of silicosis from exposure to crystalline silica during sandblasting during the late 1990's. Of the 99 workers reported, 14 have died from the disease, and at the time of the study the remaining 85 were at risk of death from silicosis and its complications. Description and Uses of Abrasive Blasting Abrasive blasting involves forcefully projecting a stream of abrasive particles onto a surface, usually with compressed air or steam. Because silica sand is commonly used in this process, workers who perform abrasive blasting are often known as sandblasters. Tasks performed by sandblasters include the following: Cleaning sand and irregularities from foundry castings Cleaning and removing paint from ship hulls, stone buildings, metal bridges, and other metal surfaces finishing tombstones, etching or frosting glass, and performing certain artistic endeavors When workers inhale the crystalline silica used in abrasive blasting, the lung tissue reacts by developing fibrotic nodules and scarring around the trapped silica particles. This fibrotic condition of the lung is called silicosis. If the nodules grow too large, breathing becomes difficult and death may result. Silicosis victims are also at high risk of developing active tuberculosis. More on the disease >> The Silica sand used in abrasive blasting typically fractures into fine particles and becomes airborne. Inhalation of such silica appears to produce a more severe lung reaction than silica that is not freshly fractured. This factor may contribute to the development of acute and accelerated forms of silicosis among sandblasters. Number of Exposed Workers Of the more than 2 million U.S. workers are at risk of developing silicosis and that more than 100,000 of these workers are employed as sandblasters. Approximately 120,000 of the 2 million workers exposed to crystalline silica will eventually develop silicosis. The disease has been know to affect as sandblasters for decades, a 1936 study in Great Britain found that 5.4% of a population of sandblasters (24 of 441) died from silicosis or silicosis with tuberculosis in a 3.5-year period. Respiratory Protection Practices Acute silicosis is less common today than it was in the 1930s because engineering controls are used to reduce exposure to respirable crystalline silica and because the use of alternative abrasives is increasing. However, data indicate that most abrasive blasters continue to work without adequate respiratory protection. In addition, workers adjacent to abrasive blasting operations (for example, painters, welders, and laborers) often wear no respiratory protection. Ventilation controls for reducing crystalline silica exposures are not used in most industries. Studies have found that even in short-term sandblasting operations (less than 2 ? hours of blasting during an 8-hour workday), the average concentration of crystalline silica was 764 micrograms per cubic meter (µg/m3), with an average silica content of 25.5%. This average dust concentration was twice the 1974 standard of the Occupational Safety and Health Administration (OSHA). In a 1974 study of respiratory protection practices during abrasive blasting, the protection factors for supplied-air respirators with helmets ranged from 1.9 to 3,750. This wide range was attributed to the varied conditions of the equipment rather than to the superiority of any brand. Maintenance was universally poor or nonexistent, and the persons responsible for selecting respiratory protection for abrasive blasting were inadequately informed about the proper use and maintenance of such equipment. The higher protection factors were associated with high rates of helmet air flow, but these high flow rates increased noise levels as a result of air turbulence. The study also indicated that the air inlets were too noisy and that the blasters' helmets tended to fall from the wearers' shoulders when they stooped. Prohibition of Silica in Abrasive Blasting Because of the high risk for silicosis in sandblasters and the difficulty in controlling exposures, the use of crystalline silica for blast cleaning operations was prohibited in Great Britain in 1950 [Factories Act 1949] and in other European countries in 1966. In 1974, National Institute for Occupational Safety and Health recommended that silica sand (or other substances containing more than 1% free silica) be prohibited as abrasive blasting material and that less hazardous materials be used in blasting operations."
-
Ok, more pics. It is almost done now. Little more welding and adding some vac. ports.
-
Bandimere Speedway is in the process of installing cooling tubes through about the first 150ft or so of its 1/4 mile track. This is the first drag track of its kind. It is now the second track in the U.S. to have a full concrete runway as well. I am sure it will only be used to cool the track to a reasonable temp like 80 degrees on a hot 105 degree day. So nothing to crazy or stupid like a 32 degree track. http://www.bandimere.com/ Thought I would post this because it is so close to home for me. This is the track I race at.
-
I JUST got one of the newer Chicago Electric ones (Has blue flame stickers). So far it seems to work great. I took the first one back though because I am an idiot. I let it charge in the sun for about 5 hours like it says. Took it out the next day and held it in the air to get the sun darken it and it didnt work. I took it back and got a different one. The new one did the same thing. I tried welding with it and it worked fine. Apparently the sun wont darken it which I suppose is a very good thing if you are doing a lot of overhead welding outside. I am not so I didn't know any better LOL. Also, one other thing about mine.... I do not have any flickering when TIG welding below 60 amps. It works just fine at low amperage. Maybe it is just because it is brand new still.
-
Oh, hey, I am fairly close to you(in the suburbs anyways). You are down by park meadows right, centennial? I am in Aurora off of 6th and I-225 roughly. It is all tore apart right now though. I have the diff out and installing a Q45 carrier, I have cams sent off to Isky to be done, and I am still in the process of welding up my plenum. If you aint got ♥♥♥♥ to do one day when I am home you are more than welcome to come check it out.